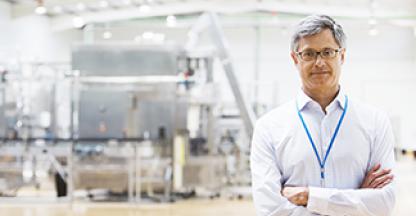
Durable goods are products that do not wear out easily and last a long time. Unlike nondurable goods, which are usually used for a single use, these products are durable. They are likely to continue providing the same or even greater utility for years. For example, a durable car will continue to serve you for years.
Nondurable items can be consumed immediately
Nondurable goods, unlike durable goods, have a short lifespan and are usually consumed quickly. In a recession, consumers tend to avoid spending money on durable goods but continue to purchase nondurable goods. These items are typically low-priced and can be bought with cash. Examples of nondurable goods are meat, fruits and vegetables, dairy products, bakery products, and dairy products. Other examples are detergent, dish soap and cosmetics.
In general, nondurable goods are the least expensive types of goods, lasting less than three years. Nondurable goods can be bought relatively frequently, which allows consumers to purchase them often without worrying about their future value. Most nondurable goods are also disposable and can be bought only one time, such as packaged food and laundry detergent. However, service goods are intangible and are created in response to customer needs. Customers plan their purchases based upon how they perceive the product. This can differ depending on its price.
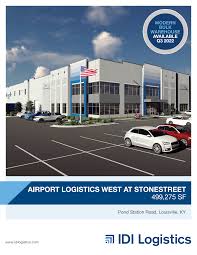
In contrast, durable goods are products that are expected to provide a steady stream of utility over a period of time. These products are also known as consumer durables. They include automobiles. Durables tend be purchased during periods of economic growth while nondurables may be purchased in times when there is economic recession.
Durable goods last longer than one year
Durable goods are tangible commodities that last for at least a year under normal usage. They can be broken down into producer durables and consumers durables. Consumer durables can include household goods like furniture, boats, and cars. Producer durables can include machinery, appliances, fine jewelry, as well as machinery.
Durable goods are expected last for at least 3 years but may require repair or servicing. Durable goods are made so that they can be used for a long time without breaking. Durable goods can be extended by proper care and maintenance for as long as 20 years.
The demand for durable goods can be a key economic indicator when the economy is growing. A rise in sales of durable goods may lead to more employment and higher returns on investments. On the other hand, declining sales of durable products could signal a decline economic activity. This means consumers are using their money to repair or service their existing products instead of spending it on new ones. As a result, a slowdown in durable goods may lead to a recession.
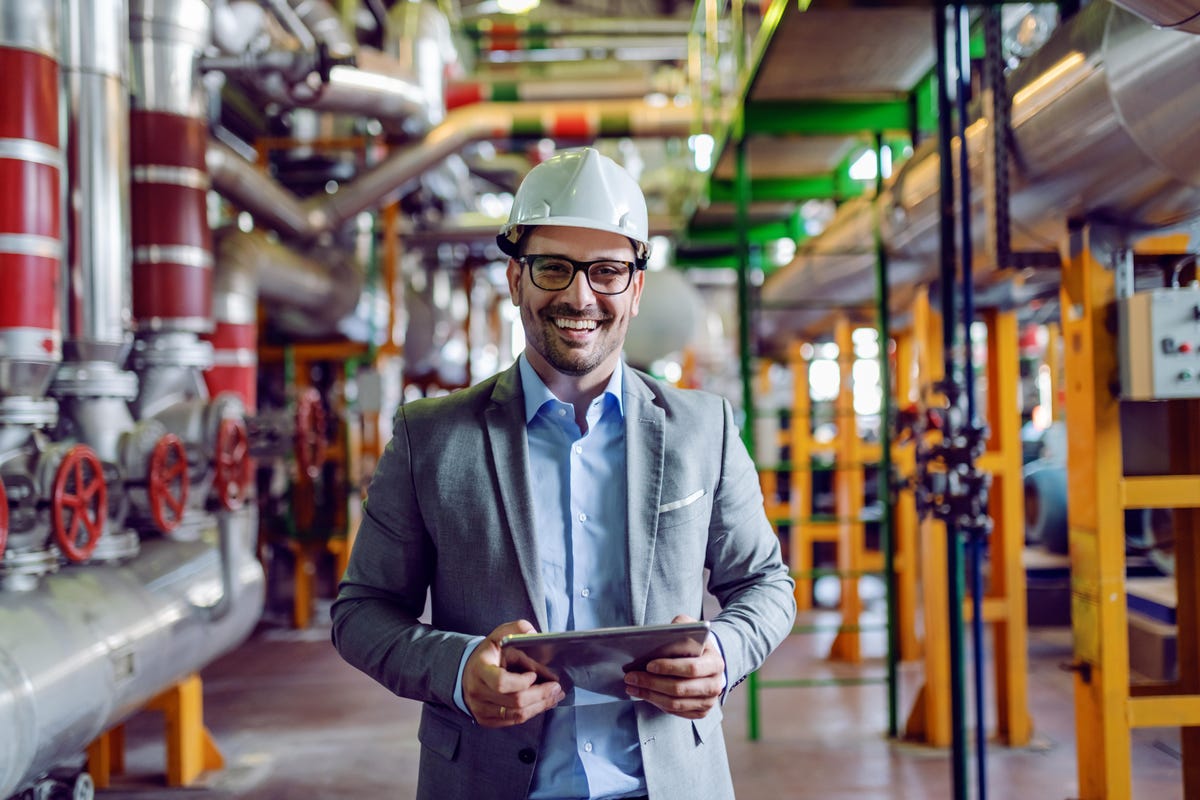
Impact of COVID-19 pandemic on durable goods
COVID-19 is a pandemic that has caused widespread illness and has had an impact on consumer spending, especially on durable goods. People stopped going to the gym and stopped attending social events as a result of the disease. People also stopped hailing taxis, which led to a decrease in consumer spending. Instead, people spent more time at their homes doing home production and leisure activities. This in turn reduced consumer spending on restaurants and other services.
The US economy is seeing dramatic effects from the COVID-19 outbreak. The disease not only increased the demand for durable goods but also prompted strong fiscal policies to increase household disposable income. This effect could be responsible for half the rise in consumer durable good spending in 2020.
The COVID-19 outbreak has affected individuals and communities as well businesses. While much has been written about the impact of COVID-19 on fast-moving commodities, not so much on the impacts on durable goods. NielsenIQ BASES just released a new survey showing that over 33% of Americans have made durable goods purchases to combat the disease. In addition, the disease has affected many consumers' purchasing habits as more time is spent at home with children.
FAQ
Are there any Manufacturing Processes that we should know before we can learn about Logistics?
No. It doesn't matter if you don't know anything about manufacturing before you learn about logistics. But, being familiar with manufacturing processes will give you a better understanding about how logistics works.
What is the difference between manufacturing and logistics
Manufacturing refers the process of producing goods from raw materials through machines and processes. Logistics encompasses the management of all aspects associated with supply chain activities such as procurement, production planning, distribution and inventory control. It also includes customer service. Sometimes manufacturing and logistics are combined to refer to a wider term that includes both the process of creating products as well as their delivery to customers.
What is the distinction between Production Planning or Scheduling?
Production Planning (PP), or production planning, is the process by which you determine what products are needed at any given time. Forecasting demand is one way to do this.
Scheduling involves the assignment of dates and times to tasks in order to complete them within the timeframe.
What does manufacturing industry mean?
Manufacturing Industries refers to businesses that manufacture products. Consumers are people who purchase these goods. This is accomplished by using a variety of processes, including production, distribution and retailing. These companies produce goods using raw materials and other equipment. This includes all types and varieties of manufactured goods, such as food items, clothings, building supplies, furnitures, toys, electronics tools, machinery vehicles, pharmaceuticals medical devices, chemicals, among others.
What are the products of logistics?
Logistics are the activities involved in moving goods from point A to point B.
They cover all aspects of transportation, such as packing, loading, transporting and unloading.
Logisticians make sure that the right product arrives at the right place at the correct time and in safe conditions. They provide information on demand forecasts as well stock levels, production schedules and availability of raw material.
They also keep track of shipments in transit, monitor quality standards, perform inventories and order replenishment, coordinate with suppliers and vendors, and provide support services for sales and marketing.
What is the role of a production manager?
Production planners ensure all aspects of the project are delivered within time and budget. They also ensure the quality of the product and service meets the client's requirements.
Statistics
- In 2021, an estimated 12.1 million Americans work in the manufacturing sector.6 (investopedia.com)
- In the United States, for example, manufacturing makes up 15% of the economic output. (twi-global.com)
- [54][55] These are the top 50 countries by the total value of manufacturing output in US dollars for its noted year according to World Bank.[56] (en.wikipedia.org)
- You can multiply the result by 100 to get the total percent of monthly overhead. (investopedia.com)
- Many factories witnessed a 30% increase in output due to the shift to electric motors. (en.wikipedia.org)
External Links
How To
How to Use 5S to Increase Productivity in Manufacturing
5S stands for "Sort", 'Set In Order", 'Standardize', & Separate>. Toyota Motor Corporation invented the 5S strategy in 1954. It allows companies to improve their work environment, thereby achieving greater efficiency.
The idea behind standardizing production processes is to make them repeatable and measurable. This means that tasks such as cleaning, sorting, storing, packing, and labeling are performed daily. This knowledge allows workers to be more efficient in their work because they are aware of what to expect.
Five steps are required to implement 5S: Sort, Set In Order, Standardize. Separate. Each step is a different action that leads to greater efficiency. By sorting, for example, you make it easy to find the items later. When you arrange items, you place them together. Next, organize your inventory into categories and store them in containers that are easily accessible. Finally, when you label your containers, you ensure everything is labeled correctly.
Employees will need to be more critical about their work. Employees must understand why they do certain tasks and decide if there's another way to accomplish them without relying on the old ways of doing things. In order to use the 5S system effectively, they must be able to learn new skills.
In addition to improving efficiency, the 5S system also increases morale and teamwork among employees. As they begin to see improvements, they feel motivated to continue working towards the goal of achieving higher levels of efficiency.