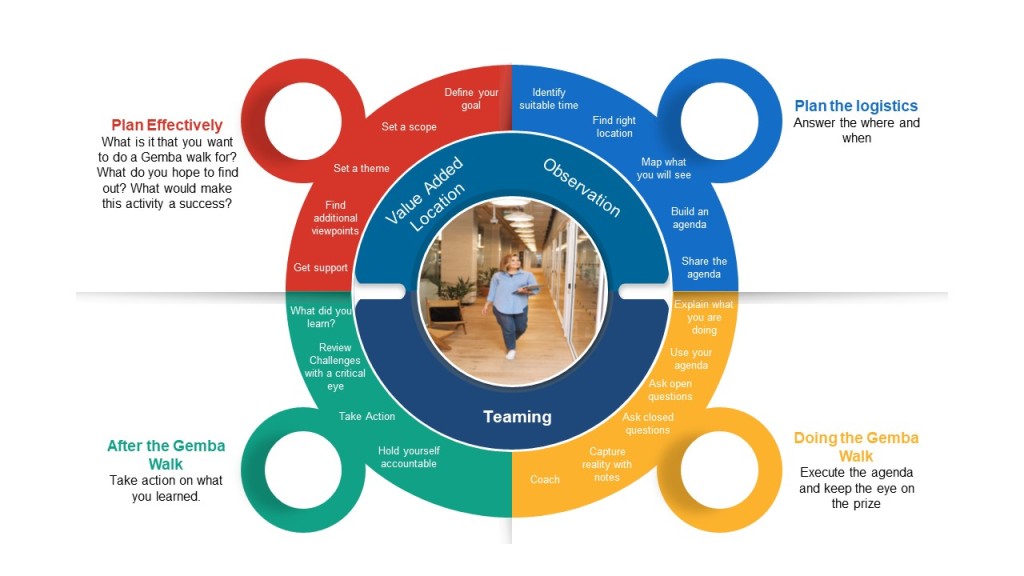
Murata Manufacturing Co. Ltd. is located in Kyoto Japan and can be a great choice for an electronics component manufacturer. From the name alone, you'll know that the company has been around for more than 100 years. You should also be aware of other companies. We'll tell you about their products as well as their services. This company manufactures electronic parts used in many kinds of electronics including printers and home appliances.
Murata Manufacturing Co., Ltd.
Murata Manufacturing Co., Ltd., Japan's leading electronic component manufacturer, is based out of Kyoto, Japan. It manufactures electronic components like circuit boards, transistors and LEDs. Continue reading to learn more about the company’s products. Learn more about Murata's manufacturing process. You can also view the most popular Murata products. For more information, visit Murata's website.
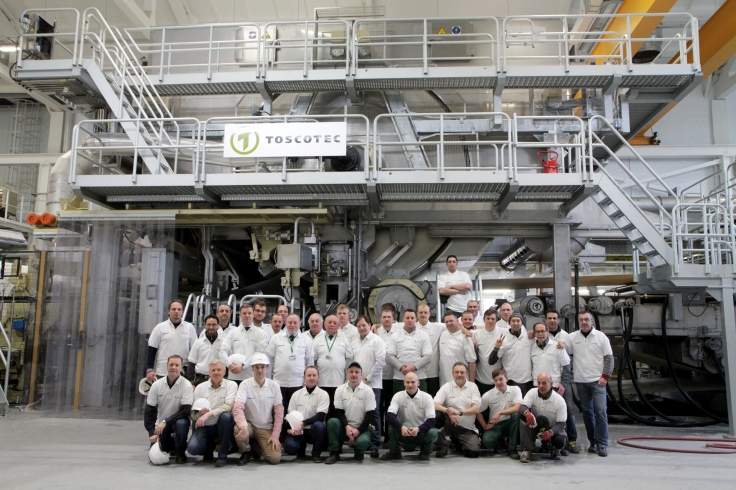
Murata Energy Device Singapore Pte Ltd
The company's motto is "Making Primary batteries." This subsidiary is part of Murata Manufacturing Co. Ltd. in Japan, headquartered in Nagaokakyo. Murata Singapore, which was founded in 1972, is the oldest Murata factory outside Japan. Its mission, is to fulfill the South East Asia electronics market demand. Murata acquired Sony Energy Devices Corporation (2017 acquisition). The headquarters of the company is located in Singapore at 1 Tuas Road.
Murata Electronics Trading (Tianjin) Co. Ltd
Since 2007, the Murata Electronics Trading Corporation (METC), has been in Tianjin. MEC is originally from Japan. It focuses its efforts on supplying high quality electronic parts to global markets. The company's operations have expanded to include sales of components that prevent EMI in the past few years. It also has technical support services that help solve customers' EMC problems.
Murata Vios
Murata Vios a new medical technology is on its way to hospitals. The Japanese firm is working to develop a monitoring system that can detect early signs of clinical decline. It is wireless and can be used in conjunction with Hicuity Health. This company provides clinical oversight and engages specialists to respond to patient deterioration. By combining these two technologies, Murata Vios is launching a custom offering to care providers and clinicians.
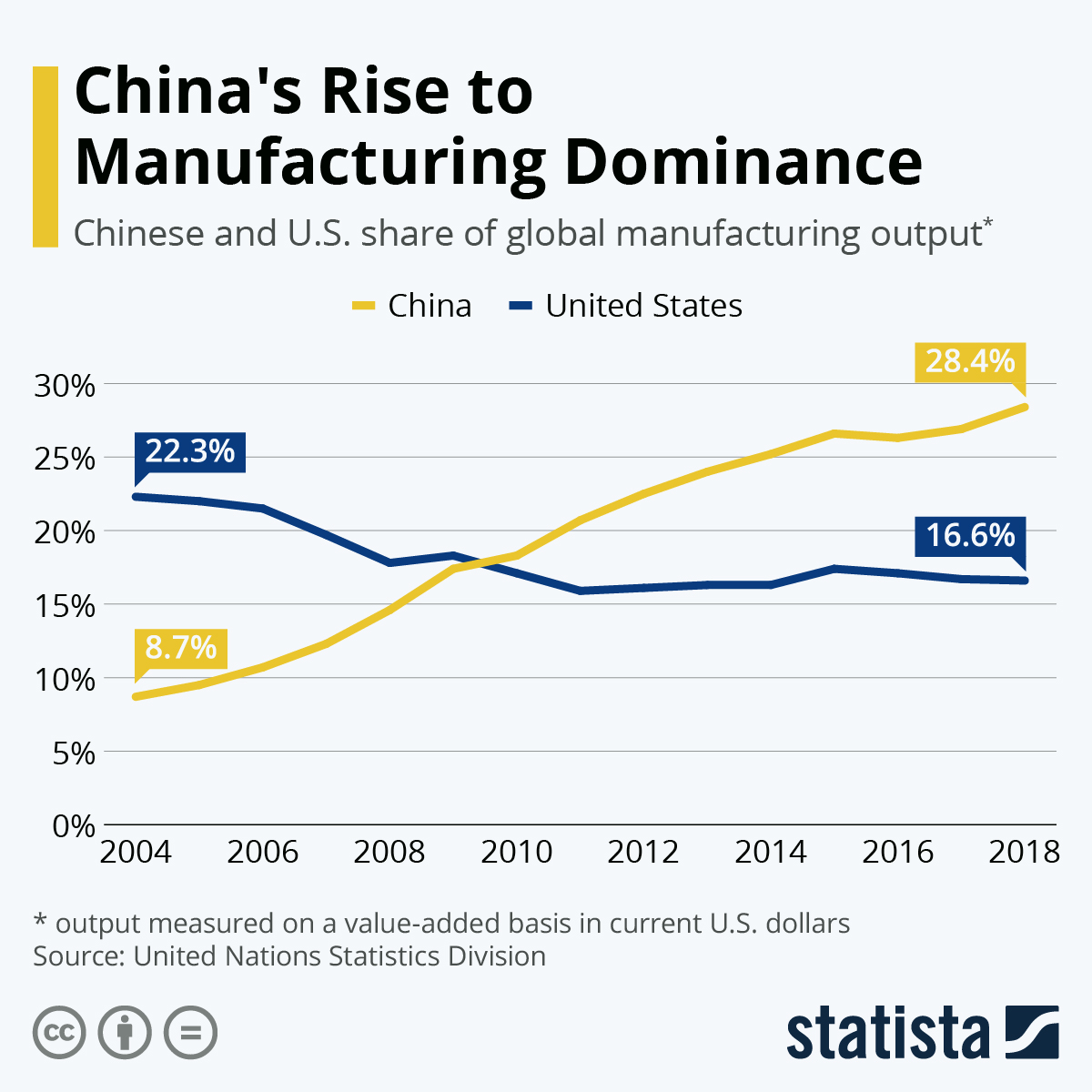
PointClickCare integration of Murata Vios
Murata, Inc.'s Vios Monitoring System has been integrated with PointClickCare, an online senior care software provider. This integration reduces errors in transcription and data entry time lags. It also improves clinician efficiency. Vios Monitoring System tracks information like heart rate (heart rate), oxygen levels, pulse, respiratory rates, and posture. These data are important in order to implement a patient-centric healthcare plan.
FAQ
How can manufacturing overproduction be reduced?
It is essential to find better ways to manage inventory to reduce overproduction. This would reduce the time needed to manage inventory. This would allow us to use our resources for more productive tasks.
This can be done by using a Kanban system. A Kanban board, a visual display to show the progress of work, is called a Kanban board. Kanban systems are where work items travel through a series of states until reaching their final destination. Each state represents a different priority level.
When work is completed, it can be transferred to the next stage. If a task is still in its beginning stages, it will continue to be so until it reaches the end.
This allows you to keep work moving along while making sure that no work gets neglected. With a Kanban board, managers can see exactly how much work is being done at any given moment. This data allows them adjust their workflow based upon real-time data.
Lean manufacturing is another way to manage inventory levels. Lean manufacturing seeks to eliminate waste from every step of the production cycle. Waste includes anything that does not add value to the product. There are several types of waste that you might encounter:
-
Overproduction
-
Inventory
-
Packaging that is not necessary
-
Materials in excess
These ideas can help manufacturers improve efficiency and reduce costs.
How can manufacturing reduce production bottlenecks?
Production bottlenecks can be avoided by ensuring that processes are running smoothly during the entire production process, starting with the receipt of an order and ending when the product ships.
This includes planning for both capacity requirements and quality control measures.
Continuous improvement techniques like Six Sigma are the best way to achieve this.
Six Sigma is a management method that helps to improve quality and reduce waste.
It emphasizes consistency and eliminating variance in your work.
What does warehouse mean?
A warehouse or storage facility is where goods are stored before they are sold. You can have it indoors or outdoors. It could be one or both.
What is the distinction between Production Planning or Scheduling?
Production Planning (PP) refers to the process of determining how much production is needed at any given moment. Forecasting demand is one way to do this.
Scheduling is the process of assigning specific dates to tasks so they can be completed within the specified timeframe.
Why is logistics important in manufacturing
Logistics are an essential component of any business. They help you achieve great results by helping you manage all aspects of product flow, from raw materials to finished goods.
Logistics also play a major role in reducing costs and increasing efficiency.
Statistics
- You can multiply the result by 100 to get the total percent of monthly overhead. (investopedia.com)
- Many factories witnessed a 30% increase in output due to the shift to electric motors. (en.wikipedia.org)
- Job #1 is delivering the ordered product according to specifications: color, size, brand, and quantity. (netsuite.com)
- In the United States, for example, manufacturing makes up 15% of the economic output. (twi-global.com)
- (2:04) MTO is a production technique wherein products are customized according to customer specifications, and production only starts after an order is received. (oracle.com)
External Links
How To
How to Use lean manufacturing in the Production of Goods
Lean manufacturing is a management style that aims to increase efficiency and reduce waste through continuous improvement. It was created in Japan by Taiichi Ohno during the 1970s and 80s. He received the Toyota Production System award (TPS), from Kanji Toyoda, founder of TPS. Michael L. Watkins published the original book on lean manufacturing, "The Machine That Changed the World," in 1990.
Lean manufacturing refers to a set of principles that improve the quality, speed and costs of products and services. It emphasizes reducing defects and eliminating waste throughout the value chain. Lean manufacturing is also known as just in time (JIT), zero defect total productive maintenance(TPM), and five-star (S). Lean manufacturing is about eliminating activities that do not add value, such as inspection, rework, and waiting.
Lean manufacturing is a way for companies to achieve their goals faster, improve product quality, and lower costs. Lean manufacturing has been deemed one of the best ways to manage the entire value-chain, including customers, distributors as well retailers and employees. Many industries worldwide use lean manufacturing. For example, Toyota's philosophy underpins its success in automobiles, electronics, appliances, healthcare, chemical engineering, aerospace, paper, food, etc.
Five basic principles of Lean Manufacturing are included in lean manufacturing
-
Define value - Find out what your business contributes to society, and what makes it different from other competitors.
-
Reduce waste - Get rid of any activity that does not add value to the supply chain.
-
Create Flow - Ensure work moves smoothly through the process without interruption.
-
Standardize and Simplify – Make processes as consistent, repeatable, and as simple as possible.
-
Build relationships - Develop and maintain personal relationships with both your internal and external stakeholders.
Lean manufacturing is not a new concept, but it has been gaining popularity over the last few years due to a renewed interest in the economy following the global financial crisis of 2008. Many companies have adopted lean manufacturing methods to increase their marketability. Economists think that lean manufacturing is a crucial factor in economic recovery.
Lean manufacturing is becoming a popular practice in automotive. It has many advantages. These include better customer satisfaction and lower inventory levels. They also result in lower operating costs.
Lean manufacturing can be applied to almost every aspect of an organization. Lean manufacturing is most useful in the production sector of an organisation because it ensures that each step in the value-chain is efficient and productive.
There are three types principally of lean manufacturing:
-
Just-in-Time Manufacturing (JIT): This type of lean manufacturing is commonly referred to as "pull systems." JIT is a process in which components can be assembled at the point they are needed, instead of being made ahead of time. This approach reduces lead time, increases availability and reduces inventory.
-
Zero Defects Manufacturing: ZDM ensures that no defective units leave the manufacturing plant. It is better to repair a part than have it removed from the production line if it needs to be fixed. This is also true for finished products that require minor repairs before shipping.
-
Continuous Improvement (CI: Continuous improvement aims to increase the efficiency of operations by constantly identifying and making improvements to reduce or eliminate waste. It involves continuous improvement of processes, people, and tools.