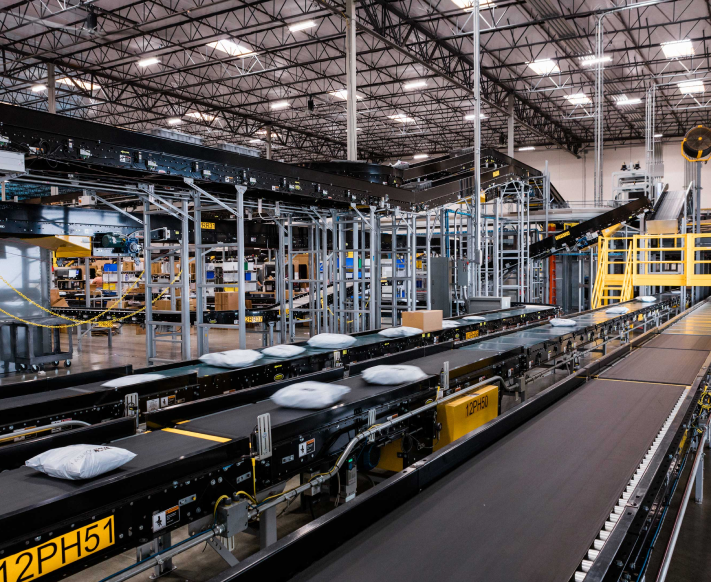
They are responsible for all aspects of purchasing, including sourcing and coordination. They interact with suppliers, vendors, and other purchasing agents. They need to have a good understanding of the company's purchasing process, and how to improve it. They should also be able negotiate the best deals on behalf of the company.
A purchasing manager also needs to have accurate and current records regarding purchases. They analyse customer requirements, assess financial reports, evaluate vendor capabilities and evaluate price trends. They also coordinate purchasing activities. They might be required to work extra hours if supplies are needed from overseas markets.
Coordinate and manage inventory, logistics and other activities. They also determine the best purchasing method and make sure that all purchased items meet company quality standards. They help to manage budgets and coordinate with their staff to ensure that purchases can be made at the most affordable price. They are also able to negotiate contracts and find the best suppliers.
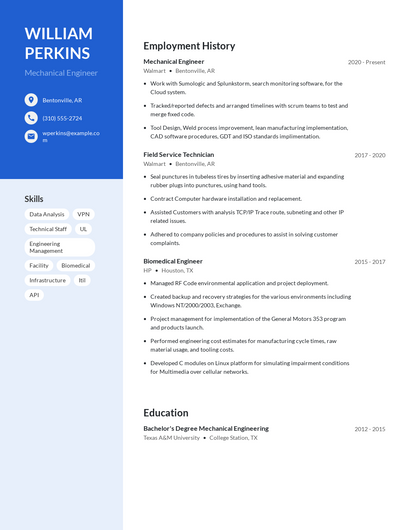
The time schedules and performance of purchasing employees are also managed by purchasing managers. They also evaluate the quality of goods purchased, their speed of delivery and how much they cost. They also visit distributor centers and make contact with sellers. They also check that suppliers are adhering to the terms of the contract. They may also have to deal with disciplinary issues and team building.
Purchasing Managers must have excellent communication skills, analytical abilities, and strategic thinking skills. They must be able and able to analyse the effect of different products on a company. They must also be able to manage suppliers and their relationships. They should also have the ability to make business decisions and to increase sales. They should be able manage complicated purchases. They must be able to evaluate new vendors, analyze their capabilities, and select the best vendor for the company.
Most purchasing managers have to have a bachelor's degree in business or a related field. It is also helpful if they have experience in inventory management and supply chain management. They should also be familiar with Microsoft Office and other software programs.
The best purchasing manager should be able to find the best deals and negotiate the most favorable contracts. They should be able to coordinate all purchases, manage inventories, and keep track on supplier and vendor performance. They must also be able to manage a group of purchasing agents.
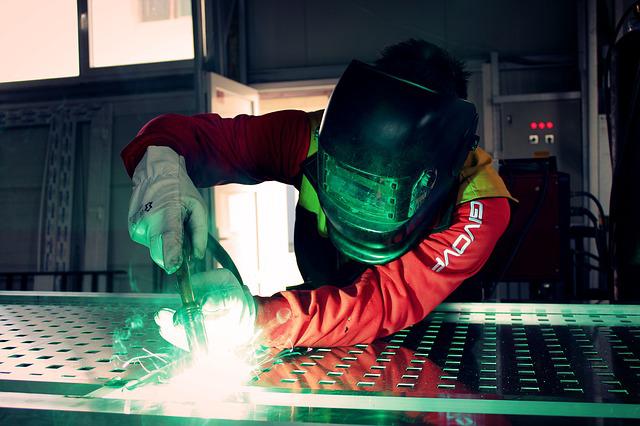
It is important that the job description for a purchase manager mentions how essential purchasing is to the company's success. It should mention how important it's for the company to stay ahead. It should also include a statement about how the company values employees' work-life balance. It should also include a call to action to urge applicants to apply.
If the company requires equipment or materials to be purchased for an international market, purchasing managers may work overtime. They may also need to deal with sellers and buyers or attend trade shows.
FAQ
What is production planning?
Production Planning refers to the development of a plan for every aspect of production. This document is designed to make sure everything is ready for when you're ready to shoot. This document should include information about how to achieve the best results on-set. This includes location information, crew details, equipment specifications, and casting lists.
The first step is to outline what you want to film. You may have already chosen the location you want, or there are locations or sets you prefer. Once you have identified the scenes and locations, you can start to determine which elements are required for each scene. For example, you might decide that you need a car but don't know exactly what model you want. In this case, you could start looking up cars online to find out what models are available and then narrow your choices by choosing between different makes and models.
Once you have found the right vehicle, you can think about adding accessories. You might need to have people in the front seats. Or maybe you just need someone to push the car around. Perhaps you would like to change the interior colour from black to white. These questions will help guide you in determining the ideal look and feel for your car. It is also worth considering the types of shots that you wish to take. Will you be filming close-ups or wide angles? Maybe the engine or steering wheel is what you are looking to film. All of these things will help you identify the exact style of car you want to film.
Once you have made all the necessary decisions, you can start to create a schedule. The schedule will show you when to begin shooting and when to stop. A schedule for each day will detail when you should arrive at the location and when you need leave. So everyone is clear about what they need to do. Hire extra staff by booking them ahead of time. It's not worth paying someone to show up if you haven't told him.
It is important to calculate the amount of filming days when you are creating your schedule. Some projects can be completed in a matter of days or weeks. Others may take several days. You should consider whether you will need more than one shot per week when creating your schedule. Multiplying takes in the same area will result both in increased costs and a longer time. It is better to be cautious and take fewer shots than you risk losing money if you are not sure if multiple takes are necessary.
Budgeting is another important aspect of production planning. It is important to set a realistic budget so you can work within your budget. Keep in mind that you can always reduce your budget if you face unexpected difficulties. However, it is important not to overestimate the amount that you will spend. You'll end up with less money after paying for other things if the cost is underestimated.
Production planning can be a complex process. However, once you know how everything works together it will become easier to plan future projects.
What are the goods of logistics?
Logistics refers to the movement of goods from one place to another.
They include all aspects of transport, including packaging, loading, transporting, unloading, storing, warehousing, inventory management, customer service, distribution, returns, and recycling.
Logisticians make sure that the right product arrives at the right place at the correct time and in safe conditions. They provide information on demand forecasts as well stock levels, production schedules and availability of raw material.
They keep track and monitor the transit of shipments, maintain quality standards, order replenishment and inventories, coordinate with suppliers, vendors, and provide support for sales and marketing.
Why automate your warehouse?
Modern warehouses have become more dependent on automation. With the rise of ecommerce, there is a greater demand for faster delivery times as well as more efficient processes.
Warehouses should be able adapt quickly to new needs. Technology is essential for warehouses to be able to adapt quickly to changing needs. The benefits of automating warehouses are numerous. Here are some reasons why it's worth investing in automation:
-
Increases throughput/productivity
-
Reduces errors
-
Improves accuracy
-
Safety increases
-
Eliminates bottlenecks
-
Allows companies to scale more easily
-
Increases efficiency of workers
-
Gives you visibility into all that is happening in your warehouse
-
Enhances customer experience
-
Improves employee satisfaction
-
This reduces downtime while increasing uptime
-
Ensures quality products are delivered on time
-
Removing human error
-
Assure compliance with regulations
What is the importance of automation in manufacturing?
Not only are service providers and manufacturers important, but so is automation. It allows them to offer services faster and more efficiently. In addition, it helps them reduce costs by reducing human errors and improving productivity.
Statistics
- [54][55] These are the top 50 countries by the total value of manufacturing output in US dollars for its noted year according to World Bank.[56] (en.wikipedia.org)
- According to the United Nations Industrial Development Organization (UNIDO), China is the top manufacturer worldwide by 2019 output, producing 28.7% of the total global manufacturing output, followed by the United States, Japan, Germany, and India.[52][53] (en.wikipedia.org)
- In 2021, an estimated 12.1 million Americans work in the manufacturing sector.6 (investopedia.com)
- (2:04) MTO is a production technique wherein products are customized according to customer specifications, and production only starts after an order is received. (oracle.com)
- It's estimated that 10.8% of the U.S. GDP in 2020 was contributed to manufacturing. (investopedia.com)
External Links
How To
How to Use 5S for Increasing Productivity in Manufacturing
5S stands as "Sort", Set In Order", Standardize", Separate" and "Store". Toyota Motor Corporation was the first to develop the 5S approach in 1954. It allows companies to improve their work environment, thereby achieving greater efficiency.
The idea behind standardizing production processes is to make them repeatable and measurable. This means that daily tasks such as cleaning and sorting, storage, packing, labeling, and packaging are possible. This knowledge allows workers to be more efficient in their work because they are aware of what to expect.
Implementing 5S requires five steps. These are Sort, Set In Order, Standardize. Separate. And Store. Each step has a different action and leads to higher efficiency. If you sort items, it makes them easier to find later. When you set items in an order, you put items together. After you have divided your inventory into groups you can store them in easy-to-reach containers. You can also label your containers to ensure everything is properly labeled.
Employees will need to be more critical about their work. Employees must understand why they do certain tasks and decide if there's another way to accomplish them without relying on the old ways of doing things. They must learn new skills and techniques in order to implement the 5S system.
In addition to increasing efficiency, the 5S method also improves morale and teamwork among employees. Once they start to notice improvements, they are motivated to keep working towards their goal of increasing efficiency.