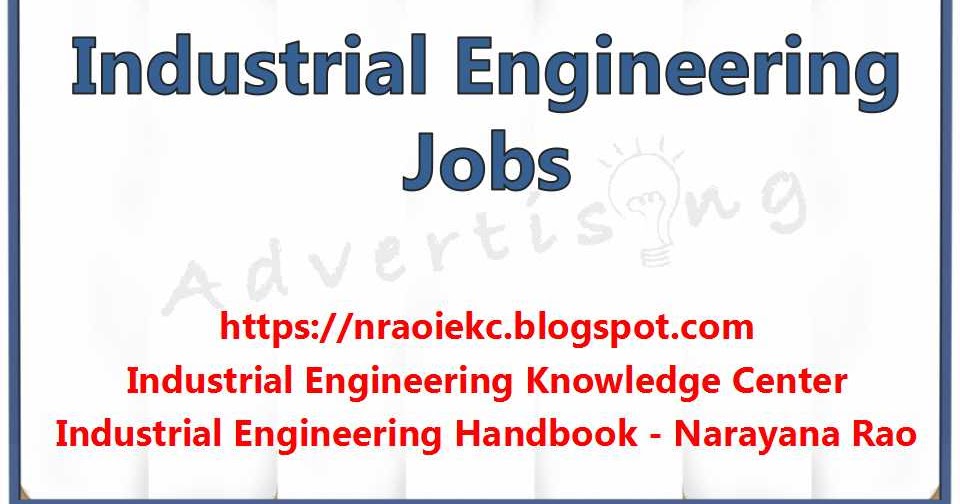
Apparel manufacturers today face a unique challenge in meeting the diverse demands of their customers. These consumers vary in terms of physiographics, socioeconomics, and demographics, and their preferences are not easily predictible. In addition, consumers have greater awareness of products and are able to find information easily. At the same time, they are becoming more inclined to buy expensive, high-fashion items.
Production efficiency
A key component of the overall strategy for apparel producers is to increase production efficiency. Because the apparel industry is dependent on human labor and changing fashion trends it is critical to ensure that production planning is in place. Apparel manufacturers have to ensure that they are able adapt to changing global needs and can meet short product development cycles. Apparel manufacturers must evaluate their existing products and adopt digital technologies to reduce product development cycles from months to days. The planning process should include critical path analysis.
Even though the apparel industry is labor-intensive it is possible to improve efficiency. This goal can be achieved with the right tools and management. An increase of efficiency by 10 to 15% can result in a 35% increase in EBITDA. In addition, an increase in efficiency can increase wages for workers and enhance the country's competitiveness in the global marketplace.
Fabric layering
Fabric layering, a technique used for apparel manufacturing, is one example. This involves placing a pattern over a laid fabric. The pattern can be made manually or with a plotter. The pattern components are laid in markers. They are then cut with a straight knife, or another cutting method.
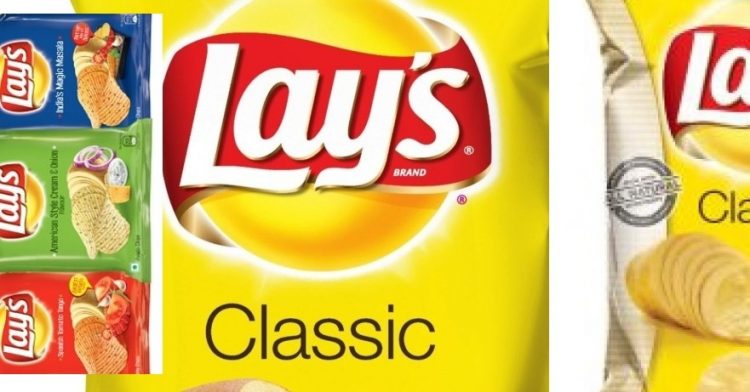
During this process, the fabric is spread evenly. The fabric can be laid in a pile, or in layers with the cutting marker. The maximum cutting width is the fabric width that is usable, minus any selvedges or needle marks. The fabric utilization refers to the amount of fabric used. The layouts can be either half-garment or whole-garment. Half-garment Lay involves placing fabric on only one side of a garment piece. Whole-garment Lay involves covering fabric on both sides. However, whole-garment lay consumes more fabric.
Cutting
A cutting is the use of cutting blades to cut specific pieces of fabric into smaller pieces. Fabric typically accounts for 60% to 70% of the cost of a garment. Therefore, it is important that every inch is used. Apparel manufacturing should have a strict control system to ensure that every inch is used.
Spreading the fabric across a large table is one of the steps in cutting fabric. In mass production, there are usually several layers used to spread the fabric. Based on the number of garments that will be produced and the thickness of fabric, the cutting master determines the appropriate layer count. After the fabric has been spread, it's measured to determine its maximum cutting width.
Pressing
The process of pressing is crucial in the production of apparel. It controls the appearance of garments and helps them to maintain their comfort. It's done in a factory. It can be manually or automated. Software can be used for controlling the automation level. A press can also be programmed to follow specific instructions. Automation of pressing in an apparel manufacturing factory can reduce the possibility of human error. The process will need to be more accurate in controlling temperature and pressure due to increasing numbers of fabric types and fibers.
To soften the fibers of a garment, heat is used to press it. The softened fibers stabilize the shape of the garment. To prevent damaging the yarn or fibres, choose the appropriate temperature.
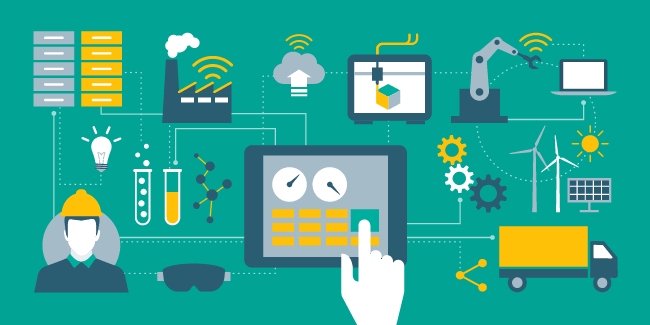
Minimum order quantity
When looking for clothing manufacturers, be sure to check the Minimum Order Quantity or MOQ of the factory. This minimum order quantity is required by many garment factories. The MOQ is dependent on the technical characteristics of your designs and varies from one factory to another. Some factories can only accept orders for a handful of hundred items, while other factories require orders for thousands.
Manufacturers who deal with bulk goods, such as manufacturers, must meet the MOQ requirement. This quantity is essential for manufacturers to be profitable. It helps them keep their costs down and keeps out small businesses that are not looking to place large orders. This is particularly important for custom orders.
FAQ
What are the 7 Rs of logistics.
The acronym 7R's for Logistics stands to represent the seven basic principles in logistics management. It was published in 2004 by the International Association of Business Logisticians as part of their "Seven Principles of Logistics Management" series.
The following letters form the acronym:
-
Responsible – ensure that all actions are legal and don't cause harm to anyone else.
-
Reliable: Have faith in your ability or the ability to honor any promises made.
-
Be responsible - Use resources efficiently and avoid wasting them.
-
Realistic – consider all aspects of operations, from cost-effectiveness to environmental impact.
-
Respectful: Treat others with fairness and equity
-
Be resourceful: Look for opportunities to save money or increase productivity.
-
Recognizable: Provide customers with value-added service
What are my options for learning more about manufacturing
The best way to learn about manufacturing is through hands-on experience. But if that is not possible you can always read books and watch educational videos.
What are the jobs in logistics?
There are many jobs available in logistics. Here are some examples:
-
Warehouse workers – They load and unload pallets and trucks.
-
Transport drivers - These are people who drive trucks and trailers to transport goods or perform pick-ups.
-
Freight handlers – They sort and package freight at warehouses.
-
Inventory managers - These are responsible for overseeing the stock of goods in warehouses.
-
Sales reps are people who sell products to customers.
-
Logistics coordinators - They plan and organize logistics operations.
-
Purchasing agents are those who purchase goods and services for the company.
-
Customer service representatives - They answer calls and emails from customers.
-
Shipping clerks: They process shipping requests and issue bills.
-
Order fillers are people who fill orders based only on what was ordered.
-
Quality control inspectors: They inspect outgoing and incoming products for any defects.
-
Others – There are many other types available in logistics. They include transport supervisors, cargo specialists and others.
Statistics
- [54][55] These are the top 50 countries by the total value of manufacturing output in US dollars for its noted year according to World Bank.[56] (en.wikipedia.org)
- In the United States, for example, manufacturing makes up 15% of the economic output. (twi-global.com)
- According to the United Nations Industrial Development Organization (UNIDO), China is the top manufacturer worldwide by 2019 output, producing 28.7% of the total global manufacturing output, followed by the United States, Japan, Germany, and India.[52][53] (en.wikipedia.org)
- In 2021, an estimated 12.1 million Americans work in the manufacturing sector.6 (investopedia.com)
- (2:04) MTO is a production technique wherein products are customized according to customer specifications, and production only starts after an order is received. (oracle.com)
External Links
How To
How to Use lean manufacturing in the Production of Goods
Lean manufacturing refers to a method of managing that seeks to improve efficiency and decrease waste. It was developed in Japan during the 1970s and 1980s by Taiichi Ohno, who received the Toyota Production System (TPS) award from TPS founder Kanji Toyoda. Michael L. Watkins published the book "The Machine That Changed the World", which was the first to be published about lean manufacturing.
Lean manufacturing, often described as a set and practice of principles, is aimed at improving the quality, speed, cost, and efficiency of products, services, and other activities. It emphasizes the elimination and minimization of waste in the value stream. Lean manufacturing is also known as just in time (JIT), zero defect total productive maintenance(TPM), and five-star (S). Lean manufacturing focuses on eliminating non-value-added activities such as rework, inspection, and waiting.
Lean manufacturing can help companies improve their product quality and reduce costs. Additionally, it helps them achieve their goals more quickly and reduces employee turnover. Lean manufacturing is considered one of the most effective ways to manage the entire value chain, including suppliers, customers, distributors, retailers, and employees. Lean manufacturing is widely used in many industries. Toyota's philosophy is the foundation of its success in automotives, electronics and appliances, healthcare, chemical engineers, aerospace, paper and food, among other industries.
Lean manufacturing includes five basic principles:
-
Define Value- Identify the added value your company brings to society. What makes you stand out from your competitors?
-
Reduce waste - Get rid of any activity that does not add value to the supply chain.
-
Create Flow - Ensure work moves smoothly through the process without interruption.
-
Standardize and simplify - Make your processes as consistent as possible.
-
Build Relationships- Develop personal relationships with both internal as well as external stakeholders.
Lean manufacturing isn’t new, but it has seen a renewed interest since 2008 due to the global financial crisis. Many businesses have adopted lean manufacturing techniques to help them become more competitive. Some economists even believe that lean manufacturing can be a key factor in economic recovery.
Lean manufacturing is becoming a popular practice in automotive. It has many advantages. These include better customer satisfaction and lower inventory levels. They also result in lower operating costs.
It can be applied to any aspect of an organisation. This is because it ensures efficiency and effectiveness in all stages of the value chain.
There are three types principally of lean manufacturing:
-
Just-in Time Manufacturing (JIT), also known as "pull system": This form of lean manufacturing is often referred to simply as "pull". JIT is a process in which components can be assembled at the point they are needed, instead of being made ahead of time. This method reduces lead times, increases availability, and decreases inventory.
-
Zero Defects Manufacturing (ZDM),: ZDM is a system that ensures no defective units are left the manufacturing facility. If a part is required to be repaired on the assembly line, it should not be scrapped. This applies to finished products, which may need minor repairs before they are shipped.
-
Continuous Improvement (CI),: Continuous improvement aims improve the efficiency and effectiveness of operations by continuously identifying issues and making changes to reduce waste. Continuous improvement refers to continuous improvement of processes as well people and tools.