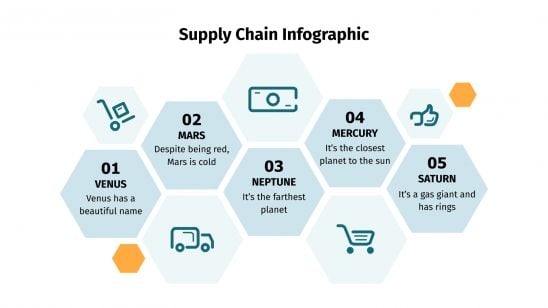
The Defense Industrial Base is a network of more that 200,000 companies who supply goods and service to the Department of Defense. It includes small businesses, big corporations, and startups. A new report from Government Accountability Office shows the risks that DIB faces as well as the challenges it faces in addressing those threats.
Over the past 10 years, the defense industrial base has declined by nearly 40 percent. In order to attract new people into the sector, the Department of Defense struggled. The Defense Department has made a number of attempts to encourage businesses to join the sector. Despite these efforts, many small firms are being left behind. This has increased national security risks.
Diverse DOD offices are working on mitigation of risks in the DIB. However, the department has not developed a comprehensive strategy to assess and manage these risks. In order to identify areas where the department can improve, GAO analyzed several reports from the department and interviewed DOD officials. GAO identified five components that could help the department meet its goals.
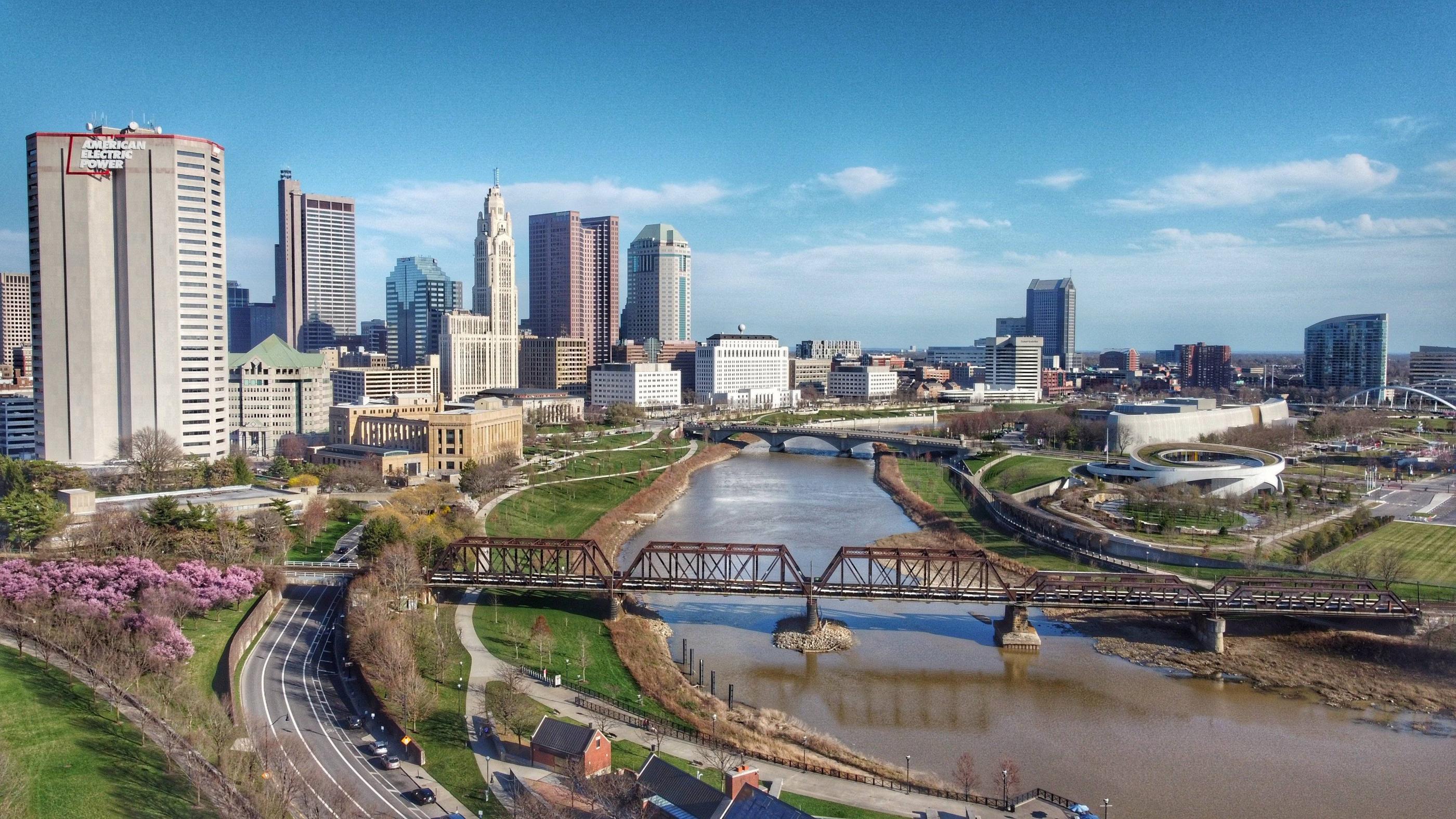
Loss of commercial suppliers will be a concern. These businesses supply parts for the Pentagon's weapon systems. The industry's small business sector has been declining over the last decade. It is not easy to know how many new companies will enter the market.
Other problems include material shortages as well as reliance on foreign vendors. Additional problems include intellectual property restrictions that slow down the military's acquisitions process and a lack of standardization for what is considered "new entrant" to the defense industry base.
GAO recommended that Defense review its policy regarding mitigating risk in the DIB. The GAO also recommended that the department continue to engage with traditional defense contractors and to implement tools that will make commercial technology providers more easily enter the DoD market. These recommendations should be part of an overall strategy for addressing industrial base concerns.
As part this strategy, the Defense Department needs to think about how it can use its OTAs as well as CSOs to accelerate acquisition strategy creation. You can restructure the supply chain to achieve dynamic results by using the right people, processes and technologies.
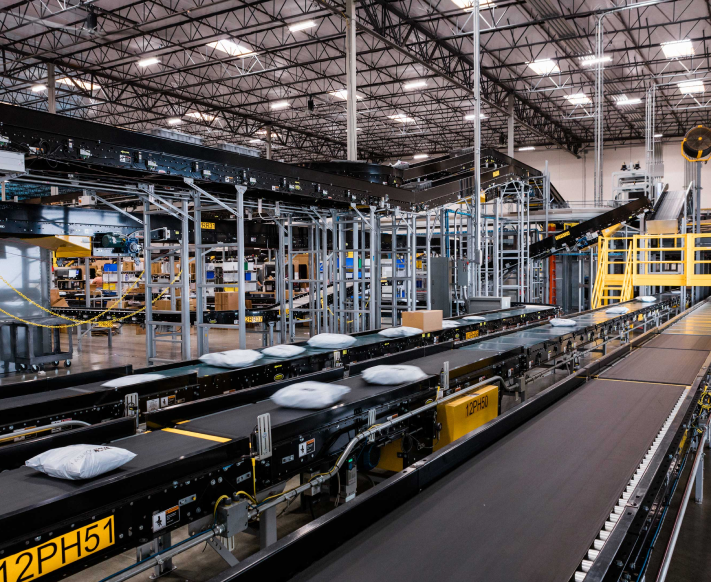
Despite the fact that the number has dropped over the past decade in defense industry, it is still developing. Many companies do not feel comfortable with the Federal Acquisition Regulation (FAR). Additionally, small businesses might not have as many opportunities to compete with the larger companies in the current market.
Innovation in defense industry base is crucially dependent on small businesses and startups. Part of the resilient DIB, companies can support National Security needs while allowing Department of Defense to develop new and better military equipment.
Overall, the defense industrial base is a complex industry that requires a comprehensive strategy to ensure that resources are aligned with the needs of the military. The Department of Defense should continue to learn about the best practices for integrating technology in its business processes. This will enable it to create more innovative products and services.
FAQ
What is the importance of automation in manufacturing?
Automation is important not only for manufacturers but also for service providers. Automation allows them to deliver services quicker and more efficiently. In addition, it helps them reduce costs by reducing human errors and improving productivity.
How can I find out more about manufacturing?
Practical experience is the best way of learning about manufacturing. However, if that's not possible, you can always read books or watch educational videos.
How can manufacturing avoid production bottlenecks
You can avoid bottlenecks in production by making sure that everything runs smoothly throughout the production cycle, from the moment you receive an order to the moment the product is shipped.
This includes planning for capacity requirements as well as quality control measures.
Continuous improvement techniques such Six Sigma are the best method to accomplish this.
Six Sigma is a management system used to improve quality and reduce waste in every aspect of your organization.
It's all about eliminating variation and creating consistency in work.
Statistics
- It's estimated that 10.8% of the U.S. GDP in 2020 was contributed to manufacturing. (investopedia.com)
- (2:04) MTO is a production technique wherein products are customized according to customer specifications, and production only starts after an order is received. (oracle.com)
- According to a Statista study, U.S. businesses spent $1.63 trillion on logistics in 2019, moving goods from origin to end user through various supply chain network segments. (netsuite.com)
- Many factories witnessed a 30% increase in output due to the shift to electric motors. (en.wikipedia.org)
- According to the United Nations Industrial Development Organization (UNIDO), China is the top manufacturer worldwide by 2019 output, producing 28.7% of the total global manufacturing output, followed by the United States, Japan, Germany, and India.[52][53] (en.wikipedia.org)
External Links
How To
How to Use Lean Manufacturing in the Production of Goods
Lean manufacturing (or lean manufacturing) is a style of management that aims to increase efficiency, reduce waste and improve performance through continuous improvement. It was developed by Taiichi Okono in Japan, during the 1970s & 1980s. TPS founder Kanji Takoda awarded him the Toyota Production System Award (TPS). Michael L. Watkins published the "The Machine That Changed the World", the first book about lean manufacturing. It was published in 1990.
Lean manufacturing is often defined as a set of principles used to improve the quality, speed, and cost of products and services. It emphasizes reducing defects and eliminating waste throughout the value chain. Lean manufacturing is also known as just in time (JIT), zero defect total productive maintenance(TPM), and five-star (S). Lean manufacturing is about eliminating activities that do not add value, such as inspection, rework, and waiting.
Lean manufacturing is a way for companies to achieve their goals faster, improve product quality, and lower costs. Lean manufacturing has been deemed one of the best ways to manage the entire value-chain, including customers, distributors as well retailers and employees. Lean manufacturing is widely practiced in many industries around the world. Toyota's philosophy is the foundation of its success in automotives, electronics and appliances, healthcare, chemical engineers, aerospace, paper and food, among other industries.
Lean manufacturing includes five basic principles:
-
Define Value- Identify the added value your company brings to society. What makes you stand out from your competitors?
-
Reduce Waste - Remove any activity which doesn't add value to your supply chain.
-
Create Flow: Ensure that the work process flows without interruptions.
-
Standardize & Simplify - Make processes as consistent and repeatable as possible.
-
Build relationships - Develop and maintain personal relationships with both your internal and external stakeholders.
Lean manufacturing isn’t new, but it has seen a renewed interest since 2008 due to the global financial crisis. Many businesses are now using lean manufacturing to improve their competitiveness. Some economists even believe that lean manufacturing can be a key factor in economic recovery.
Lean manufacturing is becoming a popular practice in automotive. It has many advantages. These include higher customer satisfaction levels, reduced inventory levels as well as lower operating costs.
Lean manufacturing can be applied to almost every aspect of an organization. Because it makes sure that all value chains are efficient and effectively managed, Lean Manufacturing is particularly helpful for organizations.
There are three main types in lean manufacturing
-
Just-in Time Manufacturing: This lean manufacturing method is commonly called "pull systems." JIT refers to a system in which components are assembled at the point of use instead of being produced ahead of time. This approach reduces lead time, increases availability and reduces inventory.
-
Zero Defects Manufacturing - ZDM: ZDM focuses its efforts on making sure that no defective units leave a manufacturing facility. You should repair any part that needs to be repaired during an assembly line. This also applies to finished products that need minor repairs before being shipped.
-
Continuous Improvement (CI),: Continuous improvement aims improve the efficiency and effectiveness of operations by continuously identifying issues and making changes to reduce waste. Continuous Improvement (CI) involves continuous improvement in processes, people, tools, and infrastructure.