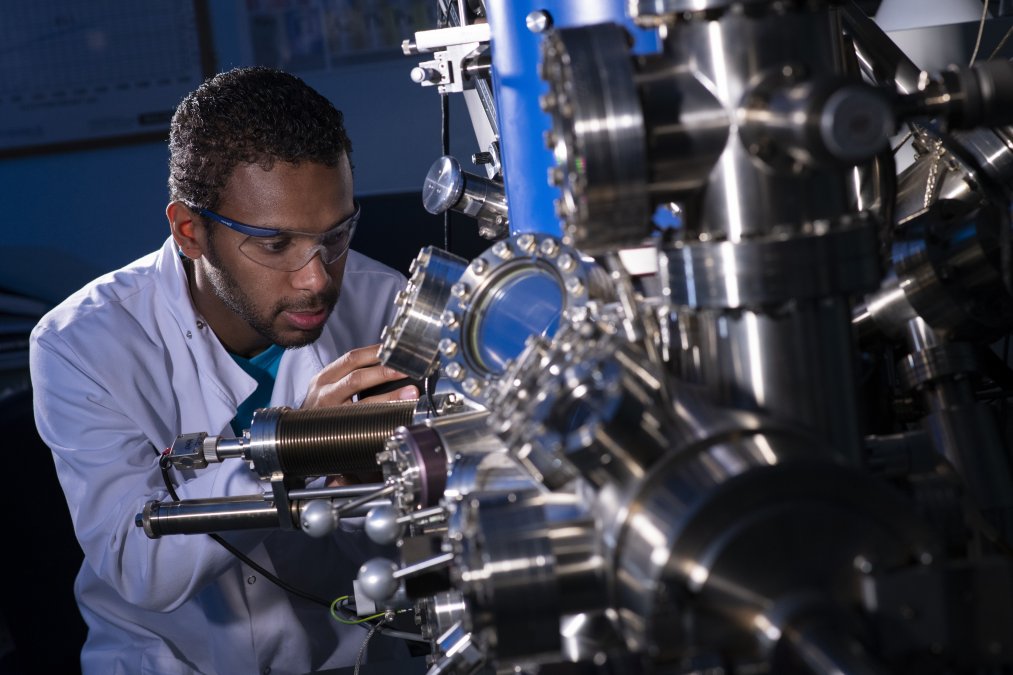
Advanced manufacturing is where companies use innovative technologies to produce better products and processes. These technologies are often referred to as cutting-edge, innovative, and advanced. Companies are increasingly incorporating these technologies into their business operations. Robotics and material deposition are some of these technologies. These technologies can be found out more.
Additive manufacturing
Advanced manufacturing through additive manufacturing is the future for many manufacturing businesses. This type involves additive manufacturing technologies also known as 3D printers. Several advantages of this type of manufacturing include increased flexibility and decreased inventory costs. This type of manufacturing also makes it less costly to import labor-intensive parts or components.
Innovations in additive manufacturing technology have greatly increased the speed of manufacturing. They allow businesses to respond quickly to supply-chain disruptions. They can create custom parts in a matter of hours, or even days. This process is especially valuable in industries that experience supply-chain problems. Advanced manufacturing can even produce parts with complex geometries.
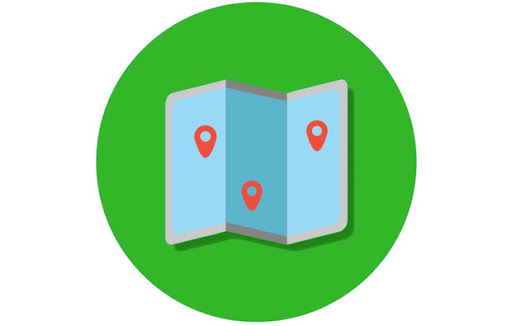
A manufacturer can also make very small quantities. You can use additive manufacturing to make custom dental appliances. The process can also be used to create complex structures such as internal heat channels. Advanced manufacturing by additive manufacturing can also be used to reduce inventory and create specialized parts. It can reduce materials costs by ninety-five percent and energy consumption by half.
Robotics
The potential for advanced robotics is recognized by most industrial producers and they are eager to incorporate them in their production lines. However, they are not satisfied with their current progress in implementation and performance. They point to the limitations and high costs of current technology as the barriers to greater deployment. They also lack key enablers to fully deploy advanced robotics in their factories.
Advanced robotics integration requires that manufacturers evaluate their system architecture. These systems should include infrastructure, analytics, data management, workflow management, and data storage. When these capabilities are in place companies can begin to look for strategic robotics partners. These partners can help companies determine the best technologies and processes for their operation. Simulating models is a great way to achieve this in robotics.
The use of advanced robotics is rapidly evolving across numerous industries. Robotic automation can be applied in many areas, such as aerospace, medical and automotive manufacturing. This technology has transformed the manufacturing sector. This technology not only lowers human labor costs but also saves money by running 24 hours a night and not requiring lights.
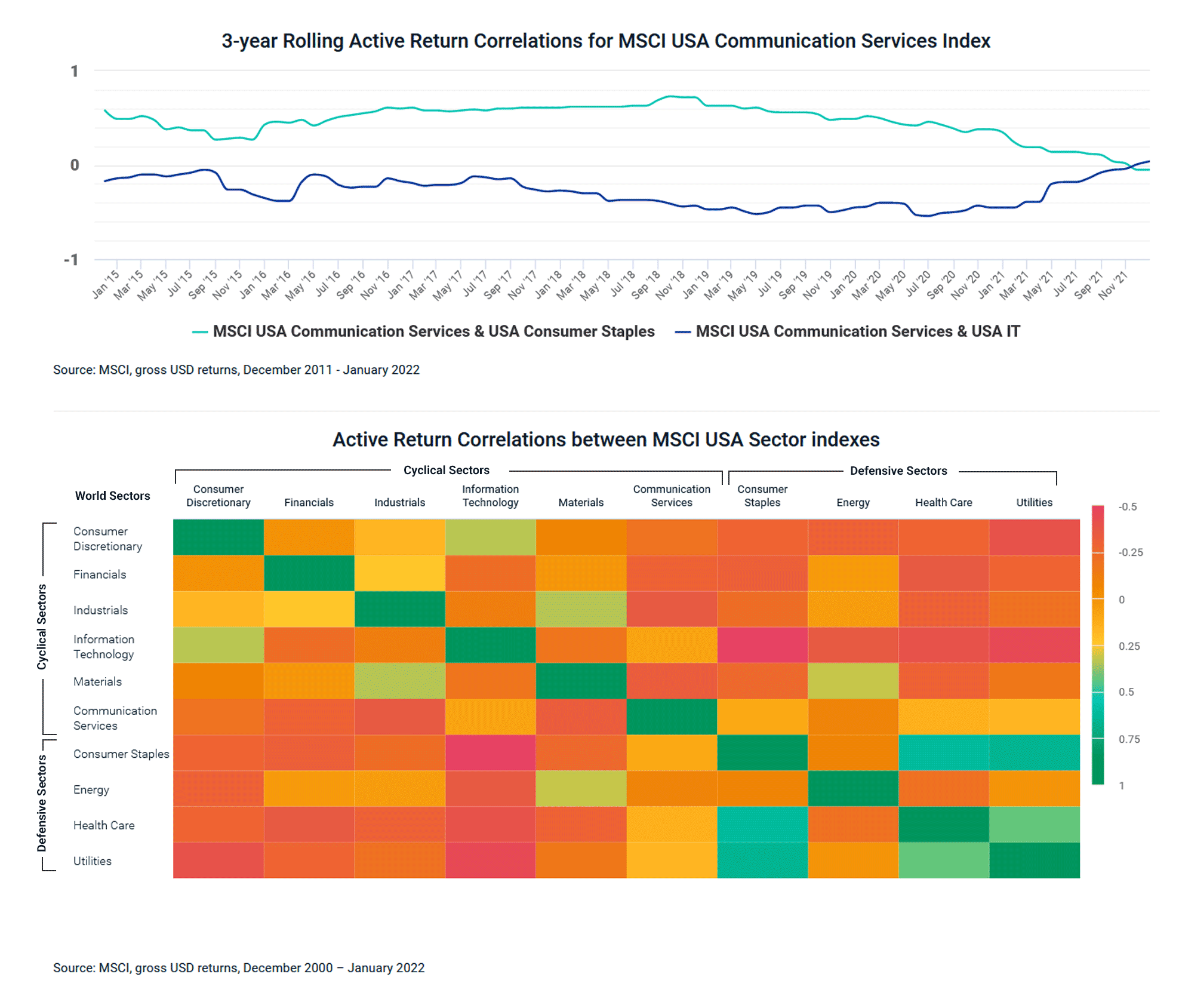
Material deposition
Material deposition is a crucial technique in advanced manufacturing. The process involves using a combination of laser beams and arc plasma energies to deposit thin films of a material on a target. Powder or wire are typically used as the substrate, and deposition occurs in an inert gas or vacuum. Other energy sources could also be utilized.
Plasma metal deposition, which utilizes a plasma source as a method to deposit metals, is one of most promising direct-energy techniques. This process can be used to create large, complex parts from wire, powder or both. This process is more efficient and produces smaller parts with a shorter leadtime.
This process is applicable to ceramics as well as polymers and metals. Metals are typically used in wire and powder forms.
FAQ
What skills does a production planner need?
Production planners must be flexible, organized, and able handle multiple tasks. You must also be able to communicate effectively with clients and colleagues.
What does it take for a logistics enterprise to succeed?
It takes a lot of skills and knowledge to run a successful logistics business. You must have good communication skills to interact effectively with your clients and suppliers. You need to understand how to analyze data and draw conclusions from it. You must be able manage stress and pressure under pressure. To improve efficiency, you must be innovative and creative. You need to have strong leadership qualities to motivate team members and direct them towards achieving organizational goals.
It is important to be organized and efficient in order to meet tight deadlines.
What are the 4 types of manufacturing?
Manufacturing refers to the transformation of raw materials into useful products by using machines and processes. It includes many different activities like designing, building and testing, packaging, shipping and selling, as well as servicing.
How can I find out more about manufacturing?
The best way to learn about manufacturing is through hands-on experience. However, if that's not possible, you can always read books or watch educational videos.
What is the difference between Production Planning and Scheduling?
Production Planning (PP) is the process of determining what needs to be produced at any given point in time. This is accomplished by forecasting the demand and identifying production resources.
Scheduling is the process of assigning specific dates to tasks so they can be completed within the specified timeframe.
Statistics
- It's estimated that 10.8% of the U.S. GDP in 2020 was contributed to manufacturing. (investopedia.com)
- In 2021, an estimated 12.1 million Americans work in the manufacturing sector.6 (investopedia.com)
- [54][55] These are the top 50 countries by the total value of manufacturing output in US dollars for its noted year according to World Bank.[56] (en.wikipedia.org)
- (2:04) MTO is a production technique wherein products are customized according to customer specifications, and production only starts after an order is received. (oracle.com)
- Many factories witnessed a 30% increase in output due to the shift to electric motors. (en.wikipedia.org)
External Links
How To
How to use Lean Manufacturing in the production of goods
Lean manufacturing (or lean manufacturing) is a style of management that aims to increase efficiency, reduce waste and improve performance through continuous improvement. It was developed in Japan during the 1970s and 1980s by Taiichi Ohno, who received the Toyota Production System (TPS) award from TPS founder Kanji Toyoda. Michael L. Watkins published the book "The Machine That Changed the World", which was the first to be published about lean manufacturing.
Lean manufacturing, often described as a set and practice of principles, is aimed at improving the quality, speed, cost, and efficiency of products, services, and other activities. It emphasizes the elimination of defects and waste throughout the value stream. Lean manufacturing is called just-in-time (JIT), zero defect, total productive maintenance (TPM), or 5S. Lean manufacturing is about eliminating activities that do not add value, such as inspection, rework, and waiting.
Lean manufacturing improves product quality and costs. It also helps companies reach their goals quicker and decreases employee turnover. Lean manufacturing has been deemed one of the best ways to manage the entire value-chain, including customers, distributors as well retailers and employees. Many industries worldwide use lean manufacturing. Toyota's philosophy is the foundation of its success in automotives, electronics and appliances, healthcare, chemical engineers, aerospace, paper and food, among other industries.
Five principles are the basis of lean manufacturing:
-
Define Value- Identify the added value your company brings to society. What makes you stand out from your competitors?
-
Reduce Waste - Remove any activity which doesn't add value to your supply chain.
-
Create Flow - Ensure work moves smoothly through the process without interruption.
-
Standardize and Simplify – Make processes as consistent, repeatable, and as simple as possible.
-
Build relationships - Develop and maintain personal relationships with both your internal and external stakeholders.
Lean manufacturing isn’t new, but it has seen a renewed interest since 2008 due to the global financial crisis. To increase their competitiveness, many businesses have turned to lean manufacturing. Many economists believe lean manufacturing will play a major role in economic recovery.
Lean manufacturing is now becoming a common practice in the automotive industry, with many benefits. These include higher customer satisfaction levels, reduced inventory levels as well as lower operating costs.
It can be applied to any aspect of an organisation. Because it makes sure that all value chains are efficient and effectively managed, Lean Manufacturing is particularly helpful for organizations.
There are three types of lean manufacturing.
-
Just-in-Time Manufacturing (JIT): This type of lean manufacturing is commonly referred to as "pull systems." JIT is a process in which components can be assembled at the point they are needed, instead of being made ahead of time. This approach is designed to reduce lead times and increase the availability of components. It also reduces inventory.
-
Zero Defects Manufacturing, (ZDM): ZDM is focused on ensuring that no defective products leave the manufacturing facility. You should repair any part that needs to be repaired during an assembly line. This applies to finished products, which may need minor repairs before they are shipped.
-
Continuous Improvement (CI), also known as Continuous Improvement, aims at improving the efficiency of operations through continuous identification and improvement to minimize or eliminate waste. Continuous Improvement (CI) involves continuous improvement in processes, people, tools, and infrastructure.