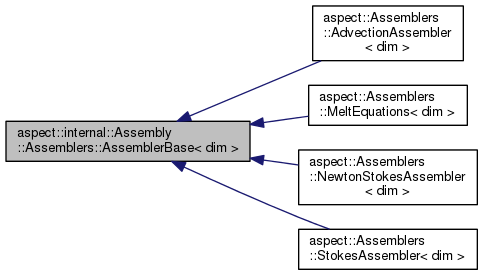
An industrial manager is an engineer who integrates different engineering processes to create an efficient management system. An industrial manager combines these engineering processes to create a single integrated management program. Here are some things you should know about the job. Below are some requirements and benefits for industrial managers. If you are looking for a challenging but rewarding career, this could be the career for your. Continue reading to learn more.
Job description
An industrial manager oversees all aspects of the production process. The job can cover every aspect of the production process but will also be responsible for sourcing raw materials and implementing equipment. Computer literacy is essential for industrial production managers, who must be able to use computers to coordinate the work of different departments, suppliers, clients, and other parties. Industrial production managers should be knowledgeable about the latest management techniques and production technologies. Many managers are members of professional organizations, attend trade shows and conferences, and take courses to get certified in their field.
Industrial managers coordinate activities across a company's departments. They make sure production lines run smoothly and meet customers' time and quality requirements. They may also supervise staffing levels or change production levels as required to minimize inventory. They may coordinate communication with suppliers or other departments, and supervise quality control programs. The majority of their role is to manage people. This includes identifying, training and motivating employees.
Education Required
To be qualified as an industrial manger, you will need a bachelor's degree either in management or business administration. Employers will prefer candidates who have a background in one or more of these fields. Additionally, industrial managers need to be computer literate. Computers are becoming increasingly essential in the manufacturing process. They help coordinate production between departments, suppliers, clients, and other parties. In order to succeed in this field, individuals interested should have the appropriate education and experience.
Many industrial production managers started their careers as production workers before moving up to the first-line supervisory position. All professionals must obtain a college business management degree to reach the industrial manager level. Some entry-level workers might be able to get this education while on the job or through classes sponsored by their employers. However, managers must have two to five year of relevant experience before becoming a manager.
Your potential to earn
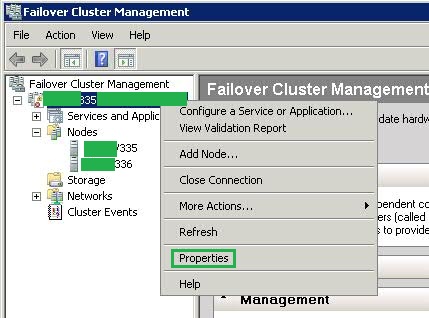
Industrial managers work in manufacturing plants and oversee the smooth operation of the entire process. They are responsible for determining how best to utilize equipment and employees, as well as making strategic decisions. Their duties include hiring and evaluating workers, setting production schedules, and ensuring that safety procedures are followed. They also oversee the day-to-day activities of a team of workers and continuously analyze the entire production process to ensure it is operating efficiently and at peak efficiency.
An industrial production manager's earnings potential is dependent on both the employer and their experience. Although it's impossible to predict the future earnings of industrial producers, the average salary was $103,380 in May 2016, with the highest-paid earning industrial production managers earning $172,000. Higher earnings may also be available for industrial production managers who have completed advanced training or certification. According to the U.S. Bureau of Labor Statistics industrial production managers who have earned a bachelor’s degree or higher could earn more.
Work environment
An industrial production manager splits his or her time between a production floor and an office. Often, the offices are located in the same building. When they work in a production zone, industrial production managers need to adhere to safety and health guidelines and use appropriate protective equipment. They spend a lot of time meeting with their subordinates and analysing production data. These managers may also have the ability to write reports. The work environment of an industrial production manager is dynamic.
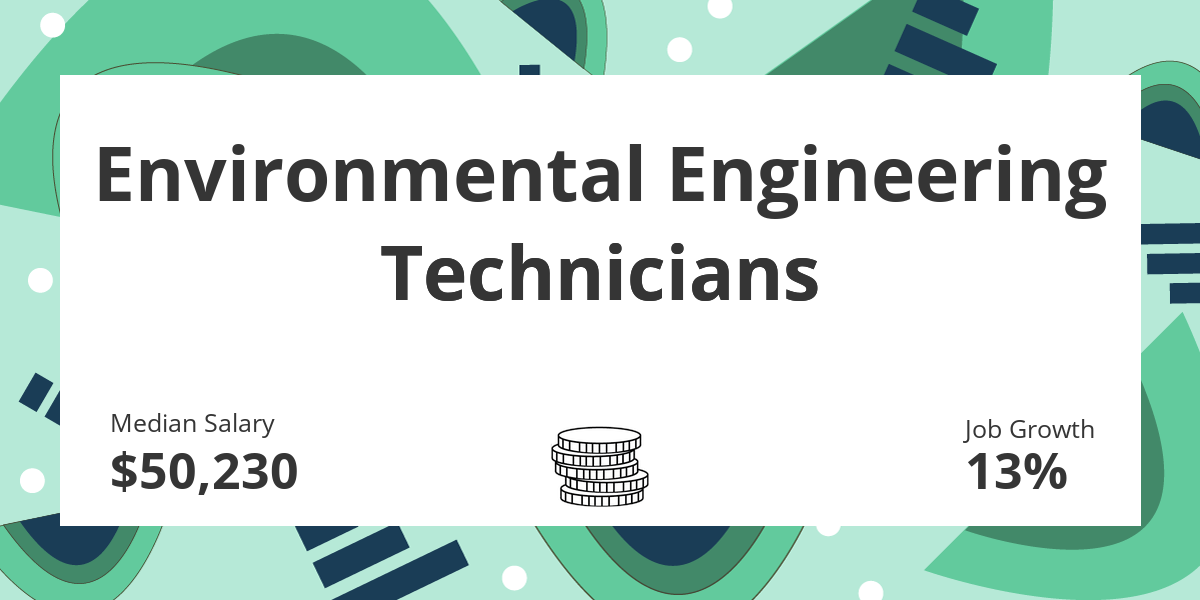
Industrial production managers play a key role in a company's overall management structure. They are responsible for coordinating the activities of workers and increasing productivity. The primary tasks of an industrial producer manager include increasing productivity and maintaining safety. Due to corporate restructuring, many levels have been eliminated and support staff reduced. Production managers are now able to handle more of the work load. This can be a significant challenge for any manager, and can make it difficult to do the job as a production manager.
FAQ
What jobs are available in logistics?
There are many jobs available in logistics. Here are some:
-
Warehouse workers - They load and unload trucks and pallets.
-
Transportation drivers: They drive trucks and trailers and deliver goods and make pick-ups.
-
Freight handlers: They sort and package freight in warehouses.
-
Inventory managers: They are responsible for the inventory and management of warehouses.
-
Sales representatives - They sell products to customers.
-
Logistics coordinators: They plan and manage logistics operations.
-
Purchasing agents – They buy goods or services necessary to run a company.
-
Customer service representatives are available to answer customer calls and emails.
-
Shipping clerks: They process shipping requests and issue bills.
-
Order fillers - These people fill orders based on what has been ordered.
-
Quality control inspectors are responsible for inspecting incoming and outgoing products looking for defects.
-
Other - Logistics has many other job opportunities, including transportation supervisors, logistics specialists, and cargo specialists.
What is the role of a manager in manufacturing?
A manufacturing manager has to ensure that all manufacturing processes work efficiently and effectively. They should be alert for any potential problems in the company and react accordingly.
They should also be able and comfortable communicating with other departments like sales and marketing.
They must also keep up-to-date with the latest trends in their field and be able use this information to improve productivity and efficiency.
Can certain manufacturing steps be automated?
Yes! Since ancient times, automation has been in existence. The Egyptians created the wheel thousands years ago. To help us build assembly lines, we now have robots.
There are many uses of robotics today in manufacturing. These include:
-
Automation line robots
-
Robot welding
-
Robot painting
-
Robotics inspection
-
Robots that create products
Automation can be applied to manufacturing in many other ways. 3D printing, for example, allows us to create custom products without waiting for them to be made.
What are the differences between these four types?
Manufacturing is the process that transforms raw materials into useful products. Manufacturing can include many activities such as designing and building, testing, packaging shipping, selling, servicing, and other related activities.
Statistics
- It's estimated that 10.8% of the U.S. GDP in 2020 was contributed to manufacturing. (investopedia.com)
- According to a Statista study, U.S. businesses spent $1.63 trillion on logistics in 2019, moving goods from origin to end user through various supply chain network segments. (netsuite.com)
- In the United States, for example, manufacturing makes up 15% of the economic output. (twi-global.com)
- (2:04) MTO is a production technique wherein products are customized according to customer specifications, and production only starts after an order is received. (oracle.com)
- According to the United Nations Industrial Development Organization (UNIDO), China is the top manufacturer worldwide by 2019 output, producing 28.7% of the total global manufacturing output, followed by the United States, Japan, Germany, and India.[52][53] (en.wikipedia.org)
External Links
How To
How to Use 5S for Increasing Productivity in Manufacturing
5S stands as "Sort", Set In Order", Standardize", Separate" and "Store". Toyota Motor Corporation invented the 5S strategy in 1954. It improves the work environment and helps companies to achieve greater efficiency.
This method has the basic goal of standardizing production processes to make them repeatable. This means that tasks such as cleaning, sorting, storing, packing, and labeling are performed daily. These actions allow workers to perform their job more efficiently, knowing what to expect.
Implementing 5S requires five steps. These are Sort, Set In Order, Standardize. Separate. And Store. Each step requires a different action, which increases efficiency. Sorting things makes it easier to find them later. Once you have placed items in an ordered fashion, you will put them together. Then, after you separate your inventory into groups, you store those groups in containers that are easy to access. Labeling your containers will ensure that everything is correctly labeled.
Employees need to reflect on how they do their jobs. Employees should understand why they do the tasks they do, and then decide if there are better ways to accomplish them. They will need to develop new skills and techniques in order for the 5S system to be implemented.
The 5S method not only increases efficiency but also boosts morale and teamwork. They feel more motivated to work towards achieving greater efficiency as they see the results.