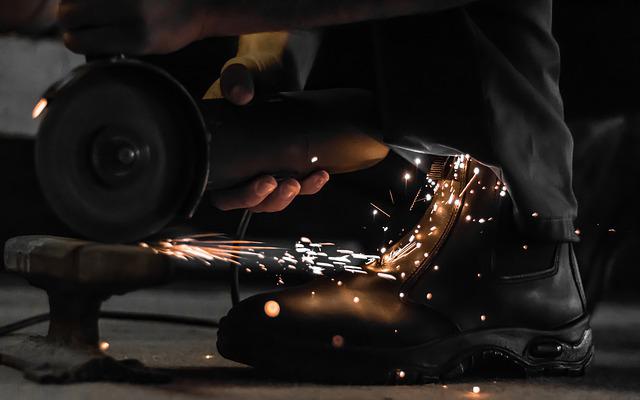
Manufacturing engineers were in high demand during the industrial revolution. They are responsible for designing manufacturing processes, which help to improve production efficiency. Manufacturing engineers have to be able to think commercially in addition to their technical skills. They must have a strong background in mathematics and science. Additionally, they must have leadership abilities.
A manufacturing engineer's salary will vary depending on his education, skills and experience. They can make between $70,960 to $126,000 annually in the United States. They can get a master’s degree to help them advance their careers. A master's degree can help them earn a better income. A master's degree will allow them to improve their skills and learn new technologies.
A PhD is also possible to make a contribution as a researcher. They can also work for the central and local government. They might also work as consultants. They may work in different areas of manufacturing.
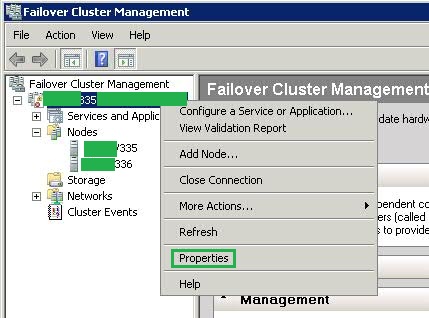
Manufacturing engineers generally earn more when they get more experience. They will become more experienced and can move up to managerial roles. In this role, they will be able to design manufacturing processes and implement automation. They will also be responsible for overseeing the day to day operations of the factory. They might also need to work weekends and nights.
Manufacturing engineers usually start as apprentices or interns. They can work in many areas of manufacturing such as aerospace engineering, food manufacturing and pharmaceutical manufacturing. They can also work in commercial or industrial design. After years of experience, they may be qualified to work as consultants. They will be able take over the factory floor and lead engineers. They will be responsible for ensuring the company follows best practices. They will also be expected to identify and resolve any errors in the manufacturing process.
Manufacturing engineers need to stay current with new manufacturing technologies and trends. They need to be able deal with any issues in a fast-paced setting and work under pressure. They also need to demonstrate leadership qualities and IT skills. They will receive a salary of a minimum wage during their first year in the industry. They can earn a slightly higher salary after they have been in the industry for a few years.
Manufacturing engineers usually earn salaries between $28,500-126,000 each year. This salary range includes bonuses and taxable wages. The state where the job is situated can affect the salary. Manufacturing Engineers can make as much at $34 an hr in some states.
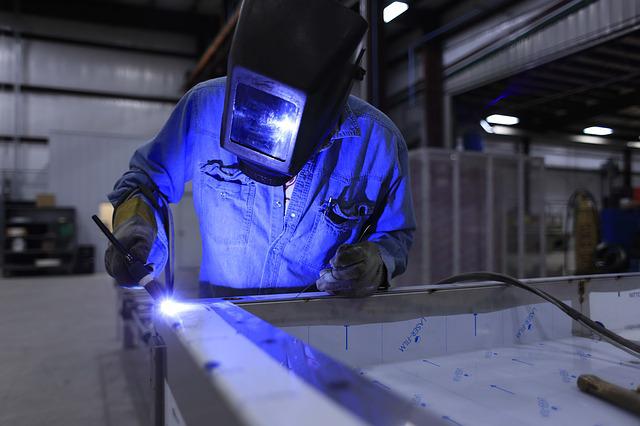
A manufacturing engineer may work in any of the many manufacturing industries such as paper manufacturing, aerospace manufacturing, and pharmaceutical manufacturing. They can work for large multinationals or smaller local companies. They can also work in central or local government.
They can also work in new industrial estates. General Motors (Boeing), Tesla and General Motors are among the most important American manufacturing firms. An engineer can also benefit from a graduate degree to learn more about the latest technologies.
FAQ
Why automate your warehouse
Modern warehouses are increasingly dependent on automation. Increased demand for efficient and faster delivery has resulted in a rise in e-commerce.
Warehouses should be able adapt quickly to new needs. They must invest heavily in technology to do this. Automation warehouses can bring many benefits. These are some of the benefits that automation can bring to warehouses:
-
Increases throughput/productivity
-
Reduces errors
-
Increases accuracy
-
Boosts safety
-
Eliminates bottlenecks
-
Allows companies scale more easily
-
This makes workers more productive
-
It gives visibility to everything that happens inside the warehouse
-
Enhances customer experience
-
Improves employee satisfaction
-
This reduces downtime while increasing uptime
-
Ensures quality products are delivered on time
-
Human error can be eliminated
-
It helps ensure compliance with regulations
What can I do to learn more about manufacturing?
Practical experience is the best way of learning about manufacturing. You can read books, or watch instructional videos if you don't have the opportunity to do so.
What type of jobs is there in logistics
There are many kinds of jobs available within logistics. Some examples are:
-
Warehouse workers - They load and unload trucks and pallets.
-
Transportation drivers – They drive trucks or trailers to transport goods and perform pick-ups.
-
Freight handlers are people who sort and pack freight into warehouses.
-
Inventory managers – These people oversee inventory at warehouses.
-
Sales reps - They sell products and services to customers.
-
Logistics coordinators - They plan and organize logistics operations.
-
Purchasing agents – They buy goods or services necessary to run a company.
-
Customer service representatives – They answer emails and phone calls from customers.
-
Shippers clerks - They process shipping order and issue bills.
-
Order fillers: They fill orders based off what has been ordered and shipped.
-
Quality control inspectors (QCI) - They inspect all incoming and departing products for potential defects.
-
Others - There is a variety of other jobs in logistics. These include transportation supervisors and cargo specialists.
How can we reduce manufacturing overproduction?
Better inventory management is key to reducing excess production. This would reduce the time needed to manage inventory. This will allow us to free up resources for more productive tasks.
You can do this by adopting a Kanban method. A Kanban Board is a visual display that tracks work progress. In a Kanban system, work items move through a sequence of states until they reach their final destination. Each state is assigned a different priority.
As an example, if work is progressing from one stage of the process to another, then the current task is complete and can be transferred to the next. If a task is still in its beginning stages, it will continue to be so until it reaches the end.
This allows you to keep work moving along while making sure that no work gets neglected. Managers can monitor the work being done by Kanban boards to see what is happening at any given time. This information allows managers to adjust their workflow based off real-time data.
Lean manufacturing, another method to control inventory levels, is also an option. Lean manufacturing focuses on eliminating waste throughout the entire production chain. Anything that doesn't add value to the product is considered waste. Here are some examples of common types.
-
Overproduction
-
Inventory
-
Unnecessary packaging
-
Material surplus
Manufacturers can reduce their costs and improve their efficiency by using these ideas.
Statistics
- Job #1 is delivering the ordered product according to specifications: color, size, brand, and quantity. (netsuite.com)
- According to the United Nations Industrial Development Organization (UNIDO), China is the top manufacturer worldwide by 2019 output, producing 28.7% of the total global manufacturing output, followed by the United States, Japan, Germany, and India.[52][53] (en.wikipedia.org)
- [54][55] These are the top 50 countries by the total value of manufacturing output in US dollars for its noted year according to World Bank.[56] (en.wikipedia.org)
- In 2021, an estimated 12.1 million Americans work in the manufacturing sector.6 (investopedia.com)
- According to a Statista study, U.S. businesses spent $1.63 trillion on logistics in 2019, moving goods from origin to end user through various supply chain network segments. (netsuite.com)
External Links
How To
How to Use lean manufacturing in the Production of Goods
Lean manufacturing is an approach to management that aims for efficiency and waste reduction. It was first developed in Japan in the 1970s/80s by Taiichi Ahno, who was awarded the Toyota Production System (TPS), award from KanjiToyoda, the founder of TPS. Michael L. Watkins published the first book on lean manufacturing in 1990.
Lean manufacturing can be described as a set or principles that are used to improve quality, speed and cost of products or services. It emphasizes the elimination and minimization of waste in the value stream. Lean manufacturing is also known as just in time (JIT), zero defect total productive maintenance(TPM), and five-star (S). Lean manufacturing seeks to eliminate non-value added activities, such as inspection, work, waiting, and rework.
Lean manufacturing is a way for companies to achieve their goals faster, improve product quality, and lower costs. Lean Manufacturing is one of the most efficient ways to manage the entire value chains, including suppliers and customers as well distributors and retailers. Lean manufacturing can be found in many industries. For example, Toyota's philosophy underpins its success in automobiles, electronics, appliances, healthcare, chemical engineering, aerospace, paper, food, etc.
Five basic principles of Lean Manufacturing are included in lean manufacturing
-
Define Value - Identify the value your business adds to society and what makes you different from competitors.
-
Reduce waste - Get rid of any activity that does not add value to the supply chain.
-
Create Flow – Ensure that work flows smoothly throughout the process.
-
Standardize and simplify – Make processes as repeatable and consistent as possible.
-
Building Relationships – Establish personal relationships with both external and internal stakeholders.
Although lean manufacturing isn't a new concept in business, it has gained popularity due to renewed interest in the economy after the 2008 global financial crisis. Many businesses are now using lean manufacturing to improve their competitiveness. Many economists believe lean manufacturing will play a major role in economic recovery.
Lean manufacturing is now becoming a common practice in the automotive industry, with many benefits. These include higher customer satisfaction levels, reduced inventory levels as well as lower operating costs.
The principles of lean manufacturing can be applied in almost any area of an organization. This is because it ensures efficiency and effectiveness in all stages of the value chain.
There are three types principally of lean manufacturing:
-
Just-in Time Manufacturing, (JIT): This kind of lean manufacturing is also commonly known as "pull-systems." JIT refers to a system in which components are assembled at the point of use instead of being produced ahead of time. This method reduces lead times, increases availability, and decreases inventory.
-
Zero Defects Manufacturing (ZDM): ZDM focuses on ensuring that no defective units leave the manufacturing facility. You should repair any part that needs to be repaired during an assembly line. This is true even for finished products that only require minor repairs prior to shipping.
-
Continuous Improvement (CI),: Continuous improvement aims improve the efficiency and effectiveness of operations by continuously identifying issues and making changes to reduce waste. Continuous Improvement (CI) involves continuous improvement in processes, people, tools, and infrastructure.