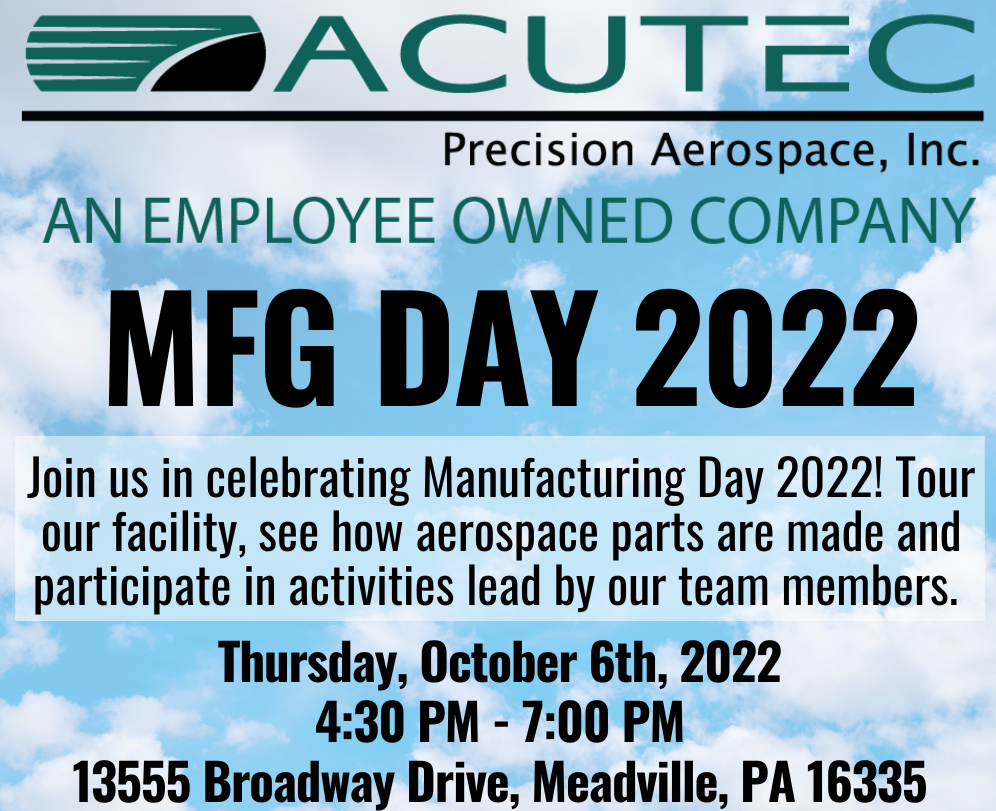
Apparel manufacturers today face a unique challenge in meeting the diverse demands of their customers. These consumers differ in terms of physiographics as well as socioeconomics. They also have diverse preferences, which can be difficult to predict. Information is also easier to access as consumers are more aware of the differences between products. They are also more likely to purchase high-fashion, expensive items.
Production efficiency
Increasing production efficiency in apparel manufacture is a key element in the overall strategy of apparel manufacturers. Because the clothing industry relies on human labor, as well as changing fashion trends, it is vital to plan production in order to keep up with the demands of the market and consumers. Apparel manufacturers must be flexible enough to meet global demands and maintain a short product cycle. Apparel producers should not only plan for new products but also evaluate the efficiency and implementation of digital technologies. This can help reduce the product development time from months to just days. The planning process should include critical path analysis.
Although the apparel manufacturing industry is very labor-intensive, it is not impossible to increase production efficiency. However, achieving this goal requires a combination of the right tools and proper management. For example, an increase of just 10 to 15% in efficiency can lead to a 3-5% increase in EBITDA. In addition, an increase in efficiency can increase wages for workers and enhance the country's competitiveness in the global marketplace.
Layering fabrics
Fabric layering is a technique used in apparel manufacture. This involves placing a pattern over a laid fabric. The pattern can either be drawn manually or by using a plotter. The pattern components can be laid in the markers. After that, they are cut with a straight blade or other cutting method.
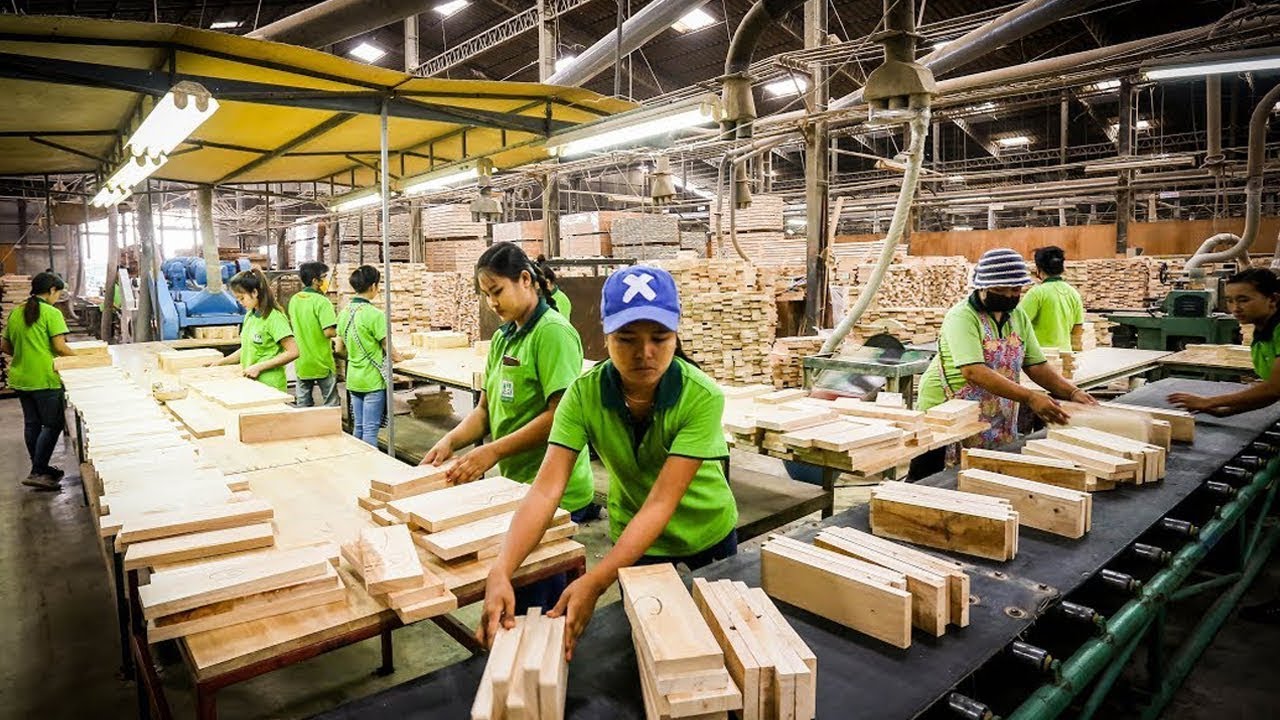
The fabric will be spread out evenly during this step. You can lay it out in a heap or with superimposed layers and the cutting marker. The maximum cut width is the fabric width less the needle marks and the selvedge. Fabric utilization is the area of fabric used. The two types of layout are half-garment lay and whole-garment lay. Half-garment Lay involves placing fabric on only one side of a garment piece. Whole-garment Lay involves covering fabric on both sides. However, whole-garment lay consumes more fabric.
Cutting
A cutting is the use of cutting blades to cut specific pieces of fabric into smaller pieces. Fabric accounts for 60-70 percent of the price of a garment. It is therefore important that all of the fabric be used. Apparel manufacturing should have a strict control system to ensure that every inch is used.
The process of cutting fabric begins with spreading the fabric over a large table. In mass production, the fabric is spread over a number layers. Based on how many garments are to be made and how thick the fabric is, the cutting master will determine the amount of layers that should be spread over a garment. After the fabric has been spread it is measured to determine the maximum cutting width.
Pressing
Pressing is an important process in the manufacture of apparel. It controls the appearance of garments and helps them to maintain their comfort. This is done in a factory. It can be manually or automated. Software can control the level of automation. Programming a press can allow it to follow specific instructions. Automating pressing can help reduce human error in apparel manufacturing factories. The increased number of fabric and fiber varieties will require more precise temperature and pressure control.
To soften the fibers of a garment, heat is used to press it. The garment's shape is stabilized by the softened fibers. To avoid damage to the yarns or fibers, it is important that you choose the right temperature.
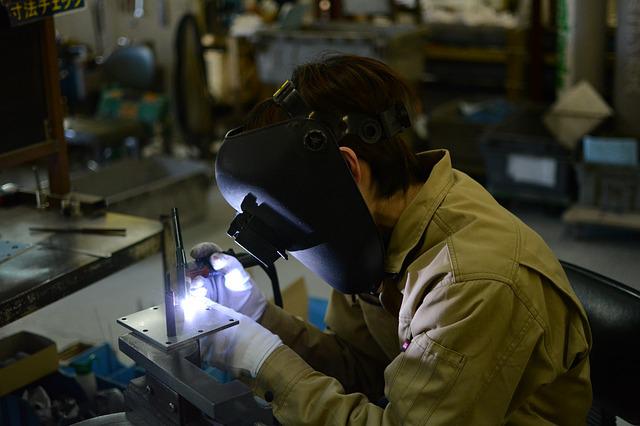
Minimum order quantity
When looking for clothing manufacturers, be sure to check the Minimum Order Quantity or MOQ of the factory. Many garment factories will not produce your garments without a minimum order amount. The MOQ varies from factory to factory and depends on the technical characteristics of your designs. Some factories are able to accept orders up to 100 items. Others require orders over a thousand.
Most manufacturers need to have a minimum order quantity (MOQ), especially if they deal in bulk products. This quantity is essential for manufacturers to be profitable. It helps them keep their costs down and keeps out small businesses that are not looking to place large orders. This is especially important for custom orders.
FAQ
What is the difference between a production planner and a project manager?
The difference between a product planner and project manager is that a planer is typically the one who organizes and plans the entire project. A production planner, however, is mostly involved in the planning stages.
What are my options for learning more about manufacturing
Hands-on experience is the best way to learn more about manufacturing. You can read books, or watch instructional videos if you don't have the opportunity to do so.
What is the importance of logistics in manufacturing?
Logistics is an integral part of every business. Logistics can help you achieve amazing results by helping to manage product flow from raw materials to finished products.
Logistics plays a significant role in reducing cost and increasing efficiency.
What do we need to know about Manufacturing Processes in order to learn more about Logistics?
No. No. It is important to know about the manufacturing processes in order to understand how logistics works.
What is the job of a logistics manger?
Logistics managers are responsible for ensuring that all goods arrive in perfect condition and on time. This is done through his/her expertise and knowledge about the company's product range. He/she must also ensure sufficient stock to meet the demand.
Statistics
- In 2021, an estimated 12.1 million Americans work in the manufacturing sector.6 (investopedia.com)
- According to a Statista study, U.S. businesses spent $1.63 trillion on logistics in 2019, moving goods from origin to end user through various supply chain network segments. (netsuite.com)
- According to the United Nations Industrial Development Organization (UNIDO), China is the top manufacturer worldwide by 2019 output, producing 28.7% of the total global manufacturing output, followed by the United States, Japan, Germany, and India.[52][53] (en.wikipedia.org)
- You can multiply the result by 100 to get the total percent of monthly overhead. (investopedia.com)
- Many factories witnessed a 30% increase in output due to the shift to electric motors. (en.wikipedia.org)
External Links
How To
How to Use Six Sigma in Manufacturing
Six Sigma is "the application statistical process control (SPC), techniques for continuous improvement." Motorola's Quality Improvement Department developed it at their Tokyo plant in Japan in 1986. Six Sigma's basic concept is to improve quality and eliminate defects through standardization. Since there are no perfect products, or services, this approach has been adopted by many companies over the years. The main goal of Six Sigma is to reduce variation from the mean value of production. This means that if you take a sample of your product, then measure its performance against the average, you can find out what percentage of the time the process deviates from the norm. If you notice a large deviation, then it is time to fix it.
The first step toward implementing Six Sigma is understanding how variability works in your business. Once you have a good understanding of the basics, you can identify potential sources of variation. Also, you will need to identify the sources of variation. Random variations happen when people make errors; systematic variations are caused externally. These are, for instance, random variations that occur when widgets are made and some fall off the production line. It would be considered a systematic problem if every widget that you build falls apart at the same location each time.
Once you have identified the problem, you can design solutions. This could mean changing your approach or redesigning the entire process. Test them again once you've implemented the changes. If they don't work, you will need to go back to the drawing boards and create a new plan.