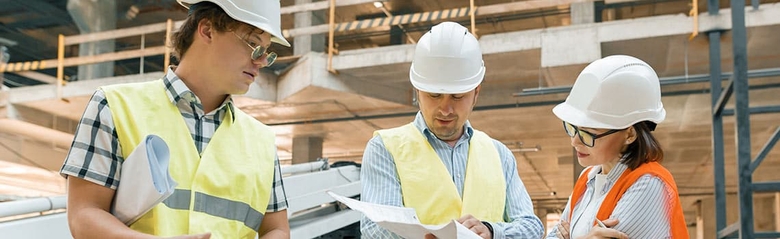
Industrial management is an engineering field where different engineering processes are integrated in order to create a management system. These engineering processes are integrated into an integrated management system by the industrial manager. Here are some things you should know about the job. These are some of the benefits and requirements to become an industrial manager. This career is for you if your qualifications are up-to-date and you're looking for a rewarding and challenging job. Continue reading for more information.
Job description
An industrial manager oversees the processes involved in the manufacturing and production of goods and services. Although the job is broad, it may also cover specific aspects such as how to source raw materials and use equipment. Industrial production managers must be computer literate, as computers increasingly play a key role in the coordination of various departments, suppliers, and clients. Additionally, industrial production managers need to be proficient in current production technologies and management methods. Many managers attend conferences and trade shows in the industry and also take courses to attain certification.
Industrial managers coordinate all activities within a company, in addition to supervising production processes. They make sure that production lines run smoothly and meet customer demands in terms of quality, time and delivery. They can also manage staffing levels, and adjust production levels as needed to reduce inventory. They may also oversee quality control programs and coordinate communication with suppliers and other departments. The majority of their role is to manage people. This includes identifying, training and motivating employees.
Education Required
A bachelor's degree is not required to be an industrial manager. Some employers prefer candidates with a background or education in these areas. Additionally, industrial managers need to be computer literate. Computers are an integral part of manufacturing. They coordinate production across departments, suppliers, customers, and even between clients. For this job, you will need the necessary education and experience.
Many industrial production managers started their careers as production workers before moving up to the first-line supervisory position. All professionals must obtain a college business management degree to reach the industrial manager level. Some entry-level workers might be able to get this education while on the job or through classes sponsored by their employers. But, managers should have at least two- to five years of relevant experience to be considered for managerial positions.
Your potential to earn
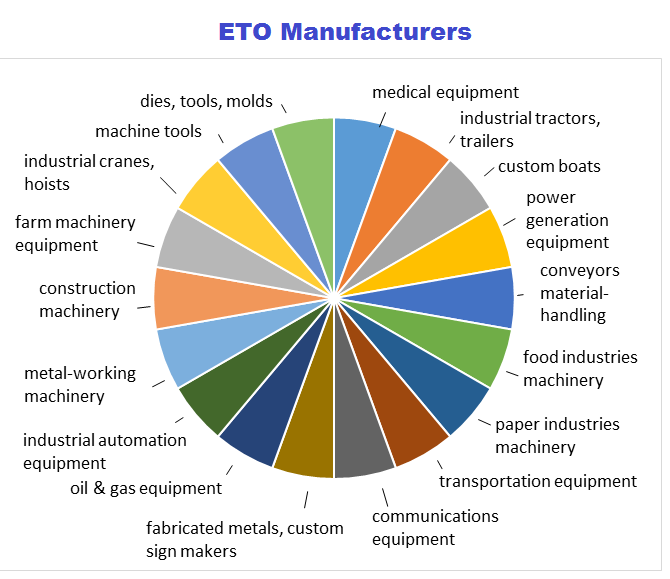
The industrial managers are responsible for overseeing the smooth running of manufacturing plants. They decide how to best utilize employees and equipment, meet production standards, and make strategic decisions. Their responsibilities include hiring, evaluating, and setting production times, and making sure safety procedures are adhered to. They also oversee the day-to-day activities of a team of workers and continuously analyze the entire production process to ensure it is operating efficiently and at peak efficiency.
The earnings potential of an industrial production manager depends on the employer and the experience of the employee. Although it is difficult to predict the future earnings, the average salary for industrial production managers was $103,380 in May 2016. The highest-paid industrial production managers earned $172,150 annually. Industrial production managers with advanced training and certification might earn higher wages. According to U.S. Bureau of Labor Statistics, those who have earned a bachelor’s or higher in industrial production management can earn more.
Environment for work
An industrial production manager divides his or her time between the production floor and an office, often in the same building. When they work in a production zone, industrial production managers need to adhere to safety and health guidelines and use appropriate protective equipment. They often spend significant time in meetings and analysis of production data. Reports may be written by these managers. A manager of industrial production often works in a dynamic environment.
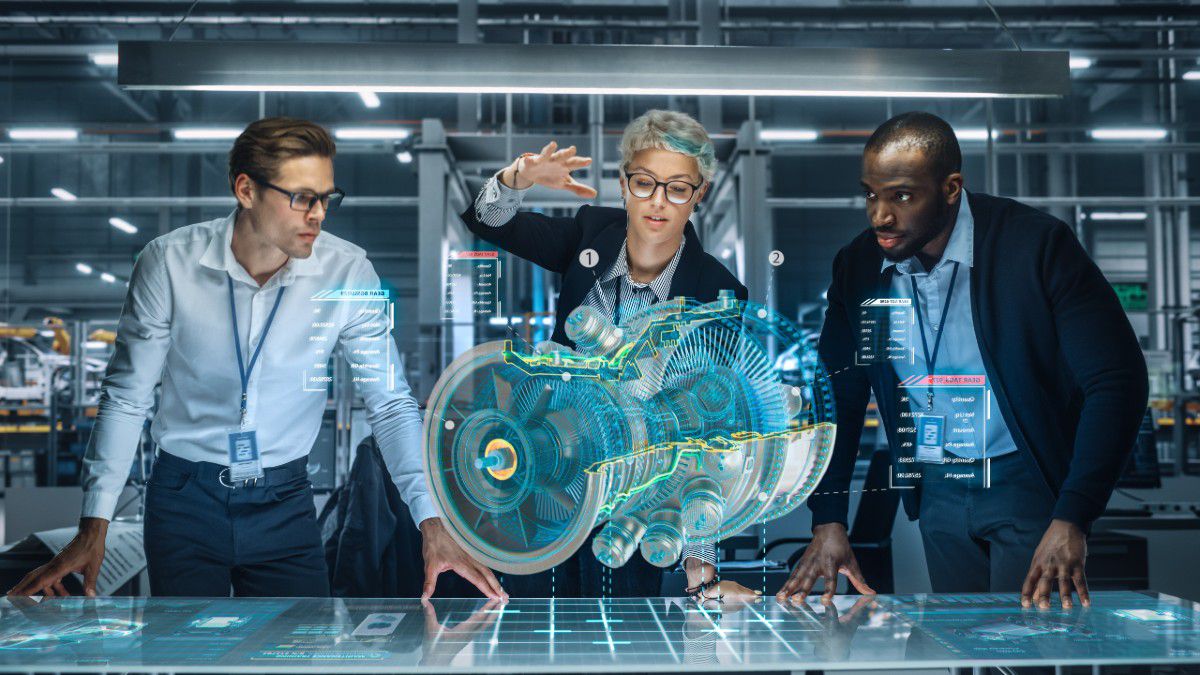
As part of a business's management structure, industrial production managers have many responsibilities. They are responsible for coordinating the activities of workers and increasing productivity. An industrial production manager's primary responsibility is to increase productivity and ensure safety. Because of corporate restructuring, many levels of management have been eliminated and support staff have been reduced, leaving more of the workload to production managers. This can be a significant challenge for any manager, and can make it difficult to do the job as a production manager.
FAQ
What are the goods of logistics?
Logistics involves the transportation of goods from point A and point B.
They encompass all aspects transport, including packaging and loading, transporting, storage, unloading.
Logisticians make sure that the right product arrives at the right place at the correct time and in safe conditions. They assist companies with their supply chain efficiency through information on demand forecasts. Stock levels, production times, and availability.
They monitor shipments in transit, ensure quality standards, manage inventories, replenish orders, coordinate with suppliers and other vendors, and offer support services for sales, marketing, and customer service.
What are the 4 types manufacturing?
Manufacturing is the process of transforming raw materials into useful products using machines and processes. It includes many different activities like designing, building and testing, packaging, shipping and selling, as well as servicing.
How important is automation in manufacturing?
Automating is not just important for manufacturers, but also for service providers. Automation allows them to deliver services quicker and more efficiently. It also helps to reduce costs and improve productivity.
What is production plan?
Production Planning is the creation of a plan to cover all aspects, such as scheduling, budgeting. Location, crew, equipment, props and other details. It is important to have everything ready and planned before you start shooting. It should also provide information about how best to produce the best results while on set. This information includes locations, crew details and equipment requirements.
First, you need to plan what you want to film. You may have decided where to shoot or even specific locations you want to use. Once you have determined your scenes and locations, it is time to start figuring out the elements that you will need for each scene. If you decide you need a car and don't know what model to choose, this could be an example. To narrow your options, you can search online for available models.
After you have chosen the right car, you will be able to begin thinking about accessories. You might need to have people in the front seats. Or maybe you just need someone to push the car around. Maybe you'd like to change the interior from black to a white color. These questions will help to determine the style and feel of your car. Also, think about what kind of shots you would like to capture. You will be filming close-ups and wide angles. Maybe you want the engine or the steering wheels to be shown. These factors will help you determine which car style you want to film.
Once you have made all the necessary decisions, you can start to create a schedule. A schedule will tell you when you need to start shooting and when you need to finish. Each day will include the time when you need to arrive at the location, when you need to leave and when you need to return home. So everyone is clear about what they need to do. Book extra staff ahead of time if you need them. You should not hire anyone who doesn't show up because of your inaction.
Your schedule will also have to be adjusted to reflect the number of days required to film. Some projects may only take a couple of days, while others could last for weeks. While creating your schedule, it is important to remember whether you will require more than one shot per day. Multiple shots at the same location can increase costs and make it more difficult to complete. It's better to be safe than sorry and shoot less takes if you're not certain whether you need more takes.
Budgeting is another crucial aspect of production plan. As it will allow you and your team to work within your financial means, setting a realistic budget is crucial. Remember that you can always reduce the budget later on if you run into unforeseen problems. However, it is important not to overestimate the amount that you will spend. If you underestimate how much something costs, you'll have less money to pay for other items.
Production planning is a very detailed process, but once you understand how everything works together, it becomes easier to plan future projects.
What is manufacturing and logistics?
Manufacturing is the production of goods using raw materials. Logistics encompasses the management of all aspects associated with supply chain activities such as procurement, production planning, distribution and inventory control. It also includes customer service. Logistics and manufacturing are often referred to as one thing. It encompasses both the creation of products and their delivery to customers.
What is the importance of logistics in manufacturing?
Logistics are an essential component of any business. They can help you achieve great success by helping you manage product flow from raw material to finished goods.
Logistics also play a major role in reducing costs and increasing efficiency.
What can I do to learn more about manufacturing?
You can learn the most about manufacturing by getting involved in it. However, if that's not possible, you can always read books or watch educational videos.
Statistics
- [54][55] These are the top 50 countries by the total value of manufacturing output in US dollars for its noted year according to World Bank.[56] (en.wikipedia.org)
- Job #1 is delivering the ordered product according to specifications: color, size, brand, and quantity. (netsuite.com)
- It's estimated that 10.8% of the U.S. GDP in 2020 was contributed to manufacturing. (investopedia.com)
- (2:04) MTO is a production technique wherein products are customized according to customer specifications, and production only starts after an order is received. (oracle.com)
- Many factories witnessed a 30% increase in output due to the shift to electric motors. (en.wikipedia.org)
External Links
How To
How to Use the Just In Time Method in Production
Just-intime (JIT), a method used to lower costs and improve efficiency in business processes, is called just-in-time. It's the process of obtaining the right amount and timing of resources when you need them. This means that you only pay the amount you actually use. Frederick Taylor first coined this term while working in the early 1900s as a foreman. Taylor observed that overtime was paid to workers if they were late in working. He realized that workers should have enough time to complete their jobs before they begin work. This would help increase productivity.
JIT teaches you to plan ahead and prepare everything so you don’t waste time. The entire project should be looked at from start to finish. You need to ensure you have enough resources to tackle any issues that might arise. If you anticipate that there might be problems, you'll have enough people and equipment to fix them. This way you won't be spending more on things that aren’t really needed.
There are many JIT methods.
-
Demand-driven JIT: This is a JIT that allows you to regularly order the parts/materials necessary for your project. This will allow for you to track the material that you have left after using it. It will also allow you to predict how long it takes to produce more.
-
Inventory-based: You stock materials in advance to make your projects easier. This allows for you to anticipate how much you can sell.
-
Project-driven: This means that you have enough money to pay for your project. Knowing how much money you have available will help you purchase the correct amount of materials.
-
Resource-based: This is the most common form of JIT. You allocate resources based on the demand. For instance, if you have a lot of orders coming in, you'll assign more people to handle them. You'll have fewer orders if you have fewer.
-
Cost-based : This is similar in concept to resource-based. But here, you aren't concerned about how many people your company has but how much each individual costs.
-
Price-based pricing: This is similar in concept to cost-based but instead you look at how much each worker costs, it looks at the overall company's price.
-
Material-based: This is very similar to cost-based but instead of looking at total costs of the company you are concerned with how many raw materials you use on an average.
-
Time-based JIT: This is another variant of resource-based JIT. Instead of focusing only on how much each employee is costing, you should focus on how long it takes to complete your project.
-
Quality-based JIT is another variant of resource-based JIT. Instead of focusing on the cost of each worker or how long it takes, think about how high quality your product is.
-
Value-based: This is one of the newest forms of JIT. In this instance, you are not concerned about the product's performance or meeting customer expectations. Instead, you focus on the added value that you provide to your market.
-
Stock-based: This inventory-based approach focuses on how many items are being produced at any one time. It's used when you want to maximize production while minimizing inventory.
-
Just-in-time (JIT) planning: This is a combination of JIT and supply chain management. It is the process that schedules the delivery of components within a short time of their order. It is essential because it reduces lead-times and increases throughput.