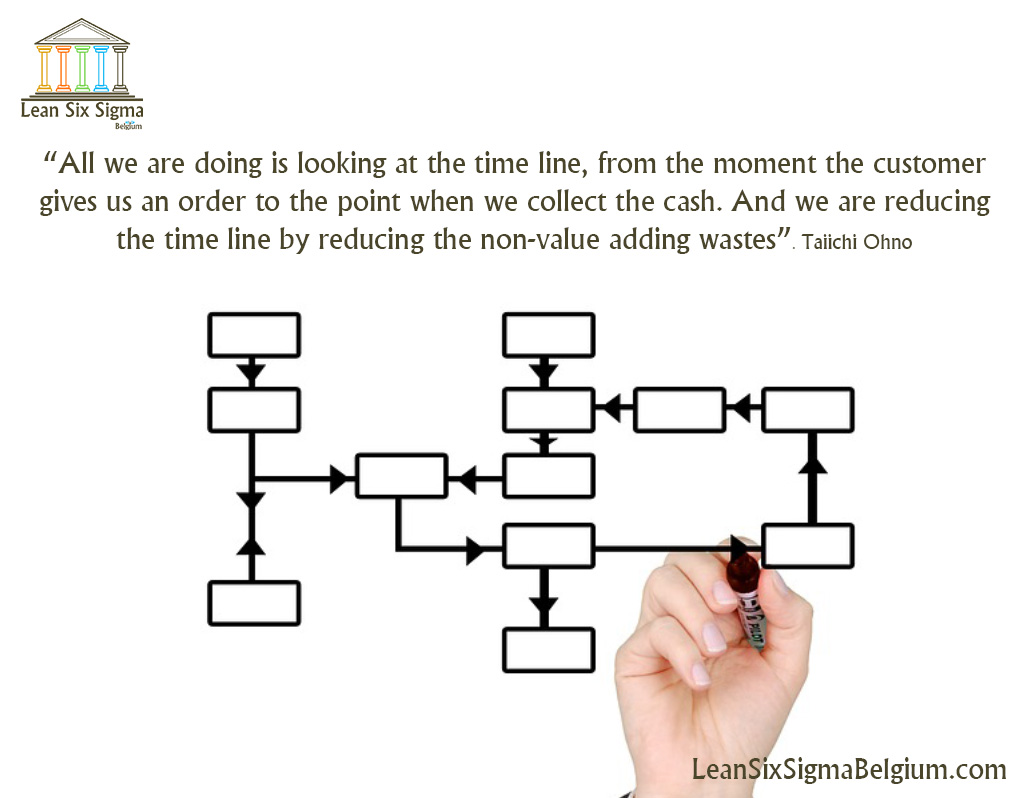
Facilities engineers, also known as maintenance and engineering engineers, provide engineering and support services for buildings and operations. They are responsible for developing and implementing procedures and recommending repairs and upgrades. They also coordinate routine and emergency maintenance. This role may include a range of engineering disciplines such as plumbing, electrical, or mechanical. Their technical skills are not only complemented by their understanding of construction law and safety standards.
As a career, facilities engineers typically begin at the entry level, and can quickly advance to more senior positions. A strong portfolio is key to standing out in this field. This could include research and articles, engineering projects, and research. Facilities engineers need to continue learning about their field. This will help them stand out when applying for a new position.
It is not required for every facility engineer, but a professional engineer certification could be an advantage when applying to a new position. An engineer must have a good understanding of engineering principles and concepts. They should also be able to make compelling presentations and analyze data. Facility engineers should be familiar with asset reliability-centered maintenance strategies and predictive maintenance.
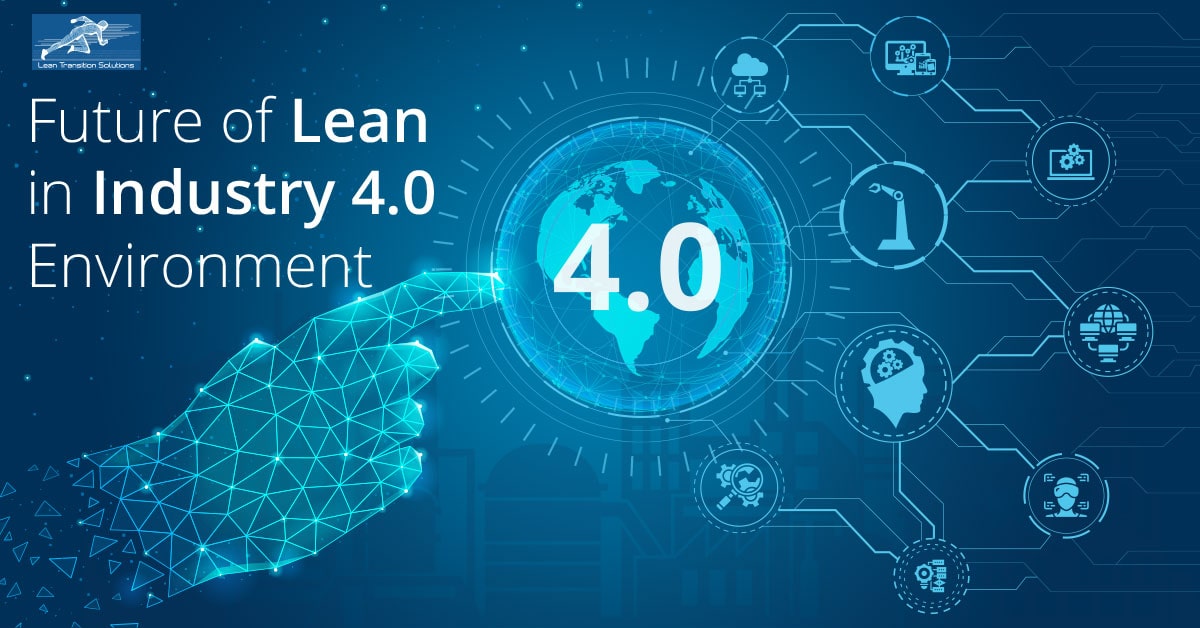
Facility engineers work in offices, construction, and manufacturing environments. They plan and execute processes to ensure that utilities are running safely and efficiently. Facilities engineers work closely with managers and other engineers. This helps to make work more efficient and resolves any problems.
The responsibilities of a facilities engineer will differ depending on the type and size of the facility they are assigned to. Typically, the job requires excellent time management skills, problem-solving abilities, and an ability to work well with others. On a typical working day, a facilities manager may be responsible for hundreds of tasks. A facilities engineer may be responsible for mechanical, electrical, or plumbing equipment. They must also be able troubleshoot problems and fix them.
There are many websites that provide news and information about the profession, including those of AFE (Association of Facility Engineers). These websites contain information about the profession, including a sample resume.
These websites are not the only way for facilities engineers to learn. They can also read articles and attend training courses. You will need to have excellent organizational skills and an understanding of different engineering and construction disciplines. Also, you must be familiar with building and safety codes.
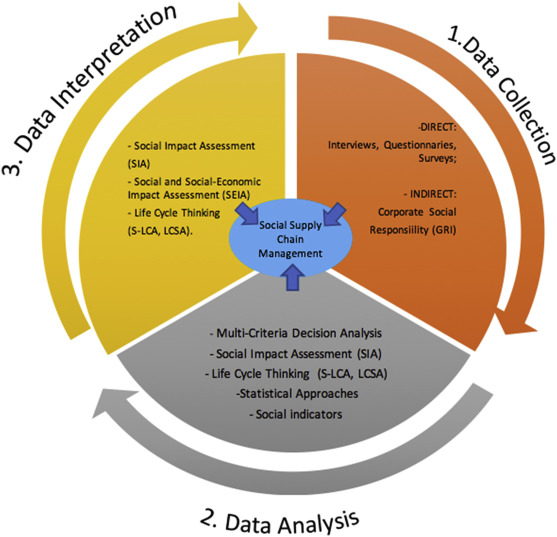
It's important to note that some of the most advanced facilities engineers are able to analyze data and perform a number of tasks at once. This requires a working knowledge in AutoCAD as well as construction techniques such as the CAM. Project management, problem-solving, and critical thinking are all skills that can be beneficial.
Facilities engineers have the opportunity to work with many people, which is one of the greatest advantages. These engineers can work with many different materials and coordinate other engineers' work.
FAQ
Can we automate some parts of manufacturing?
Yes! Yes! Automation has existed since ancient times. The Egyptians invented the wheel thousands of years ago. We now use robots to help us with assembly lines.
There are many applications for robotics in manufacturing today. These include:
-
Assembly line robots
-
Robot welding
-
Robot painting
-
Robotics inspection
-
Robots that create products
Manufacturing can also be automated in many other ways. 3D printing makes it possible to produce custom products in a matter of days or weeks.
What are the 4 types of manufacturing?
Manufacturing is the process of transforming raw materials into useful products using machines and processes. Manufacturing involves many activities, including designing, building, testing and packaging, shipping, selling, service, and so on.
What are manufacturing and logistic?
Manufacturing is the production of goods using raw materials. Logistics covers all aspects involved in managing supply chains, including procurement and production planning. Logistics and manufacturing are often referred to as one thing. It encompasses both the creation of products and their delivery to customers.
Why is logistics important in manufacturing
Logistics is an integral part of every business. They are essential to any business's success.
Logistics play a key role in reducing expenses and increasing efficiency.
Do we need to know about Manufacturing Processes before learning about Logistics?
No. No. Knowing about manufacturing processes will help you understand how logistics works.
Statistics
- Many factories witnessed a 30% increase in output due to the shift to electric motors. (en.wikipedia.org)
- [54][55] These are the top 50 countries by the total value of manufacturing output in US dollars for its noted year according to World Bank.[56] (en.wikipedia.org)
- (2:04) MTO is a production technique wherein products are customized according to customer specifications, and production only starts after an order is received. (oracle.com)
- It's estimated that 10.8% of the U.S. GDP in 2020 was contributed to manufacturing. (investopedia.com)
- According to the United Nations Industrial Development Organization (UNIDO), China is the top manufacturer worldwide by 2019 output, producing 28.7% of the total global manufacturing output, followed by the United States, Japan, Germany, and India.[52][53] (en.wikipedia.org)
External Links
How To
How to Use Lean Manufacturing for the Production of Goods
Lean manufacturing (or lean manufacturing) is a style of management that aims to increase efficiency, reduce waste and improve performance through continuous improvement. It was created in Japan by Taiichi Ohno during the 1970s and 80s. He received the Toyota Production System award (TPS), from Kanji Toyoda, founder of TPS. Michael L. Watkins published the original book on lean manufacturing, "The Machine That Changed the World," in 1990.
Lean manufacturing refers to a set of principles that improve the quality, speed and costs of products and services. It emphasizes the elimination of defects and waste throughout the value stream. Lean manufacturing is called just-in-time (JIT), zero defect, total productive maintenance (TPM), or 5S. Lean manufacturing seeks to eliminate non-value added activities, such as inspection, work, waiting, and rework.
Lean manufacturing is a way for companies to achieve their goals faster, improve product quality, and lower costs. Lean manufacturing can be used to manage all aspects of the value chain. Customers, suppliers, distributors, retailers and employees are all included. Lean manufacturing practices are widespread in many industries. Toyota's philosophy, for example, is what has enabled it to be successful in electronics, automobiles, medical devices, healthcare and chemical engineering as well as paper and food.
Five fundamental principles underlie lean manufacturing.
-
Define value - Find out what your business contributes to society, and what makes it different from other competitors.
-
Reduce waste - Stop any activity that isn't adding value to the supply chains.
-
Create Flow – Ensure that work flows smoothly throughout the process.
-
Standardize and simplify – Make processes as repeatable and consistent as possible.
-
Develop Relationships: Establish personal relationships both with internal and external stakeholders.
Lean manufacturing isn’t new, but it has seen a renewed interest since 2008 due to the global financial crisis. Many businesses have adopted lean manufacturing techniques to help them become more competitive. According to some economists, lean manufacturing could be a significant factor in the economic recovery.
Lean manufacturing is now becoming a common practice in the automotive industry, with many benefits. These include higher customer satisfaction levels, reduced inventory levels as well as lower operating costs.
The principles of lean manufacturing can be applied in almost any area of an organization. It is especially useful for the production aspect of an organization, as it ensures that every step in the value chain is efficient and effective.
There are three types of lean manufacturing.
-
Just-in-Time Manufacturing (JIT): This type of lean manufacturing is commonly referred to as "pull systems." JIT is a process in which components can be assembled at the point they are needed, instead of being made ahead of time. This approach is designed to reduce lead times and increase the availability of components. It also reduces inventory.
-
Zero Defects Manufacturing (ZDM),: ZDM is a system that ensures no defective units are left the manufacturing facility. Repairing a part that is damaged during assembly should be done, not scrapping. This applies to finished goods that may require minor repairs before shipment.
-
Continuous Improvement (CI: Continuous improvement aims to increase the efficiency of operations by constantly identifying and making improvements to reduce or eliminate waste. Continuous Improvement involves continuous improvement of processes.