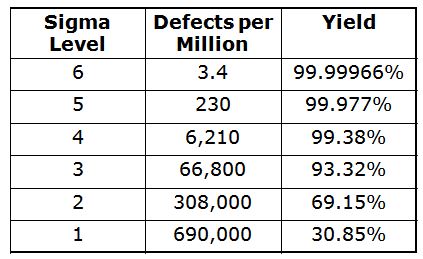
Hoshinkanri, Visual board and Value Stream mapping are just a few tools that make up the lean toolbox. These tools use statistical data and quality control to reduce defects and improve processes performance. Lean tools are also beneficial for improving safety and health of employees, as well the delivery and cycle times and raw material quality. You can find more information in our articles about these tools. These articles also provide examples and explain the basics of these tools.
Hoshinkanri
When it comes to implementing the principles of Hoshin Kanri, it's crucial to communicate the goals of each department to each other. It is essential to communicate clearly the company's goals and the results they produce. Google Images provides a sample Hoshin Kanri Matrix. The matrix's main purpose is to ensure that everyone is working towards the same goals.
Hoshin Kanri is an inclusive approach that will help you determine what areas of your business are in need of improvement. The Hoshin Kanri method helps you identify the most important activities and help you create a clear path that leads from your general goals to specific actions. It can help you visualize the relationship between each step and how it relates to others. Compared to boring business plans, Hoshin Kanri encourages a collaborative approach to improving the overall company.
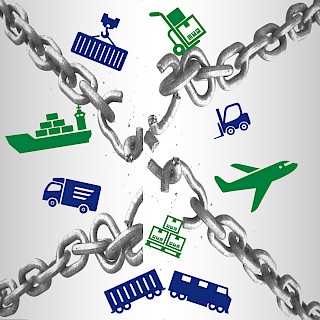
Visual board
The visual board can be used to measure the process's results, but it is not universal. It is only useful when there are people involved in the implementation. To create emotion behind the numbers, a visual management board must be made for each user. You can use it to track performance indicators such as the number of pieces produced in a given time or the hours worked. While there is no universal code for this tool, there are several key elements that make it useful in a lean production environment.
A visual management board allows you to communicate quickly to your team members what is needed and who is responsible for each task. This information can all be viewed on a board in less that 20 seconds. To ensure that everyone on the same page, managers must also see results from these activities. A visual management board can be updated regularly to make sure that everyone is on the same page.
Value Stream Mapping
When using value stream mapping in tools lean, a facilitator must identify the bottleneck or constraint in the process. A bottleneck is the process step with the highest WIP. If a process is three steps long and has a throughput of 60 units/hour but a potential WIP rate of 42 units/hour, then Step 2 would be the bottleneck. The value stream map can be used as a guide to pinpoint bottlenecks, and identify opportunities for process improvement.
To properly conduct a value stream mapping, it is important to understand the system or process and the customer's perspective. This is often a multi-functional and complex process. It may require training and extensive involvement from several people. Larger companies might hire a value stream manager to lead the mapping. Even though value stream mapping is a huge undertaking, it can be done by smaller companies that help to identify areas for improvement and possible savings. A powerful tool in tools Lean is value stream mapping.
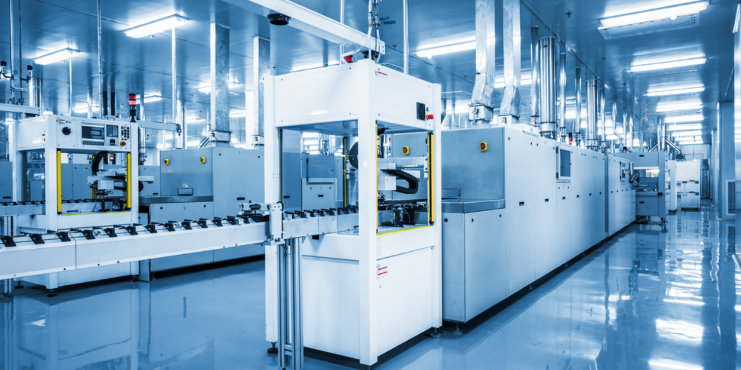
Process observation, analysis
Lean management is built on the concepts of continuous improvement, process observation and quality control. Process observation is used to verify that standards are being met and that processes are producing the desired results. Processes that are abandoned will eventually fail. Process observation and analysis may have cultural implications. Managers should clearly communicate the reasons for process observation and the potential benefits. Lean management systems include process observation and analysis. Managers need to communicate the importance of this part to their teams.
First, verifying the process flow map is essential to implement Lean. This can be done by walking through the process. Once the process flow map has been verified, the next step will be to analyze the data. In the Measure phase, the team collects data on the current process, product, or service. The project leader applies statistical hypotheses testing techniques to pinpoint the root cause. The analysis determines if the problem has been eliminated or improved.
FAQ
What does it take to run a logistics business?
It takes a lot of skills and knowledge to run a successful logistics business. Effective communication skills are necessary to work with suppliers and clients. You should be able analyse data and draw inferences. You need to be able work under pressure and manage stressful situations. In order to innovate and create new ways to improve efficiency, creativity is essential. Strong leadership qualities are essential to motivate your team and help them achieve their organizational goals.
To meet tight deadlines, you must also be efficient and organized.
What does manufacturing industry mean?
Manufacturing Industries refers to businesses that manufacture products. Consumers are people who purchase these goods. These companies use a variety processes such as distribution, retailing and management to accomplish their purpose. These companies produce goods using raw materials and other equipment. This includes all types of manufactured goods, including food items, clothing, building supplies, furniture, toys, electronics, tools, machinery, vehicles, pharmaceuticals, medical devices, chemicals, and many others.
What is the role of a logistics manager
Logistics managers make sure all goods are delivered on schedule and without damage. This is achieved by using their knowledge and experience with the products of the company. He/she should make sure that enough stock is on hand to meet the demands.
How is a production manager different from a producer planner?
The difference between a product planner and project manager is that a planer is typically the one who organizes and plans the entire project. A production planner, however, is mostly involved in the planning stages.
How can we increase manufacturing efficiency?
First, we need to identify which factors are most critical in affecting production times. We then need to figure out how to improve these variables. You can start by identifying the most important factors that impact production time. Once you have identified them, it is time to identify solutions.
How can manufacturing excess production be decreased?
The key to reducing overproduction lies in developing better ways to manage inventory. This would reduce the time spent on unproductive activities like purchasing, storing and maintaining excess stock. We could use these resources to do other productive tasks.
One way to do this is to adopt a Kanban system. A Kanbanboard is a visual tool that allows you to keep track of the work being done. Work items are moved through various states to reach their destination in a Kanban system. Each state represents an individual priority level.
If work is moving from one stage to the other, then the current task can be completed and moved on to the next. If a task is still in its beginning stages, it will continue to be so until it reaches the end.
This helps to keep work moving forward while ensuring that no work is left behind. Managers can monitor the work being done by Kanban boards to see what is happening at any given time. This allows them the ability to adjust their workflow using real-time data.
Lean manufacturing is another option to control inventory levels. Lean manufacturing is about eliminating waste from all stages of the production process. Anything that does not contribute to the product's value is considered waste. Here are some examples of common types.
-
Overproduction
-
Inventory
-
Packaging not required
-
Material surplus
Manufacturers can reduce their costs and improve their efficiency by using these ideas.
What are the 4 types manufacturing?
Manufacturing refers to the transformation of raw materials into useful products by using machines and processes. It includes many different activities like designing, building and testing, packaging, shipping and selling, as well as servicing.
Statistics
- [54][55] These are the top 50 countries by the total value of manufacturing output in US dollars for its noted year according to World Bank.[56] (en.wikipedia.org)
- You can multiply the result by 100 to get the total percent of monthly overhead. (investopedia.com)
- (2:04) MTO is a production technique wherein products are customized according to customer specifications, and production only starts after an order is received. (oracle.com)
- According to a Statista study, U.S. businesses spent $1.63 trillion on logistics in 2019, moving goods from origin to end user through various supply chain network segments. (netsuite.com)
- In the United States, for example, manufacturing makes up 15% of the economic output. (twi-global.com)
External Links
How To
How to Use Just-In-Time Production
Just-in-time (JIT) is a method that is used to reduce costs and maximize efficiency in business processes. It's the process of obtaining the right amount and timing of resources when you need them. This means that you only pay the amount you actually use. Frederick Taylor was the first to coin this term. He developed it while working as a foreman during the early 1900s. He observed how workers were paid overtime if there were delays in their work. He concluded that if workers were given enough time before they start work, productivity would increase.
JIT is a way to plan ahead and make sure you don't waste any money. Also, you should look at the whole project from start-to-finish and make sure you have the resources necessary to address any issues. You'll be prepared to handle any potential problems if you know in advance. This way you won't be spending more on things that aren’t really needed.
There are different types of JIT methods:
-
Demand-driven JIT: You order the parts and materials you need for your project every other day. This will allow to track how much material has been used up. This will let you know how long it will be to produce more.
-
Inventory-based : You can stock the materials you need in advance. This allows for you to anticipate how much you can sell.
-
Project-driven: This approach involves setting aside sufficient funds to cover your project's costs. Once you have an idea of how much material you will need, you can purchase the necessary materials.
-
Resource-based JIT is the most widespread form. Here, you allocate certain resources based on demand. If you have many orders, you will assign more people to manage them. If you don't receive many orders, then you'll assign fewer employees to handle the load.
-
Cost-based: This is the same as resource-based except that you don't care how many people there are but how much each one of them costs.
-
Price-based: This is similar to cost-based but instead of looking at individual workers' salaries, you look at the total company price.
-
Material-based: This is quite similar to cost-based, but instead of looking at the total cost of the company, you're concerned with how much raw materials you spend on average.
-
Time-based: This is another variation of resource-based JIT. Instead of focusing only on how much each employee is costing, you should focus on how long it takes to complete your project.
-
Quality-based JIT - This is another form of resource-based JIT. Instead of thinking about the cost of each employee or the time it takes to produce something, you focus on how good your product quality.
-
Value-based JIT is the newest form of JIT. You don't worry about whether the products work or if they meet customer expectations. Instead, you're focused on how much value you add to the market.
-
Stock-based is an inventory-based system that measures the number of items produced at any given moment. This is used to increase production and minimize inventory.
-
Just-intime planning (JIT), is a combination JIT/sales chain management. It is the process of scheduling components' delivery as soon as they have been ordered. It reduces lead times and improves throughput.