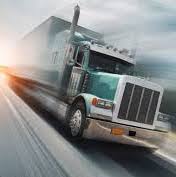
Gemba walk was developed originally by Toyota. This tool takes managers to the shop floor in order to gain insight into the company's process. This is an essential part in any facility improvement plan. It allows managers to see the process and make better decisions. This practice can also help to identify and solve problems.
Gemba, a Japanese term meaning "where the work happens", is a Japanese term. It is used to identify the factory floor and shop floor but can also refer to any other place where a product, or service, is created. Gemba is also the Japanese name for a business philosophy. It sets out a number of goals. In general, the goal of Gemba is to achieve in-depth knowledge of the processes in an organization, while eliminating waste and improving efficiency.
Companies that want to improve their processes or eliminate waste should consider Gemba walks. They promote collaboration and harmony within an organization. They encourage employees to exchange ideas which can lead to a better product or service. They can also help managers and executives to better understand the processes in their company.
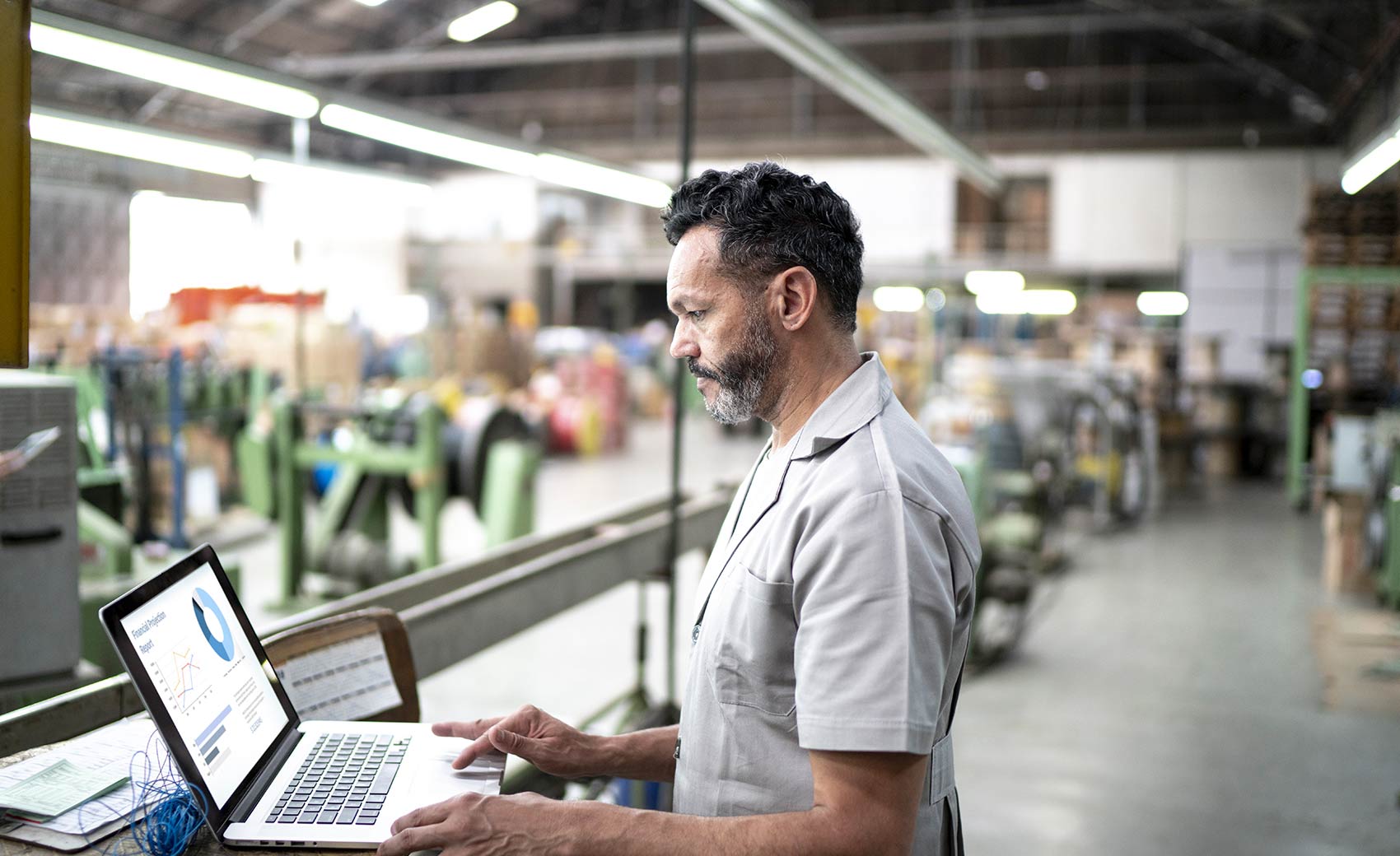
Gemba walks should be conducted by managers and supervisors. However, executives can also conduct them on their own. Gemba walks should always be conducted by senior executives. Gemba walks should be completed with a Lean teacher, Sensei, for approximately 45-60 minutes each week. The best time to observe workers' work is during their busiest hours.
Gemba Walks help managers and executives understand how the processes work, and they also help to identify improvement opportunities. They help improve an organization's safety. Safety issues account for the majority of waste generated by manufacturing plants. Continuous improvement can be made possible through safety improvements.
Gemba Walks are an important part of the Lean process, but they should be implemented at all levels of the organization. They are a great way for executives and leaders to get a fresh view on customers. This will lead to better products and services. Gemba Walks can help an organization achieve its full potential.
Gemba Walks play an important role in Lean process designs. They are often used as part of Kaizen events by key stakeholders. Kaizen events are gatherings of key stakeholders that evaluate activities and assess activities. They are based on the Japanese term "continuous improvement."
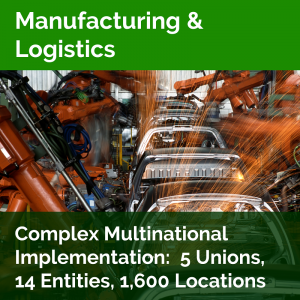
Gemba Walks should be conducted on a regular basis. If done properly, they can reduce waste as well as improve productivity. Because these are the busiest hours of the day, it is best to do them during shift changes. This will help executives and project mangers gain a better understanding of their business. Executives and project managers need to take note of potential improvements such as new products, services, or ideas from employees.
FAQ
What are the 7 Rs of logistics management?
The acronym "7R's" of Logistics stands for seven principles that underpin logistics management. It was developed by International Association of Business Logisticians (IABL), and published as part of their "Seven Principles of Logistics Management Series" in 2004.
The following letters make up the acronym:
-
Responsive - ensure all actions are legal and not harmful to others.
-
Reliable: Have faith in your ability or the ability to honor any promises made.
-
Reasonable - make sure you use your resources well and don't waste them.
-
Realistic - Take into consideration all aspects of operations including cost-effectiveness, environmental impact, and other factors.
-
Respectful - treat people fairly and equitably.
-
Be resourceful: Look for opportunities to save money or increase productivity.
-
Recognizable - provide customers with value-added services.
Are there ways to automate parts of manufacturing?
Yes! Automation has been around since ancient times. The Egyptians created the wheel thousands years ago. Nowadays, we use robots for assembly lines.
In fact, there are several applications of robotics in manufacturing today. These include:
-
Robots for assembly line
-
Robot welding
-
Robot painting
-
Robotics inspection
-
Robots that create products
Manufacturing can also be automated in many other ways. 3D printing makes it possible to produce custom products in a matter of days or weeks.
What are the essential elements of running a logistics firm?
A successful logistics business requires a lot more than just knowledge. You must have good communication skills to interact effectively with your clients and suppliers. You must be able analyze data and draw out conclusions. You must be able and able to handle stress situations and work under pressure. To increase efficiency and creativity, you need to be creative. You must be a strong leader to motivate others and direct them to achieve organizational goals.
You must be organized to meet tight deadlines.
What is the responsibility of a production planner?
Production planners make sure that every aspect of the project is delivered on-time, within budget, and within schedule. A production planner ensures that the service and product meet the client's expectations.
Statistics
- Many factories witnessed a 30% increase in output due to the shift to electric motors. (en.wikipedia.org)
- It's estimated that 10.8% of the U.S. GDP in 2020 was contributed to manufacturing. (investopedia.com)
- Job #1 is delivering the ordered product according to specifications: color, size, brand, and quantity. (netsuite.com)
- In 2021, an estimated 12.1 million Americans work in the manufacturing sector.6 (investopedia.com)
- According to the United Nations Industrial Development Organization (UNIDO), China is the top manufacturer worldwide by 2019 output, producing 28.7% of the total global manufacturing output, followed by the United States, Japan, Germany, and India.[52][53] (en.wikipedia.org)
External Links
How To
How to use 5S in Manufacturing to Increase Productivity
5S stands in for "Sort", the "Set In Order", "Standardize", or "Separate". Toyota Motor Corporation was the first to develop the 5S approach in 1954. It allows companies to improve their work environment, thereby achieving greater efficiency.
This method aims to standardize production processes so that they are repeatable, measurable and predictable. This means that daily tasks such as cleaning and sorting, storage, packing, labeling, and packaging are possible. Workers can be more productive by knowing what to expect.
Five steps are required to implement 5S: Sort, Set In Order, Standardize. Separate. Each step is a different action that leads to greater efficiency. You can make it easy for people to find things later by sorting them. You arrange items by placing them in an order. Then, after you separate your inventory into groups, you store those groups in containers that are easy to access. Finally, label all containers correctly.
Employees must be able to critically examine their work practices. Employees must understand why they do certain tasks and decide if there's another way to accomplish them without relying on the old ways of doing things. They must learn new skills and techniques in order to implement the 5S system.
The 5S method increases efficiency and morale among employees. They will feel motivated to strive for higher levels of efficiency once they start to see results.