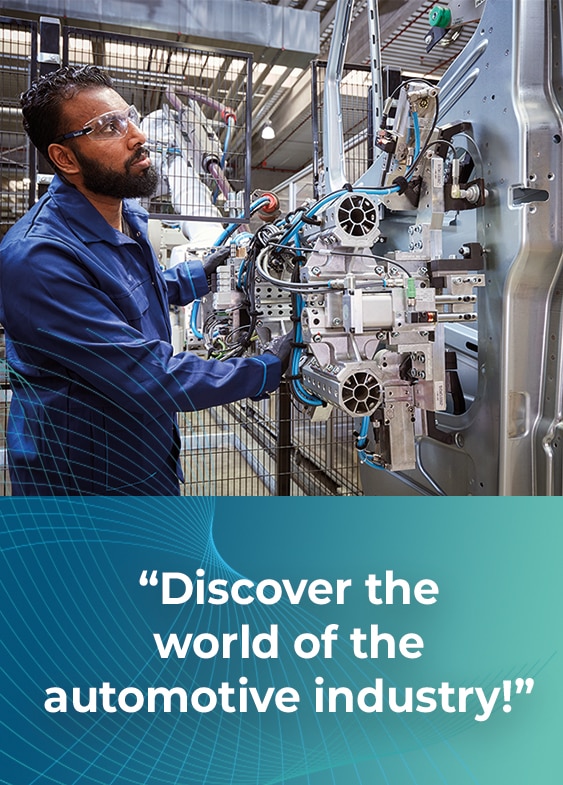
Purchasing Managers, also called Materials Managers, are responsible in sourcing and coordinating all purchases. They are responsible for coordinating all purchasing activities with suppliers and vendors. They need to be familiar with the company's buying process and how they can improve it. They must also be able and willing to negotiate the best deals possible for the company.
Purchasing managers also have to maintain accurate and up-to-date purchasing records. They assess customer needs, analyze financial statements, evaluate vendors' capabilities, and evaluate price trends. They also coordinate purchasing activities with other departments. If the company requires supplies from foreign markets, they may have to work overtime.
As well as managing inventory and logistics, purchasing managers coordinate and manage them. They make decisions about the best way to purchase products and ensure they meet company quality standards. They work closely with their staff to make sure that they are able to manage their budgets. They negotiate deals and find the best vendors.
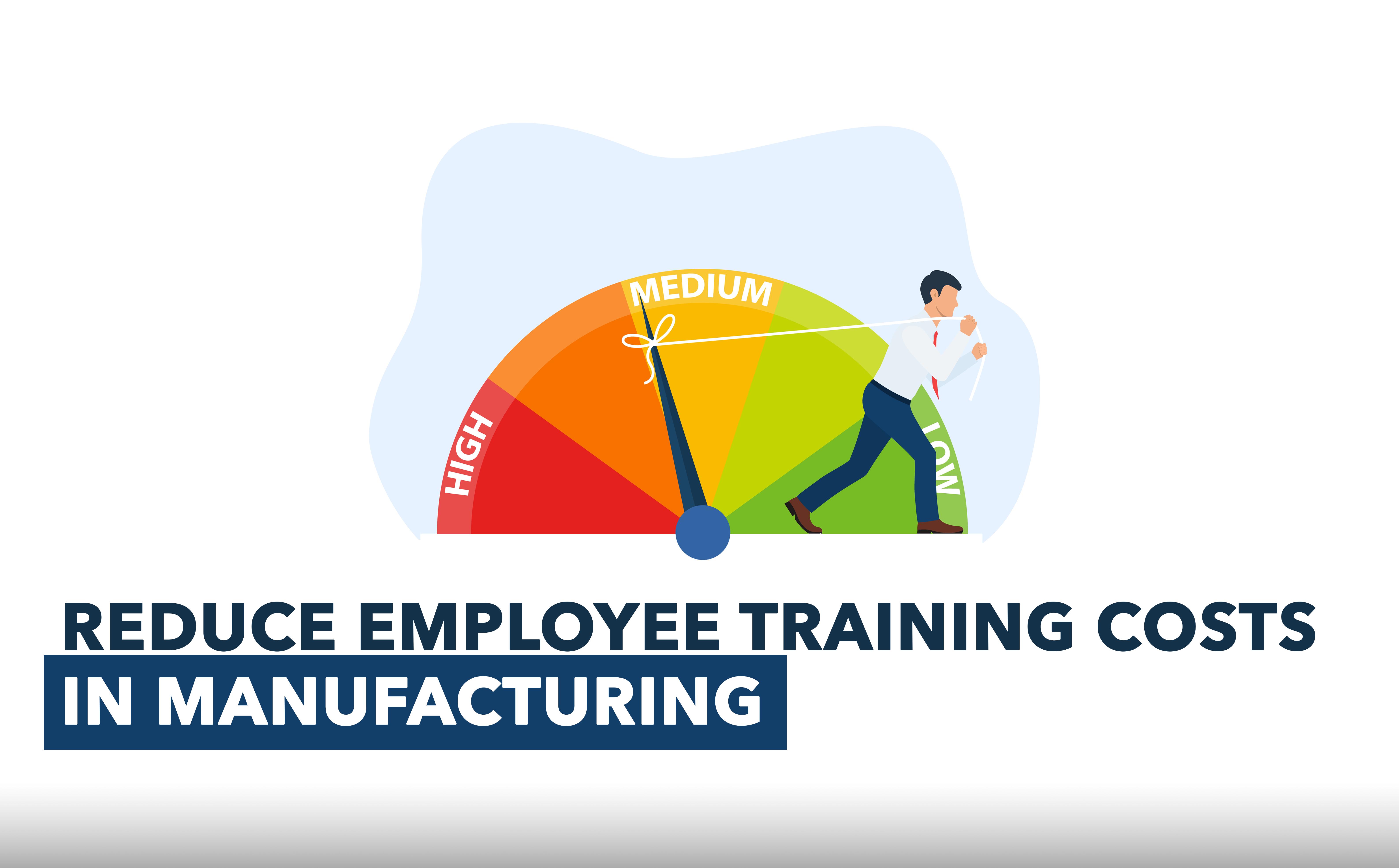
All purchasing employees are monitored and managed by Purchasing Managers. They evaluate the quality, speed, and cost of all purchased goods. They also contact sellers and suppliers and visit their distribution centers. They also make sure that suppliers comply with the terms of the contract. They may also have responsibility for team building and disciplinary issues.
Purchasing Managers must have excellent communication skills, analytical abilities, and strategic thinking skills. They need to be able analyse the effects of various products on the company. They should also have the knowledge to manage suppliers and their relations. They should also have the ability to make business decisions and to increase sales. They should also be able handle complex purchases. They should be able evaluate potential vendors and analyze their capabilities to find the right vendor for the company.
Most purchasing managers have to have a bachelor's degree in business or a related field. Experience in supply chain and inventory management is also an asset. They should also be familiar with Microsoft Office and other software programs.
The best purchasing managers should be able find the best deals and negotiate favorable contracts. They should also be able to coordinate all purchasing activities, manage inventories, and keep track of vendor and supplier performance. They should also have the ability to manage a team of purchasing agents.
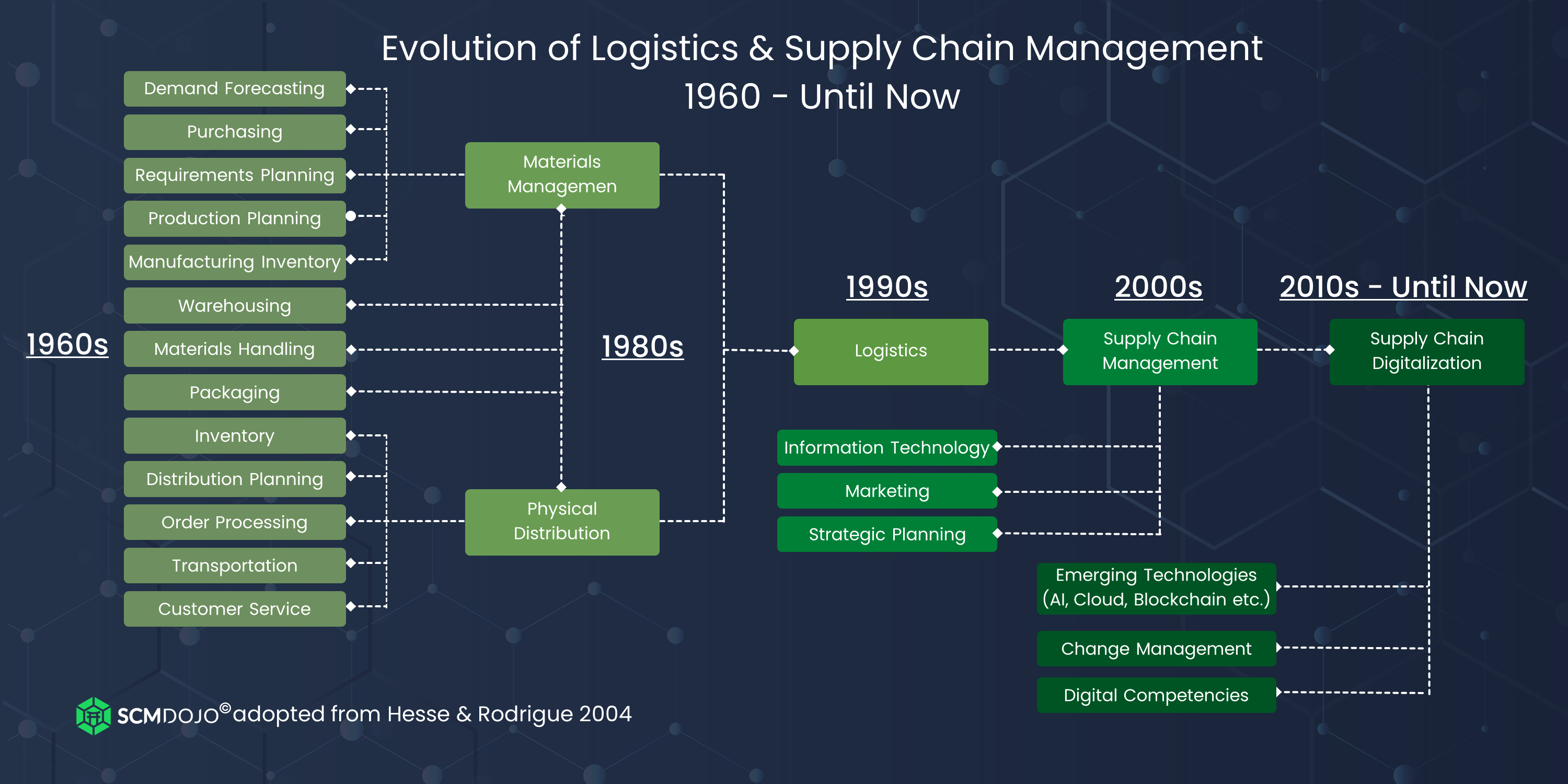
The job description of a purchasing manager should mention the importance of purchasing to the company. It should mention how important it's for the company to stay ahead. It should mention how employees are valued by the company. It should also contain a call-to-action to encourage applicants.
If the company has to buy materials or equipment for international markets, Purchasing Managers might work overtime. They may have to deal directly with vendors and buyers and attend trade fairs.
FAQ
What is the difference between Production Planning, Scheduling and Production Planning?
Production Planning (PP) is the process of determining what needs to be produced at any given point in time. This is accomplished by forecasting the demand and identifying production resources.
Scheduling is the process that assigns dates to tasks so they can get completed within a given timeframe.
Is there anything we should know about Manufacturing Processes prior to learning about Logistics.
No. You don't have to know about manufacturing processes before learning about logistics. Knowing about manufacturing processes will help you understand how logistics works.
What are the 7 Rs of logistics?
The acronym 7R's of Logistic is an acronym that stands for seven fundamental principles of logistics management. It was developed by International Association of Business Logisticians (IABL), and published as part of their "Seven Principles of Logistics Management Series" in 2004.
The acronym is composed of the following letters.
-
Responsible – ensure that all actions are legal and don't cause harm to anyone else.
-
Reliable – have faith in your ability and capability to keep promises.
-
Use resources effectively and sparingly.
-
Realistic - Take into consideration all aspects of operations including cost-effectiveness, environmental impact, and other factors.
-
Respectful - show respect and treat others fairly and fairly
-
Be resourceful: Look for opportunities to save money or increase productivity.
-
Recognizable - provide customers with value-added services.
How can manufacturing reduce production bottlenecks?
To avoid production bottlenecks, ensure that all processes run smoothly from the moment you receive your order to the time the product ships.
This includes planning to meet capacity requirements and quality control.
Continuous improvement techniques such Six Sigma are the best method to accomplish this.
Six Sigma is a management system used to improve quality and reduce waste in every aspect of your organization.
It's all about eliminating variation and creating consistency in work.
Why is logistics important in manufacturing
Logistics are an essential part of any business. They are essential to any business's success.
Logistics also play a major role in reducing costs and increasing efficiency.
Statistics
- In the United States, for example, manufacturing makes up 15% of the economic output. (twi-global.com)
- Many factories witnessed a 30% increase in output due to the shift to electric motors. (en.wikipedia.org)
- Job #1 is delivering the ordered product according to specifications: color, size, brand, and quantity. (netsuite.com)
- You can multiply the result by 100 to get the total percent of monthly overhead. (investopedia.com)
- In 2021, an estimated 12.1 million Americans work in the manufacturing sector.6 (investopedia.com)
External Links
How To
How to Use 5S for Increasing Productivity in Manufacturing
5S stands as "Sort", Set In Order", Standardize", Separate" and "Store". The 5S methodology was developed at Toyota Motor Corporation in 1954. It helps companies achieve higher levels of efficiency by improving their work environment.
The idea behind standardizing production processes is to make them repeatable and measurable. This means that tasks such as cleaning, sorting, storing, packing, and labeling are performed daily. These actions allow workers to perform their job more efficiently, knowing what to expect.
Five steps are required to implement 5S: Sort, Set In Order, Standardize. Separate. Each step has a different action and leads to higher efficiency. Sorting things makes it easier to find them later. When you arrange items, you place them together. Once you have separated your inventory into groups and organized them, you will store these groups in easily accessible containers. Finally, label all containers correctly.
Employees will need to be more critical about their work. Employees must understand why they do certain tasks and decide if there's another way to accomplish them without relying on the old ways of doing things. To be successful in the 5S system, employees will need to acquire new skills and techniques.
The 5S Method not only improves efficiency, but it also helps employees to be more productive and happier. As they begin to see improvements, they feel motivated to continue working towards the goal of achieving higher levels of efficiency.