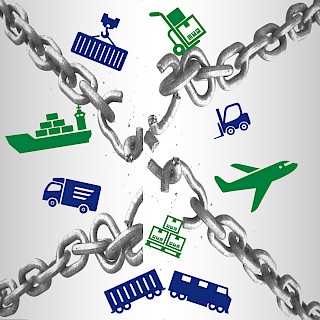
Houston has many opportunities for those who are interested in a career as a logistics professional. There are many job opportunities in this sector, including warehouse jobs, logistic coordinator jobs, and warehouse manager positions. If you are interested to work in the logistics industry you can sign-up for job alerts via email.
Greater Houston has interfaith ministries
Interfaith Ministries Greater Houston is a network of people from diverse faith traditions working together to improve Houston's neighborhoods. These organizations offer services such a meal for homebound seniors, refugee service, and volunteering. They promote interfaith relationships and community partnerships. Interfaith Ministries Greater Houston's mission is to unite people from different faith traditions and to build bridges of understanding.
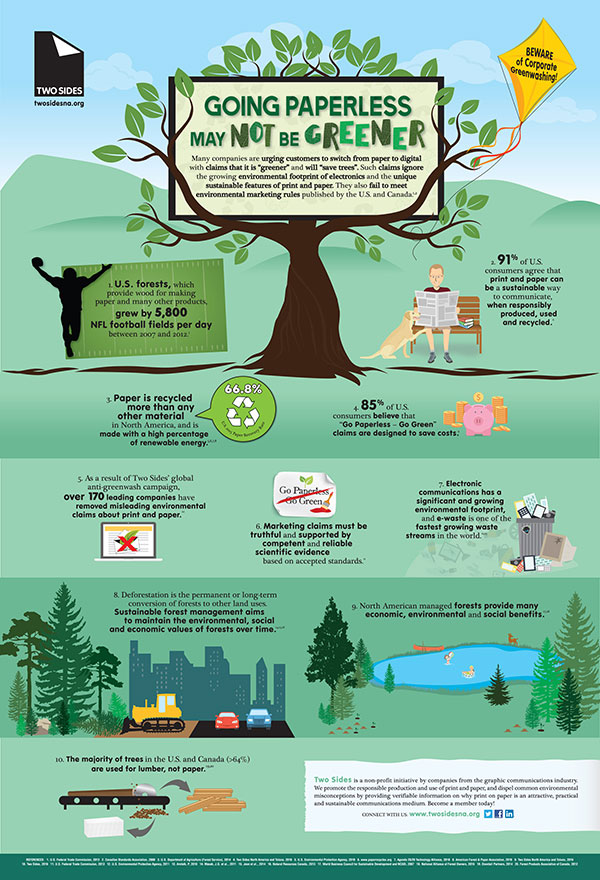
The Church Welfare Bureau was the original organization that founded the organization. This bureau organized the Protestant community in order to minister to the needy. The organization was reorganized under the name of Protestant Charities in 1964 and expanded to include Jewish people. Houston Metropolitan Ministries was established as the charter organization for Interfaith Ministries Greater Houston in 1969. Since then, Interfaith Ministries has served the Houston area.
The Refugee Services Program at Interfaith Ministries in Greater Houston helps resettle refugees fleeing persecution. This organization is a partner with Episcopal Migration Ministries, and the U.S. State Department in helping refugees settle in Houston. They assist clients in becoming self-sufficient and productive members within six months. Every year, this program aids hundreds of refugees.
Logistics careers
There are many career options in Houston logistics. These include positions at transportation companies, manufacturing companies, and third-party logistic companies. These positions can be found in either a domestic or foreign organization. These professionals are often paid more than the national average, and there are many opportunities to advance. Logistics professionals are also in high demand for jobs with governmental agencies and consulting firms. For students interested in many industries, a logistics degree opens up many career opportunities. The salaries and opportunities for advancement in this field are limitless.
Houston is a wonderful place to start a job in logistics. Houston's growing economy is an excellent place to both live and work. The city offers a high salary and many top companies. Careers in Houston logistics can be a good fit for those with an interest in international business.
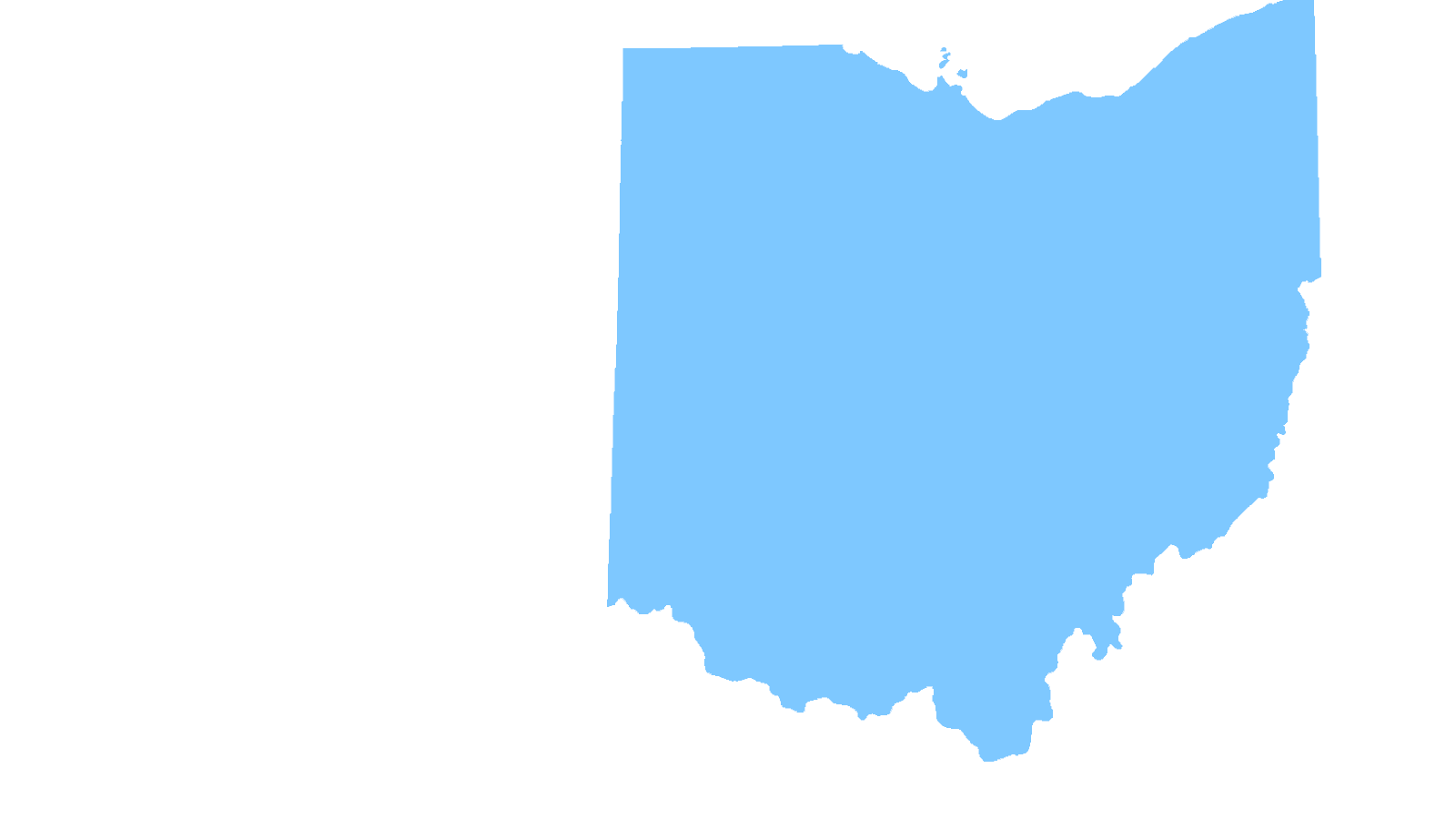
Job description
Whether you're looking for a full-time or part-time job, there are several opportunities in the Houston logistics field. The area is home to many businesses, making a career in logistics a rewarding one. These positions range from working for transportation and manufacturing firms to working for educational institutions and government agencies. No matter your background, logistics jobs are great for those who want to advance their careers.
FAQ
Is there anything we should know about Manufacturing Processes prior to learning about Logistics.
No. No. However, knowing about manufacturing processes will definitely give you a better understanding of how logistics works.
What do you mean by warehouse?
A warehouse is a place where goods are stored until they are sold. It can be an indoor space or an outdoor area. In some cases, it may be a combination of both.
How can efficiency in manufacturing be improved?
First, we need to identify which factors are most critical in affecting production times. We then need to figure out how to improve these variables. If you aren't sure where to begin, think about the factors that have the greatest impact on production time. Once you identify them, look for solutions.
What are the responsibilities of a manufacturing manager
A manufacturing manager must make sure that all manufacturing processes run smoothly and effectively. They must also be alert to any potential problems and take appropriate action.
They must also be able to communicate with sales and marketing departments.
They should also be aware of the latest trends in their industry and be able to use this information to help improve productivity and efficiency.
Why is logistics important in manufacturing
Logistics are essential to any business. They help you achieve great results by helping you manage all aspects of product flow, from raw materials to finished goods.
Logistics also play a major role in reducing costs and increasing efficiency.
What is production planning?
Production Planning involves developing a plan for all aspects of the production, including scheduling, budgeting, casting, crew, location, equipment, props, etc. It is important to have everything ready and planned before you start shooting. This document should include information about how to achieve the best results on-set. This information includes locations, crew details and equipment requirements.
The first step is to outline what you want to film. You may have decided where to shoot or even specific locations you want to use. Once you have identified the scenes and locations, you can start to determine which elements are required for each scene. You might decide you need a car, but not sure what make or model. In this case, you could start looking up cars online to find out what models are available and then narrow your choices by choosing between different makes and models.
After you've found the perfect car, it's time to start thinking about adding extras. Do you need people sitting in the front seats? You might also need someone to help you get around the back. You may want to change the interior's color from black or white. These questions can help you decide the right look for your car. Another thing you can do is think about what type of shots are desired. Are you going to be shooting close-ups? Or wide angles? Maybe the engine or steering wheel is what you are looking to film. These factors will help you determine which car style you want to film.
Once you have established all the details, you can create a schedule. You can use a schedule to determine when and where you need it to be shot. The schedule will show you when to get there, what time to leave, and when to return home. It will help everyone know exactly what they have to do and when. You can also make sure to book extra staff in advance if you have to hire them. There is no point in hiring someone who won't turn up because you didn't let him know.
You will need to factor in the days that you have to film when creating your schedule. Some projects may only take a couple of days, while others could last for weeks. While creating your schedule, it is important to remember whether you will require more than one shot per day. Multiple takes at the same place will result in higher costs and longer completion times. You can't be certain if you will need multiple takes so it is better not to shoot too many.
Budgeting is another crucial aspect of production plan. A realistic budget will help you work within your means. Remember that you can always reduce the budget later on if you run into unforeseen problems. However, you shouldn't overestimate the amount of money you will spend. You'll end up with less money after paying for other things if the cost is underestimated.
Production planning is a detailed process. But, once you understand the workings of everything, it becomes easier for future projects to be planned.
Statistics
- (2:04) MTO is a production technique wherein products are customized according to customer specifications, and production only starts after an order is received. (oracle.com)
- According to a Statista study, U.S. businesses spent $1.63 trillion on logistics in 2019, moving goods from origin to end user through various supply chain network segments. (netsuite.com)
- In 2021, an estimated 12.1 million Americans work in the manufacturing sector.6 (investopedia.com)
- Job #1 is delivering the ordered product according to specifications: color, size, brand, and quantity. (netsuite.com)
- In the United States, for example, manufacturing makes up 15% of the economic output. (twi-global.com)
External Links
How To
How to use the Just-In Time Method in Production
Just-intime (JIT), which is a method to minimize costs and maximize efficiency in business process, is one way. It is a process where you get the right amount of resources at the right moment when they are needed. This means that only what you use is charged to your account. The term was first coined by Frederick Taylor, who developed his theory while working as a foreman in the early 1900s. He saw how overtime was paid to workers for work that was delayed. He decided that workers would be more productive if they had enough time to complete their work before they started to work.
JIT teaches you to plan ahead and prepare everything so you don’t waste time. The entire project should be looked at from start to finish. You need to ensure you have enough resources to tackle any issues that might arise. You'll be prepared to handle any potential problems if you know in advance. This way you won't be spending more on things that aren’t really needed.
There are different types of JIT methods:
-
Demand-driven: This JIT is where you place regular orders for the parts/materials that are needed for your project. This will allow to track how much material has been used up. You'll also be able to estimate how long it will take to produce more.
-
Inventory-based : You can stock the materials you need in advance. This allows you to forecast how much you will sell.
-
Project-driven : This is a method where you make sure that enough money is set aside to pay the project's cost. When you know how much you need, you'll purchase the appropriate amount of materials.
-
Resource-based: This is the most common form of JIT. You allocate resources based on the demand. For example, if there is a lot of work coming in, you will have more people assigned to them. If you don't have many orders, you'll assign fewer people to handle the workload.
-
Cost-based: This is the same as resource-based except that you don't care how many people there are but how much each one of them costs.
-
Price-based: This is a variant of cost-based. However, instead of focusing on the individual workers' costs, this looks at the total price of the company.
-
Material-based is an alternative to cost-based. Instead of looking at the total cost in the company, this method focuses on the average amount of raw materials that you consume.
-
Time-based JIT: A variation on resource-based JIT. Instead of focusing solely on the amount each employee costs, focus on how long it takes for the project to be completed.
-
Quality-based JIT - This is another form of resource-based JIT. Instead of thinking about the cost of each employee or the time it takes to produce something, you focus on how good your product quality.
-
Value-based: This is one of the newest forms of JIT. You don't worry about whether the products work or if they meet customer expectations. Instead, you are focused on adding value to the marketplace.
-
Stock-based: This stock-based method focuses on the actual quantity of products being made at any given time. It's used when you want to maximize production while minimizing inventory.
-
Just-intime planning (JIT), is a combination JIT/sales chain management. This refers to the scheduling of the delivery of components as soon after they are ordered. It's important as it reduces leadtimes and increases throughput.