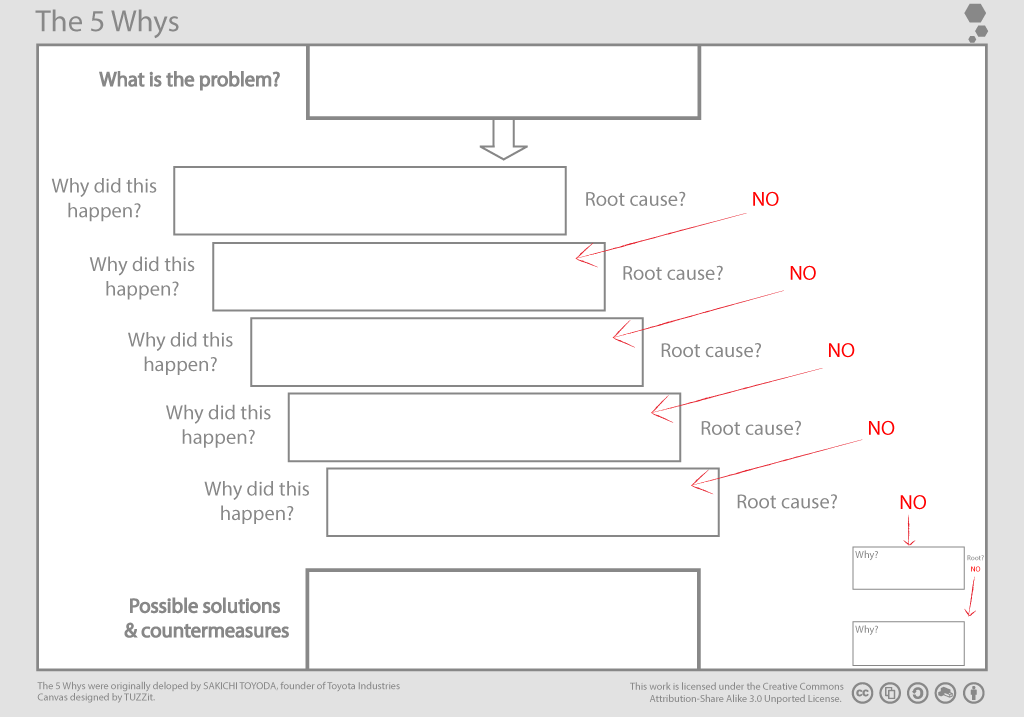
Among the tools in the lean toolbox are Hoshin Kanri, Visual board, Value Stream Mapping, and Process Observation and Analysis. These methods make use of statistical data to identify defects and improve the process' performance. Lean tools can also improve safety and health, cycle time and delivery time, as well as quality and raw material. For more information, read our articles on these tools. We also give examples and explain the basics.
Hoshin Kanri
Communication is key when it comes down to communicating the goals of each division to one another in order to implement the principles of Hoshin Kari. It's important to clearly communicate your company’s objectives and the results you get. Google Images has a sample Hoshin Kanri template. The matrix's main purpose is to ensure that everyone is working towards the same goals.
The Hoshin Kanri method is an inclusive method that can help you identify what aspects of your business need to change and improve. It can help you identify specific activities that need to be changed and also provide a clear path to move from general goals to concrete actions. It helps you track your progress, and shows how each step links to the next. Hoshin Kanri encourages collaboration to improve the company as a whole, rather than boring business plans.
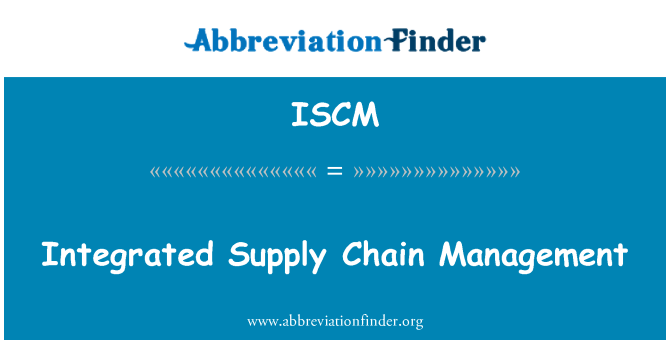
Visual board
While the visual board is a powerful tool for measuring the results of a process, it is not a universal tool. It cannot be used to implement a process that involves people. To create emotion behind the numbers, a visual management board must be made for each user. It can also be used as a tool for monitoring performance indicators such pieces produced in a standard time or labor hours. Although there is no universal code, there a few key elements that make this tool work in a lean environment.
One of the most important aspects of a visual board for management is the ability of all team members to quickly communicate what needs to be done, and who will do each task. In less than 20 seconds, this information can be seen on the board. To ensure that everyone on the same page, managers must also see results from these activities. To ensure everyone is on the same page, a visual management board can easily be created and updated.
Value Stream Mapping
A facilitator should identify the bottleneck in order to use value stream mapping in tools Lean. A bottleneck refers to the process step that has the largest WIP. If a three-step procedure has a throughput speed of 60 units an hour but a potential working capital of 42 units an hour, Step 2 will be the bottleneck. The value stream map can be used as a guide to pinpoint bottlenecks, and identify opportunities for process improvement.
A value stream mapping is only possible if you understand the customer's perspective and the system. This is a complex and cross-functional process. It may require training and extensive involvement from several people. Larger companies might employ a value stream coordinator to manage the mapping. Although value stream mapping may be a big project, smaller projects can identify areas where there are potential savings and improvements. Value stream mapping is a powerful tool in tools lean.
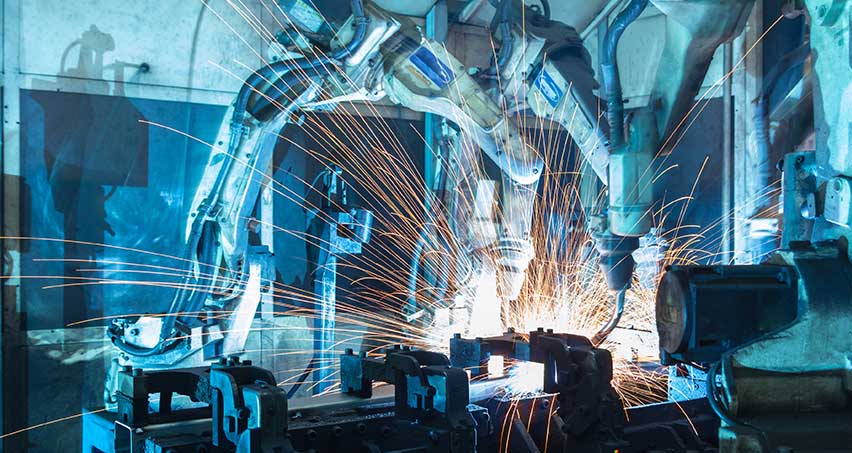
Process Observation and Analysis
Lean management is founded on continuous improvement and process observation. Process observation is designed to maintain standards and ensure processes produce the expected outcomes. Abandoned processes will eventually degrade. Process observation or analysis can have cultural implications. Therefore, managers should explain clearly why they need it and the advantages it brings. Lean management systems include process observation and analysis. Managers need to communicate the importance of this part to their teams.
When implementing Lean, the first step is to verify the process flow map by conducting a walk-through of the process. Once the process flow map has been verified, the next step will be to analyze the data. The Measure phase collects data regarding the current process, product, and/or service. The project leader applies statistical hypotheses testing techniques to pinpoint the root cause. This analyze determines whether the problem has been solved or improved.
FAQ
Are there any Manufacturing Processes that we should know before we can learn about Logistics?
No. You don't have to know about manufacturing processes before learning about logistics. Knowing about manufacturing processes will help you understand how logistics works.
What is the responsibility of a production planner?
A production planner makes sure all project elements are delivered on schedule, within budget, as well as within the agreed scope. They also ensure the quality of the product and service meets the client's requirements.
What type of jobs is there in logistics
There are many types of jobs in logistics. Here are some:
-
Warehouse workers: They load and unload trucks, pallets, and other cargo.
-
Transport drivers - These are people who drive trucks and trailers to transport goods or perform pick-ups.
-
Freight handlers: They sort and package freight in warehouses.
-
Inventory managers: They are responsible for the inventory and management of warehouses.
-
Sales representatives - They sell products to customers.
-
Logistics coordinators are responsible for organizing and planning logistics operations.
-
Purchasing agents - They purchase goods and services needed for company operations.
-
Customer service representatives are available to answer customer calls and emails.
-
Shipping clerks – They process shipping orders, and issue bills.
-
Order fillers are people who fill orders based only on what was ordered.
-
Quality control inspectors are responsible for inspecting incoming and outgoing products looking for defects.
-
Others - There are many other types of jobs available in logistics, such as transportation supervisors, cargo specialists, etc.
What is the importance of logistics in manufacturing?
Logistics are an essential component of any business. They can help you achieve great success by helping you manage product flow from raw material to finished goods.
Logistics play an important role in reducing costs as well as increasing efficiency.
Statistics
- According to the United Nations Industrial Development Organization (UNIDO), China is the top manufacturer worldwide by 2019 output, producing 28.7% of the total global manufacturing output, followed by the United States, Japan, Germany, and India.[52][53] (en.wikipedia.org)
- (2:04) MTO is a production technique wherein products are customized according to customer specifications, and production only starts after an order is received. (oracle.com)
- According to a Statista study, U.S. businesses spent $1.63 trillion on logistics in 2019, moving goods from origin to end user through various supply chain network segments. (netsuite.com)
- Job #1 is delivering the ordered product according to specifications: color, size, brand, and quantity. (netsuite.com)
- In 2021, an estimated 12.1 million Americans work in the manufacturing sector.6 (investopedia.com)
External Links
How To
How to use the Just-In Time Method in Production
Just-in-time is a way to cut costs and increase efficiency in business processes. It allows you to get the right amount resources at the right time. This means that you only pay for what you actually use. Frederick Taylor first coined this term while working in the early 1900s as a foreman. He saw how overtime was paid to workers for work that was delayed. He decided to ensure workers have enough time to do their jobs before starting work to improve productivity.
JIT is a way to plan ahead and make sure you don't waste any money. It is important to look at your entire project from beginning to end and ensure that you have enough resources to handle any issues that may arise. You can anticipate problems and have enough equipment and people available to fix them. This will ensure that you don't spend more money on things that aren't necessary.
There are many JIT methods.
-
Demand-driven: This type of JIT allows you to order the parts/materials required for your project on a regular basis. This will let you track the amount of material left over after you've used it. This will allow to you estimate the time it will take for more to be produced.
-
Inventory-based: You stock materials in advance to make your projects easier. This allows you predict the amount you can expect to sell.
-
Project-driven : This is a method where you make sure that enough money is set aside to pay the project's cost. Once you have an idea of how much material you will need, you can purchase the necessary materials.
-
Resource-based JIT : This is probably the most popular type of JIT. Here, you allocate certain resources based on demand. For example, if there is a lot of work coming in, you will have more people assigned to them. If you don't receive many orders, then you'll assign fewer employees to handle the load.
-
Cost-based: This approach is very similar to resource-based. However, you don't just care about the number of people you have; you also need to consider how much each person will cost.
-
Price-based: This is similar to cost-based but instead of looking at individual workers' salaries, you look at the total company price.
-
Material-based: This is very similar to cost-based but instead of looking at total costs of the company you are concerned with how many raw materials you use on an average.
-
Time-based: Another variation of resource-based JIT. Instead of worrying about how much each worker costs, you can focus on how long the project takes.
-
Quality-based JIT is another variant of resource-based JIT. Instead of thinking about the cost of each employee or the time it takes to produce something, you focus on how good your product quality.
-
Value-based JIT: One of the most recent forms of JIT. In this instance, you are not concerned about the product's performance or meeting customer expectations. Instead, your goal is to add value to the market.
-
Stock-based: This inventory-based approach focuses on how many items are being produced at any one time. This is used to increase production and minimize inventory.
-
Just-in-time planning (JIT): This is a combination JIT and supply-chain management. This refers to the scheduling of the delivery of components as soon after they are ordered. This is important as it reduces lead time and increases throughput.