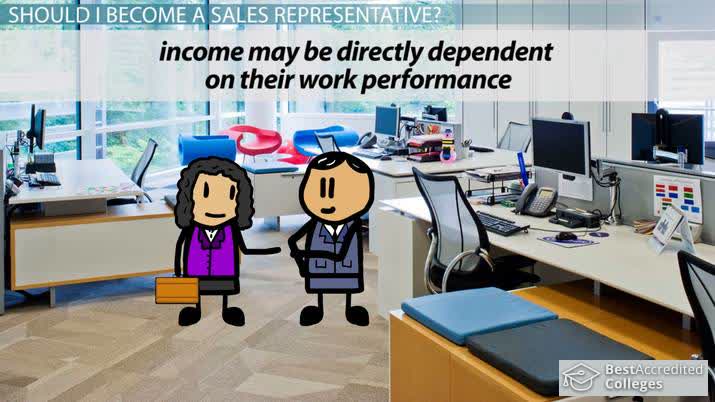
The supply chain certification is a great way for you to show that your expertise in the field. A credential such as the CSCP will make you more valuable to your employer and will set you apart from your peers. It will make your organization more competitive in today's economic environment. Here are some benefits of being certified in supply chains management.
CSCP certifies supply chains at every stage of the supply chain.
Supply chain professionals will find the CSCP certification valuable because it gives them a better understanding of the supply chains and allows them to see the whole process. End-to end supply chain activities can be complex. The CSCP certificate tests the candidate’s skills in coordinating these activities and integrating them. Companies are looking to hire supply chain professionals who will add value at every point of the supply-chain.
The CSCP certification exam consists in eight modules. They cover all aspects of supply chain management. The questions in the exam are divided into two parts, with the first three focusing on knowledge of the curriculum. The final two questions are intended to test candidates' preparation for the final exam. A pass is defined as a score between 200 and 350 points. Scores of 300 or greater are considered passing. A score below this number is considered a fail.
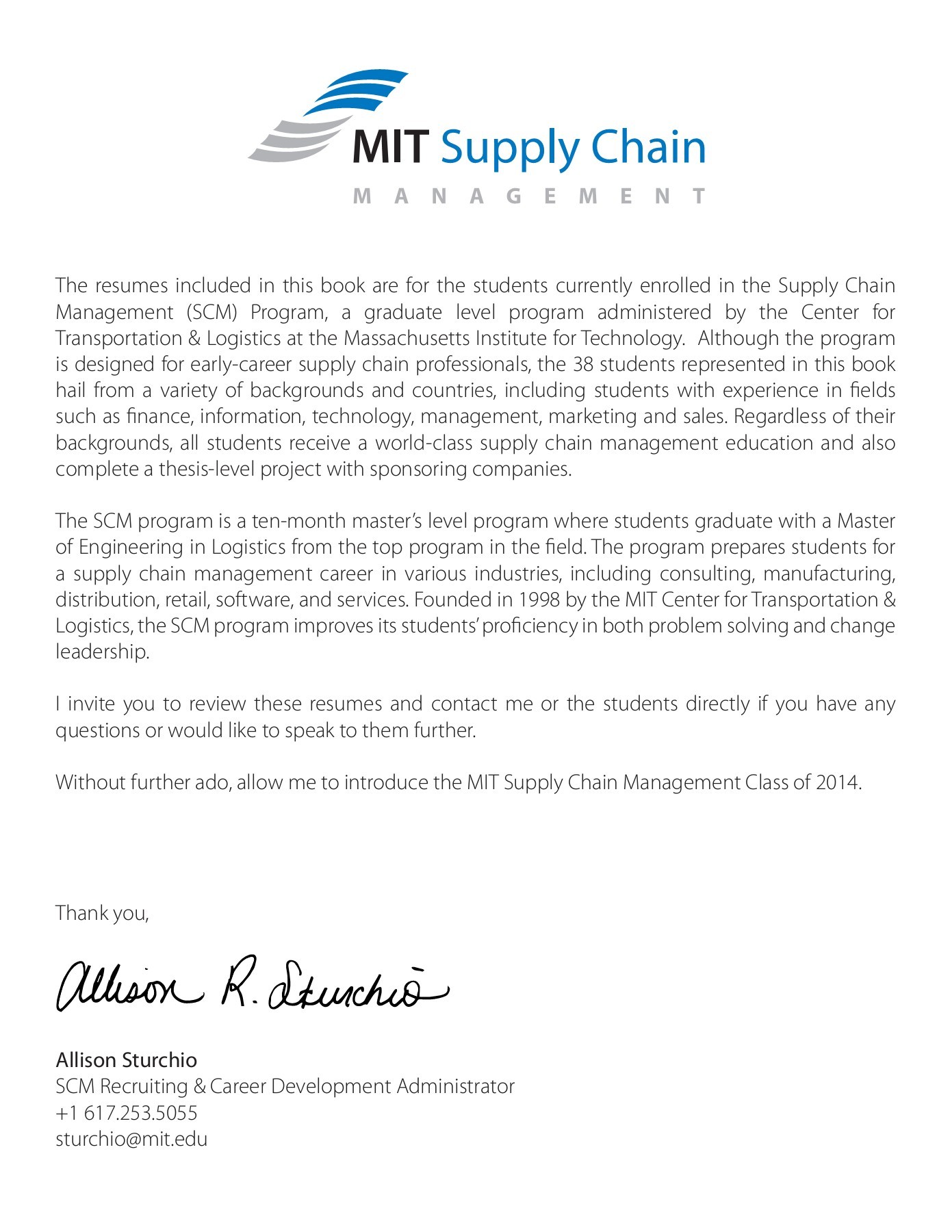
CPSM certification is a specialized supply chain certification
The CPSM credential (Certified Professional in Supply Management), is one of the most prestigious and highly respected supply chain certifications. The Institute for Supply Management, which is the world's largest supply management association, issues the CPSM credential. International recognition is granted to CPSM certificates.
The CPSM certification is a high standard of excellence for supply-management professionals. It includes three modules that test your advanced knowledge and skills. Earning this certification will allow supply management professionals to implement supply chain strategies throughout an organization. The certification process takes between six and twelve months. Successful candidates must renew the credential every three year.
CSCP requires four-year undergraduate degree
A CSCP certification is a Certified Supply Chain Professional. It shows that an individual has a high level of knowledge and experience with supply chain management. This credential differentiates one from their peers and proves that they have the expertise in their field. There are many options to choose from if you are interested in getting this certification.
Three years of experience in the workplace and a bachelor's degree are required for the CSCP exam. Students will need to accumulate 75 professional learning points every five year in order for their certification to continue. If they retake the exam, they will need to earn another 75 points.
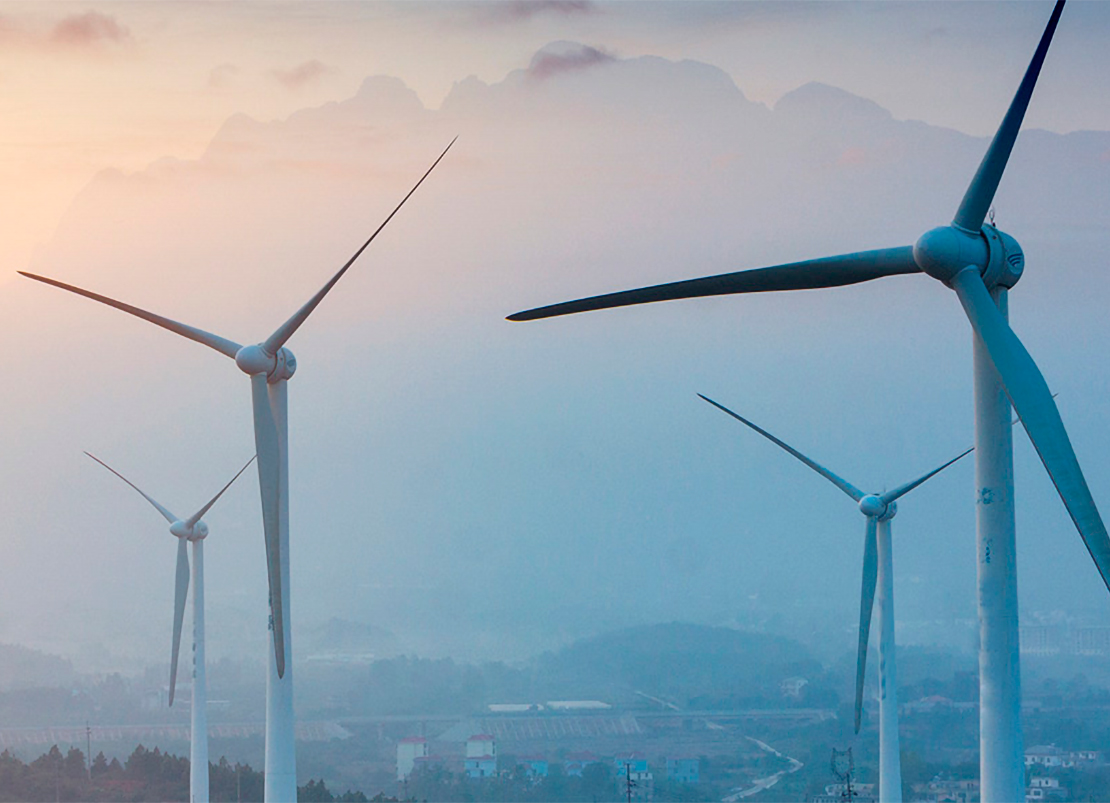
Supply chain certification requires a retake fee
Multiple-choice online certification exam Certified Supply Chain Fundamentals(tm). You can take the test anywhere in the world. It consists of 50 multiple-choice questions. To receive the certification, you must score 70% or better on the test. Retake fees are $450 USD.
For the exam to be valid, you must have previously worked in a decisionmaking position. Any job that involves controlling processes or defining projects is considered "decision-making". This could include a supervisory or management position. Other certifications such as ASQ can be used to take the Supplier Quality Professional exam.
FAQ
How can manufacturing reduce production bottlenecks?
Production bottlenecks can be avoided by ensuring that processes are running smoothly during the entire production process, starting with the receipt of an order and ending when the product ships.
This includes both planning for capacity and quality control.
Continuous improvement techniques such Six Sigma can help you achieve this.
Six Sigma is a management method that helps to improve quality and reduce waste.
It's all about eliminating variation and creating consistency in work.
What skills does a production planner need?
You must be flexible and organized to become a productive production planner. Communication skills are essential to ensure that you can communicate effectively with clients, colleagues, and customers.
How can manufacturing overproduction be reduced?
Better inventory management is key to reducing excess production. This would decrease the time that is spent on inefficient activities like purchasing, storing, or maintaining excess stock. By doing this, we could free up resources for other productive tasks.
A Kanban system is one way to achieve this. A Kanbanboard is a visual tool that allows you to keep track of the work being done. Kanban systems allow work items to move through different states until they reach their final destination. Each state represents a different priority level.
For instance, when work moves from one stage to another, the current task is complete enough to be moved to the next stage. A task that is still in the initial stages of a process will be considered complete until it moves on to the next stage.
This allows work to move forward and ensures that no work is missed. Managers can see how much work has been done and the status of each task at any time with a Kanban Board. This information allows them to adjust their workflow based on real-time data.
Another way to control inventory levels is to implement lean manufacturing. Lean manufacturing is about eliminating waste from all stages of the production process. Anything that does not contribute to the product's value is considered waste. Some common types of waste include:
-
Overproduction
-
Inventory
-
Packaging not required
-
Materials in excess
Manufacturers can increase efficiency and decrease costs by implementing these ideas.
Statistics
- In the United States, for example, manufacturing makes up 15% of the economic output. (twi-global.com)
- According to the United Nations Industrial Development Organization (UNIDO), China is the top manufacturer worldwide by 2019 output, producing 28.7% of the total global manufacturing output, followed by the United States, Japan, Germany, and India.[52][53] (en.wikipedia.org)
- You can multiply the result by 100 to get the total percent of monthly overhead. (investopedia.com)
- [54][55] These are the top 50 countries by the total value of manufacturing output in US dollars for its noted year according to World Bank.[56] (en.wikipedia.org)
- According to a Statista study, U.S. businesses spent $1.63 trillion on logistics in 2019, moving goods from origin to end user through various supply chain network segments. (netsuite.com)
External Links
How To
Six Sigma and Manufacturing
Six Sigma is defined as "the application of statistical process control (SPC) techniques to achieve continuous improvement." Motorola's Quality Improvement Department in Tokyo, Japan developed Six Sigma in 1986. Six Sigma's core idea is to improve the quality of processes by standardizing and eliminating defects. Many companies have adopted Six Sigma in recent years because they believe that there are no perfect products and services. Six Sigma's main objective is to reduce variations from the production average. You can calculate the percentage of deviation from the norm by taking a sample of your product and comparing it to the average. If there is a significant deviation from the norm, you will know that something needs to change.
The first step toward implementing Six Sigma is understanding how variability works in your business. Once you have this understanding, you will need to identify sources and causes of variation. You'll also want to determine whether these variations are random or systematic. Random variations are caused by human errors. Systematic variations can be caused by outside factors. These are, for instance, random variations that occur when widgets are made and some fall off the production line. You might notice that your widgets always fall apart at the same place every time you put them together.
Once you have identified the problem, you can design solutions. The solution could involve changing how you do things, or redesigning your entire process. Test them again once you've implemented the changes. If they don't work, you will need to go back to the drawing boards and create a new plan.