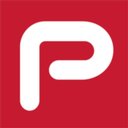
They use their creativity and technical knowledge to find solutions to problems. They can be asked to prepare and analyze reports or test equipment.
Apart from the technical skills, a mechanical engineer must also have communication skills and the ability work with people from different backgrounds. This skill is essential for complex jobs that require a team of people. For a position in mechanical engineering, a resume should be concise and clearly written. Bullet points are helpful to highlight each skill. Including action words can also add extra oomph to your resume.
This role requires excellent communication skills, both written and verbal. You must be able to explain complicated machines and tools to non-mechanical engineers, and you must be willing to present your ideas and findings in a professional manner. Your ability to communicate effectively can make or break your chances of being selected for a specific job.
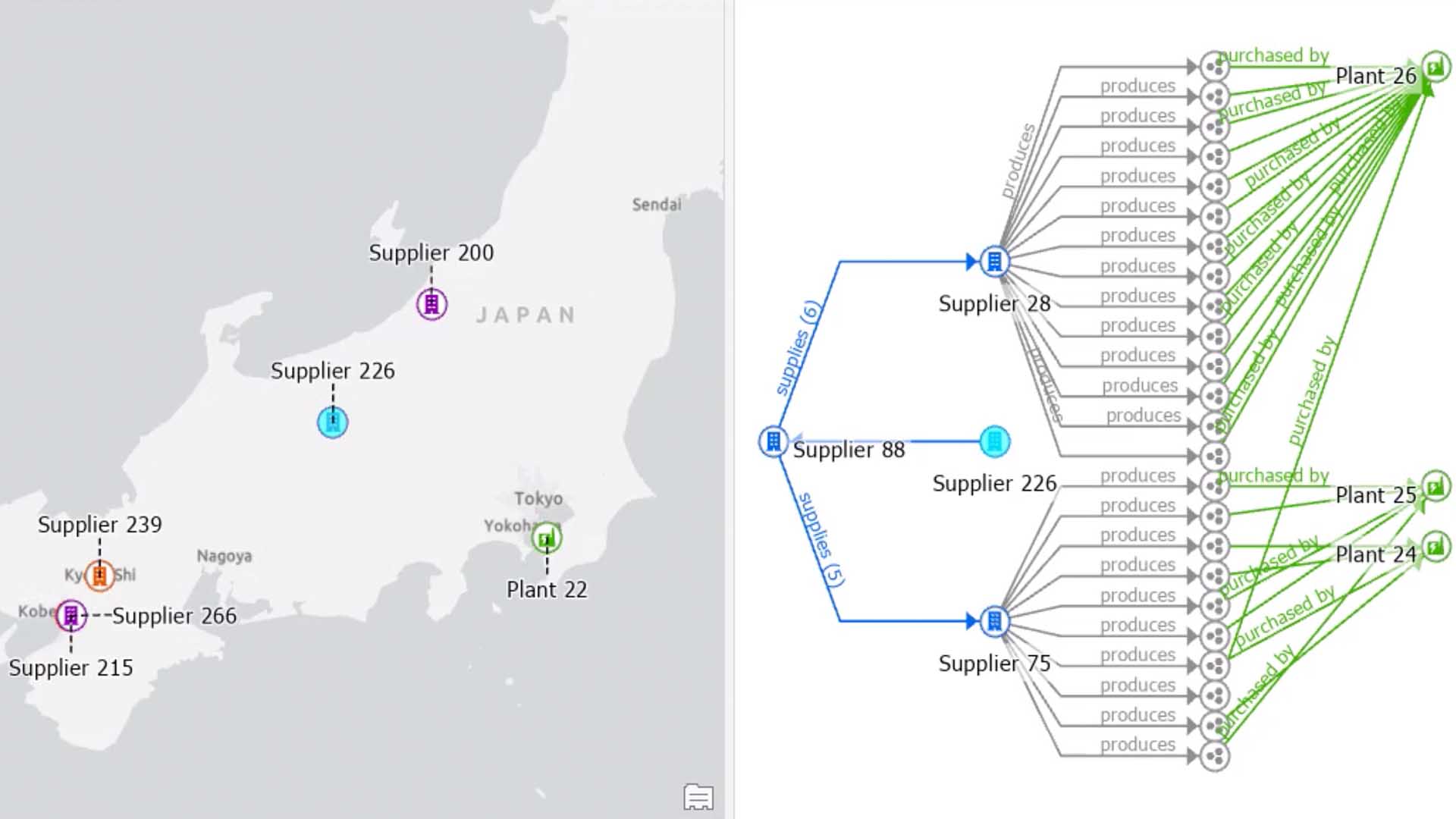
You must also have an understanding of how to use CAD (computer-aided design) programs. These programs can be used to create 3D models of parts or drawings. No matter whether you are using a computer to create 3D models of parts or a mechanical machine, communicating the details of your designs is crucial.
You should list your education history and achievements on your resume. It is a good idea to list any degree you have in a related area along with your graduation date. However, if you have a degree from more than ten years ago, you should not include this. Potential employers will be able to see your education by adding it.
Also, include any professional awards or accomplishments. This will demonstrate to potential employers that your experience spans a wide range of industries. You should also include any internships. It is important that you list your academic and professional accomplishments, but it is also crucial to express your passion for the field.
Most of the technical skills needed by a mechanical engineer can be learned on-the-job. These skills include FEA (Finite Element Analysis), simulation software, and CAD software. Other skills, like stress analysis, can be acquired through certifications.
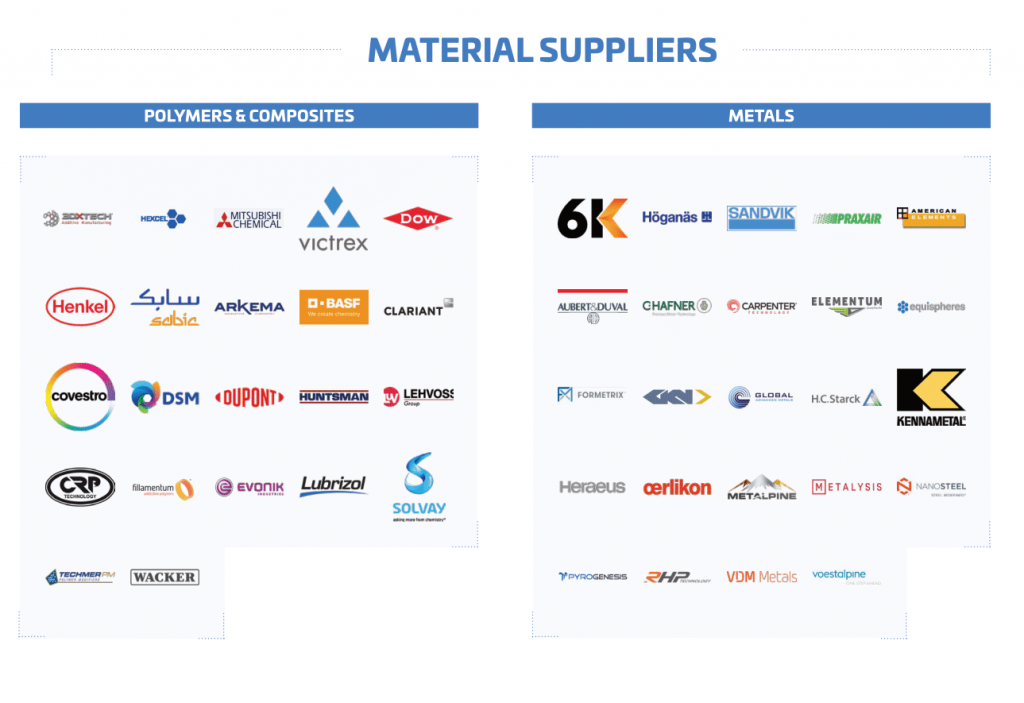
The soft skills that are necessary to succeed in the field of mechanical engineering are those that are difficult to measure. They are equally important as the hard skills. These include your problem solving skills, creativity, and leadership skills.
It is important to highlight the most noteworthy projects you have worked on when applying for a position in mechanical engineering. These projects will show your ability to work well with others and demonstrate your problem-solving abilities. Also, consider the skills you might have that could be useful in other roles.
You must be a leader and inspire others to solve problems. You need to assign roles, motivate your team members to accomplish their goals, as well as make sure that everyone is aware and focused on the end goal.
FAQ
What is the job of a manufacturer manager?
Manufacturing managers must ensure that manufacturing processes are efficient, effective, and cost-effective. They should be aware of any issues within the company and respond accordingly.
They should also learn how to communicate effectively with other departments, including sales and marketing.
They should be informed about industry trends and be able make use of this information to improve their productivity and efficiency.
Can some manufacturing processes be automated?
Yes! Automation has been around since ancient times. The Egyptians invented the wheel thousands of years ago. Today, robots assist in the assembly of lines.
There are many applications for robotics in manufacturing today. These include:
-
Assembly line robots
-
Robot welding
-
Robot painting
-
Robotics inspection
-
Robots that create products
Automation could also be used to improve manufacturing. 3D printing makes it possible to produce custom products in a matter of days or weeks.
What is production management?
Production Planning refers to the development of a plan for every aspect of production. This document aims to ensure that everything is planned and ready when you are ready to shoot. You should also have information to ensure the best possible results on set. It should include information about shooting locations, casting lists, crew details, equipment requirements, and shooting schedules.
First, you need to plan what you want to film. You might have an idea of where you want to film, or you may have specific locations or sets in mind. Once you have identified your locations and scenes, you can start working out which elements you require for each scene. For example, you might decide that you need a car but don't know exactly what model you want. You could look online for cars to see what options are available, and then narrow down your choices by selecting between different makes or models.
After you have chosen the right car, you will be able to begin thinking about accessories. Do you need people sitting in the front seats? You might also need someone to help you get around the back. You might want to change your interior color from black and white. These questions can help you decide the right look for your car. You can also think about the type of shots you want to get. Do you want to film close-ups, or wider angles? Maybe the engine or steering wheel is what you are looking to film. This will allow you to determine the type of car you want.
Once you have all the information, you are ready to create a plan. The schedule will show you when to begin shooting and when to stop. The schedule will show you when to get there, what time to leave, and when to return home. This way, everyone knows what they need to do and when. If you need to hire extra staff, you can make sure you book them in advance. It is not worth hiring someone who won’t show up because you didn’t tell him.
It is important to calculate the amount of filming days when you are creating your schedule. Some projects are quick and easy, while others take weeks. You should consider whether you will need more than one shot per week when creating your schedule. Multiple takes of the same location will lead to higher costs and take more time. If you are unsure if you need multiple takes, it is better to err on the side of caution and shoot fewer takes rather than risk wasting money.
Budget setting is an important part of production planning. You will be able to manage your resources if you have a realistic budget. Remember that you can always reduce the budget later on if you run into unforeseen problems. However, it is important not to overestimate the amount that you will spend. If you underestimate the cost of something, you will have less money left after paying for other items.
Planning production is a tedious process. Once you have a good understanding of how everything works together, planning future projects becomes easy.
What jobs are available in logistics?
There are many kinds of jobs available within logistics. These are some of the jobs available in logistics:
-
Warehouse workers - They load and unload trucks and pallets.
-
Transport drivers - These are people who drive trucks and trailers to transport goods or perform pick-ups.
-
Freight handlers – They sort and package freight at warehouses.
-
Inventory managers: They are responsible for the inventory and management of warehouses.
-
Sales reps - They sell products and services to customers.
-
Logistics coordinators – They plan and coordinate logistics operations.
-
Purchasing agents are those who purchase goods and services for the company.
-
Customer service representatives – They answer emails and phone calls from customers.
-
Shipping clerks: They process shipping requests and issue bills.
-
Order fillers - These people fill orders based on what has been ordered.
-
Quality control inspectors (QCI) - They inspect all incoming and departing products for potential defects.
-
Others – There are many other types available in logistics. They include transport supervisors, cargo specialists and others.
How can we improve manufacturing efficiency?
First, we need to identify which factors are most critical in affecting production times. Next, we must find ways to improve those factors. If you don’t know where to begin, consider which factors have the largest impact on production times. Once you have identified them, it is time to identify solutions.
What are the 7 Rs of logistics management?
The 7R's of Logistics is an acronym for the seven basic principles of logistics management. It was developed by International Association of Business Logisticians (IABL), and published as part of their "Seven Principles of Logistics Management Series" in 2004.
The following letters form the acronym:
-
Responsive - ensure all actions are legal and not harmful to others.
-
Reliable - have confidence in the ability to deliver on commitments made.
-
Use resources effectively and sparingly.
-
Realistic – consider all aspects of operations, from cost-effectiveness to environmental impact.
-
Respectful: Treat others with fairness and equity
-
Resourceful - look for opportunities to save money and increase productivity.
-
Recognizable - provide customers with value-added services.
How can manufacturing excess production be decreased?
Improved inventory management is the key to reducing overproduction. This would reduce the time spent on unproductive activities like purchasing, storing and maintaining excess stock. This would allow us to use our resources for more productive tasks.
You can do this by adopting a Kanban method. A Kanban board can be used to monitor work progress. Work items are moved through various states to reach their destination in a Kanban system. Each state represents a different priority.
If work is moving from one stage to the other, then the current task can be completed and moved on to the next. If a task is still in its beginning stages, it will continue to be so until it reaches the end.
This allows for work to continue moving forward, while also ensuring that there is no work left behind. Managers can see how much work has been done and the status of each task at any time with a Kanban Board. This information allows them to adjust their workflow based on real-time data.
Lean manufacturing is another option to control inventory levels. Lean manufacturing focuses on eliminating waste throughout the entire production chain. Anything that doesn't add value to the product is considered waste. Here are some examples of common types.
-
Overproduction
-
Inventory
-
Packaging that is not necessary
-
Excess materials
These ideas will help manufacturers increase efficiency and lower costs.
Statistics
- [54][55] These are the top 50 countries by the total value of manufacturing output in US dollars for its noted year according to World Bank.[56] (en.wikipedia.org)
- (2:04) MTO is a production technique wherein products are customized according to customer specifications, and production only starts after an order is received. (oracle.com)
- It's estimated that 10.8% of the U.S. GDP in 2020 was contributed to manufacturing. (investopedia.com)
- According to a Statista study, U.S. businesses spent $1.63 trillion on logistics in 2019, moving goods from origin to end user through various supply chain network segments. (netsuite.com)
- You can multiply the result by 100 to get the total percent of monthly overhead. (investopedia.com)
External Links
How To
How to Use 5S to Increase Productivity in Manufacturing
5S stands to stand for "Sort", “Set In Order", “Standardize", and "Store". Toyota Motor Corporation created the 5S methodology in 1954. It assists companies in improving their work environments and achieving higher efficiency.
This method has the basic goal of standardizing production processes to make them repeatable. Cleaning, sorting and packing are all done daily. This knowledge allows workers to be more efficient in their work because they are aware of what to expect.
There are five steps to implementing 5S, including Sort, Set In Order, Standardize, Separate and Store. Each step has a different action and leads to higher efficiency. Sorting things makes it easier to find them later. When you set items in an order, you put items together. You then organize your inventory in groups. Labeling your containers will ensure that everything is correctly labeled.
This requires employees to critically evaluate how they work. Employees need to understand the reasons they do certain jobs and determine if there is a better way. They must learn new skills and techniques in order to implement the 5S system.
In addition to increasing efficiency, the 5S method also improves morale and teamwork among employees. They feel more motivated to work towards achieving greater efficiency as they see the results.