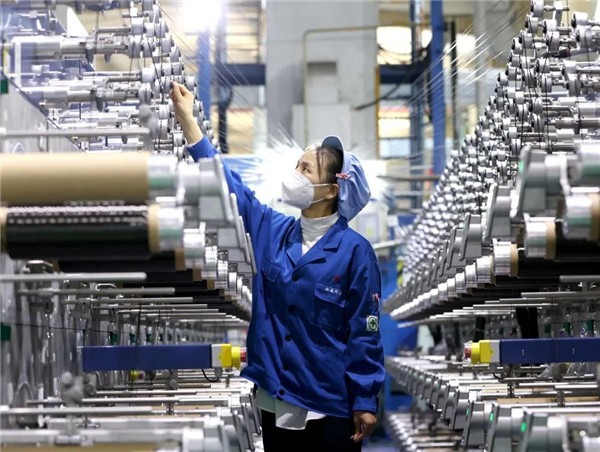
The National Association of Manufacturers, founded in 1898, is a trade organization that represents close to 14,000 member businesses from every industry sector in the U.S. NAM works hard to ensure success for 12 million American manufacturer. It works to promote new industries and increase awareness of manufacturing. NAM has several offices in the United States.
NAM is the nation’s most prominent advocate for manufacturers. It consists of small and medium-sized manufacturers. It supports advanced manufacturing and new industries. NAM also plays a crucial role in Washington policymaking. Its executives are responsible for reducing regulatory burdens and supporting trade and export. Washington, D.C., is where NAM headquarters are located. The NAM's executive team is skilled in developing and researching products and services that increase the manufacturers' competitiveness.
Texas Association of Manufacturers (TAM), applauded SB 1's passage by the 84th Legislature. The bill will provide broad tax relief to Texas businesses, which will help them grow. Senator Bill Nelson, and Representative Bill Bonnen are sponsoring the bill. The legislation also addresses the state’s tax code, Chapter 312 which allows temporary tax exemptions.
Texas' aerospace and aircraft manufacturing sectors are a large part of the state’s economic activity. It provides nearly 49 billion dollars in economic activity and 200,000 jobs. To keep its strong position in the state, the industry must be sustainable. The reform of TSCA is crucial to ensure the sector's growth and competitiveness. AMT's USMTO assistance program assists member companies in setting up business operations in Brazil. The USMTO program generated more than $400,000,000 in manufacturing orders in May.
Texas's aerospace industry and aircraft manufacturing sector need to be competitive in order for Texas to continue to create jobs and generate revenue. The sector's efforts have been important in strengthening Texas' manufacturing sector.
Texas Association of Manufacturers is in favor of Chapter 312 of Texas Tax Code being renewed. The Association also supports payments in the Operating Reserve Demand Curve. These payments help manufacturers pay for dispatchable generation, which is essential to ensure the security of the electricity grid. After Winter Storm Uri, the ORDC payments were expanded due to changes in "phase one" operations of the Public Utility Commission.
AMT is a leading trade group in the United States. It has offices located in more than 30 US cities. Its senior executives have extensive experience in both public and private policy. Its mission is to promote advanced manufacturing and technology. It is responsible for regulatory convergence between America and the European Union. It works to protect and promote manufacturers in every industrial sector. It has established several industry-specific boards, including one that is for small and medium-sized businesses. It also promotes technology and innovation.
AMT's new video introduces "MT Ambassadors," young professionals who educate others about manufacturing careers. It also promotes its USMTO Program, which assists member companies to explore Brazil. The Top Shops conference and Top Shops program help manufacturers identify and benchmark their businesses. The Association for Manufacturing Technology also collaborates with it to encourage interoperability within the manufacturing system. The MTConnect program improves the capability of manufacturers to share and transmit data across various manufacturing technologies.
FAQ
What's the difference between Production Planning & Scheduling?
Production Planning (PP), also known as forecasting and identifying production capacities, is the process that determines what product needs to be produced at any particular time. Forecasting and identifying production capacity are two key elements to this process.
Scheduling refers the process by which tasks are assigned dates so that they can all be completed within the given timeframe.
What makes a production planner different from a project manger?
The major difference between a Production Planner and a Project Manager is that a Project Manager is often the person responsible for organizing and planning the entire project. While a Production Planner is involved mainly in the planning stage,
What does the term manufacturing industries mean?
Manufacturing Industries are businesses that produce products for sale. These products are sold to consumers. These companies use various processes such as production, distribution, retailing, management, etc., to fulfill this purpose. They produce goods from raw materials by using machines and other machinery. This covers all types of manufactured goods including clothing, food, building supplies and furniture, as well as electronics, tools, machinery, vehicles and pharmaceuticals.
What is manufacturing and logistics?
Manufacturing is the production of goods using raw materials. Logistics encompasses the management of all aspects associated with supply chain activities such as procurement, production planning, distribution and inventory control. It also includes customer service. Sometimes manufacturing and logistics are combined to refer to a wider term that includes both the process of creating products as well as their delivery to customers.
What is the role and responsibility of a Production Planner?
Production planners ensure that all project aspects are completed on time, within budget and within the scope. They make sure that the product and services meet client expectations.
How can we increase manufacturing efficiency?
The first step is to determine the key factors that impact production time. Next, we must find ways to improve those factors. You can start by identifying the most important factors that impact production time. Once you have identified them, it is time to identify solutions.
What are the logistics products?
Logistics is the process of moving goods from one point to another.
They encompass all aspects transport, including packaging and loading, transporting, storage, unloading.
Logisticians make sure that the right product arrives at the right place at the correct time and in safe conditions. Logisticians assist companies in managing their supply chains by providing information such as demand forecasts, stock levels and production schedules.
They also keep track of shipments in transit, monitor quality standards, perform inventories and order replenishment, coordinate with suppliers and vendors, and provide support services for sales and marketing.
Statistics
- You can multiply the result by 100 to get the total percent of monthly overhead. (investopedia.com)
- It's estimated that 10.8% of the U.S. GDP in 2020 was contributed to manufacturing. (investopedia.com)
- [54][55] These are the top 50 countries by the total value of manufacturing output in US dollars for its noted year according to World Bank.[56] (en.wikipedia.org)
- In 2021, an estimated 12.1 million Americans work in the manufacturing sector.6 (investopedia.com)
- In the United States, for example, manufacturing makes up 15% of the economic output. (twi-global.com)
External Links
How To
How to Use lean manufacturing in the Production of Goods
Lean manufacturing (or lean manufacturing) is a style of management that aims to increase efficiency, reduce waste and improve performance through continuous improvement. It was developed by Taiichi Okono in Japan, during the 1970s & 1980s. TPS founder Kanji Takoda awarded him the Toyota Production System Award (TPS). Michael L. Watkins published the "The Machine That Changed the World", the first book about lean manufacturing. It was published in 1990.
Lean manufacturing can be described as a set or principles that are used to improve quality, speed and cost of products or services. It emphasizes reducing defects and eliminating waste throughout the value chain. Lean manufacturing is called just-in-time (JIT), zero defect, total productive maintenance (TPM), or 5S. Lean manufacturing eliminates non-value-added tasks like inspection, rework, waiting.
Lean manufacturing is a way for companies to achieve their goals faster, improve product quality, and lower costs. Lean manufacturing can be used to manage all aspects of the value chain. Customers, suppliers, distributors, retailers and employees are all included. Many industries worldwide use lean manufacturing. Toyota's philosophy has been a key driver of success in many industries, including automobiles and electronics.
Five principles are the basis of lean manufacturing:
-
Define Value- Identify the added value your company brings to society. What makes you stand out from your competitors?
-
Reduce waste - Stop any activity that isn't adding value to the supply chains.
-
Create Flow. Ensure that your work is uninterrupted and flows seamlessly.
-
Standardize & Simplify - Make processes as consistent and repeatable as possible.
-
Develop Relationships: Establish personal relationships both with internal and external stakeholders.
Lean manufacturing is not a new concept, but it has been gaining popularity over the last few years due to a renewed interest in the economy following the global financial crisis of 2008. To increase their competitiveness, many businesses have turned to lean manufacturing. Many economists believe lean manufacturing will play a major role in economic recovery.
Lean manufacturing is becoming a popular practice in automotive. It has many advantages. These include higher customer satisfaction levels, reduced inventory levels as well as lower operating costs.
It can be applied to any aspect of an organisation. Lean manufacturing is most useful in the production sector of an organisation because it ensures that each step in the value-chain is efficient and productive.
There are three main types of lean manufacturing:
-
Just-in Time Manufacturing, (JIT): This kind of lean manufacturing is also commonly known as "pull-systems." JIT stands for a system where components are assembled on the spot rather than being made in advance. This method reduces lead times, increases availability, and decreases inventory.
-
Zero Defects Manufacturing: ZDM ensures that no defective units leave the manufacturing plant. If a part needs to be fixed during the assembly line, it should be repaired rather than scrapped. This applies to finished goods that may require minor repairs before shipment.
-
Continuous Improvement: Continuous Improvement aims to improve efficiency by continually identifying problems and making adjustments to eliminate or minimize waste. Continuous improvement involves continuous improvement of processes and people as well as tools.