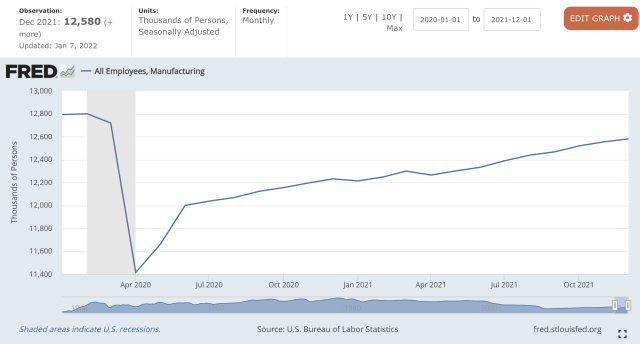
Durable goods are items which do not easily wear out and yield utility over a long period of time. These products are more durable than nondurable goods which can only be used once. These products are durable, meaning they can continue to offer the same or more utility for many years. A car that's durable will serve you for many years.
Nondurable goods can be consumed immediately
In contrast to durable goods, which have a long lifespan, nondurable goods are consumed immediately. In a recession, consumers tend to avoid spending money on durable goods but continue to purchase nondurable goods. These items have lower prices and can be paid with cash. Nondurable goods include meats, fruits, vegetables and dairy products. Other examples of nondurable goods include detergent, dishwash soap, and cosmetics.
In general, nondurable goods are the least expensive types of goods, lasting less than three years. They can also be bought frequently, meaning consumers can purchase them regularly without worrying about their future price. Nondurable goods such as laundry detergent and packaged food are disposable. However, service goods are tangible and are made to meet consumer demands. How consumers perceive a product can affect how they plan to purchase it. Prices may also play a role.
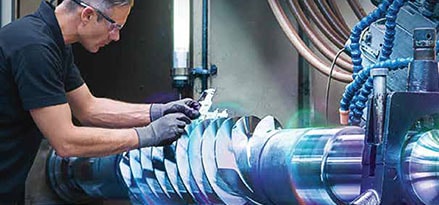
Durable goods are, in contrast, products that are expected provide a steady flow of utility over a time period. These products are often called consumer durables. They include automobiles, household furniture, sporting items, and jewelry. Durables are most commonly purchased during periods when economic growth is occurring, while nondurables will be purchased during economic recession.
Durable goods can last for more than a year
Durable goods can be defined as tangible commodities that are durable and last at least one (1) year under normal use. There are two types: producer durables and consumer durables. Consumer durables refer to household goods such as furniture, boats, cars, and other motor vehicles. Producer durables includes machinery, equipment, fine jewelry, and appliances.
Durable goods are expected last for at least 3 years but may require repair or servicing. Durable goods are designed to be durable and last for many years. You can extend the life expectancy of durable goods up to 20-years with proper maintenance and care.
In times of economic growth, durable goods demand is often a key indicator. In order to increase employment and improve investment returns, durable goods should be sold more often. However, a drop in durable goods sales may indicate a decrease of economic activity. This is because consumers use their money to repair and service existing products rather than spending it on new items. As a result, a slowdown in durable goods may lead to a recession.

Impact of the COVID-19 pandemic sur durable goods
COVID-19, which was a pandemic that brought about widespread illness, has had a significant impact on consumer spending. The disease caused people to withdraw from the outdoors and stop going to the gym, or even attending social events. Also, they stopped hailing cabs which resulted to decreased consumer spending. Instead, people spent more time at home doing house production and leisure activities. This reduced consumer spending on services and restaurants.
The US economy has seen a dramatic impact from the COVID-19 pandemic. In addition to the increase in durable goods, strong fiscal policies were implemented by the government that led to an increase in household disposable income. This effect may have been responsible for half of 2020's rise in durable goods consumption.
The COVID-19 outbreak has affected individuals and communities as well businesses. While attention has been focused on the effect on fast-moving items, less has been done on the impact on durable goods. NielsenIQ BASES recently conducted a survey that revealed that nearly a third of respondents have made durables purchases in response. The disease has also affected consumers' purchasing habits because they spend more of their time at home caring for children.
FAQ
What are the four types in manufacturing?
Manufacturing is the process by which raw materials are transformed into useful products through machines and processes. It includes many different activities like designing, building and testing, packaging, shipping and selling, as well as servicing.
What type of jobs is there in logistics
There are different kinds of jobs available in logistics. These are some of the jobs available in logistics:
-
Warehouse workers – They load and unload pallets and trucks.
-
Transportation drivers: They drive trucks and trailers and deliver goods and make pick-ups.
-
Freight handlers – They sort and package freight at warehouses.
-
Inventory managers – These people oversee inventory at warehouses.
-
Sales representatives: They sell products to customers.
-
Logistics coordinators - They organize and plan logistics operations.
-
Purchasing agents: They are responsible for purchasing goods and services to support company operations.
-
Customer service representatives - They answer calls and emails from customers.
-
Shipping clerks: They process shipping requests and issue bills.
-
Order fillers are people who fill orders based only on what was ordered.
-
Quality control inspectors – They inspect incoming and outgoing products to ensure that there are no defects.
-
Other - Logistics has many other job opportunities, including transportation supervisors, logistics specialists, and cargo specialists.
Why is logistics so important in manufacturing?
Logistics is an integral part of every business. They are essential to any business's success.
Logistics plays a significant role in reducing cost and increasing efficiency.
Why automate your warehouse
Modern warehousing is becoming more automated. With the rise of ecommerce, there is a greater demand for faster delivery times as well as more efficient processes.
Warehouses must adapt quickly to meet changing customer needs. To do so, they must invest heavily in technology. Automation of warehouses offers many benefits. Here are some benefits of investing in automation
-
Increases throughput/productivity
-
Reduces errors
-
Increases accuracy
-
Safety increases
-
Eliminates bottlenecks
-
Allows companies scale more easily
-
This makes workers more productive
-
Gives you visibility into all that is happening in your warehouse
-
Enhances customer experience
-
Improves employee satisfaction
-
Reducing downtime and increasing uptime
-
Ensures quality products are delivered on time
-
Eliminates human error
-
This helps to ensure compliance with regulations
How can overproduction in manufacturing be reduced?
Improved inventory management is the key to reducing overproduction. This would reduce the time spent on unproductive activities like purchasing, storing and maintaining excess stock. This could help us free up our time for other productive tasks.
A Kanban system is one way to achieve this. A Kanban board, a visual display to show the progress of work, is called a Kanban board. Kanban systems allow work items to move through different states until they reach their final destination. Each state has a different priority level.
For instance, when work moves from one stage to another, the current task is complete enough to be moved to the next stage. However, if a task is still at the beginning stages, it will remain so until it reaches the end of the process.
This helps to keep work moving forward while ensuring that no work is left behind. Managers can view the Kanban board to see how much work they have done. This information allows them to adjust their workflow based on real-time data.
Another way to control inventory levels is to implement lean manufacturing. Lean manufacturing focuses on eliminating waste throughout the entire production chain. Anything that doesn't add value to the product is considered waste. Some common types of waste include:
-
Overproduction
-
Inventory
-
Packaging not required
-
Exceed materials
These ideas can help manufacturers improve efficiency and reduce costs.
Statistics
- Many factories witnessed a 30% increase in output due to the shift to electric motors. (en.wikipedia.org)
- According to the United Nations Industrial Development Organization (UNIDO), China is the top manufacturer worldwide by 2019 output, producing 28.7% of the total global manufacturing output, followed by the United States, Japan, Germany, and India.[52][53] (en.wikipedia.org)
- (2:04) MTO is a production technique wherein products are customized according to customer specifications, and production only starts after an order is received. (oracle.com)
- In 2021, an estimated 12.1 million Americans work in the manufacturing sector.6 (investopedia.com)
- [54][55] These are the top 50 countries by the total value of manufacturing output in US dollars for its noted year according to World Bank.[56] (en.wikipedia.org)
External Links
How To
Six Sigma in Manufacturing
Six Sigma can be described as "the use of statistical process control (SPC), techniques to achieve continuous improvement." Motorola's Quality Improvement Department in Tokyo, Japan developed Six Sigma in 1986. Six Sigma's main goal is to improve process quality by standardizing processes and eliminating defects. Many companies have adopted Six Sigma in recent years because they believe that there are no perfect products and services. Six Sigma's main objective is to reduce variations from the production average. This means that you can take a sample from your product and then compare its performance to the average to find out how often the process differs from the norm. If you notice a large deviation, then it is time to fix it.
Understanding how your business' variability is a key step towards Six Sigma implementation is the first. Once you have this understanding, you will need to identify sources and causes of variation. Also, you will need to identify the sources of variation. Random variations happen when people make errors; systematic variations are caused externally. For example, if you're making widgets, and some of them fall off the assembly line, those would be considered random variations. But if you notice that every widget you make falls apart at the exact same place each time, this would indicate that there is a problem.
Once you've identified where the problems lie, you'll want to design solutions to eliminate those problems. It might mean changing the way you do business or redesigning it entirely. To verify that the changes have worked, you need to test them again. If they fail, you can go back to the drawing board to come up with a different plan.