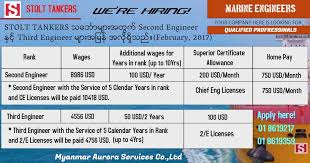
A cost estimate is required for almost everything a company does. They are the cost estimators. They are responsible for determining the costs associated with manufacturing and developing new products or services. They also have to determine the cost of building a brand new structure. This includes analyzing the costs of materials and labor.
Construction companies employ most cost estimators. They need to be able to understand construction processes and methods. They also need to be familiar with computer-aided design (CAD) software. This type of software is used to increase the efficiency of design and manufacturing. It is also necessary for cost estimators to be able read data from databases. They can also utilize other software such as Microsoft Excel.
To make accurate cost estimates, cost estimators collaborate with other professionals. They analyze the project blueprints, site conditions, as well as other materials, to determine each component's costs. They may also work with engineers to determine the gauges and machining operations required.
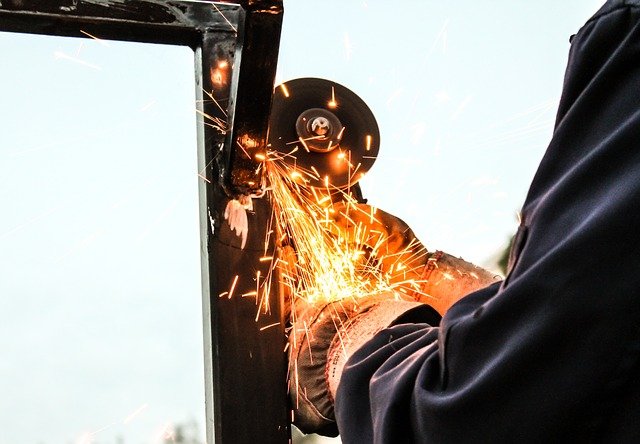
Cost estimators must be detail-oriented, assertive, and dependable. They must be able to analyze information that is difficult to interpret. They must be able to communicate clearly and accurately their findings. They should also be able to communicate with clients and professionals.
Cost estimators typically work in the engineering or cost divisions of a company. They must be able to apply science and math skills. They should also be familiar with computer software, including CAD, BIM, and commercial software. They might also need to complete a certification course. Certified Cost Estimator/Analyst(CCEA), Professional cost estimator/Analyst and Certified Professional Estimator are some examples of certifications.
Cost estimators may specialize in particular industries or services. Some individuals specialize in building or construction costs, while others focus on software development costs. Cost estimators are also able to find work in other areas, such as auto repair and maintenance, construction, and specialty trade contractors.
These people communicate with engineers, clients, or suppliers. They are also proficient in industry terminology. Before preparing cost estimates, they also have a lot of knowledge. Apart from preparing cost estimates and finding ways to cut costs, many people in this occupation also do studies.
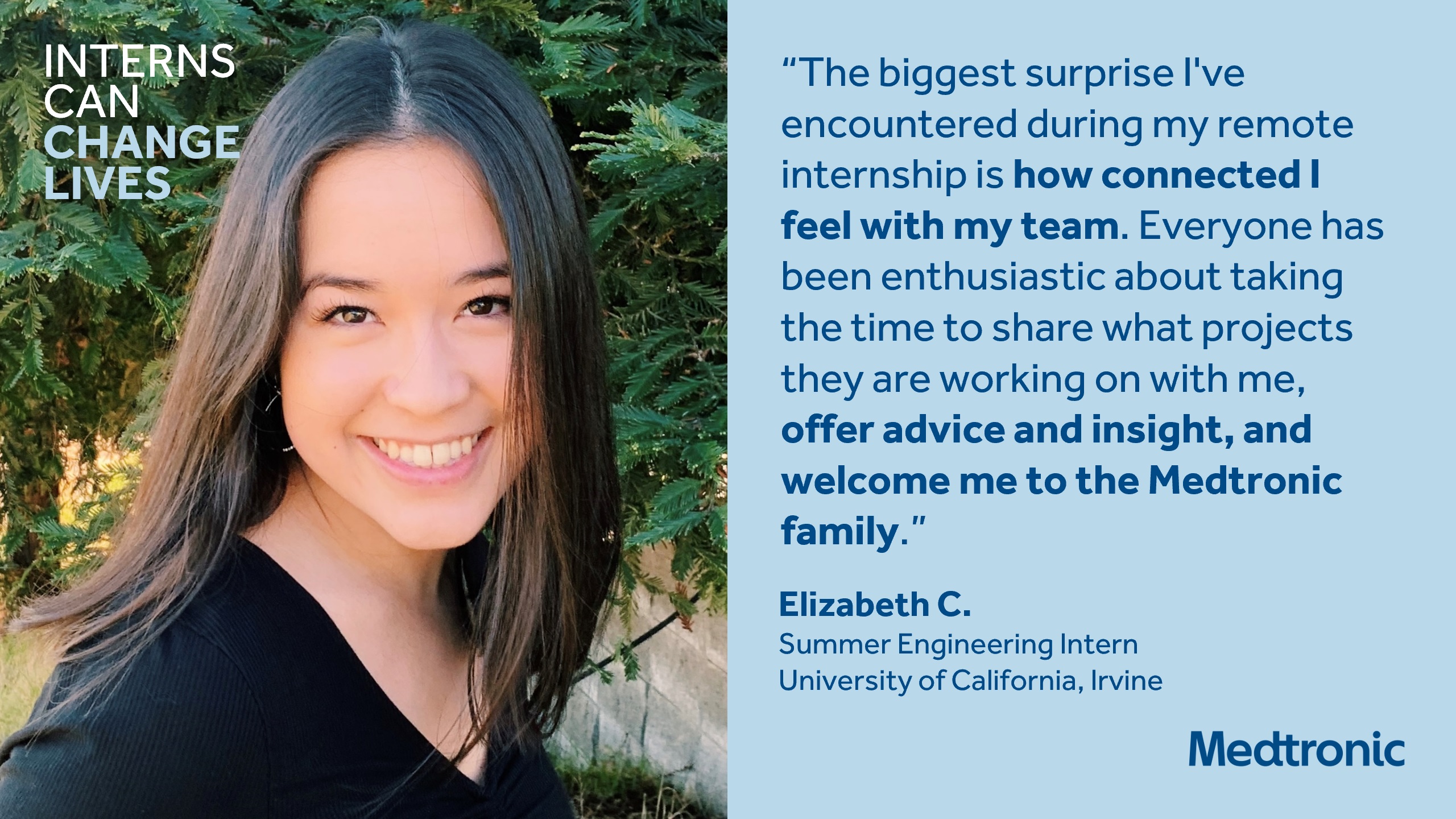
Job applicants might need a bachelor's or master's depending on their industry. They may also need an internship. They may also be eligible for cooperative education programs. In addition, construction companies are also increasingly looking for individuals with a degree in building construction or construction management.
Cost estimators work in construction firms and other manufacturing companies. They are responsible for estimating the costs of products and services to ensure that companies can place profitable bids. They also analyze data related the supply chain as well as other factors that may affect costs. You can also hire cost estimators to work on government programs. They may also be required to redesign existing products.
Cost estimators must have a strong understanding of computer-aided design (CAD) software. They can also learn how to use automated cost estimation software.
FAQ
What are the 7 R's of logistics?
The acronym 7Rs of Logistics refers to the seven core principles of logistics management. It was developed by the International Association of Business Logisticians (IABL) and published in 2004 as part of its "Seven Principles of Logistics Management" series.
The acronym consists of the following letters:
-
Responsible - ensure that actions are in compliance with legal requirements and do not cause harm to others.
-
Reliable – have faith in your ability and capability to keep promises.
-
Be responsible - Use resources efficiently and avoid wasting them.
-
Realistic - consider all aspects of operations, including cost-effectiveness and environmental impact.
-
Respectful: Treat others with fairness and equity
-
Be resourceful: Look for opportunities to save money or increase productivity.
-
Recognizable - Provide value-added services to customers
What is the job of a production plan?
A production planner makes sure all project elements are delivered on schedule, within budget, as well as within the agreed scope. They make sure that the product and services meet client expectations.
What are the goods of logistics?
Logistics involves the transportation of goods from point A and point B.
They cover all aspects of transportation, such as packing, loading, transporting and unloading.
Logisticians ensure that products reach the right destination at the right moment and under safe conditions. They help companies manage their supply chain efficiency by providing information on demand forecasts, stock levels, production schedules, and availability of raw materials.
They also keep track of shipments in transit, monitor quality standards, perform inventories and order replenishment, coordinate with suppliers and vendors, and provide support services for sales and marketing.
What does it take for a logistics enterprise to succeed?
It takes a lot of skills and knowledge to run a successful logistics business. Good communication skills are essential to effectively communicate with your suppliers and clients. You need to understand how to analyze data and draw conclusions from it. You will need to be able handle pressure well and work in stressful situations. You must be creative and innovative to develop new ideas to improve efficiency. You need to have strong leadership qualities to motivate team members and direct them towards achieving organizational goals.
It is important to be organized and efficient in order to meet tight deadlines.
Statistics
- (2:04) MTO is a production technique wherein products are customized according to customer specifications, and production only starts after an order is received. (oracle.com)
- Many factories witnessed a 30% increase in output due to the shift to electric motors. (en.wikipedia.org)
- In 2021, an estimated 12.1 million Americans work in the manufacturing sector.6 (investopedia.com)
- Job #1 is delivering the ordered product according to specifications: color, size, brand, and quantity. (netsuite.com)
- You can multiply the result by 100 to get the total percent of monthly overhead. (investopedia.com)
External Links
How To
How to Use lean manufacturing in the Production of Goods
Lean manufacturing refers to a method of managing that seeks to improve efficiency and decrease waste. It was first developed in Japan in the 1970s/80s by Taiichi Ahno, who was awarded the Toyota Production System (TPS), award from KanjiToyoda, the founder of TPS. Michael L. Watkins published the first book on lean manufacturing in 1990.
Lean manufacturing, often described as a set and practice of principles, is aimed at improving the quality, speed, cost, and efficiency of products, services, and other activities. It is about eliminating defects and waste from all stages of the value stream. Lean manufacturing is called just-in-time (JIT), zero defect, total productive maintenance (TPM), or 5S. Lean manufacturing seeks to eliminate non-value added activities, such as inspection, work, waiting, and rework.
Lean manufacturing can help companies improve their product quality and reduce costs. Additionally, it helps them achieve their goals more quickly and reduces employee turnover. Lean manufacturing is a great way to manage the entire value chain including customers, suppliers, distributors and retailers as well as employees. Lean manufacturing practices are widespread in many industries. For example, Toyota's philosophy underpins its success in automobiles, electronics, appliances, healthcare, chemical engineering, aerospace, paper, food, etc.
Lean manufacturing includes five basic principles:
-
Define Value: Identify the social value of your business and what sets you apart.
-
Reduce Waste - Remove any activity which doesn't add value to your supply chain.
-
Create Flow – Ensure that work flows smoothly throughout the process.
-
Standardize & simplify - Make processes consistent and repeatable.
-
Develop Relationships: Establish personal relationships both with internal and external stakeholders.
Although lean manufacturing isn't a new concept in business, it has gained popularity due to renewed interest in the economy after the 2008 global financial crisis. To increase their competitiveness, many businesses have turned to lean manufacturing. Many economists believe lean manufacturing will play a major role in economic recovery.
With many benefits, lean manufacturing is becoming more common in the automotive industry. These include better customer satisfaction and lower inventory levels. They also result in lower operating costs.
It can be applied to any aspect of an organisation. Lean manufacturing is most useful in the production sector of an organisation because it ensures that each step in the value-chain is efficient and productive.
There are three main types of lean manufacturing:
-
Just-in-Time Manufacturing (JIT): This type of lean manufacturing is commonly referred to as "pull systems." JIT refers to a system in which components are assembled at the point of use instead of being produced ahead of time. This approach is designed to reduce lead times and increase the availability of components. It also reduces inventory.
-
Zero Defects Manufacturing - ZDM: ZDM focuses its efforts on making sure that no defective units leave a manufacturing facility. Repairing a part that is damaged during assembly should be done, not scrapping. This is also true for finished products that require minor repairs before shipping.
-
Continuous Improvement (CI): CI aims to improve the efficiency of operations by continuously identifying problems and making changes in order to eliminate or minimize waste. Continuous Improvement involves continuous improvement of processes.