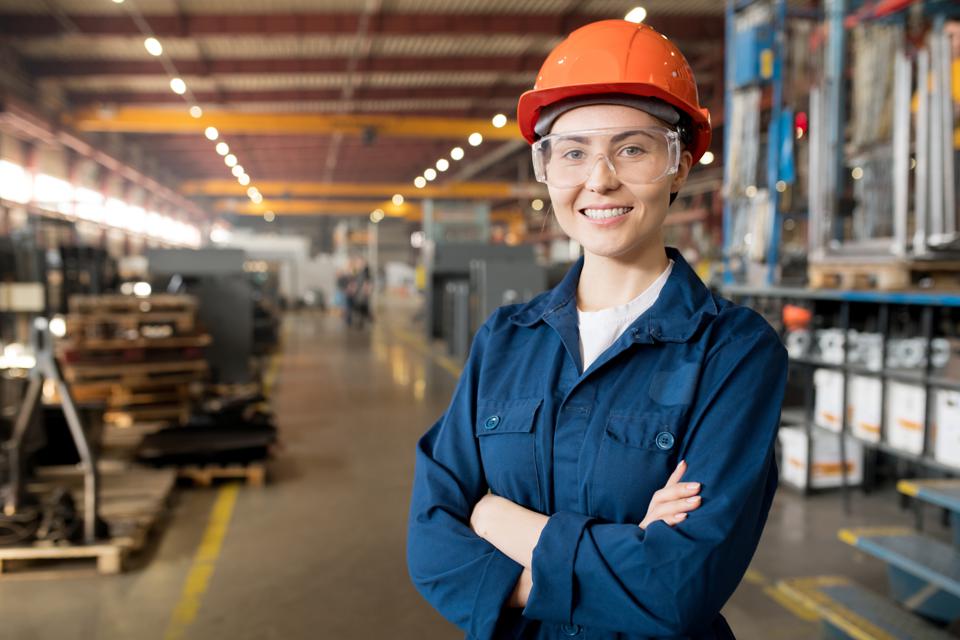
Robotics Suppliers and manufacturers employ robotics technicians. They are responsible in maintaining and repairing the equipment used to create and operate robotics systems. A degree is required as well as practical experience. A robotics technician salary can vary considerably depending on the level of education and experience.
Technicians in robotics typically have an associate's or bachelor's degree in a related field. This could be in electronics, mathematics or mechanical engineering. The degree provides students with a strong background in science and mathematics as well as computer programming. A robotics technician can work alongside a team made up of robotics professionals to develop, test and maintain robot systems after completing the program.
These systems are used in virtually every area of our lives. Robots can be found in many industries. They are used for material handling, transportation, the defense department, and the medical field. In the military, a robot can collect information, such as land mines, for troops. Mechatronics is an engineering discipline that combines electrical, mechanical, and computer engineering.
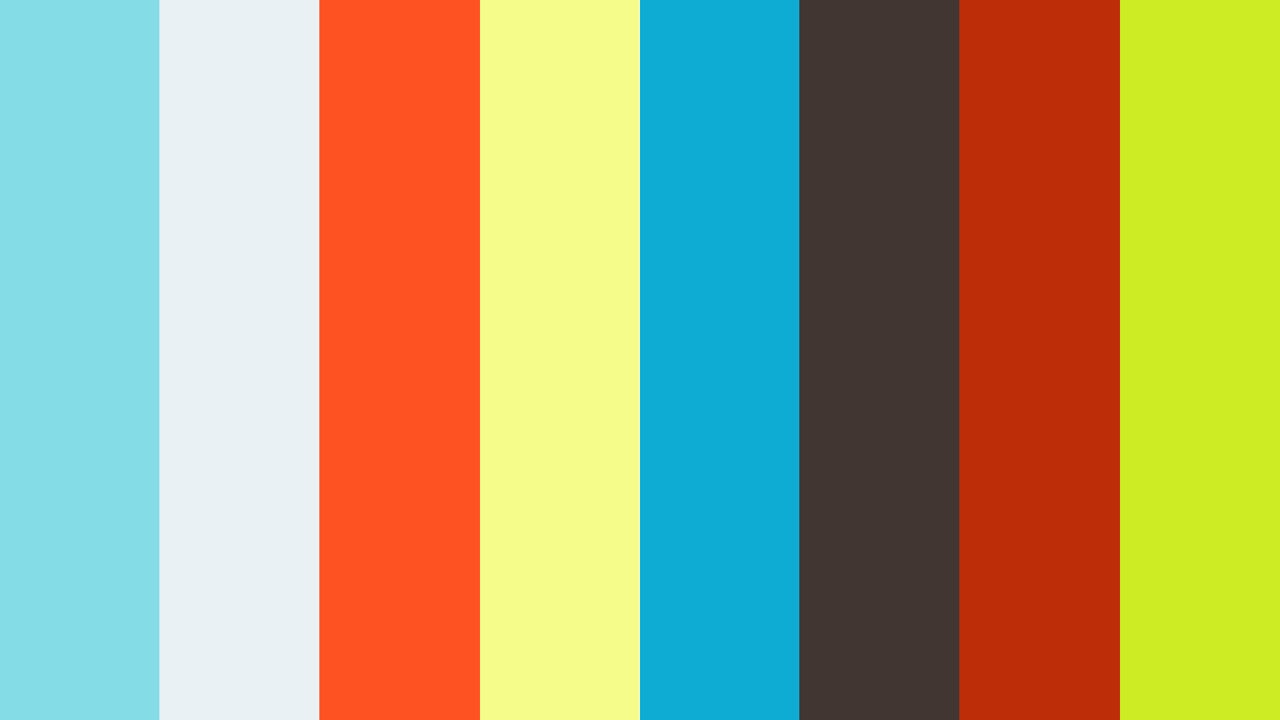
There are many colleges and universities in the United States that offer robotics technician programs. You can also apply directly for jobs with robotics technicians at companies. You must have a passion for problem-solving, as well as a knack for math and science to be a successful robot operator. However, employers will also generally require applicants to have a high school diploma.
Although the robotics technician's salary is not particularly large, the profession does require a considerable degree of education. Most robotics technicians obtain a two-year associate's degree in robot technology. Additional training is possible as part of the job. However, the employer will usually provide some on the-job training.
Robotics technicians will work shifts, depending on what industry they are working in. Robotics operators are responsible for programming robots in order to complete specific tasks. If the robot is not working properly, the operator must find the source of the problem and fix it. Operators will be required to work nights or weekends.
Robotics technicians are usually paid between $44,175 up to $84,520. Atlanta, GA is the ideal place for Robotics Technicians. This is due to its high quality of living. Robotics Technicians in Atlanta earn $1,841 a paycheck.
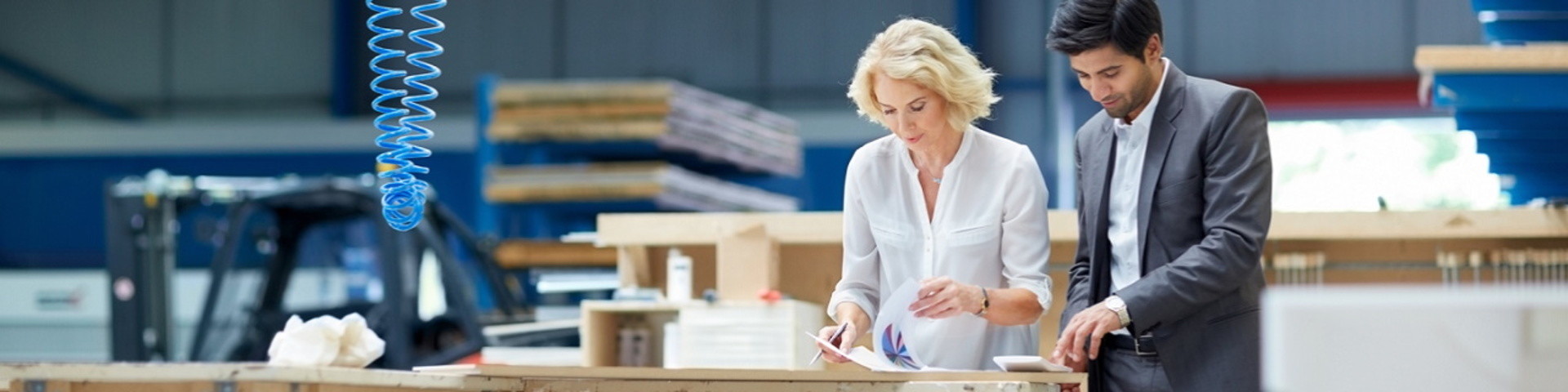
Atlanta's state tax rate is lower for robotics technicians. In Georgia, robotics technicians pay 6% in taxes in 2018. That is higher than the national average. Atlanta is an affordable city, so it's a great place to live.
Robotics technicians can be a great fit for people who want a positive impact on the global community. Robotics technicians can earn high salaries as they are experts in their field. They can be employed as either a maintenance technician, or a robot operator.
FAQ
What are manufacturing and logistics?
Manufacturing is the process of creating goods from raw materials by using machines and processes. Logistics includes all aspects related to supply chain management, such as procurement, distribution planning, inventory control and transportation. Logistics and manufacturing are often referred to as one thing. It encompasses both the creation of products and their delivery to customers.
What skills do production planners need?
You must be flexible and organized to become a productive production planner. Also, you must be able and willing to communicate with clients and coworkers.
What's the difference between Production Planning & Scheduling?
Production Planning (PP), or production planning, is the process by which you determine what products are needed at any given time. Forecasting demand is one way to do this.
Scheduling refers the process by which tasks are assigned dates so that they can all be completed within the given timeframe.
Why automate your factory?
Modern warehouses are increasingly dependent on automation. E-commerce has increased the demand for quicker delivery times and more efficient processes.
Warehouses need to adapt quickly to meet changing needs. Technology investment is necessary to enable warehouses to respond quickly to changing demands. Automation of warehouses offers many benefits. These are just a few reasons to invest in automation.
-
Increases throughput/productivity
-
Reduces errors
-
Increases accuracy
-
Safety Boosts
-
Eliminates bottlenecks
-
Companies can scale up more easily
-
Makes workers more efficient
-
It gives visibility to everything that happens inside the warehouse
-
Enhances customer experience
-
Improves employee satisfaction
-
This reduces downtime while increasing uptime
-
Ensures quality products are delivered on time
-
Eliminates human error
-
Assure compliance with regulations
Statistics
- According to the United Nations Industrial Development Organization (UNIDO), China is the top manufacturer worldwide by 2019 output, producing 28.7% of the total global manufacturing output, followed by the United States, Japan, Germany, and India.[52][53] (en.wikipedia.org)
- Many factories witnessed a 30% increase in output due to the shift to electric motors. (en.wikipedia.org)
- [54][55] These are the top 50 countries by the total value of manufacturing output in US dollars for its noted year according to World Bank.[56] (en.wikipedia.org)
- In the United States, for example, manufacturing makes up 15% of the economic output. (twi-global.com)
- It's estimated that 10.8% of the U.S. GDP in 2020 was contributed to manufacturing. (investopedia.com)
External Links
How To
How to use 5S in Manufacturing to Increase Productivity
5S stands for "Sort", "Set In Order", "Standardize", "Separate" and "Store". Toyota Motor Corporation invented the 5S strategy in 1954. This methodology helps companies improve their work environment to increase efficiency.
This method has the basic goal of standardizing production processes to make them repeatable. It means tasks like cleaning, sorting or packing, labeling, and storing are done every day. These actions allow workers to perform their job more efficiently, knowing what to expect.
Implementing 5S involves five steps: Sort, Set in Order, Standardize Separate, Store, and Each step has a different action and leads to higher efficiency. You can make it easy for people to find things later by sorting them. When items are ordered, they are put together. Once you have separated your inventory into groups and organized them, you will store these groups in easily accessible containers. Labeling your containers will ensure that everything is correctly labeled.
Employees will need to be more critical about their work. Employees should understand why they do the tasks they do, and then decide if there are better ways to accomplish them. They will need to develop new skills and techniques in order for the 5S system to be implemented.
In addition to increasing efficiency, the 5S method also improves morale and teamwork among employees. As they begin to see improvements, they feel motivated to continue working towards the goal of achieving higher levels of efficiency.