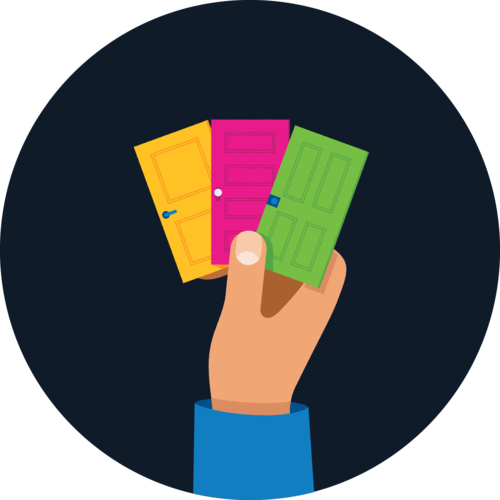
Cybersecurity is crucial for manufacturers as the Internet of Things (IoT), transforms the manufacturing sector. Companies must ensure that their customer information and assets are protected in light of the increasing number of cyberattacks. The right technology can be used to help companies protect themselves and respond to potential threats. Industrial equipment can be protected with a physical security system that includes cameras, locks, and access cards.
Kaspersky Labs reports that one third of all cybersecurity incidents target manufacturers. These threats are increasingly complex and widespread. These threats include ransomware, phishing attacks and malware. Manufacturers should protect their intellectual property and designs. It's important to devise a strategy that reduces the risk of cyberattacks.
Cybersecurity for manufacturers is critical for protecting sensitive data and information like customer orders, product specifications, design blueprints, and other details. Cybersecurity plans should include a plan for how to deal with a cyberattack, which can be as costly as $3 million to $6 million. Companies are vulnerable to theft and data breaches as well disruption of production lines. Many manufacturers face challenges in keeping up with cyberattacks.
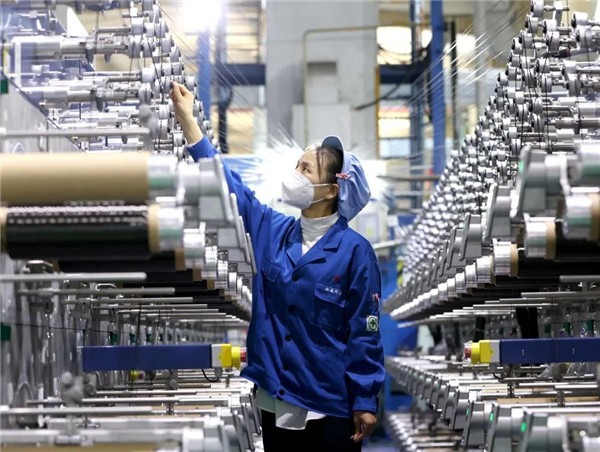
Protecting employee and customer information is critical to protecting your company's reputation, revenue and image. You must conduct an audit of your system to determine vulnerabilities and your overall readiness to ensure your cybersecurity plan succeeds.
Contact your local Manufacturing Executive Program (MEP), if you are ready to get started. Expert advice will be provided on how to protect your business from cyberattacks.
Aside from performing an audit of the systems, it is important to establish a backup plan. It's also crucial to test your system regularly to ensure it works as intended. Reduce the possibility of being attacked by creating hard copies key documents and setting up a process for testing your system's effectiveness.
Many manufacturers don't have cybersecurity measures in place, including data standards. Nearly half the OEMs are using obsolete or noncompliant hardware, software, processes, and software. But, companies are increasingly investing in digital technology. Digital technologies like cloud computing, sensor networks, and machine learning are changing the industry. Although the Internet of Things, (IoT), and increasing globalization have created new concerns, a cybersecurity strategy will ensure that your business is protected.
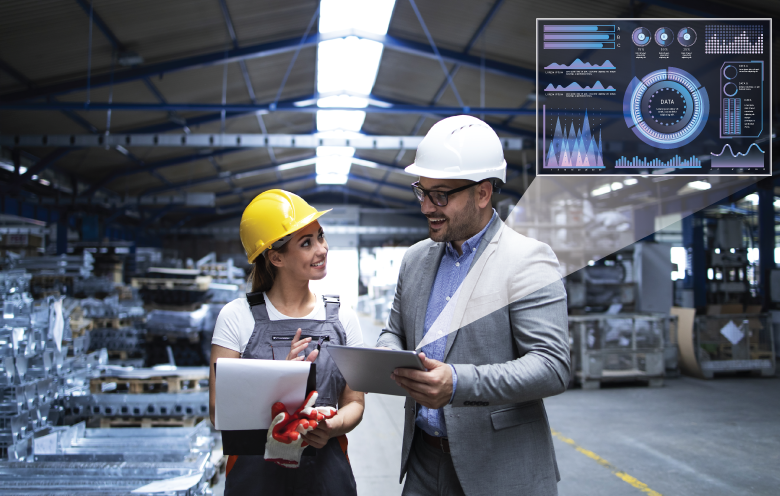
It is important to fully understand the requirements of different manufacturing industries when developing a cybersecurity strategy. For example, international manufacturers with long supply chain must follow standards based on their country, region, or partner. However, smaller or medium-sized companies often have more stringent cybersecurity policy. Regardless of your size, you should invest in a comprehensive strategy to safeguard your business from cyberattacks.
Cybersecurity Framework for Manufacturers by the National Institute of Standards and Technology, (NIST), is a resource designed to help manufacturers protect themselves from cyberattacks. This framework provides a plan for managing cybersecurity activities within a variety sectors, including industrial manufacture.
FAQ
Is automation necessary in manufacturing?
Automation is essential for both manufacturers and service providers. It allows them to offer services faster and more efficiently. They can also reduce their costs by reducing human error and improving productivity.
Why is logistics so important in manufacturing?
Logistics are an essential part of any business. They can help you achieve great success by helping you manage product flow from raw material to finished goods.
Logistics play an important role in reducing costs as well as increasing efficiency.
What are the 7 Rs of logistics?
The acronym "7R's" of Logistics stands for seven principles that underpin logistics management. It was created by the International Association of Business Logisticians and published in 2004 under its "Seven Principles of Logistics Management".
The acronym is made up of the following letters:
-
Responsible – ensure that all actions are legal and don't cause harm to anyone else.
-
Reliable - Have confidence in your ability to fulfill all of your commitments.
-
Use resources effectively and sparingly.
-
Realistic - Take into consideration all aspects of operations including cost-effectiveness, environmental impact, and other factors.
-
Respectful - treat people fairly and equitably.
-
Resourceful - look for opportunities to save money and increase productivity.
-
Recognizable - Provide value-added services to customers
Statistics
- Many factories witnessed a 30% increase in output due to the shift to electric motors. (en.wikipedia.org)
- You can multiply the result by 100 to get the total percent of monthly overhead. (investopedia.com)
- According to a Statista study, U.S. businesses spent $1.63 trillion on logistics in 2019, moving goods from origin to end user through various supply chain network segments. (netsuite.com)
- It's estimated that 10.8% of the U.S. GDP in 2020 was contributed to manufacturing. (investopedia.com)
- [54][55] These are the top 50 countries by the total value of manufacturing output in US dollars for its noted year according to World Bank.[56] (en.wikipedia.org)
External Links
How To
How to use Lean Manufacturing in the production of goods
Lean manufacturing refers to a method of managing that seeks to improve efficiency and decrease waste. It was first developed in Japan in the 1970s/80s by Taiichi Ahno, who was awarded the Toyota Production System (TPS), award from KanjiToyoda, the founder of TPS. Michael L. Watkins published the book "The Machine That Changed the World", which was the first to be published about lean manufacturing.
Lean manufacturing is often defined as a set of principles used to improve the quality, speed, and cost of products and services. It emphasizes eliminating waste and defects throughout the value stream. Lean manufacturing is also known as just in time (JIT), zero defect total productive maintenance(TPM), and five-star (S). Lean manufacturing is about eliminating activities that do not add value, such as inspection, rework, and waiting.
In addition to improving product quality and reducing costs, lean manufacturing helps companies achieve their goals faster and reduces employee turnover. Lean manufacturing has been deemed one of the best ways to manage the entire value-chain, including customers, distributors as well retailers and employees. Lean manufacturing is widely used in many industries. Toyota's philosophy is a great example of this. It has helped to create success in automobiles as well electronics, appliances and healthcare.
Lean manufacturing is based on five principles:
-
Define Value: Identify the social value of your business and what sets you apart.
-
Reduce waste - Get rid of any activity that does not add value to the supply chain.
-
Create Flow – Ensure that work flows smoothly throughout the process.
-
Standardize and simplify - Make your processes as consistent as possible.
-
Build Relationships - Establish personal relationships with both internal and external stakeholders.
Although lean manufacturing has always been around, it is gaining popularity in recent years because of a renewed interest for the economy after 2008's global financial crisis. Many businesses have adopted lean production techniques to make them more competitive. Some economists even believe that lean manufacturing can be a key factor in economic recovery.
Lean manufacturing is now becoming a common practice in the automotive industry, with many benefits. These include improved customer satisfaction, reduced inventory levels, lower operating costs, increased productivity, and better overall safety.
The principles of lean manufacturing can be applied in almost any area of an organization. It is especially useful for the production aspect of an organization, as it ensures that every step in the value chain is efficient and effective.
There are three types of lean manufacturing.
-
Just-in Time Manufacturing, (JIT): This kind of lean manufacturing is also commonly known as "pull-systems." JIT means that components are assembled at the time of use and not manufactured in advance. This approach reduces lead time, increases availability and reduces inventory.
-
Zero Defects Manufacturing (ZDM),: ZDM is a system that ensures no defective units are left the manufacturing facility. If a part needs to be fixed during the assembly line, it should be repaired rather than scrapped. This applies to finished goods that may require minor repairs before shipment.
-
Continuous Improvement (CI), also known as Continuous Improvement, aims at improving the efficiency of operations through continuous identification and improvement to minimize or eliminate waste. Continuous Improvement involves continuous improvement of processes.