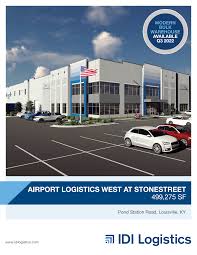
Flow describes the state of being in which all steps of a manufacturing process flow seamlessly without interruption. Every step adds value to the product and goods can flow without being impeded. Many companies plan out the production of a certain quantity of stock to ensure that production orders are fulfilled as efficiently and effectively as possible. This is Lean Manufacturing's "push production". Here are the key elements of flow:
Manufacturing in real-time
When lean manufacturing came to the U.S., it was dominated by "just-in–time" manufacturing. While the concept has its benefits, it is not the most practical way to run a company. It takes many skills and new mindsets to reduce costs and increase efficiency. You will reap the full benefits if it is something you enjoy.
Among the most important aspects of just-in-time manufacturing is standardizing procedures and working with smaller lots. To promote just-in–time thinking, a well-planned layout of the facility is essential. Cellular manufacturing, for instance, can facilitate production flow. Cellular organization of workstations or parts bins can help ensure a smoother flow. And just-in-time manufacturers should avoid long changeover times.
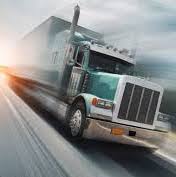
Standardized work
Standardized work is essential in applying lean manufacturing to manufacturing processes. This is the system of work that focuses on the workers and the steps they need to perform in order to produce a product or service. This refers to the ongoing improvement of the system through kaizen. The cell leader is responsible to update standardized work documents as soon as takt time changes. Standardized work documentation can be used as a starting point for improvement activities such as kaizen, and other activities.
Standardized work processes can help organizations improve their productivity and service quality. They also reduce product development times and minimize human error. As people have a better understanding of the process, this helps the organization solve problems faster. This allows the organization to increase customer satisfaction and continuous improvement. It is easy to implement these processes within a company when they are standardized. It is a smart idea to create a mission statement.
Continuous improvement
Lean principles are a way to improve your company's performance. This leads to a number of benefits. Although these benefits are often additive, there is one common thread: higher productivity, lower costs and shorter lead times. Lean continuous improvements are aimed at increasing value creation. But how is continuous improvement possible? This article will give you an overview of some common benefits of continuous improvement. It's simple: Continuous Improvement helps companies save money.
Continuous improvement focuses on small, incremental improvements and not large-scale changes. Although individual improvements are small and seem insignificant, the total improvement is substantial. The slow process of improvement is not about making big leaps. In a lean manufacturing environment, continuous improvement focuses on alignment of goals, allowing the business to maximize productivity and profitability. Continuous improvement methods can streamline production and make it easier for all involved to reach a common goal.
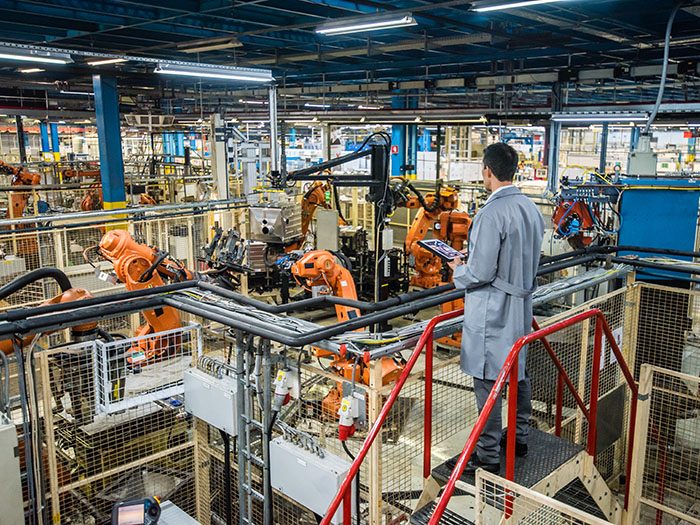
Kaizen
Kaizen in lean manufacturing focuses on waste elimination. In some cases, it is used to improve production yield, decrease lead time, and improve quality. A team of employees is assigned a specific role to study the problem and propose solutions. A kaizen activity usually starts with the creation a process value stream map. Then, the team conducts time studies of relevant operations. The process continues until each step is improved, and the overall process becomes more efficient.
One example: A manufacturing plant may choose to buy a new forklift after identifying inefficiencies. The operator might move inventory around to speed up loading and unloading. Similarly, the value stream is a map of processes that create products and services. Five S's were used to increase workplace productivity and employee productivity during the mapping process. There are seven types. Each type focuses on a different aspect or part of the manufacturing process.
FAQ
What's the difference between Production Planning & Scheduling?
Production Planning (PP), is the process of deciding what production needs to take place at any given time. This is accomplished by forecasting the demand and identifying production resources.
Scheduling involves the assignment of dates and times to tasks in order to complete them within the timeframe.
What are the jobs in logistics?
There are many kinds of jobs available within logistics. Here are some examples:
-
Warehouse workers: They load and unload trucks, pallets, and other cargo.
-
Transportation drivers - They drive trucks and trailers to deliver goods and carry out pick-ups.
-
Freight handlers, - They sort out and pack freight in warehouses.
-
Inventory managers – They manage the inventory in warehouses.
-
Sales reps - They sell products and services to customers.
-
Logistics coordinators: They plan and manage logistics operations.
-
Purchasing agents - They purchase goods and services needed for company operations.
-
Customer service representatives – They answer emails and phone calls from customers.
-
Shipping clerks - They process shipping orders and issue bills.
-
Order fillers are people who fill orders based only on what was ordered.
-
Quality control inspectors (QCI) - They inspect all incoming and departing products for potential defects.
-
Others - There is a variety of other jobs in logistics. These include transportation supervisors and cargo specialists.
What skills are required to be a production manager?
You must be flexible and organized to become a productive production planner. Communication skills are essential to ensure that you can communicate effectively with clients, colleagues, and customers.
Statistics
- It's estimated that 10.8% of the U.S. GDP in 2020 was contributed to manufacturing. (investopedia.com)
- You can multiply the result by 100 to get the total percent of monthly overhead. (investopedia.com)
- (2:04) MTO is a production technique wherein products are customized according to customer specifications, and production only starts after an order is received. (oracle.com)
- According to a Statista study, U.S. businesses spent $1.63 trillion on logistics in 2019, moving goods from origin to end user through various supply chain network segments. (netsuite.com)
- According to the United Nations Industrial Development Organization (UNIDO), China is the top manufacturer worldwide by 2019 output, producing 28.7% of the total global manufacturing output, followed by the United States, Japan, Germany, and India.[52][53] (en.wikipedia.org)
External Links
How To
How to Use Lean Manufacturing for the Production of Goods
Lean manufacturing is an approach to management that aims for efficiency and waste reduction. It was developed by Taiichi Okono in Japan, during the 1970s & 1980s. TPS founder Kanji Takoda awarded him the Toyota Production System Award (TPS). Michael L. Watkins published the first book on lean manufacturing in 1990.
Lean manufacturing is often described as a set if principles that help improve the quality and speed of products and services. It emphasizes the elimination and minimization of waste in the value stream. Just-in-time (JIT), zero defect (TPM), and 5S are all examples of lean manufacturing. Lean manufacturing focuses on eliminating non-value-added activities such as rework, inspection, and waiting.
In addition to improving product quality and reducing costs, lean manufacturing helps companies achieve their goals faster and reduces employee turnover. Lean manufacturing has been deemed one of the best ways to manage the entire value-chain, including customers, distributors as well retailers and employees. Lean manufacturing practices are widespread in many industries. Toyota's philosophy has been a key driver of success in many industries, including automobiles and electronics.
Five fundamental principles underlie lean manufacturing.
-
Define Value - Determine the value that your business brings to society. Also, identify what sets you apart from your competitors.
-
Reduce waste - Stop any activity that isn't adding value to the supply chains.
-
Create Flow: Ensure that the work process flows without interruptions.
-
Standardize & Simplify - Make processes as consistent and repeatable as possible.
-
Build Relationships- Develop personal relationships with both internal as well as external stakeholders.
Lean manufacturing is not a new concept, but it has been gaining popularity over the last few years due to a renewed interest in the economy following the global financial crisis of 2008. Many businesses are now using lean manufacturing to improve their competitiveness. In fact, some economists believe that lean manufacturing will be an important factor in economic recovery.
With many benefits, lean manufacturing is becoming more common in the automotive industry. These include better customer satisfaction and lower inventory levels. They also result in lower operating costs.
The principles of lean manufacturing can be applied in almost any area of an organization. This is because it ensures efficiency and effectiveness in all stages of the value chain.
There are three types of lean manufacturing.
-
Just-in Time Manufacturing (JIT), also known as "pull system": This form of lean manufacturing is often referred to simply as "pull". JIT is a method in which components are assembled right at the moment of use, rather than being manufactured ahead of time. This strategy aims to decrease lead times, increase availability of parts and reduce inventory.
-
Zero Defects Manufacturing, (ZDM): ZDM is focused on ensuring that no defective products leave the manufacturing facility. You should repair any part that needs to be repaired during an assembly line. This applies to finished products, which may need minor repairs before they are shipped.
-
Continuous Improvement (CI),: Continuous improvement aims improve the efficiency and effectiveness of operations by continuously identifying issues and making changes to reduce waste. It involves continuous improvement of processes, people, and tools.