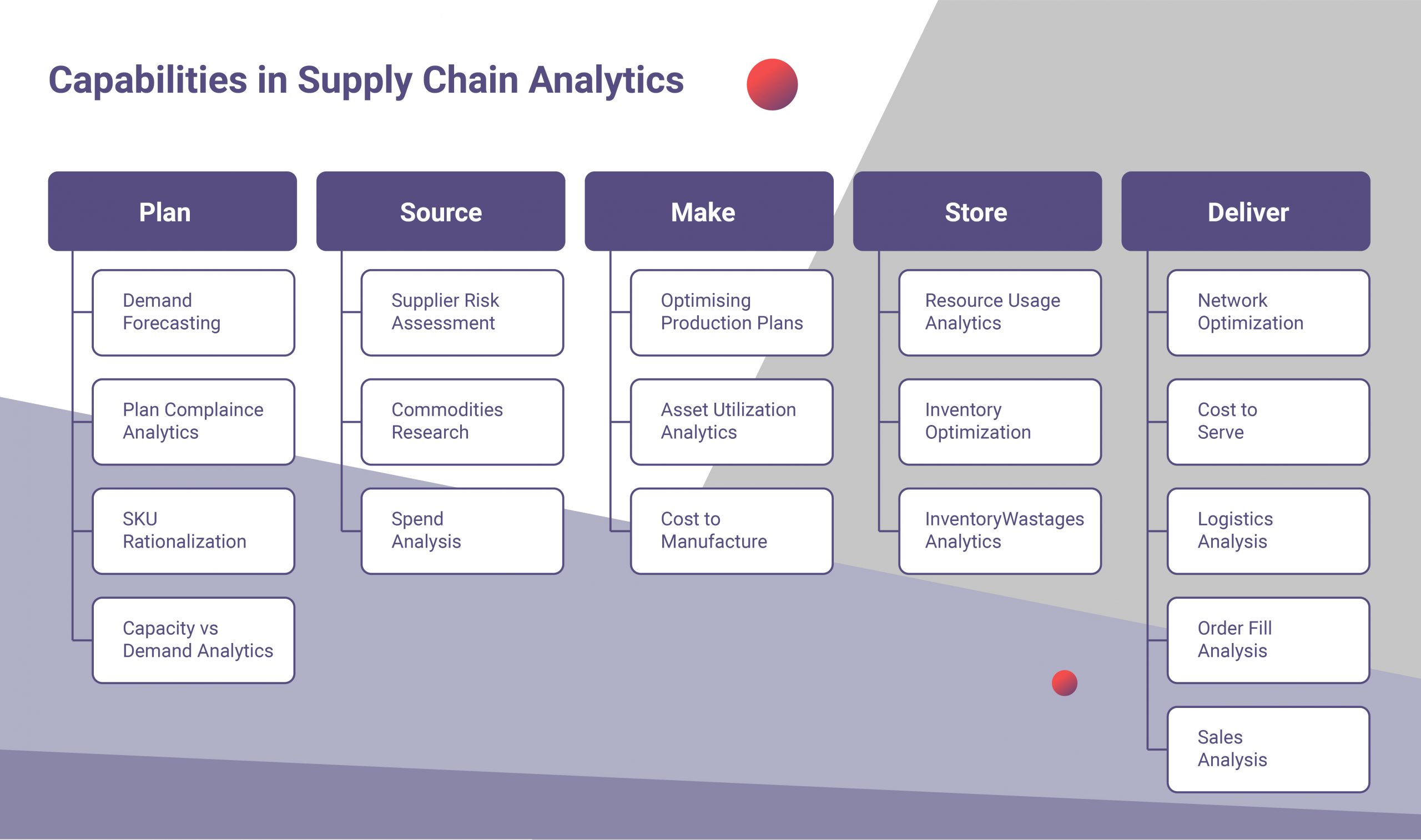
A Master of Science degree in Supply Chain Management can bring you many benefits. First, you will be able to take advantage of the increasing demand for supply chain managers. In addition to the benefits, this degree is also highly sought-after for its career potential. Learn about the different program options and education requirements to pursue this degree. A cost breakdown is also available. Learn more.
Career opportunities
An MBA in Supply Chain Management can help you become a supply chain management expert and a bridge to other positions. Supply chain jobs can bridge into other careers and are more common in today's economy. A master's in Supply Chain Management could give you a competitive edge as well as a lucrative career. This degree opens up many career possibilities in many industries. So it's important you understand how to maximize your degree.
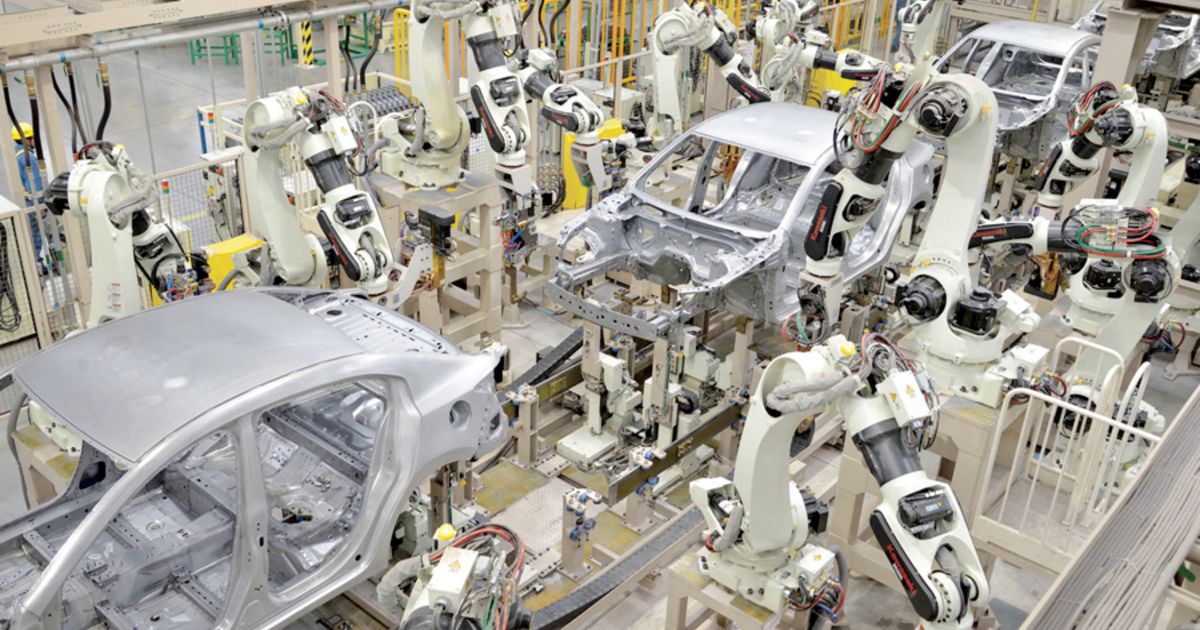
Education requirements
Rutgers Business School provides an online master in science supply chain administration program for 30 credits. This prepares students in one of most rapidly-growing fields of business. Many of the biggest companies around the globe consider supply chain management an essential skill and actively recruit students to their ranks. This program covers everything you need to know about supply chain management.
Programs available
If you'd like to become a supply chain manager, there are several Master of Science supply chains management programs available. These programs will prepare for a career as a supply chain manager and provide the expertise and skills necessary to succeed. The average Master's degree requires 30 credits. But, your program may require more. If you would like to be flexible with your time, you can choose to enroll in accelerated classes or asynchronous courses. For more information on the programs, contact the graduate schools directly to inquire about start dates, transferable credits, and financial aid acceptance.
Cost
A Master of Science in Supply Chain Management, or MSSCM, is significantly cheaper than other graduate degrees. Because the MSSCM program has fewer credits, graduates can get their top-notch graduate degree for half the price of other programs. In addition, generous scholarships provided by Saint Louis University's alumni and friends allow students to pay for their education with much less than they might expect.
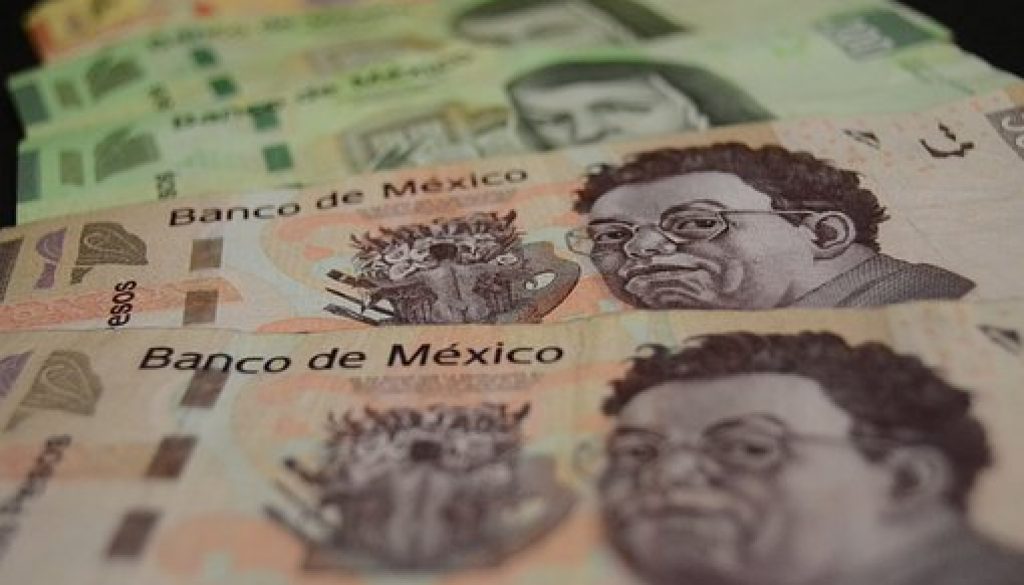
The average program length
30 credits are required to complete a Master of Science in Supply Chain Management (MSSCM). This curriculum is for professionals who work. Through simulations and case studies, the curriculum emphasizes practical learning. Students will get real-world exposure and can then apply what they have learned to their current workplace. The program is designed for students with a bachelor's degree in business, engineering, economics, or another related field.
FAQ
What is the role of a production manager?
Production planners make sure that every aspect of the project is delivered on-time, within budget, and within schedule. They ensure that the product or service is of high quality and meets client requirements.
How does a production planner differ from a project manager?
The difference between a product planner and project manager is that a planer is typically the one who organizes and plans the entire project. A production planner, however, is mostly involved in the planning stages.
What does "warehouse" mean?
A warehouse, or storage facility, is where goods are stored prior to being sold. It can be indoors or out. It may also be an indoor space or an outdoor area.
What's the difference between Production Planning & Scheduling?
Production Planning (PP), or production planning, is the process by which you determine what products are needed at any given time. This is accomplished by forecasting the demand and identifying production resources.
Scheduling involves the assignment of dates and times to tasks in order to complete them within the timeframe.
What is the difference between manufacturing and logistics
Manufacturing refers to the process of making goods using raw materials and machines. Logistics is the management of all aspects of supply chain activities, including procurement, production planning, distribution, warehousing, inventory control, transportation, and customer service. Manufacturing and logistics can often be grouped together to describe a larger term that covers both the creation of products, and the delivery of them to customers.
Do we need to know about Manufacturing Processes before learning about Logistics?
No. No. However, knowing about manufacturing processes will definitely give you a better understanding of how logistics works.
How can manufacturing overproduction be reduced?
In order to reduce excess production, you need to develop better inventory management methods. This would reduce time spent on activities such as purchasing, stocking, and maintaining excess stock. This could help us free up our time for other productive tasks.
One way to do this is to adopt a Kanban system. A Kanban Board is a visual display that tracks work progress. Kanban systems allow work items to move through different states until they reach their final destination. Each state is assigned a different priority.
When work is completed, it can be transferred to the next stage. But if a task remains in the beginning stages it will stay that way until it reaches its end.
This allows work to move forward and ensures that no work is missed. With a Kanban board, managers can see exactly how much work is being done at any given moment. This allows them to adjust their workflows based on real-time information.
Lean manufacturing is another option to control inventory levels. Lean manufacturing emphasizes eliminating waste in all phases of production. Waste includes anything that does not add value to the product. Some common types of waste include:
-
Overproduction
-
Inventory
-
Unnecessary packaging
-
Overstock materials
Manufacturers can increase efficiency and decrease costs by implementing these ideas.
Statistics
- In 2021, an estimated 12.1 million Americans work in the manufacturing sector.6 (investopedia.com)
- [54][55] These are the top 50 countries by the total value of manufacturing output in US dollars for its noted year according to World Bank.[56] (en.wikipedia.org)
- According to a Statista study, U.S. businesses spent $1.63 trillion on logistics in 2019, moving goods from origin to end user through various supply chain network segments. (netsuite.com)
- Many factories witnessed a 30% increase in output due to the shift to electric motors. (en.wikipedia.org)
- You can multiply the result by 100 to get the total percent of monthly overhead. (investopedia.com)
External Links
How To
How to Use Lean Manufacturing in the Production of Goods
Lean manufacturing is a management style that aims to increase efficiency and reduce waste through continuous improvement. It was first developed in Japan in the 1970s/80s by Taiichi Ahno, who was awarded the Toyota Production System (TPS), award from KanjiToyoda, the founder of TPS. Michael L. Watkins published the original book on lean manufacturing, "The Machine That Changed the World," in 1990.
Lean manufacturing, often described as a set and practice of principles, is aimed at improving the quality, speed, cost, and efficiency of products, services, and other activities. It emphasizes the elimination and minimization of waste in the value stream. Lean manufacturing can be described as just-in–time (JIT), total productive maintenance, zero defect (TPM), or even 5S. Lean manufacturing eliminates non-value-added tasks like inspection, rework, waiting.
Lean manufacturing improves product quality and costs. It also helps companies reach their goals quicker and decreases employee turnover. Lean manufacturing is a great way to manage the entire value chain including customers, suppliers, distributors and retailers as well as employees. Lean manufacturing practices are widespread in many industries. Toyota's philosophy has been a key driver of success in many industries, including automobiles and electronics.
Five basic principles of Lean Manufacturing are included in lean manufacturing
-
Define Value- Identify the added value your company brings to society. What makes you stand out from your competitors?
-
Reduce Waste – Eliminate all activities that don't add value throughout the supply chain.
-
Create Flow – Ensure that work flows smoothly throughout the process.
-
Standardize and simplify – Make processes as repeatable and consistent as possible.
-
Build Relationships - Establish personal relationships with both internal and external stakeholders.
Although lean manufacturing isn't a new concept in business, it has gained popularity due to renewed interest in the economy after the 2008 global financial crisis. Many businesses are now using lean manufacturing to improve their competitiveness. In fact, some economists believe that lean manufacturing will be an important factor in economic recovery.
Lean manufacturing, which has many benefits, is now a standard practice in the automotive industry. These include better customer satisfaction and lower inventory levels. They also result in lower operating costs.
Any aspect of an enterprise can benefit from Lean manufacturing. However, it is particularly useful when applied to the production side of an organization because it ensures that all steps in the value chain are efficient and effective.
There are three main types of lean manufacturing:
-
Just-in-Time Manufacturing (JIT): This type of lean manufacturing is commonly referred to as "pull systems." JIT refers to a system in which components are assembled at the point of use instead of being produced ahead of time. This approach aims to reduce lead times, increase the availability of parts, and reduce inventory.
-
Zero Defects Manufacturing (ZDM),: ZDM is a system that ensures no defective units are left the manufacturing facility. You should repair any part that needs to be repaired during an assembly line. This applies to finished products, which may need minor repairs before they are shipped.
-
Continuous Improvement: Continuous Improvement aims to improve efficiency by continually identifying problems and making adjustments to eliminate or minimize waste. Continuous improvement involves continuous improvement of processes and people as well as tools.