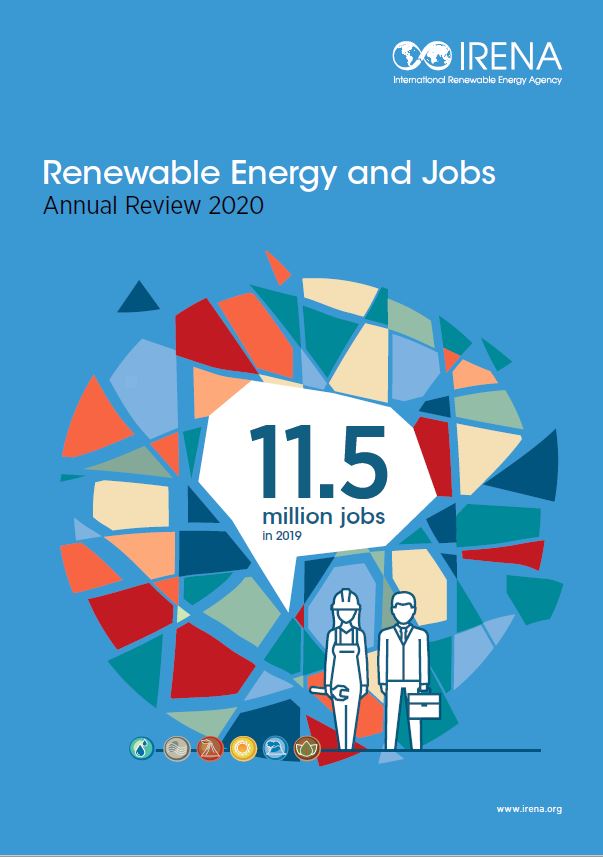
Despite the many benefits that lean manufacturing brings, companies often face difficulties in implementing this strategy. It is crucial that companies create a comprehensive plan to overcome any obstacles. Companies that have implemented Lean know that there are three key issues that hinder its success.
A commitment to lean manufacturing, regardless of how big a company might be, is vital to its success. While there is no hard and fast rule to determine how committed a company is to the implementation of lean, it is important that management acquaints staff with the changes in the corporate culture.
It is also crucial to ensure that resources get allocated correctly. Public organizations often find that they spend their budgets on unnecessary items. Managers have been reported to buy equipment they don't need in order to save money. This can lead to operational bottlenecks which can result in inefficient implementations of lean manufacturing.
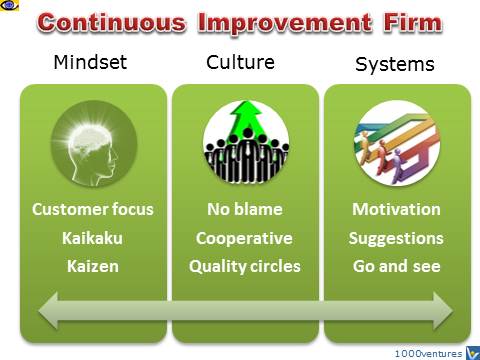
Reluctant cultural change is one major obstacle to lean manufacturing. Employees, especially those who have worked for the company for many years, aren’t used to change. Some employees will wait for the majority to speak up and convince them to move in a new direction. In order to break through this resistance, management must communicate the benefits of the program and explain why the change is necessary.
Another significant challenge is the lack of a strategic transformation plan. Even though companies may be able to transform many business operations at once; it is vital that they have a long term strategy. This strategy helps companies mentor future leaders, maintain competitiveness and improve operations. It helps identify operational bottlenecks and addresses growth opportunities.
It is vital to train workers to overcome resistance. Training is essential to help workers understand their roles and expectations. They also acquire multi-skills which allow them to work more independently. Workers also learn problem solving skills through training, which can help them maintain Lean through performance improvements.
Managers must be open with workers in order to overcome resistance. Managers may try to force workers to follow their instructions but they must also explain why it is necessary. In some instances, managers were found to have given incorrect instructions to their workers, which resulted in ineffective implementation.
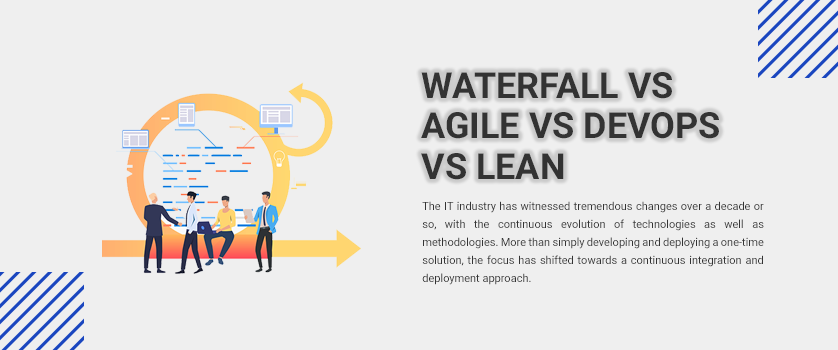
Managers, regardless of company size, must be present at the shop floor to help identify areas for improvement. Managers must also develop training modules and familiarize staff with new digital tools. These tools, such as 5S, improve visual management.
A clear vision is essential for lean manufacturing implementation. This vision should outline the responsibilities of employees and include a schedule to implement lean. It also includes a method for measuring success.
FAQ
What is the responsibility of a logistics manager?
A logistics manager ensures that all goods are delivered on time and without damage. This is done using his/her knowledge of the company's products. He/she should ensure that sufficient stock is available in order to meet customer demand.
What are manufacturing & logistics?
Manufacturing is the production of goods using raw materials. Logistics includes all aspects related to supply chain management, such as procurement, distribution planning, inventory control and transportation. Manufacturing and logistics are often considered together as a broader term that encompasses both the process of creating products and delivering them to customers.
What are the four types of manufacturing?
Manufacturing is the process of transforming raw materials into useful products using machines and processes. It can involve many activities like designing, manufacturing, testing packaging, shipping, selling and servicing.
Why is logistics so important in manufacturing?
Logistics are essential to any business. Logistics can help you achieve amazing results by helping to manage product flow from raw materials to finished products.
Logistics are also important in reducing costs and improving efficiency.
Do we need to know about Manufacturing Processes before learning about Logistics?
No. It doesn't matter if you don't know anything about manufacturing before you learn about logistics. Knowing about manufacturing processes will help you understand how logistics works.
What is the job of a manufacturer manager?
A manufacturing manager must ensure that all manufacturing processes are efficient and effective. They should be alert for any potential problems in the company and react accordingly.
They must also be able to communicate with sales and marketing departments.
They should also be knowledgeable about the latest trends in the industry so they can use this information for productivity and efficiency improvements.
Statistics
- [54][55] These are the top 50 countries by the total value of manufacturing output in US dollars for its noted year according to World Bank.[56] (en.wikipedia.org)
- It's estimated that 10.8% of the U.S. GDP in 2020 was contributed to manufacturing. (investopedia.com)
- You can multiply the result by 100 to get the total percent of monthly overhead. (investopedia.com)
- In 2021, an estimated 12.1 million Americans work in the manufacturing sector.6 (investopedia.com)
- According to a Statista study, U.S. businesses spent $1.63 trillion on logistics in 2019, moving goods from origin to end user through various supply chain network segments. (netsuite.com)
External Links
How To
Six Sigma and Manufacturing
Six Sigma is defined by "the application SPC (statistical process control) techniques to achieve continuous improvements." Motorola's Quality Improvement Department, Tokyo, Japan, developed it in 1986. Six Sigma's main goal is to improve process quality by standardizing processes and eliminating defects. Since there are no perfect products, or services, this approach has been adopted by many companies over the years. Six Sigma aims to reduce variation in the production's mean value. It is possible to measure the performance of your product against an average and find the percentage of time that it differs from the norm. If you notice a large deviation, then it is time to fix it.
Understanding how variability works in your company is the first step to Six Sigma. Once you have a good understanding of the basics, you can identify potential sources of variation. These variations can also be classified as random or systematic. Random variations happen when people make errors; systematic variations are caused externally. You could consider random variations if some widgets fall off the assembly lines. You might notice that your widgets always fall apart at the same place every time you put them together.
Once you've identified the problem areas you need to find solutions. It might mean changing the way you do business or redesigning it entirely. Test them again once you've implemented the changes. If they don't work you need to rework them and come up a better plan.