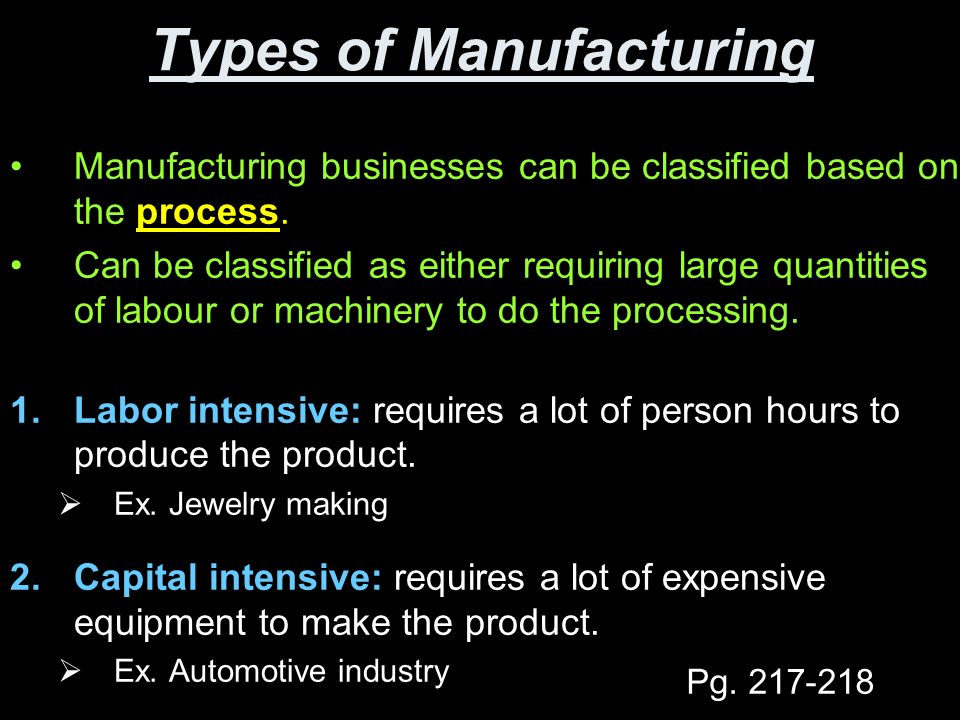
Typically, tool and die makers work in machine shops. They can operate milling machines and lathes as well other types. They repair tools and dies that are used by machinists. They might also design tools to be sold.
Tool and Die makers must adhere to strict quality control and precision in all of their work. They ensure that their work is accurate and inspect finished products. Tool and die makers may work with engineers to improve processes. They may also visit the plant of a customer to test the tool's performance. They are required to keep their work space clean and organized. They may also wear protective gear. They might suggest tools that will make the process more efficient.
Tool and diemakers usually work 40 hours a week. They may also be expected do moderately heavy lifting. They must also have strong academic backgrounds. Employers prefer associate's or bachelors degrees in related fields. They might also be eligible for formal training on the job or apprenticeship programs.
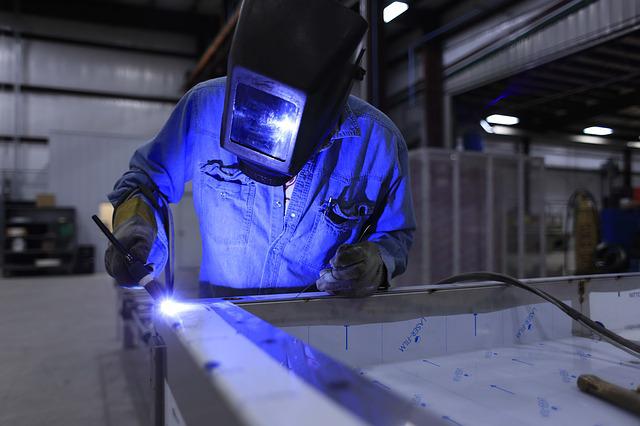
Tool and die-makers typically complete four-year apprenticeships with their employers. They are trained by an experienced worker while they're in the apprenticeship program. They also receive technical college courses in the evening. The program includes hands-on training, as well as classroom instruction. They may also be given the chance to program computer controlled machine tools. They may also have the opportunity to advance to supervisory or managerial positions.
Most tool and die-makers have a high school diploma. A degree in engineering or physics may also be an option. They may also have some prior training in science or math. This training is often very useful.
Good eyesight is crucial for tool and die-makers. They need to be able to concentrate and have patience. They need to be strong enough to lift heavy machinery. They should be hardworking and able to lift heavy items. They should be capable of reading engineering drawings and specifications. They should also have excellent interpersonal skills. They must have excellent computer skills. They may be required to maintain computer numerically control (CNC) machines.
Tool and die makers need to have an analytical mind. They must understand how tools work and how to fix them. They should also possess problem-solving and mechanical skills. They might also need to learn new machining methods. They must be skilled in digital skills such computer-aided design and manufacturing (CAM) software. They should also be skilled in sales. They must be able work with and independently.
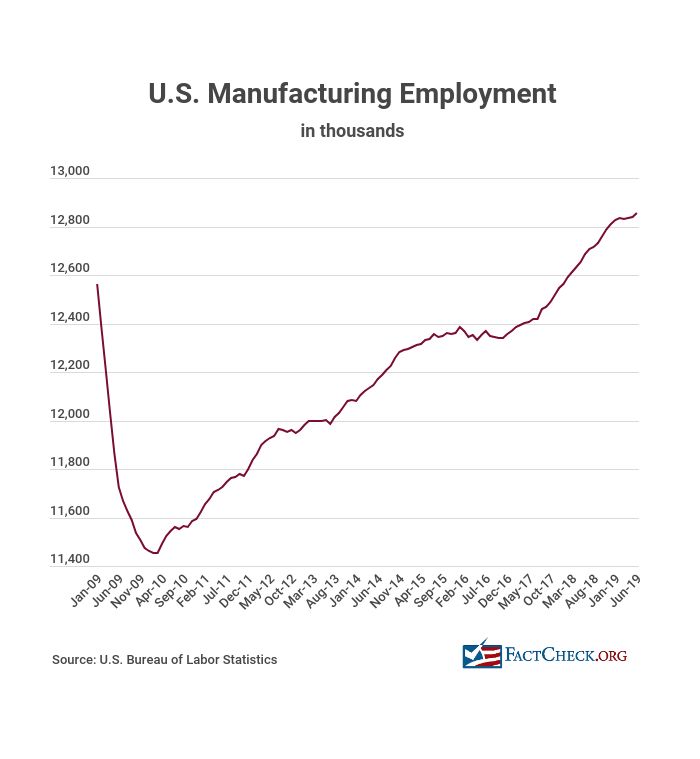
Apprentices can expect to work 40 hours per semaine during an apprenticeship program. They attend classroom courses at night and work on a job during the day. They eventually take on more challenging assignments. A high school diploma is required for most apprenticeships. They will also need to take courses in science, math, and technology.
Some tool and diemakers go on to get a master's or bachelor's degree. The average salary of tool and die makers is $56,186. However, their job prospects are expected to decrease in the future due to automation.
FAQ
Is it possible to automate certain parts of manufacturing
Yes! Yes. The Egyptians discovered the wheel thousands and years ago. Today, robots assist in the assembly of lines.
There are many applications for robotics in manufacturing today. These include:
-
Robots for assembly line
-
Robot welding
-
Robot painting
-
Robotics inspection
-
Robots that produce products
There are many other examples of how manufacturing could benefit from automation. For example, 3D printing allows us to make custom products without having to wait for weeks or months to get them manufactured.
What is meant by manufacturing industries?
Manufacturing Industries refers to businesses that manufacture products. Consumers are the people who purchase these products. These companies use a variety processes such as distribution, retailing and management to accomplish their purpose. They create goods from raw materials, using machines and various other equipment. This includes all types manufactured goods such as clothing, building materials, furniture, electronics, tools and machinery.
Are there any Manufacturing Processes that we should know before we can learn about Logistics?
No. No. However, knowing about manufacturing processes will definitely give you a better understanding of how logistics works.
How can efficiency in manufacturing be improved?
First, we need to identify which factors are most critical in affecting production times. The next step is to identify the most important factors that affect production time. You can start by identifying the most important factors that impact production time. Once you identify them, look for solutions.
What are the responsibilities of a logistic manager?
A logistics manager makes sure that all goods are delivered on-time and in good condition. This is done using his/her knowledge of the company's products. He/she also needs to ensure adequate stock to meet demand.
Statistics
- According to the United Nations Industrial Development Organization (UNIDO), China is the top manufacturer worldwide by 2019 output, producing 28.7% of the total global manufacturing output, followed by the United States, Japan, Germany, and India.[52][53] (en.wikipedia.org)
- Job #1 is delivering the ordered product according to specifications: color, size, brand, and quantity. (netsuite.com)
- You can multiply the result by 100 to get the total percent of monthly overhead. (investopedia.com)
- (2:04) MTO is a production technique wherein products are customized according to customer specifications, and production only starts after an order is received. (oracle.com)
- Many factories witnessed a 30% increase in output due to the shift to electric motors. (en.wikipedia.org)
External Links
How To
How to Use Six Sigma in Manufacturing
Six Sigma can be described as "the use of statistical process control (SPC), techniques to achieve continuous improvement." Motorola's Quality Improvement Department created Six Sigma at their Tokyo plant, Japan in 1986. Six Sigma's main goal is to improve process quality by standardizing processes and eliminating defects. Since there are no perfect products, or services, this approach has been adopted by many companies over the years. Six Sigma seeks to reduce variation between the mean production value. This means that you can take a sample from your product and then compare its performance to the average to find out how often the process differs from the norm. If you notice a large deviation, then it is time to fix it.
Understanding how variability works in your company is the first step to Six Sigma. Once you understand this, you can then identify the causes of variation. This will allow you to decide if these variations are random and systematic. Random variations happen when people make errors; systematic variations are caused externally. For example, if you're making widgets, and some of them fall off the assembly line, those would be considered random variations. But if you notice that every widget you make falls apart at the exact same place each time, this would indicate that there is a problem.
After identifying the problem areas, you will need to devise solutions. That solution might involve changing the way you do things or redesigning the process altogether. To verify that the changes have worked, you need to test them again. If they don't work you need to rework them and come up a better plan.