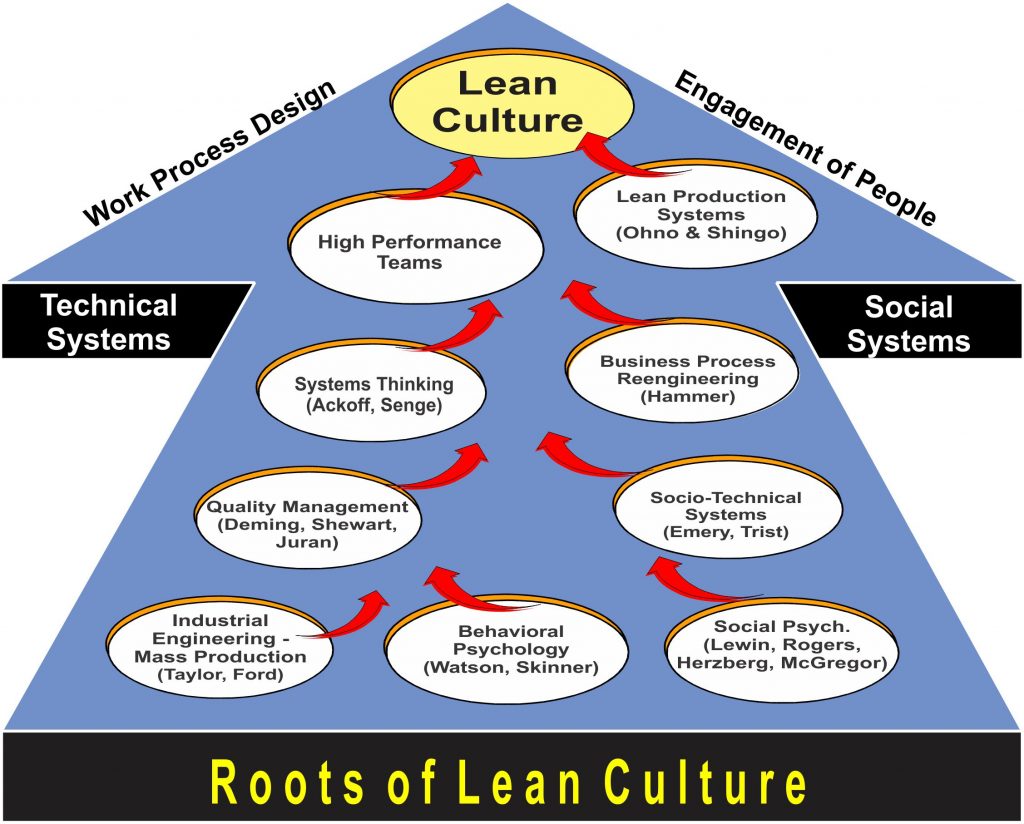
OEE stands for Overall Equipment Effectiveness. OEE is used to measure the equipment's effectiveness. This article will explain the basics of OEE and how it is calculated. It is a best-practice metric that measures availability, performance, and quality. OEE is used to improve the efficiency of manufacturing operations by reducing downtime and increasing production. It helps manufacturers save money.
OEE refers to a measure of labor efficiency.
OEE is an indicator of overall production quality. It's based on the interaction of availability and quality. OEE represents the loss of time due to inconsistent production. These include the time down, rate fluctuations in process, scrap, and any rework that is generated during operative modes.
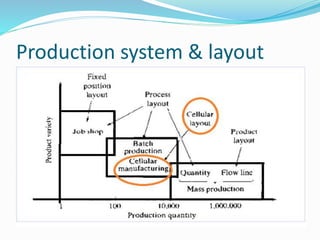
It's based on Availability and Performance as well as Quality
OEE refers to a production management system that emphasizes availability, performance, and quality. The time a product or service is made available for sale or use is called availability. For example, availability could be defined as between delivery to customers and recovery or between scrapping or repair. Performance directly relates to the quality and performance of a business. It is possible to measure your performance by hiring a professional company who can evaluate your business processes and offer recommendations for improvement.
It is a benchmark for best practices.
OEE is a fantastic tool for measuring and optimizing your operation. This metric allows you to analyze different levels of your operations, which can help you reduce waste and improve your operations. However, it is important to note that it cannot be used as an end-all-be-all metric. You should pilot any OEE improvement program before you start it.
It is a directional measurement
OEE can be defined to its exact meaning. It is also used as a directional indicator to compare performance between similar machines within a company. Companies can track the efficiency of their machines by measuring it consistently across all machines.
It is called a TPM metric.
It is useful for measuring production efficiency. It measures losses and inefficiencies across three key areas: availability; performance; and quality. The metric can be used to track improvements and identify areas for improvement.
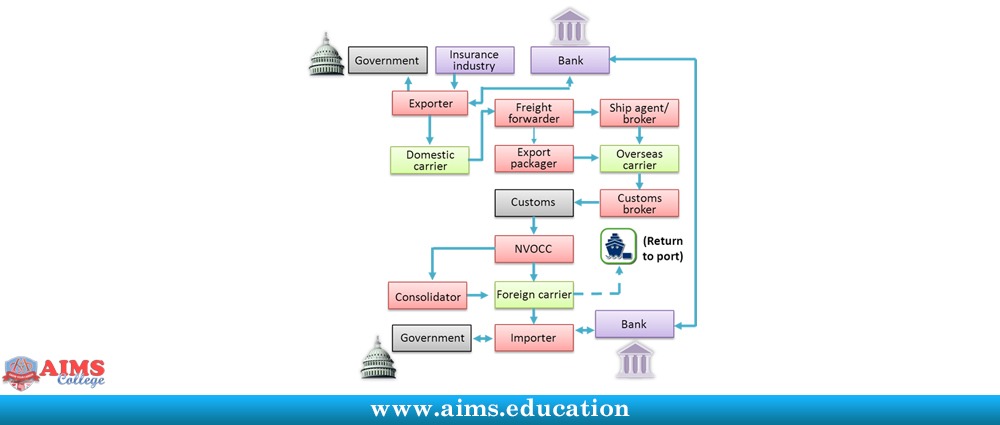
It is a manufacturing best practise
OEE stands for overall equipment efficiency. It is the ratio of what a machine (or cell) can produce in a specified time frame to how long it takes to produce that product. It is important to minimize downtime and maximize OEE. As a result, manufacturing operations can improve quality and reduce costs.
FAQ
What are the main products of logistics?
Logistics is the process of moving goods from one point to another.
They cover all aspects of transportation, such as packing, loading, transporting and unloading.
Logisticians ensure that the right product reaches the right place at the right time and under safe conditions. They help companies manage their supply chain efficiency by providing information on demand forecasts, stock levels, production schedules, and availability of raw materials.
They can also track shipments in transit and monitor quality standards.
How does manufacturing avoid bottlenecks in production?
The key to avoiding bottlenecks in production is to keep all processes running smoothly throughout the entire production cycle, from the time you receive an order until the time when the product ships.
This includes both planning for capacity and quality control.
This can be done by using continuous improvement techniques, such as Six Sigma.
Six Sigma can be used to improve the quality and decrease waste in all areas of your company.
It focuses on eliminating variation and creating consistency in your work.
What is the role of a production manager?
A production planner ensures all aspects of the project are delivered on time, within budget, and within scope. They also ensure the quality of the product and service meets the client's requirements.
What does the term manufacturing industries mean?
Manufacturing Industries refers to businesses that manufacture products. The people who buy these products are called consumers. These companies use a variety processes such as distribution, retailing and management to accomplish their purpose. They create goods from raw materials, using machines and various other equipment. This includes all types if manufactured goods.
How can we increase manufacturing efficiency?
The first step is to identify the most important factors affecting production time. We must then find ways that we can improve these factors. If you aren't sure where to begin, think about the factors that have the greatest impact on production time. Once you've identified them, try to find solutions for each of those factors.
What is production plan?
Production Planning is the creation of a plan to cover all aspects, such as scheduling, budgeting. Location, crew, equipment, props and other details. This document ensures that everything is prepared and available when you are ready for shooting. This document should include information about how to achieve the best results on-set. This includes location information, crew details, equipment specifications, and casting lists.
The first step in filming is to define what you want. You may have already chosen the location you want, or there are locations or sets you prefer. Once you have identified the scenes and locations, you can start to determine which elements are required for each scene. Perhaps you have decided that you need to buy a car but aren't sure which model. In this case, you could start looking up cars online to find out what models are available and then narrow your choices by choosing between different makes and models.
After you have selected the car you want, you can begin to think about additional features. Are you looking for people to sit in the front seats? Perhaps you have someone who needs to be able to walk around the back of your car. Perhaps you would like to change the interior colour from black to white. These questions will help you determine the exact look and feel of your car. The type of shots that you are looking for is another thing to consider. What type of shots will you choose? Maybe you want to show the engine and the steering wheel. These things will help you to identify the car that you are looking for.
Once you have all the information, you are ready to create a plan. A schedule will tell you when you need to start shooting and when you need to finish. A schedule for each day will detail when you should arrive at the location and when you need leave. It will help everyone know exactly what they have to do and when. Book extra staff ahead of time if you need them. It is not worth hiring someone who won’t show up because you didn’t tell him.
Also, consider how many days you will be filming your schedule. Some projects are quick and easy, while others take weeks. When creating your schedule, be aware of whether you need more shots per day. Multiple takes at the same place will result in higher costs and longer completion times. If you are unsure if you need multiple takes, it is better to err on the side of caution and shoot fewer takes rather than risk wasting money.
Budgeting is another important aspect of production planning. As it will allow you and your team to work within your financial means, setting a realistic budget is crucial. Keep in mind that you can always reduce your budget if you face unexpected difficulties. However, you shouldn't overestimate the amount of money you will spend. You'll end up with less money after paying for other things if the cost is underestimated.
Planning production is a tedious process. Once you have a good understanding of how everything works together, planning future projects becomes easy.
Statistics
- According to the United Nations Industrial Development Organization (UNIDO), China is the top manufacturer worldwide by 2019 output, producing 28.7% of the total global manufacturing output, followed by the United States, Japan, Germany, and India.[52][53] (en.wikipedia.org)
- [54][55] These are the top 50 countries by the total value of manufacturing output in US dollars for its noted year according to World Bank.[56] (en.wikipedia.org)
- In 2021, an estimated 12.1 million Americans work in the manufacturing sector.6 (investopedia.com)
- Many factories witnessed a 30% increase in output due to the shift to electric motors. (en.wikipedia.org)
- According to a Statista study, U.S. businesses spent $1.63 trillion on logistics in 2019, moving goods from origin to end user through various supply chain network segments. (netsuite.com)
External Links
How To
How to use 5S to increase Productivity in Manufacturing
5S stands in for "Sort", the "Set In Order", "Standardize", or "Separate". Toyota Motor Corporation developed the 5S method in 1954. It allows companies to improve their work environment, thereby achieving greater efficiency.
The basic idea behind this method is to standardize production processes, so they become repeatable, measurable, and predictable. It means tasks like cleaning, sorting or packing, labeling, and storing are done every day. Workers can be more productive by knowing what to expect.
Five steps are required to implement 5S: Sort, Set In Order, Standardize. Separate. Each step has a different action and leads to higher efficiency. Sorting things makes it easier to find them later. When items are ordered, they are put together. Next, organize your inventory into categories and store them in containers that are easily accessible. Labeling your containers will ensure that everything is correctly labeled.
Employees will need to be more critical about their work. Employees need to be able understand their motivations and discover alternative ways to do them. They will need to develop new skills and techniques in order for the 5S system to be implemented.
The 5S method increases efficiency and morale among employees. As they begin to see improvements, they feel motivated to continue working towards the goal of achieving higher levels of efficiency.