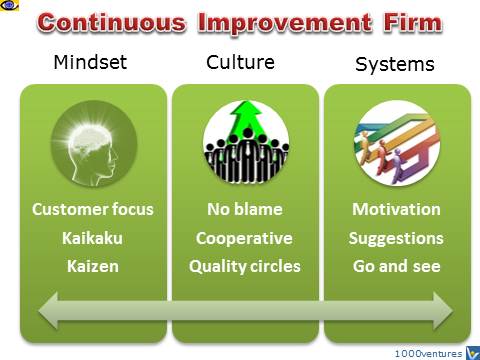
Lean to Agile is a great way for teams to cut waste and increase productivity. It is about prioritizing work and eliminating wasted effort, while empowering teams as well as scrum masters to take care of the rest. Agile teams must be empowered to become product owners.
Time-to-market
The time it takes from ideation to full release is one of the most critical measures of product success. This timeframe will determine how quickly your company can gain market share or revenue. Companies need to know their development processes, and how they use them. This will allow them to refine their processes and maximize their potential to improve their time-to market.
Using outsourcing as a tool to reduce time-to-market is one way to shorten the time required to market a new product. A network of trusted supporting partners is another way to reduce time. This will help you reduce risk and to share your resources.
Iteration
Iteration is a key element of agile software development. Iteration is a key element of agile software development. This concept emphasizes the value of small, measured steps that can be evaluated faster than a complete process. These features yield better results and higher chances of success. It is not always easy to do. The end product of an iteration should be running and releasable. It should be integrated, tested and deployed to an internal server.
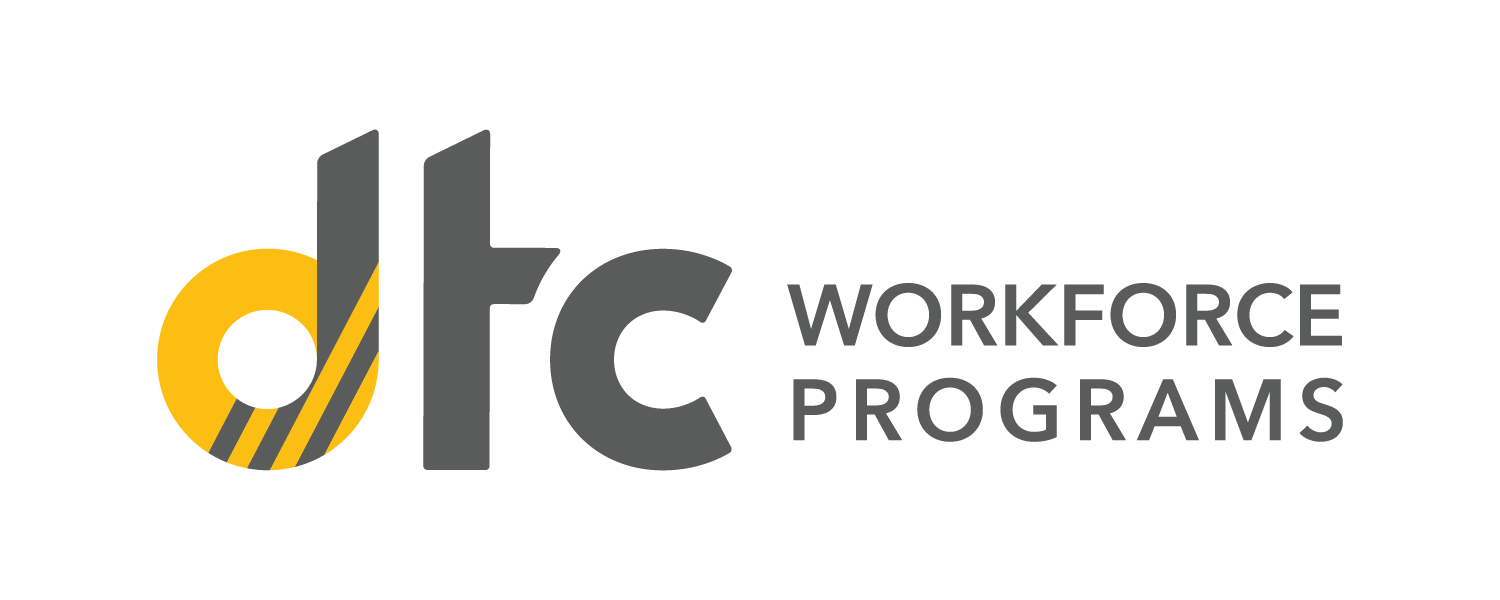
Iterations allow teams to refine their backlog, identify risks and fix them. The goal is for each iteration to improve on the previous one. Developers may refactor or add new features to existing features. This continues until the product's release is complete.
Collaborative processes
Agile Manifesto emphasizes collaboration between business stakeholders, developers, and other stakeholders. This allows teams to prioritize work based on business goals. Lean processes encourage a value stream. This is the end-to–end list of actions required to produce the product or services customers desire. Although these approaches are similar, there are some key differences.
Agile is a more flexible approach than Lean. Lean UX teams don't use large, rigid tools for project management. Instead, they work as a team, scale up quickly and collaborate to achieve a goal. In addition, Agile is a system of small-world networks and deliverables. It emphasizes autonomy, exploration, collaboration, and teamwork. Scaling from a single project to a multiple-project program requires an agile approach.
User research in agile teams
Agile teams are increasingly incorporating user research into their processes. This mindset is becoming increasingly common in product design, but it's also being applied to other areas. Teams are becoming more aware of the importance usability and user experience and the need to do quick and flexible research. Agile teams adopt agile thinking to ensure user-centric research is at the forefront. They use this mindset to discover processes that link to the product roadmap.
It is important to simplify and make user research more accessible. This means creating repeatable user research templates that non-practitioners can easily use to run tests. These templates should answer most of the questions and cover all phases of product development. UX platforms offer preloaded templates as well as automated workflows that can ensure consistency in results.
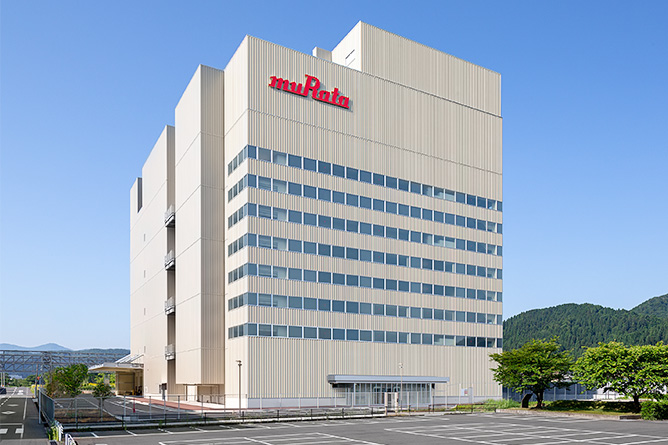
Creation of value
Although the concept of value creation may seem odd, it does make sense. You can create value in a narrower or wider scope. However, the process cannot be completely binary. In certain cases, a smaller scope creates a small value, and a larger scope generates more value. The idea of having a complete scope is still possible.
Lean and agile help customers deliver a focused and high-value product. Combining these two approaches allows companies to produce better products and deliver them faster. These methods reduce overhead and empower employees to work together, focusing on the customer's needs.
FAQ
What is the responsibility of a production planner?
Production planners ensure that all project aspects are completed on time, within budget and within the scope. They also ensure the quality of the product and service meets the client's requirements.
How can overproduction in manufacturing be reduced?
Better inventory management is key to reducing excess production. This would reduce the time spent on unproductive activities like purchasing, storing and maintaining excess stock. This could help us free up our time for other productive tasks.
This can be done by using a Kanban system. A Kanbanboard is a visual tool that allows you to keep track of the work being done. Kanban systems are where work items travel through a series of states until reaching their final destination. Each state represents an individual priority level.
When work is completed, it can be transferred to the next stage. It is possible to keep a task in the beginning stages until it gets to the end.
This allows you to keep work moving along while making sure that no work gets neglected. Managers can view the Kanban board to see how much work they have done. This data allows them adjust their workflow based upon real-time data.
Lean manufacturing, another method to control inventory levels, is also an option. Lean manufacturing focuses on eliminating waste throughout the entire production chain. Anything that does nothing to add value to a product is waste. Some common types of waste include:
-
Overproduction
-
Inventory
-
Packaging not required
-
Materials in excess
These ideas will help manufacturers increase efficiency and lower costs.
What are the responsibilities for a manufacturing manager
A manufacturing manager must ensure that all manufacturing processes are efficient and effective. They should also be aware and responsive to any company problems.
They must also be able to communicate with sales and marketing departments.
They should also be aware of the latest trends in their industry and be able to use this information to help improve productivity and efficiency.
What does manufacturing mean?
Manufacturing Industries refers to businesses that manufacture products. The people who buy these products are called consumers. This is accomplished by using a variety of processes, including production, distribution and retailing. They produce goods from raw materials by using machines and other machinery. This includes all types and varieties of manufactured goods, such as food items, clothings, building supplies, furnitures, toys, electronics tools, machinery vehicles, pharmaceuticals medical devices, chemicals, among others.
Statistics
- (2:04) MTO is a production technique wherein products are customized according to customer specifications, and production only starts after an order is received. (oracle.com)
- You can multiply the result by 100 to get the total percent of monthly overhead. (investopedia.com)
- Job #1 is delivering the ordered product according to specifications: color, size, brand, and quantity. (netsuite.com)
- According to the United Nations Industrial Development Organization (UNIDO), China is the top manufacturer worldwide by 2019 output, producing 28.7% of the total global manufacturing output, followed by the United States, Japan, Germany, and India.[52][53] (en.wikipedia.org)
- In 2021, an estimated 12.1 million Americans work in the manufacturing sector.6 (investopedia.com)
External Links
How To
How to Use Lean Manufacturing for the Production of Goods
Lean manufacturing is an approach to management that aims for efficiency and waste reduction. It was developed in Japan between 1970 and 1980 by Taiichi Ohno. TPS founder Kanji Tyoda gave him the Toyota Production System, or TPS award. The first book published on lean manufacturing was titled "The Machine That Changed the World" written by Michael L. Watkins and published in 1990.
Lean manufacturing is often defined as a set of principles used to improve the quality, speed, and cost of products and services. It is about eliminating defects and waste from all stages of the value stream. Lean manufacturing is called just-in-time (JIT), zero defect, total productive maintenance (TPM), or 5S. Lean manufacturing eliminates non-value-added tasks like inspection, rework, waiting.
Lean manufacturing is a way for companies to achieve their goals faster, improve product quality, and lower costs. Lean manufacturing is considered one of the most effective ways to manage the entire value chain, including suppliers, customers, distributors, retailers, and employees. Many industries worldwide use lean manufacturing. Toyota's philosophy is a great example of this. It has helped to create success in automobiles as well electronics, appliances and healthcare.
Lean manufacturing is based on five principles:
-
Define value - Find out what your business contributes to society, and what makes it different from other competitors.
-
Reduce waste - Get rid of any activity that does not add value to the supply chain.
-
Create Flow. Ensure that your work is uninterrupted and flows seamlessly.
-
Standardize and Simplify – Make processes as consistent, repeatable, and as simple as possible.
-
Build relationships - Develop and maintain personal relationships with both your internal and external stakeholders.
Although lean manufacturing isn't a new concept in business, it has gained popularity due to renewed interest in the economy after the 2008 global financial crisis. To increase their competitiveness, many businesses have turned to lean manufacturing. Economists think that lean manufacturing is a crucial factor in economic recovery.
Lean manufacturing has many benefits in the automotive sector. These include higher customer satisfaction levels, reduced inventory levels as well as lower operating costs.
Lean manufacturing can be applied to almost every aspect of an organization. It is especially useful for the production aspect of an organization, as it ensures that every step in the value chain is efficient and effective.
There are three main types:
-
Just-in Time Manufacturing (JIT), also known as "pull system": This form of lean manufacturing is often referred to simply as "pull". JIT stands for a system where components are assembled on the spot rather than being made in advance. This method reduces lead times, increases availability, and decreases inventory.
-
Zero Defects Manufacturing, (ZDM): ZDM is focused on ensuring that no defective products leave the manufacturing facility. If a part is required to be repaired on the assembly line, it should not be scrapped. This applies to finished products, which may need minor repairs before they are shipped.
-
Continuous Improvement (CI): CI aims to improve the efficiency of operations by continuously identifying problems and making changes in order to eliminate or minimize waste. Continuous Improvement (CI) involves continuous improvement in processes, people, tools, and infrastructure.