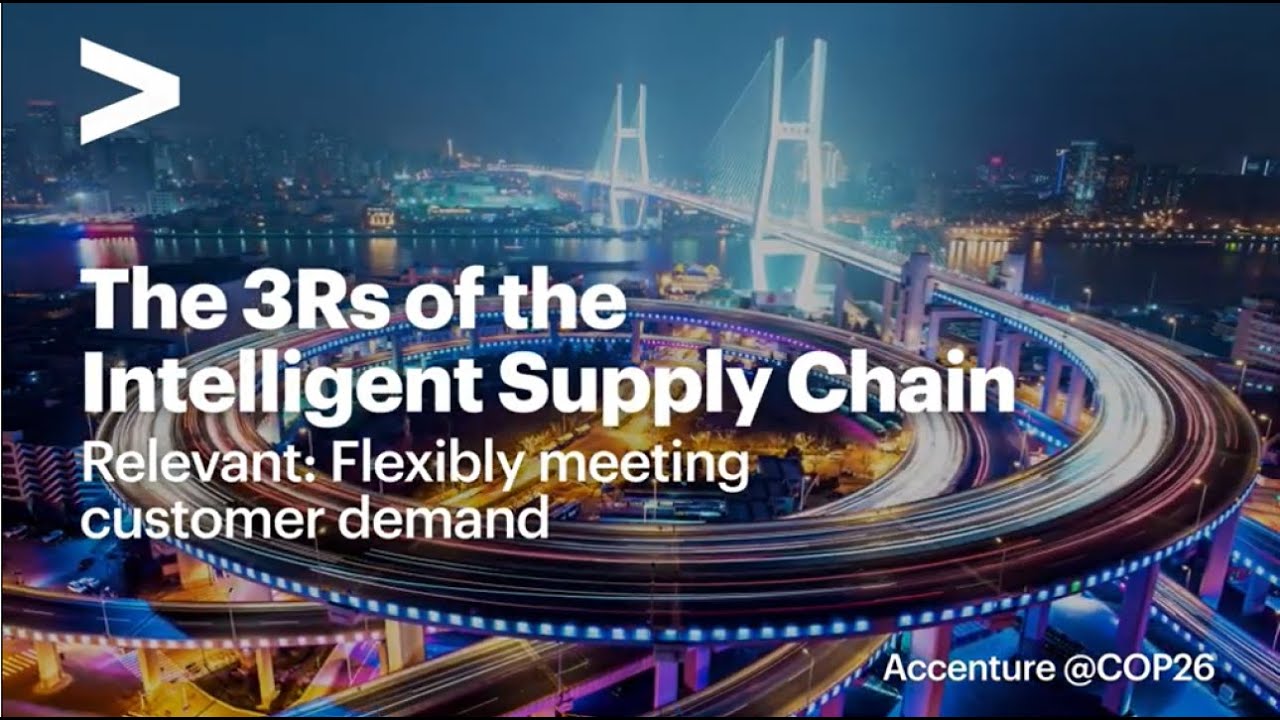
Companies can use lean product development methods to ensure products that are best suited for their customers' needs. They reduce waste and speed up product creation, while ensuring that products meet customer demands. Companies can remain competitive through the use of lean processes.
Lean product engineering is an approach to combining engineering and manufacturing. Its purpose is build a functioning product with less stock, effort and time. It includes rapid learning cycles and uses visual planning techniques such as visual boards. It also incorporates set-based concurrent Engineering.
Understanding the customer is key to lean product development. This begins with understanding the customer. It is important that you understand the product's functionality and features. These features are usually extra and wasteful, if the customer doesn't need them. It includes the creation and implementation of a validation and verification plan.
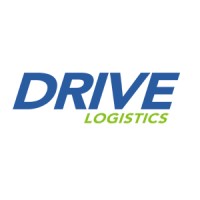
Next, we need to build an activity network. This allows teams to plan and decide their work. The network offers a framework to help develop value. It reduces waste and assists teams in finding ways to improve their processes.
The ideal PD process focuses on a continuous flow of value from conception to production. It should be free of bureaucratic repercussions and loopbacks that correct errors. It should be able to represent the entire value stream. The system must not fail and cause systemic vision loss. This should be a one-piece flow in manufacturing.
First, determine the value. This is accomplished by reviewing the literature and analysing the business case. It is crucial to establish the value expectations for all stakeholders. It is important to define the product scope. This includes customer value as well as the features and functions. These elements will determine the technology and the process.
Next, design the value stream. This involves removing steps from the value stream that do not add value. Unused designs and untested code should be removed. It is important that there are fewer tasks being completed at once. This is typically done through frequent changes of priorities.
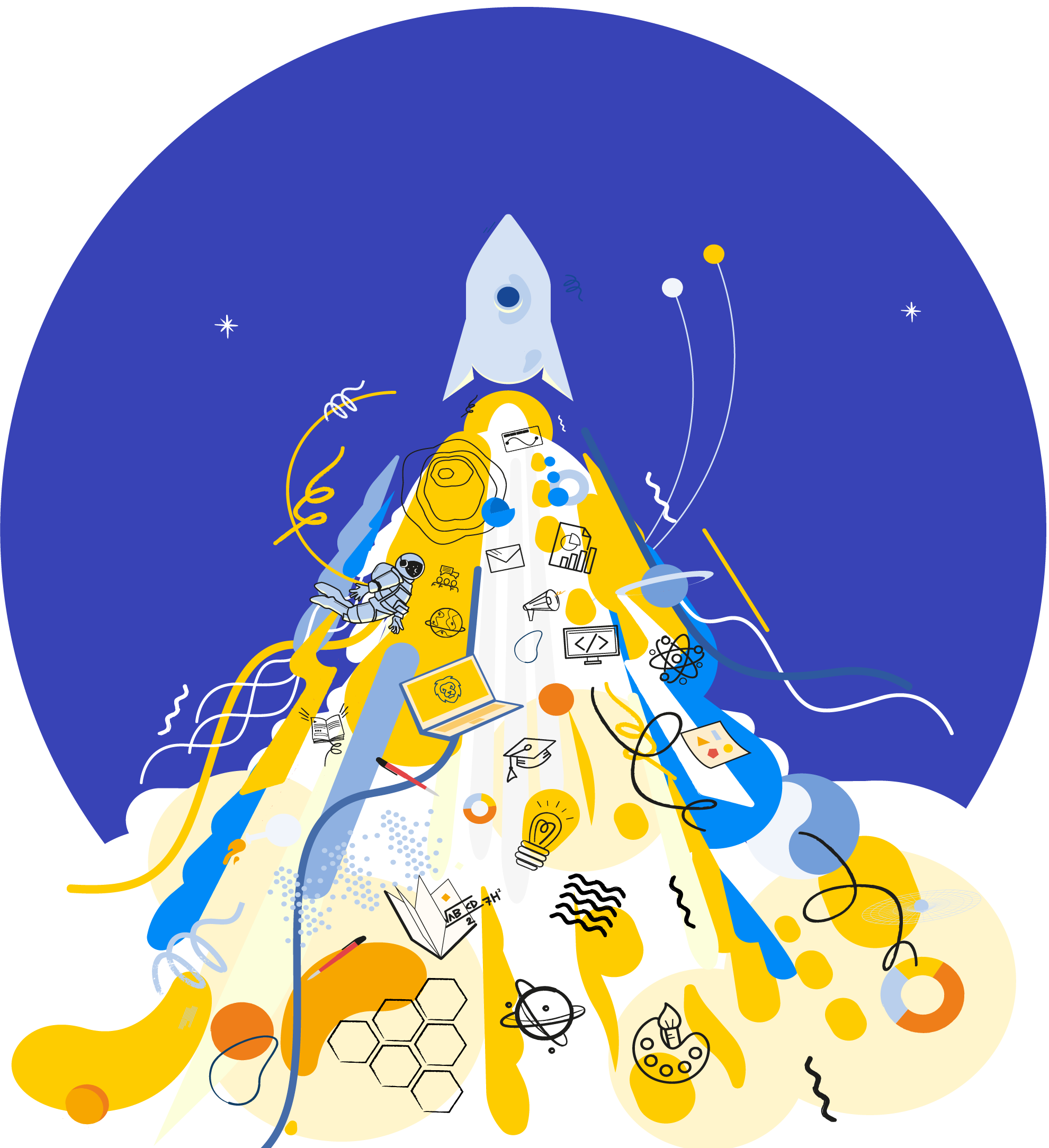
Lean product creation is a highly valuable tool that can help businesses reduce their costs, find inefficiencies in their processes and remain competitive. Lean product development allows companies to create sustainable value streams that will allow them to be profitable in the future. It has helped companies from all industries, including healthcare, high-tech and manufacturing.
Lean product engineering uses a set based concurrent engineering approach which allows teams and individuals to develop products with fewer resources. Because of their complicated codebases, it took big companies longer to develop new products in the past than start-ups. This can be difficult to maintain and build upon.
FAQ
Is automation important in manufacturing?
Not only is automation important for manufacturers, but it's also vital for service providers. It allows them provide faster and more efficient services. They can also reduce their costs by reducing human error and improving productivity.
What is the job of a production plan?
A production planner ensures all aspects of the project are delivered on time, within budget, and within scope. They ensure that the product or service is of high quality and meets client requirements.
Are there ways to automate parts of manufacturing?
Yes! Automation has been around since ancient times. The Egyptians invented the wheel thousands of years ago. Robots are now used to assist us in assembly lines.
In fact, there are several applications of robotics in manufacturing today. They include:
-
Assembly line robots
-
Robot welding
-
Robot painting
-
Robotics inspection
-
Robots create products
There are many other examples of how manufacturing could benefit from automation. 3D printing makes it possible to produce custom products in a matter of days or weeks.
Why automate your warehouse
Modern warehouses have become more dependent on automation. E-commerce has brought increased demand for more efficient and quicker delivery times.
Warehouses should be able adapt quickly to new needs. In order to do this, they need to invest in technology. Automating warehouses is a great way to save money. These are just a few reasons to invest in automation.
-
Increases throughput/productivity
-
Reduces errors
-
Increases accuracy
-
Boosts safety
-
Eliminates bottlenecks
-
This allows companies to scale easily
-
Workers are more productive
-
Gives you visibility into all that is happening in your warehouse
-
Enhances customer experience
-
Improves employee satisfaction
-
This reduces downtime while increasing uptime
-
Quality products delivered on time
-
Removes human error
-
It ensures compliance with regulations
What is it like to manage a logistics company?
You need to have a lot of knowledge and skills to manage a successful logistic business. You must have good communication skills to interact effectively with your clients and suppliers. You must be able analyze data and draw out conclusions. You must be able and able to handle stress situations and work under pressure. You need to be innovative and creative to come up with new ways to increase efficiency. To motivate and guide your team towards reaching organizational goals, you must have strong leadership skills.
It is important to be organized and efficient in order to meet tight deadlines.
What is the role of a manager in manufacturing?
A manufacturing manager has to ensure that all manufacturing processes work efficiently and effectively. They should also be aware and responsive to any company problems.
They should also be able and comfortable communicating with other departments like sales and marketing.
They should also be aware of the latest trends in their industry and be able to use this information to help improve productivity and efficiency.
Statistics
- Many factories witnessed a 30% increase in output due to the shift to electric motors. (en.wikipedia.org)
- In 2021, an estimated 12.1 million Americans work in the manufacturing sector.6 (investopedia.com)
- According to the United Nations Industrial Development Organization (UNIDO), China is the top manufacturer worldwide by 2019 output, producing 28.7% of the total global manufacturing output, followed by the United States, Japan, Germany, and India.[52][53] (en.wikipedia.org)
- In the United States, for example, manufacturing makes up 15% of the economic output. (twi-global.com)
- It's estimated that 10.8% of the U.S. GDP in 2020 was contributed to manufacturing. (investopedia.com)
External Links
How To
Six Sigma in Manufacturing:
Six Sigma is defined as "the application of statistical process control (SPC) techniques to achieve continuous improvement." It was developed by Motorola's Quality Improvement Department at their plant in Tokyo, Japan, in 1986. Six Sigma's core idea is to improve the quality of processes by standardizing and eliminating defects. Many companies have adopted Six Sigma in recent years because they believe that there are no perfect products and services. Six Sigma aims to reduce variation in the production's mean value. You can calculate the percentage of deviation from the norm by taking a sample of your product and comparing it to the average. If it is too large, it means that there are problems.
Understanding the nature of variability in your business is the first step to Six Sigma. Once you understand this, you can then identify the causes of variation. It is important to identify whether the variations are random or systemic. Random variations are caused when people make mistakes. While systematic variations are caused outside of the process, they can occur. Random variations would include, for example, the failure of some widgets to fall from the assembly line. It would be considered a systematic problem if every widget that you build falls apart at the same location each time.
Once you identify the problem areas, it is time to create solutions. It might mean changing the way you do business or redesigning it entirely. After implementing the new changes, you should test them again to see if they worked. If they don’t work, you’ll need to go back and rework the plan.