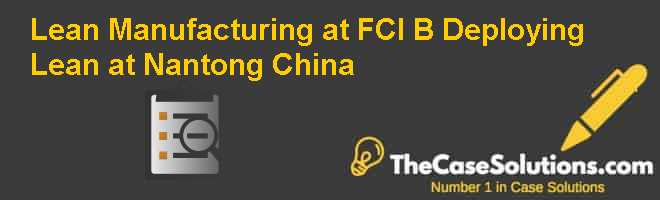
During the Great Recession, Ohio manufacturers lost a total of 166,000 manufacturing jobs. Ohio's manufacturing sector has shown some signs of recovery, but it has not been as fast as other states. Ohio's manufacturing job opportunities are still lower than they were prior to the recession.
Ohio's manufacturing jobs have declined due to increased competition from Europe and Japan. Manufacturers have been forced to become technologically more advanced and shed labor costs. The global economic climate is lukewarm which has led to job loss.
Ohio's workforce shortage is one the biggest challenges facing its manufacturers. There are many initiatives that can be taken to address the state's skilled labor shortage. These initiatives, which are isolated and fragmented, do not address all workforce challenges facing manufacturers. The Ohio Governor's Office of Workforce Transformation produced a special report on the workforce shortfall that recommended better collaboration between business and education. However, the report showed a disconnect in the school curriculum and the business needs.
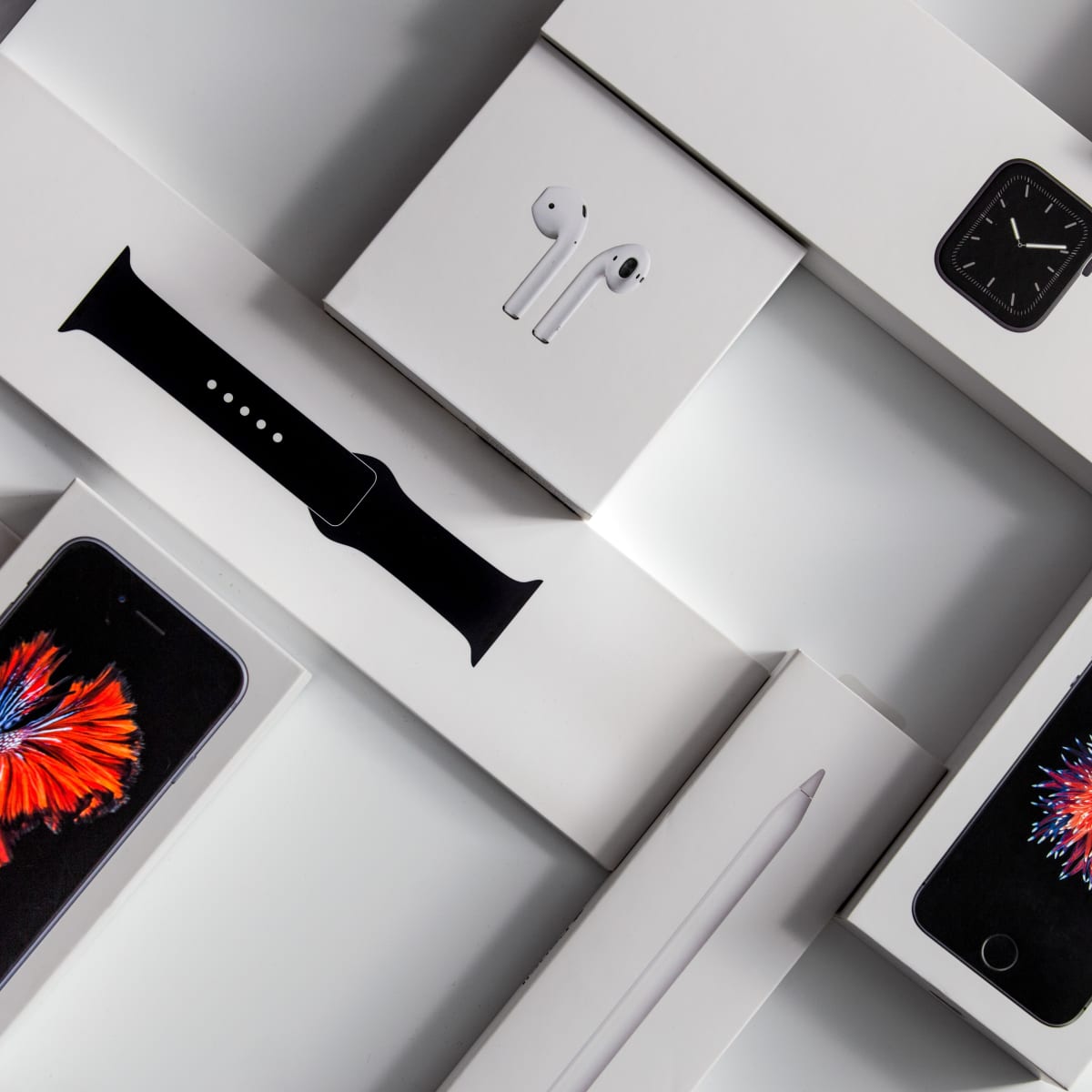
Ohio's workforce consists of a diverse, complex, multi-faceted and diverse group. Manufacturing workers are less likely to be represented by a union than workers in other industries in the state. However, unionized manufacturing jobs offer solid benefits and livable wages.
Ohio's manufacturing sector contributes significantly to its economy. Utilizing interstate highways and railways as well as inland waterways, manufacturers can distribute their goods at a competitive price. In addition, the state is a top exporter of goods. The state also produces natural gaz, which is a big draw for private investors.
Despite the fact that the state has been able to recover over 50,000 manufacturing jobs within the last four year, Kasich's term as president saw little improvement in job growth. Manufacturing job gains averaged 7 per cent in Kasich's first three years. Manufacturing jobs have dropped by 1,771 jobs in the last two years. These losses are due to the slowing economy, the auto industry, and lukewarm global demand.
Ohio is a top exporter for goods. The top export markets are the U.S.A., Canada, Mexico and the U.K. In the past year, exports decreased by $1.4 Billion. Ohio manufacturers are still concerned about trade policy. While trade policy changes may be helpful to certain workers, they will not address the whole range of problems.
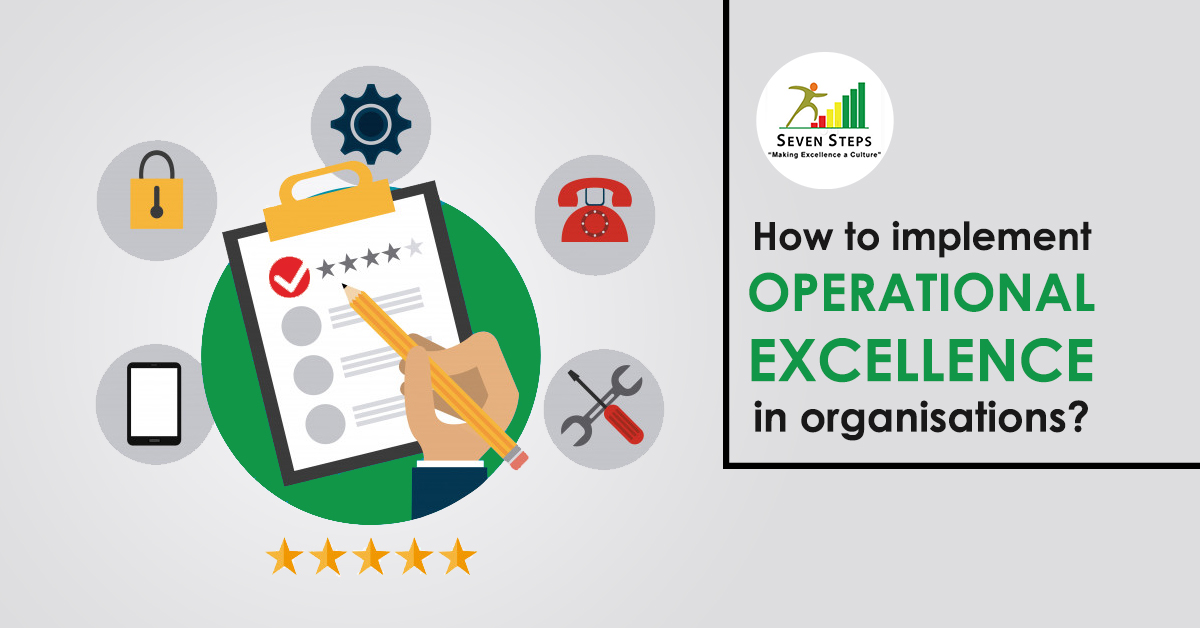
Ohio's manufacturing sector is still one of the most important. Manufacturing jobs can be a high-paying job for semi-skilled workers, even if they don't have post-secondary training. Wages have not kept up to the pace of Ohio's production. While manufacturing jobs are more lucrative than those in other industries, they are not sufficient to provide a middle-class lifestyle.
Ohio's manufacturing workforce consists of a diverse group of workers. To keep pace with the rest of the country, Ohio's manufacturing industry has been diversifying. The economy has become more service-oriented, and manufacturing is no longer the primary employer in Ohio. Manufacturers now focus more on international exposure, and developing skills for the future.
FAQ
What are my options for learning more about manufacturing
The best way to learn about manufacturing is through hands-on experience. However, if that's not possible, you can always read books or watch educational videos.
What is the distinction between Production Planning or Scheduling?
Production Planning (PP), also known as forecasting and identifying production capacities, is the process that determines what product needs to be produced at any particular time. This is accomplished by forecasting the demand and identifying production resources.
Scheduling involves the assignment of dates and times to tasks in order to complete them within the timeframe.
What does "warehouse" mean?
A warehouse is an area where goods are stored before being sold. It can be an indoor space or an outdoor area. In some cases it could be both indoors and outdoors.
Statistics
- (2:04) MTO is a production technique wherein products are customized according to customer specifications, and production only starts after an order is received. (oracle.com)
- Many factories witnessed a 30% increase in output due to the shift to electric motors. (en.wikipedia.org)
- Job #1 is delivering the ordered product according to specifications: color, size, brand, and quantity. (netsuite.com)
- [54][55] These are the top 50 countries by the total value of manufacturing output in US dollars for its noted year according to World Bank.[56] (en.wikipedia.org)
- According to the United Nations Industrial Development Organization (UNIDO), China is the top manufacturer worldwide by 2019 output, producing 28.7% of the total global manufacturing output, followed by the United States, Japan, Germany, and India.[52][53] (en.wikipedia.org)
External Links
How To
How to Use 5S to Increase Productivity in Manufacturing
5S stands for "Sort", 'Set In Order", 'Standardize', & Separate>. Toyota Motor Corporation developed the 5S method in 1954. It assists companies in improving their work environments and achieving higher efficiency.
The basic idea behind this method is to standardize production processes, so they become repeatable, measurable, and predictable. This means that daily tasks such as cleaning and sorting, storage, packing, labeling, and packaging are possible. Through these actions, workers can perform their jobs more efficiently because they know what to expect from them.
Five steps are required to implement 5S: Sort, Set In Order, Standardize. Separate. Each step requires a different action to increase efficiency. By sorting, for example, you make it easy to find the items later. You arrange items by placing them in an order. Once you have separated your inventory into groups and organized them, you will store these groups in easily accessible containers. You can also label your containers to ensure everything is properly labeled.
Employees will need to be more critical about their work. Employees must understand why they do certain tasks and decide if there's another way to accomplish them without relying on the old ways of doing things. To be successful in the 5S system, employees will need to acquire new skills and techniques.
The 5S method not only increases efficiency but also boosts morale and teamwork. They will feel motivated to strive for higher levels of efficiency once they start to see results.