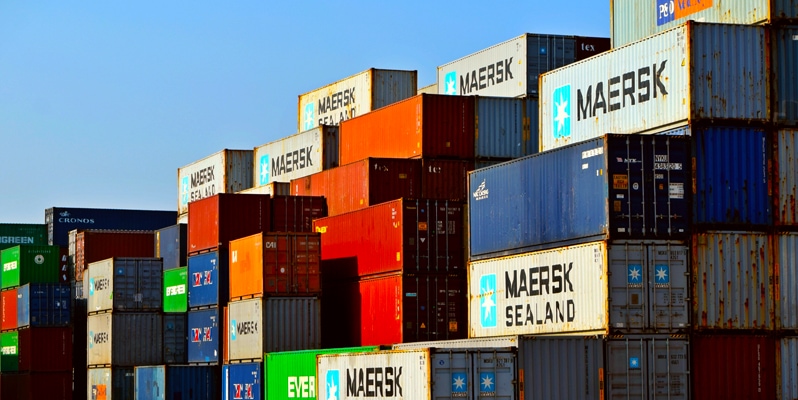
There are many opportunities for industrial engineering jobs in Chicago. It is therefore important to know what to study and how to get work. Here, you will discover a few common reasons to consider pursuing a career in industrial engineering. Read on to learn more about job descriptions, salary ranges, and educational requirements.
Job description
They are responsible to develop systems that combine workers, machines, and material. Industrial engineers may work in offices or factories. In order to improve the efficiency of their work, they may spend some time watching workers. They typically hold a bachelor's degree or equivalent in industrial engineering. In May 2021, the median annual salary for industrial engineers was $95,300.
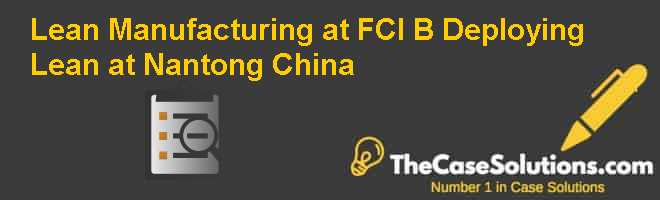
Salary
Industrial engineers use integrated systems to manage industrial processes. Some are forbidden from working in hazardous environments such as mines. The BLS's Industrial Engineer Salary Survey collects data on the wages of workers in this occupation throughout the country. This data includes changes in the annual pay over five year periods and is accurate down to the year and state.
Industrial engineering jobs in Chicago are typically more lucrative than those in other areas of the country. You will need to have excellent interpersonal communication skills as well as analytical thinking and technical expertise in order to work in this field. The skills that industrial engineers have gained from a variety of jobs are combined to create a solution for a business. They often take on moderately challenging industrial engineering tasks and also conduct statistical analyses of data. These analyses can help to improve production flow as well as standard times. They also plan and implement strategies including Bottleneck Analysis, Value Stream Mapping, and Bottleneck Mapping.
You can find locations
Chicago is a great location for industrial engineers. It has a wide variety of options and will allow you to use your diverse skill sets in many different industries. This career is extremely flexible. Moreover, it allows you to see the results of your hard work.
Education requirements
Industrial engineers need a bachelor's in a related field as well as several years experience. They also require strong communication and analytical skills. They must communicate clearly with group members and be able answer their questions. They must be familiar with the principles and applications of plane geometry, trigonometry, and other related concepts.
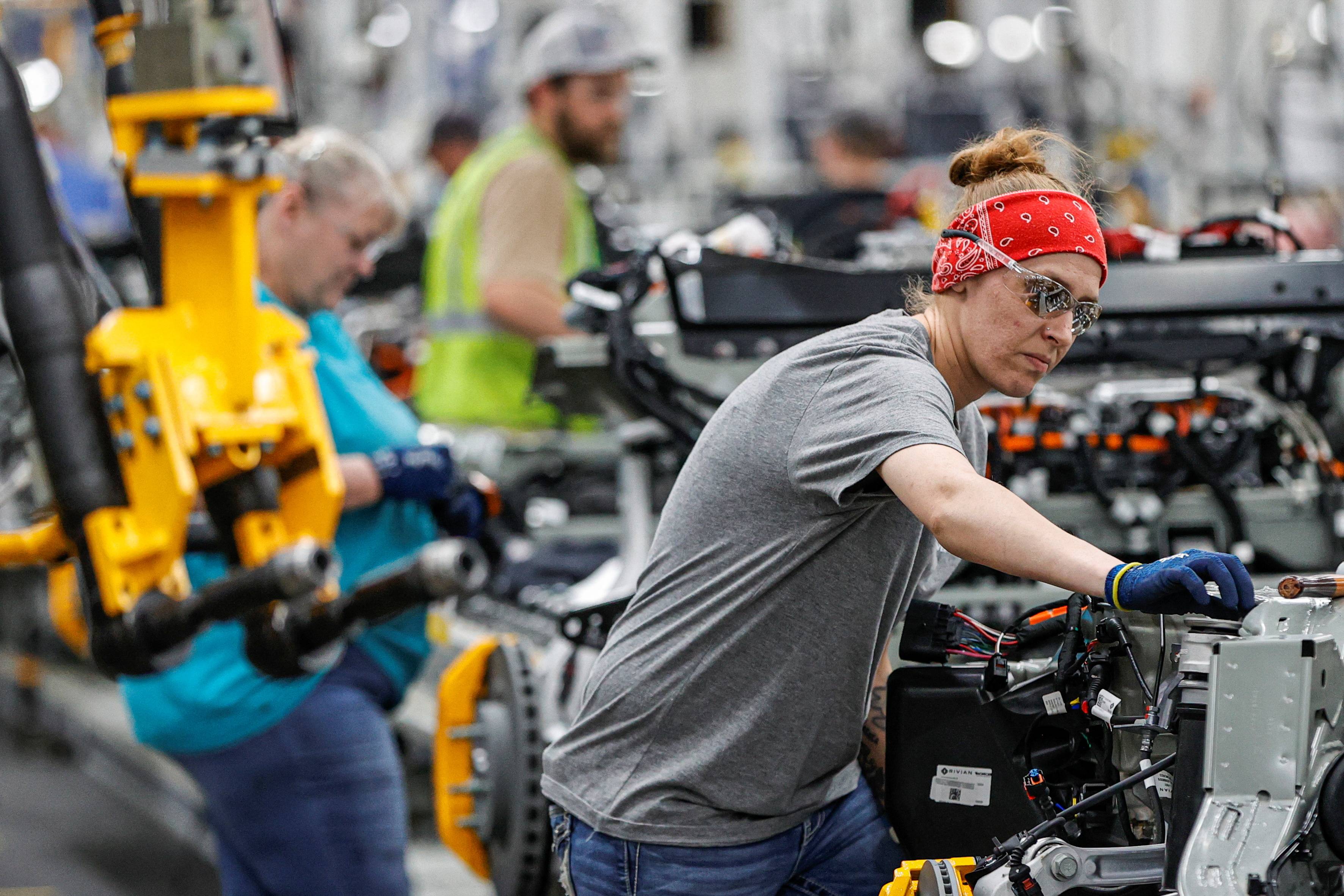
In addition to these core skills, industrial engineers must be able to communicate effectively with diverse audiences. They must have strong ethics and be able recognize their responsibilities when working in engineering. They must be able to make informed decisions regarding engineering solutions and consider their effects in a global context. They should also be able work together and set goals and objectives. They should also be able to analyse data and draw inferences.
FAQ
What are the four types in manufacturing?
Manufacturing is the process that transforms raw materials into useful products. It involves many different activities such as designing, building, testing, packaging, shipping, selling, servicing, etc.
How can manufacturing overproduction be reduced?
It is essential to find better ways to manage inventory to reduce overproduction. This would reduce the time needed to manage inventory. This would allow us to use our resources for more productive tasks.
One way to do this is to adopt a Kanban system. A Kanbanboard is a visual tool that allows you to keep track of the work being done. In a Kanban system, work items move through a sequence of states until they reach their final destination. Each state represents an individual priority level.
As an example, if work is progressing from one stage of the process to another, then the current task is complete and can be transferred to the next. A task that is still in the initial stages of a process will be considered complete until it moves on to the next stage.
This keeps work moving and ensures no work is lost. Managers can see how much work has been done and the status of each task at any time with a Kanban Board. This information allows them to adjust their workflow based on real-time data.
Lean manufacturing can also be used to reduce inventory levels. Lean manufacturing emphasizes eliminating waste in all phases of production. Waste includes anything that does not add value to the product. These are some of the most common types.
-
Overproduction
-
Inventory
-
Packaging not required
-
Overstock materials
These ideas will help manufacturers increase efficiency and lower costs.
What is the difference in Production Planning and Scheduling, you ask?
Production Planning (PP), also known as forecasting and identifying production capacities, is the process that determines what product needs to be produced at any particular time. Forecasting demand is one way to do this.
Scheduling is the process that assigns dates to tasks so they can get completed within a given timeframe.
What are my options for learning more about manufacturing
Experience is the best way for you to learn about manufacturing. If that is not possible, you could always read books or view educational videos.
How can manufacturing avoid production bottlenecks
Avoiding production bottlenecks is as simple as keeping all processes running smoothly, from the time an order is received until the product ships.
This includes planning for both capacity requirements and quality control measures.
Continuous improvement techniques such Six Sigma can help you achieve this.
Six Sigma is a management method that helps to improve quality and reduce waste.
It's all about eliminating variation and creating consistency in work.
Statistics
- According to a Statista study, U.S. businesses spent $1.63 trillion on logistics in 2019, moving goods from origin to end user through various supply chain network segments. (netsuite.com)
- It's estimated that 10.8% of the U.S. GDP in 2020 was contributed to manufacturing. (investopedia.com)
- (2:04) MTO is a production technique wherein products are customized according to customer specifications, and production only starts after an order is received. (oracle.com)
- In the United States, for example, manufacturing makes up 15% of the economic output. (twi-global.com)
- Many factories witnessed a 30% increase in output due to the shift to electric motors. (en.wikipedia.org)
External Links
How To
How to use Lean Manufacturing in the production of goods
Lean manufacturing refers to a method of managing that seeks to improve efficiency and decrease waste. It was developed in Japan during the 1970s and 1980s by Taiichi Ohno, who received the Toyota Production System (TPS) award from TPS founder Kanji Toyoda. Michael L. Watkins published the "The Machine That Changed the World", the first book about lean manufacturing. It was published in 1990.
Lean manufacturing is often described as a set if principles that help improve the quality and speed of products and services. It is about eliminating defects and waste from all stages of the value stream. Lean manufacturing can be described as just-in–time (JIT), total productive maintenance, zero defect (TPM), or even 5S. Lean manufacturing eliminates non-value-added tasks like inspection, rework, waiting.
Lean manufacturing improves product quality and costs. It also helps companies reach their goals quicker and decreases employee turnover. Lean manufacturing is considered one of the most effective ways to manage the entire value chain, including suppliers, customers, distributors, retailers, and employees. Lean manufacturing is widely used in many industries. Toyota's philosophy, for example, is what has enabled it to be successful in electronics, automobiles, medical devices, healthcare and chemical engineering as well as paper and food.
Five fundamental principles underlie lean manufacturing.
-
Define Value: Identify the social value of your business and what sets you apart.
-
Reduce waste - Get rid of any activity that does not add value to the supply chain.
-
Create Flow - Make sure work runs smoothly without interruptions.
-
Standardize and simplify – Make processes as repeatable and consistent as possible.
-
Build relationships - Develop and maintain personal relationships with both your internal and external stakeholders.
Lean manufacturing isn’t new, but it has seen a renewed interest since 2008 due to the global financial crisis. Many companies have adopted lean manufacturing methods to increase their marketability. Many economists believe lean manufacturing will play a major role in economic recovery.
Lean manufacturing is becoming a popular practice in automotive. It has many advantages. These include higher customer satisfaction levels, reduced inventory levels as well as lower operating costs.
The principles of lean manufacturing can be applied in almost any area of an organization. It is especially useful for the production aspect of an organization, as it ensures that every step in the value chain is efficient and effective.
There are three types principally of lean manufacturing:
-
Just-in-Time Manufacturing: Also known as "pull systems", this type of lean manufacturing uses just-in-time manufacturing (JIT). JIT refers to a system in which components are assembled at the point of use instead of being produced ahead of time. This approach reduces lead time, increases availability and reduces inventory.
-
Zero Defects Manufacturing: ZDM ensures that no defective units leave the manufacturing plant. If a part needs to be fixed during the assembly line, it should be repaired rather than scrapped. This applies to finished products, which may need minor repairs before they are shipped.
-
Continuous Improvement (CI): CI aims to improve the efficiency of operations by continuously identifying problems and making changes in order to eliminate or minimize waste. Continuous Improvement involves continuous improvement of processes.