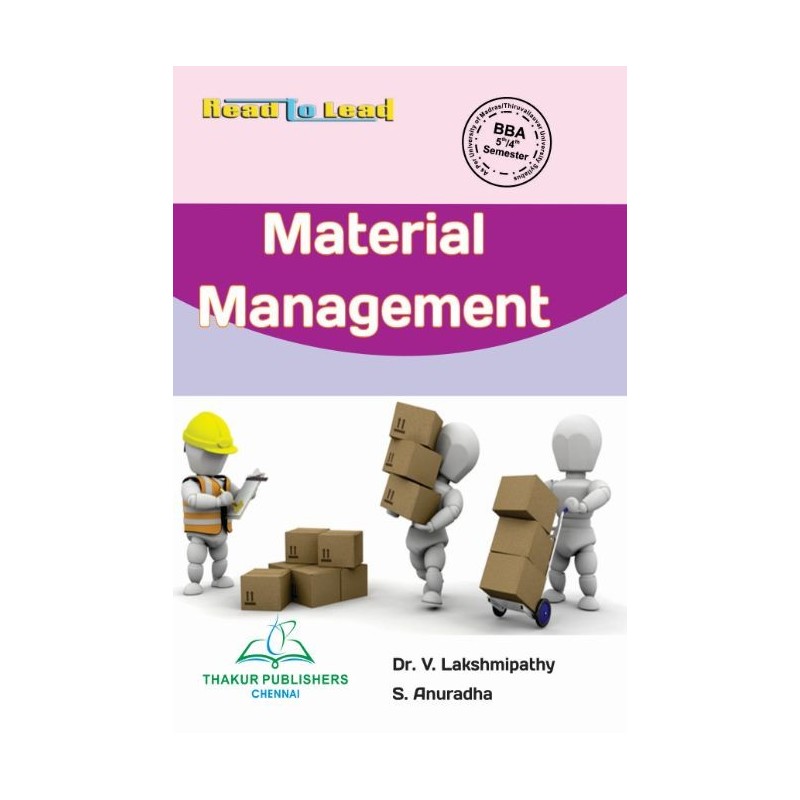
The foundation of continuous improvements is PDCA, or Plan, Do, Check, Act. This method of improvement is highly effective, and can produce significant results if it is implemented correctly. Employee involvement is essential for continuous improvement. To achieve this, a variety resources are needed. However, measurement and costing are just two benefits of the process. Without employees and customers, the PDCA cycle will not be complete.
PDCA cycle
Continuous improvement demands that you apply the PDCA Cycle to all aspects of your business. This cycle works by continuously improving a process and building on past improvements. As the team tests new processes, you might be able to spot new trends. Or, you may discover a new baseline that can help you identify areas of improvement. The PDCA cycle is a great tool to use for identifying improvement opportunities, but it also requires that you apply it carefully and in a controlled manner.
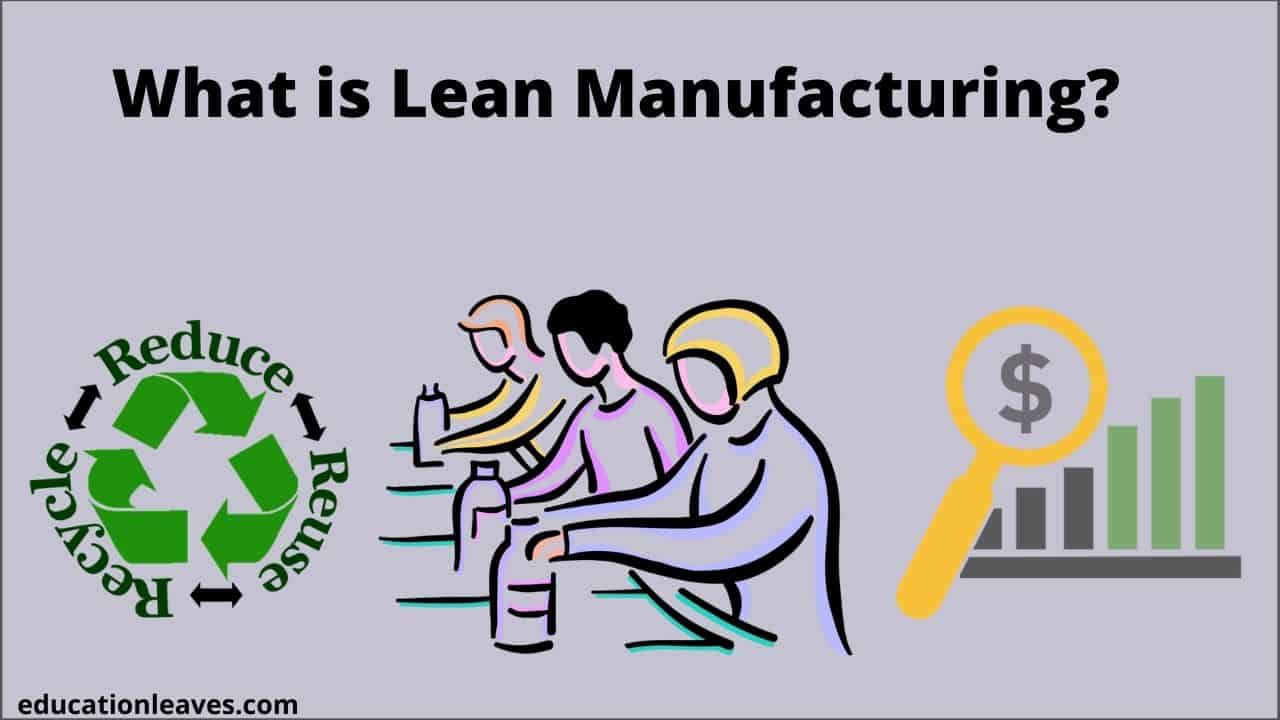
Employee involvement
Although employee involvement is often called many things, it is a concept that all organizations recognize as important. Research has shown that employee involvement is directly tied to important work outcomes. There are four types of employee involvement. They can be classified as: representative participation through unions; direct communication; upward problem solving; and teamwork. These forms of employee involvement are often reinforced through the culture, environment, and leadership of an organization. These are some examples for employee involvement.
Measurement
Many companies now include measurements in their continuous improvements initiatives. W. Edwards Deming introduced The Deming Cycle. This cycle includes a Check phase which assesses how well an improvement program is meeting its goals. If results are not as expected, the process is modified to make it better. Unless the results are satisfactory, the cycle will be repeated. These are part of continuous improvement.
Costs
For CI to be considered cost-effective, it is essential that an enterprise-wide cost evaluation of CI efforts be done. The business imperative to achieve the highest customer satisfaction and employee engagement scores should guide the cost-benefit analysis. Cost-benefit analyses should include ROI and budget adjustments to ensure success. The cost-benefit assessment should include benchmarking key business processes against industry averages, as well as key performance areas.
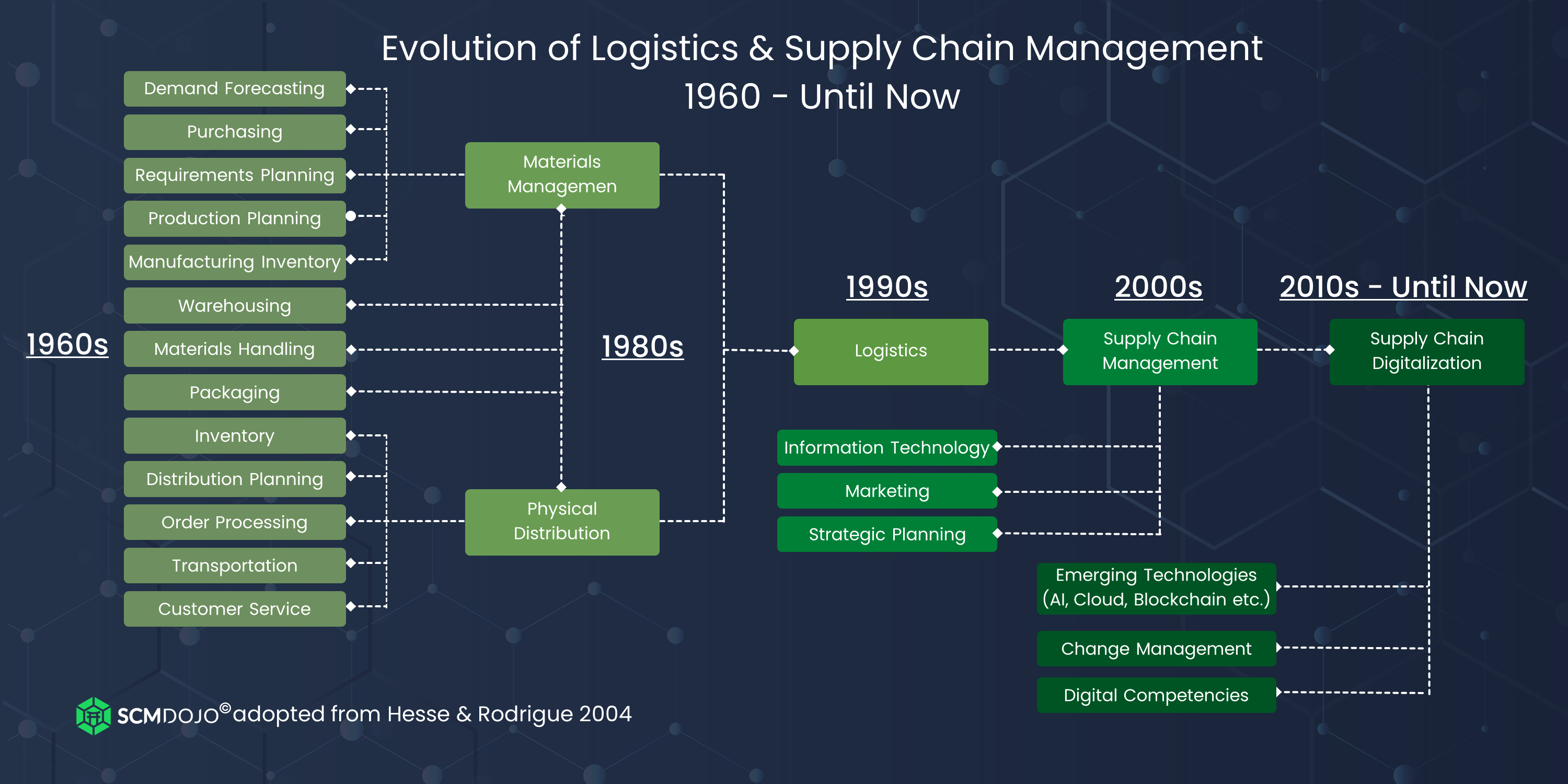
Benefits
Constant improvement offers clear benefits. Focusing on learning and failure will lead to more breakthroughs. Employees will feel more invested in the company if they are encouraged to look for ways to improve. A team that invests in the testing of new technologies or tools can also result in empowered employees. And the benefits of continuous improvement go beyond saving money. Successful changes can improve employee satisfaction as well as make employees' jobs easier.
FAQ
What does it mean to be a manufacturer?
Manufacturing Industries are those businesses that make products for sale. These products are sold to consumers. These companies use various processes such as production, distribution, retailing, management, etc., to fulfill this purpose. They create goods from raw materials, using machines and various other equipment. This includes all types of manufactured goods, including food items, clothing, building supplies, furniture, toys, electronics, tools, machinery, vehicles, pharmaceuticals, medical devices, chemicals, and many others.
What is the difference between a production planner and a project manager?
The main difference between a production planner and a project manager is that a project manager is usually the person who plans and organizes the entire project, whereas a production planner is mainly involved in the planning stage of the project.
What is the role and responsibility of a Production Planner?
A production planner ensures all aspects of the project are delivered on time, within budget, and within scope. They ensure that the product or service is of high quality and meets client requirements.
What is the responsibility of a manufacturing manager?
A manufacturing manager must make sure that all manufacturing processes run smoothly and effectively. They must also be alert to any potential problems and take appropriate action.
They should also be able and comfortable communicating with other departments like sales and marketing.
They should also be aware of the latest trends in their industry and be able to use this information to help improve productivity and efficiency.
Statistics
- [54][55] These are the top 50 countries by the total value of manufacturing output in US dollars for its noted year according to World Bank.[56] (en.wikipedia.org)
- Many factories witnessed a 30% increase in output due to the shift to electric motors. (en.wikipedia.org)
- In the United States, for example, manufacturing makes up 15% of the economic output. (twi-global.com)
- According to the United Nations Industrial Development Organization (UNIDO), China is the top manufacturer worldwide by 2019 output, producing 28.7% of the total global manufacturing output, followed by the United States, Japan, Germany, and India.[52][53] (en.wikipedia.org)
- It's estimated that 10.8% of the U.S. GDP in 2020 was contributed to manufacturing. (investopedia.com)
External Links
How To
How to use Lean Manufacturing in the production of goods
Lean manufacturing is a management system that aims at increasing efficiency and reducing waste. It was created in Japan by Taiichi Ohno during the 1970s and 80s. He received the Toyota Production System award (TPS), from Kanji Toyoda, founder of TPS. Michael L. Watkins published the book "The Machine That Changed the World", which was the first to be published about lean manufacturing.
Lean manufacturing is often defined as a set of principles used to improve the quality, speed, and cost of products and services. It emphasizes eliminating waste and defects throughout the value stream. The five-steps of Lean Manufacturing are just-in time (JIT), zero defect and total productive maintenance (TPM), as well as 5S. Lean manufacturing focuses on eliminating non-value-added activities such as rework, inspection, and waiting.
Lean manufacturing is a way for companies to achieve their goals faster, improve product quality, and lower costs. Lean manufacturing has been deemed one of the best ways to manage the entire value-chain, including customers, distributors as well retailers and employees. Lean manufacturing can be found in many industries. For example, Toyota's philosophy underpins its success in automobiles, electronics, appliances, healthcare, chemical engineering, aerospace, paper, food, etc.
Five basic principles of Lean Manufacturing are included in lean manufacturing
-
Define value - Find out what your business contributes to society, and what makes it different from other competitors.
-
Reduce waste - Stop any activity that isn't adding value to the supply chains.
-
Create Flow - Make sure work runs smoothly without interruptions.
-
Standardize and simplify – Make processes as repeatable and consistent as possible.
-
Develop Relationships: Establish personal relationships both with internal and external stakeholders.
Although lean manufacturing isn't a new concept in business, it has gained popularity due to renewed interest in the economy after the 2008 global financial crisis. To increase their competitiveness, many businesses have turned to lean manufacturing. In fact, some economists believe that lean manufacturing will be an important factor in economic recovery.
With many benefits, lean manufacturing is becoming more common in the automotive industry. These include better customer satisfaction and lower inventory levels. They also result in lower operating costs.
Lean manufacturing can be applied to almost every aspect of an organization. Because it makes sure that all value chains are efficient and effectively managed, Lean Manufacturing is particularly helpful for organizations.
There are three types of lean manufacturing.
-
Just-in Time Manufacturing: This lean manufacturing method is commonly called "pull systems." JIT refers to a system in which components are assembled at the point of use instead of being produced ahead of time. This approach reduces lead time, increases availability and reduces inventory.
-
Zero Defects Manufacturing, (ZDM): ZDM is focused on ensuring that no defective products leave the manufacturing facility. If a part needs to be fixed during the assembly line, it should be repaired rather than scrapped. This applies to finished products, which may need minor repairs before they are shipped.
-
Continuous Improvement (CI), also known as Continuous Improvement, aims at improving the efficiency of operations through continuous identification and improvement to minimize or eliminate waste. It involves continuous improvement of processes, people, and tools.