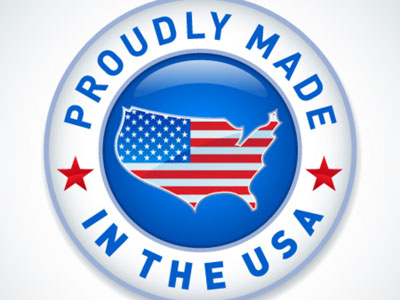
Andon is a visual indicator that draws attention to a problem in order to fix it permanently. It's a tool to empower plant floor operators, and speed up teamwork.
Andon
( ) – a Japanese term, it is derived from the paper-enclosed fixed lanterns that were used during the Edo period between the 17th Century and the 19th Century. In Japanese, it also refers to a system of tying light signals or sounds to a specific process issue in order to alert operators and management.
Toyota uses the term "build-in" quality as a core principle of its Jidoka. It is a component in their TPS system (Toyota Production System). In the US this term is frequently cited as a key principle for their Jidoka, or build-in quality. This is an important component of the TPS (Toyota Production System).
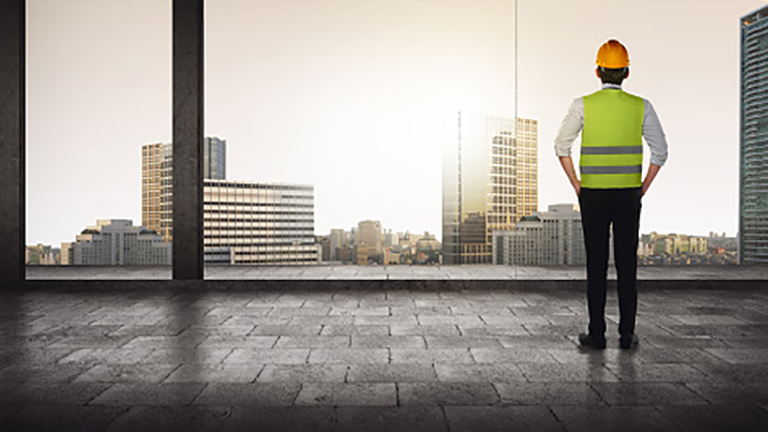
What is anon?
Toyota invented the Andon system, a lean production method. It is a simple, straightforward system consisting of a board that has green, red and yellow lights. Each color indicates the different status of production. The production line runs normally when the green light is on. The yellow light means that the problem has been identified and is being dealt with. When the red lights are on, production stops. The workers can take a pause, prepare parts, get help, or simply fill their bins.
Andon is very easy to use. Supervisors can understand immediately what happened. The system was designed to give immediate feedback, ensuring that all problems are solved as quickly as possible.
There are many types of andons, but most common is a red light with a sound or buzzer to alert production teams. These signal alert and resolve systems help identify problems that might lead to downtime, or repeat issues.
An effective andon board can help to keep the production running in case of a malfunction. This simple tool increases productivity, decreases downtime and improves safety and product quality.
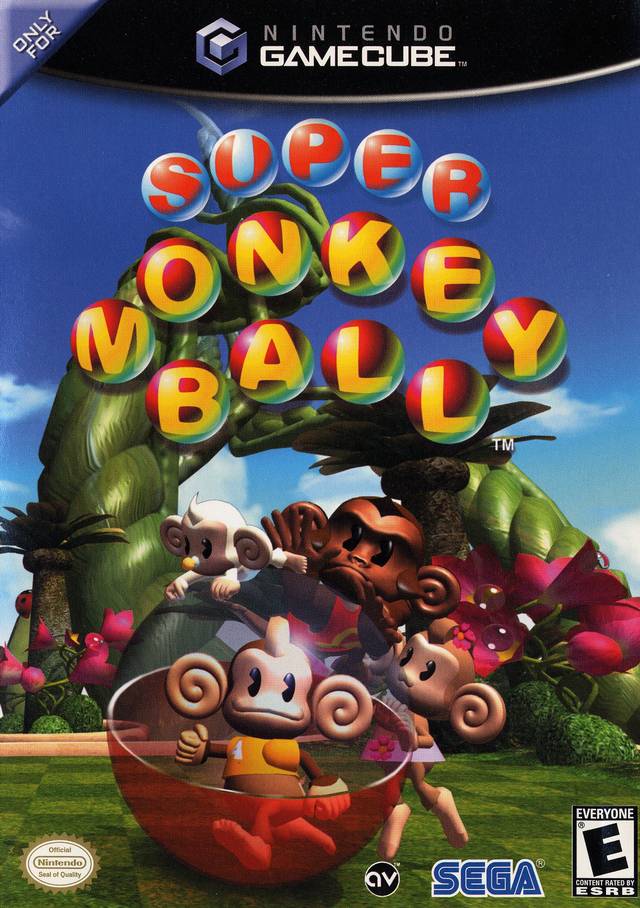
What is andon toyota?
Toyota had a cord that employees could pull on the production floor if they suspected a problem with a car. The cord was used by workers to stop production if they thought the car's integrity had been compromised.
Modern andon uses technology to deliver curated information to make it easier to identify problems as they arise, to send real-time notifications to all stakeholders, and to pinpoint the root causes that need a permanent fix. Nevertheless, a human touch is required to interpret and act on this information.
How to make the andon system work?
Creating a culture of openness and honesty among workers and supervisors is essential. The more reluctant they are, they are more likely not to address problems or hide them. To improve this, you can tie line stops with problem resolution so that workers will be more likely to push the button or pull the cord when something is wrong.
FAQ
Why is logistics important for manufacturing?
Logistics is an integral part of every business. They can help you achieve great success by helping you manage product flow from raw material to finished goods.
Logistics are also important in reducing costs and improving efficiency.
What is the difference between Production Planning, Scheduling and Production Planning?
Production Planning (PP), is the process of deciding what production needs to take place at any given time. Forecasting and identifying production capacity are two key elements to this process.
Scheduling is the process that assigns dates to tasks so they can get completed within a given timeframe.
What are manufacturing and logistic?
Manufacturing refers the process of producing goods from raw materials through machines and processes. Logistics covers all aspects involved in managing supply chains, including procurement and production planning. Manufacturing and logistics can often be grouped together to describe a larger term that covers both the creation of products, and the delivery of them to customers.
What are the 7 Rs of logistics.
The acronym "7R's" of Logistics stands for seven principles that underpin logistics management. It was published in 2004 by the International Association of Business Logisticians as part of their "Seven Principles of Logistics Management" series.
The acronym consists of the following letters:
-
Responsible – ensure that all actions are legal and don't cause harm to anyone else.
-
Reliable – have faith in your ability and capability to keep promises.
-
Reasonable - make sure you use your resources well and don't waste them.
-
Realistic - Consider all aspects of operations, including environmental impact and cost effectiveness.
-
Respectful - show respect and treat others fairly and fairly
-
Reliable - Find ways to save money and increase your productivity.
-
Recognizable: Provide customers with value-added service
How does manufacturing avoid bottlenecks in production?
To avoid production bottlenecks, ensure that all processes run smoothly from the moment you receive your order to the time the product ships.
This includes both quality control and capacity planning.
Continuous improvement techniques such Six Sigma are the best method to accomplish this.
Six Sigma management is a system that improves quality and reduces waste within your organization.
It is focused on creating consistency and eliminating variation in your work.
What does it take to run a logistics business?
To run a successful logistics company, you need a lot knowledge and skills. Good communication skills are essential to effectively communicate with your suppliers and clients. It is important to be able to analyse data and draw conclusions. You must be able manage stress and pressure under pressure. In order to innovate and create new ways to improve efficiency, creativity is essential. Strong leadership qualities are essential to motivate your team and help them achieve their organizational goals.
You should also be organized and efficient to meet tight deadlines.
Statistics
- According to a Statista study, U.S. businesses spent $1.63 trillion on logistics in 2019, moving goods from origin to end user through various supply chain network segments. (netsuite.com)
- According to the United Nations Industrial Development Organization (UNIDO), China is the top manufacturer worldwide by 2019 output, producing 28.7% of the total global manufacturing output, followed by the United States, Japan, Germany, and India.[52][53] (en.wikipedia.org)
- Many factories witnessed a 30% increase in output due to the shift to electric motors. (en.wikipedia.org)
- It's estimated that 10.8% of the U.S. GDP in 2020 was contributed to manufacturing. (investopedia.com)
- (2:04) MTO is a production technique wherein products are customized according to customer specifications, and production only starts after an order is received. (oracle.com)
External Links
How To
Six Sigma in Manufacturing:
Six Sigma can be described as "the use of statistical process control (SPC), techniques to achieve continuous improvement." Motorola's Quality Improvement Department created Six Sigma at their Tokyo plant, Japan in 1986. The basic idea behind Six Sigma is to improve quality by improving processes through standardization and eliminating defects. Many companies have adopted Six Sigma in recent years because they believe that there are no perfect products and services. Six Sigma aims to reduce variation in the production's mean value. It is possible to measure the performance of your product against an average and find the percentage of time that it differs from the norm. If there is a significant deviation from the norm, you will know that something needs to change.
Understanding how your business' variability is a key step towards Six Sigma implementation is the first. Once you have this understanding, you will need to identify sources and causes of variation. This will allow you to decide if these variations are random and systematic. Random variations are caused by human errors. Systematic variations can be caused by outside factors. If you make widgets and some of them end up on the assembly line, then those are considered random variations. If however, you notice that each time you assemble a widget it falls apart in exactly the same spot, that is a problem.
Once you've identified the problem areas you need to find solutions. The solution could involve changing how you do things, or redesigning your entire process. To verify that the changes have worked, you need to test them again. If they don’t work, you’ll need to go back and rework the plan.