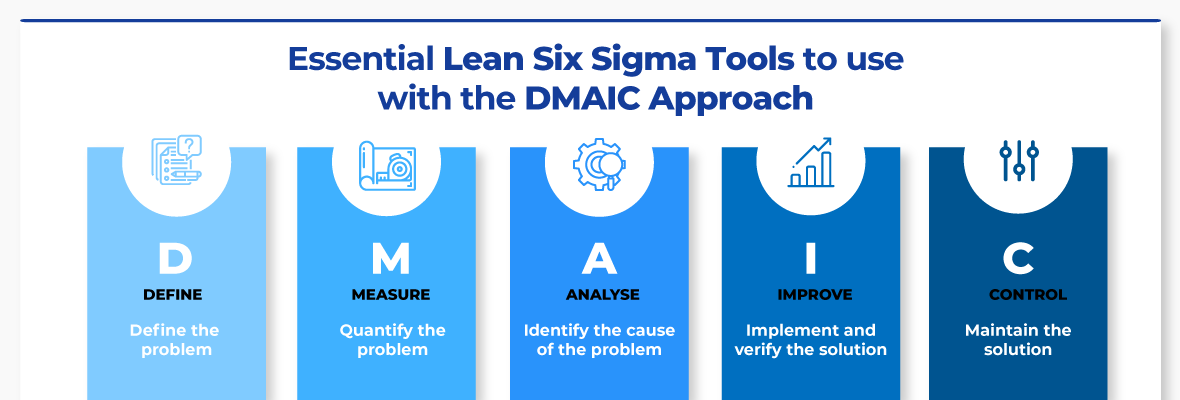
The MIT Supply Chain Management course is one of most highly regarded in all of the world. Its enrollment ranks second to Michigan State's MS SCM. The program is open to students from all walks of life. Many have post-graduate degrees. The Supply Chain Class currently has a wide range of students. It is possible to calculate the acceptance rates by dividing admissions numbers by newly-awarded MM credentials.
The Supply Chain Management Program at MIT
The Supply Chain Management Program at MIT is an interdisciplinary degree program that brings together business professionals from all walks of the globe. The program offers master's level coursework and industry interaction. It also provides professional development. The school's website has more information.
Online courses
A course in online supply chain management can be beneficial for both new and experienced managers. These courses can not only enhance your career but can also help you build a sense community. Allegue was able expand her network by taking these courses and has met people all over the globe. Allegue learned more about supply chains, and how they affect decisions.
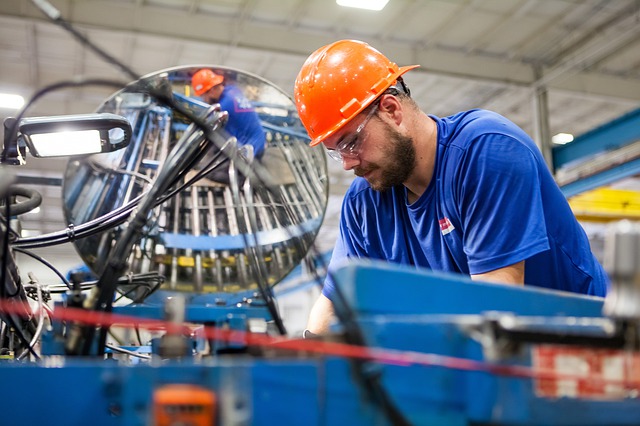
On-campus program
The MIT Supply Chain On-Campus Program is for students interested in a career in logistics. The curriculum is focused on analytical problem-solving and leadership skills. The curriculum includes courses in finance, database analysis, logistics, and finance. The program also includes a project in graduate research that requires students to collaborate with a partner company.
SCALE Centers
The MIT Center for Transportation & Logistics' (SCALE), is a leading center in supply chain management. The Center has nearly 50 years of experience in the field. It has also helped many companies to gain competitive advantage by its cutting-edge research.
Scholarships
The MIT SCALE LA Scholarship is a merit based full tuition scholarship that will allow students at MIT to receive the award while they are pursuing their education. This scholarship will allow students to be elected class president and participate on the MIT GCLOG team. It also allows them to participate in the academic activities. Financial need is required to be eligible for this award. Deadline for applications: November 15, 2020
Fellowships
Apply for a Fellowship in MIT Supply Chain Management if supply chain management is something you want to pursue. This program honors exceptional students who have experience in supply chain management. The fellowships are fully-funded and provide full tuition for the successful applicants. Applicants must have two years of relevant work experience and show leadership potential. AWESOME helps MIT SCM identify the most promising students.
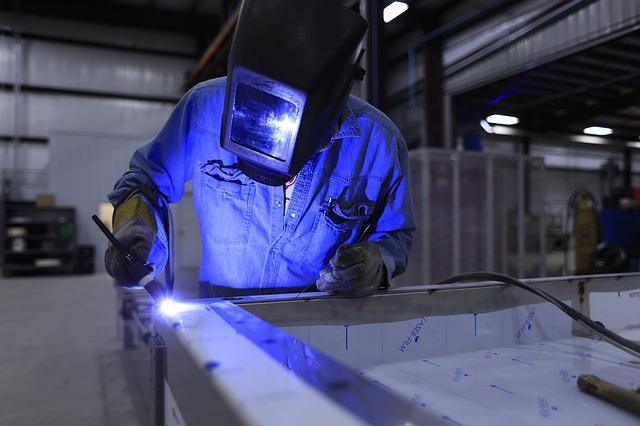
SCALE Connect conference at MIT
SCALE Connect was organized by MIT in collaboration to the Space Center Market Conference. It brought together high-ranking government officials, academics, commercial industry representatives, and others in order to discuss policy, and keep abreast of developments in commercial orbit missions. The conference's main benefit was collaboration, as students had to participate virtually.
FAQ
What are the responsibilities for a manufacturing manager
A manufacturing manager must make sure that all manufacturing processes run smoothly and effectively. They should be alert for any potential problems in the company and react accordingly.
They should also know how to communicate with other departments such as sales and marketing.
They should also be aware of the latest trends in their industry and be able to use this information to help improve productivity and efficiency.
How can we improve manufacturing efficiency?
First, identify the factors that affect production time. Then we need to find ways to improve these factors. If you don’t know how to start, look at which factors have the greatest impact upon production time. Once you've identified them, try to find solutions for each of those factors.
What does manufacturing mean?
Manufacturing Industries refers to businesses that manufacture products. Consumers are people who purchase these goods. To accomplish this goal, these companies employ a range of processes including distribution, sales, management, and production. These companies produce goods using raw materials and other equipment. This includes all types and varieties of manufactured goods, such as food items, clothings, building supplies, furnitures, toys, electronics tools, machinery vehicles, pharmaceuticals medical devices, chemicals, among others.
What are the 7 R's of logistics?
The acronym 7R's of Logistic is an acronym that stands for seven fundamental principles of logistics management. It was developed and published by the International Association of Business Logisticians in 2004 as part of the "Seven Principles of Logistics Management".
The following letters form the acronym:
-
Responsible – ensure that all actions are legal and don't cause harm to anyone else.
-
Reliable - You can have confidence that you will fulfill your promises.
-
Reasonable - make sure you use your resources well and don't waste them.
-
Realistic - Take into consideration all aspects of operations including cost-effectiveness, environmental impact, and other factors.
-
Respectful: Treat others with fairness and equity
-
Resourceful - look for opportunities to save money and increase productivity.
-
Recognizable: Provide customers with value-added service
What are the four types of manufacturing?
Manufacturing is the process that transforms raw materials into useful products. It can involve many activities like designing, manufacturing, testing packaging, shipping, selling and servicing.
Why is logistics important in manufacturing
Logistics are an integral part any business. Logistics can help you achieve amazing results by helping to manage product flow from raw materials to finished products.
Logistics play an important role in reducing costs as well as increasing efficiency.
How can manufacturing excess production be decreased?
It is essential to find better ways to manage inventory to reduce overproduction. This would reduce the time spent on unproductive activities like purchasing, storing and maintaining excess stock. This will allow us to free up resources for more productive tasks.
This can be done by using a Kanban system. A Kanban board, a visual display to show the progress of work, is called a Kanban board. Kanban systems allow work items to move through different states until they reach their final destination. Each state is assigned a different priority.
If work is moving from one stage to the other, then the current task can be completed and moved on to the next. A task that is still in the initial stages of a process will be considered complete until it moves on to the next stage.
This allows for work to continue moving forward, while also ensuring that there is no work left behind. Managers can view the Kanban board to see how much work they have done. This allows them the ability to adjust their workflow using real-time data.
Another way to control inventory levels is to implement lean manufacturing. Lean manufacturing focuses on eliminating waste throughout the entire production chain. Any product that isn't adding value can be considered waste. Some common types of waste include:
-
Overproduction
-
Inventory
-
Unnecessary packaging
-
Materials in excess
Manufacturers can reduce their costs and improve their efficiency by using these ideas.
Statistics
- In the United States, for example, manufacturing makes up 15% of the economic output. (twi-global.com)
- It's estimated that 10.8% of the U.S. GDP in 2020 was contributed to manufacturing. (investopedia.com)
- (2:04) MTO is a production technique wherein products are customized according to customer specifications, and production only starts after an order is received. (oracle.com)
- Job #1 is delivering the ordered product according to specifications: color, size, brand, and quantity. (netsuite.com)
- Many factories witnessed a 30% increase in output due to the shift to electric motors. (en.wikipedia.org)
External Links
How To
How to use 5S in Manufacturing to Increase Productivity
5S stands in for "Sort", the "Set In Order", "Standardize", or "Separate". Toyota Motor Corporation was the first to develop the 5S approach in 1954. It helps companies achieve higher levels of efficiency by improving their work environment.
This method has the basic goal of standardizing production processes to make them repeatable. This means that tasks such as cleaning, sorting, storing, packing, and labeling are performed daily. Workers can be more productive by knowing what to expect.
Five steps are required to implement 5S: Sort, Set In Order, Standardize. Separate. Each step requires a different action, which increases efficiency. You can make it easy for people to find things later by sorting them. When items are ordered, they are put together. You then organize your inventory in groups. Finally, label all containers correctly.
Employees need to reflect on how they do their jobs. Employees must understand why they do certain tasks and decide if there's another way to accomplish them without relying on the old ways of doing things. They must learn new skills and techniques in order to implement the 5S system.
In addition to improving efficiency, the 5S system also increases morale and teamwork among employees. As they begin to see improvements, they feel motivated to continue working towards the goal of achieving higher levels of efficiency.