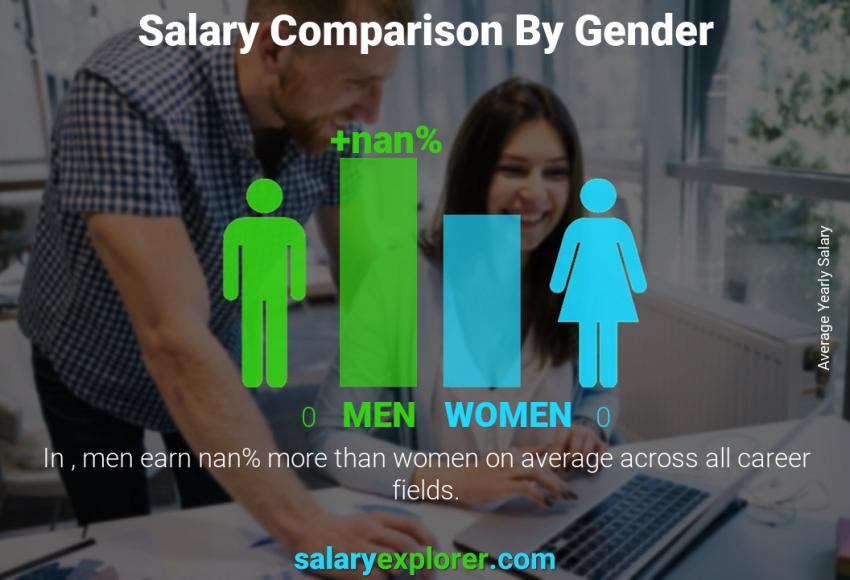
If you are interested in a career in chemistry, you may be wondering what a chemist salary is. Below is a list of average salaries for chemists and a breakdown of the different degrees that can be earned. A bachelor's in chemistry can lead to a salary of $50,000 to more than a hundred thousand dollars. Your location, degree earned, and employer will determine how much you make each year.
Average chemist salary
The Bureau of Labor Statistics estimates that the average starting salary for chemistry is $81,870 annually. The top-paid chemists are paid more than $130,000 per annum. The lowest-paid chemists get $42,960 a year. Pharmacist and medicine manufacturing companies are the most common places for chemists. The oil and gas industry offers the highest starting chemistry salary. According to the Bureau of Labor Statistics, there will be a 7 percent rise in chemist jobs in the next decade. More graduates who have had laboratory experience will be hired than those with no.
The average salary for chemistry depends on where you live and how much experience you have. The salary for a chemist will vary depending on the level of education, experience and additional skills. An $85,114 annual salary can be earned by an experienced California chemist. The salaries offered in other states may be more diverse. If you're looking to become a chemist, a PhD can increase your salary by 30% to 50% or more.
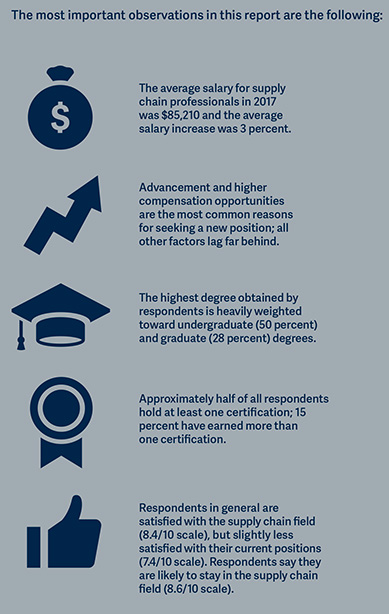
For chemists with a bachelor's, the salary range is
A chemistry degree could lead to a career in many different fields. According to the Bureau of Labor Statistics in 2010, there were 82,000 chemists living in the United States. A bachelor's degree in chemistry is sufficient to get a job in the field, but a graduate degree will allow you to earn more and take on more responsibility. According to the American Chemical Society, a chemist's median salary was $40,000 in 2011, but the starting salary for a Ph.D. is about $85,000.
Although a career in chemistry can be very lucrative, it is important to also consider the salary. A Ph.D. (in chemistry) can pay upwards to $60,000 depending on experience and job type. As a rule, the best-paid chemists work for the federal governments, research universities, or teaching.
Master's-level chemists can expect a range of salaries
A master's degree in chemistry can lead to a salary of up to 128,000 USD per year. However, the median salary can be found in many cases. Salary ranges vary for this career. A graduate with only two years of experience can expect to earn about forty thousand euros. A chemist who has more than ten years experience can make up to 239,000 dollars per year.
Most chemistry positions require a master’s degree or Ph.D. but they can be achieved with a bachelor’s degree. Graduates often specialize in a subfield. According to the American Chemical Society, the median starting salary for a chemist with a bachelor's degree was $43,000. The salary for those who worked in companies employing more than 25,000 people was $50,000.
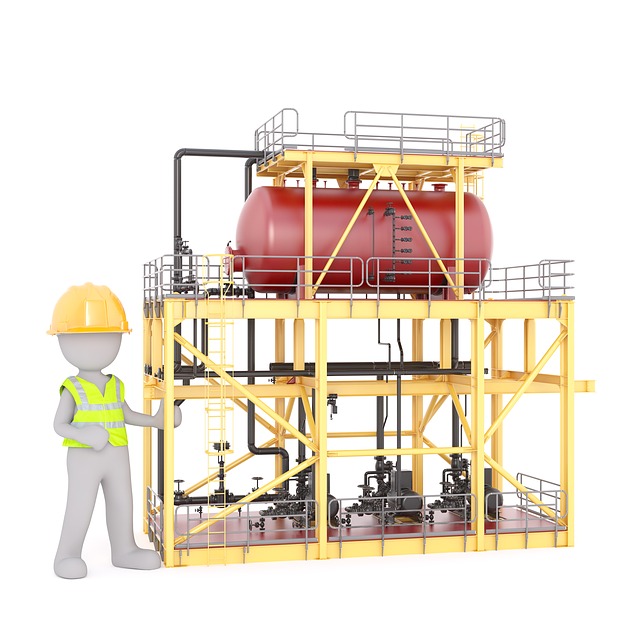
The salary range for chemists who have a Ph.D.
A PhD chemist's salary will depend on his/her previous work experience, as well as where and what he/she applies for. For example, the average salary for scientists in Germany is 40,400 Euros per year in small firms. In large companies, salaries can be as high as 50,000 euros. Scientists will generally be paid according the collective wage agreements that are in place within the company.
The U.S. has a lot of chemists, and they make a great living. However, they also have responsibilities in education or research. University professors typically work on government-funded and private-industry-funded projects. The field also offers opportunities for secondary school teachers. According to American Chemical Society, a bachelor's-level chemist earns around $40,000 per annum, while a master's-level chemist earns around $46,000 per annum. In 2011, a Ph.D. in chemistry earned a median salary of $85,000.
FAQ
What is the importance of automation in manufacturing?
Automation is essential for both manufacturers and service providers. They can provide services more quickly and efficiently thanks to automation. It also helps to reduce costs and improve productivity.
Can we automate some parts of manufacturing?
Yes! Since ancient times, automation has been in existence. The Egyptians invented the wheel thousands of years ago. Nowadays, we use robots for assembly lines.
There are many applications for robotics in manufacturing today. These include:
-
Robots for assembly line
-
Robot welding
-
Robot painting
-
Robotics inspection
-
Robots that create products
Manufacturing can also be automated in many other ways. For example, 3D printing allows us to make custom products without having to wait for weeks or months to get them manufactured.
What are the 7 Rs of logistics?
The acronym 7Rs of Logistics refers to the seven core principles of logistics management. It was developed and published by the International Association of Business Logisticians in 2004 as part of the "Seven Principles of Logistics Management".
The acronym is composed of the following letters.
-
Responsive - ensure all actions are legal and not harmful to others.
-
Reliable – have faith in your ability and capability to keep promises.
-
It is reasonable to use resources efficiently and not waste them.
-
Realistic - Take into consideration all aspects of operations including cost-effectiveness, environmental impact, and other factors.
-
Respectful: Treat others with fairness and equity
-
You are resourceful and look for ways to save money while increasing productivity.
-
Recognizable: Provide customers with value-added service
Statistics
- (2:04) MTO is a production technique wherein products are customized according to customer specifications, and production only starts after an order is received. (oracle.com)
- According to a Statista study, U.S. businesses spent $1.63 trillion on logistics in 2019, moving goods from origin to end user through various supply chain network segments. (netsuite.com)
- According to the United Nations Industrial Development Organization (UNIDO), China is the top manufacturer worldwide by 2019 output, producing 28.7% of the total global manufacturing output, followed by the United States, Japan, Germany, and India.[52][53] (en.wikipedia.org)
- [54][55] These are the top 50 countries by the total value of manufacturing output in US dollars for its noted year according to World Bank.[56] (en.wikipedia.org)
- You can multiply the result by 100 to get the total percent of monthly overhead. (investopedia.com)
External Links
How To
How to Use Lean Manufacturing in the Production of Goods
Lean manufacturing is a management system that aims at increasing efficiency and reducing waste. It was first developed in Japan in the 1970s/80s by Taiichi Ahno, who was awarded the Toyota Production System (TPS), award from KanjiToyoda, the founder of TPS. Michael L. Watkins published the book "The Machine That Changed the World", which was the first to be published about lean manufacturing.
Lean manufacturing, often described as a set and practice of principles, is aimed at improving the quality, speed, cost, and efficiency of products, services, and other activities. It is about eliminating defects and waste from all stages of the value stream. The five-steps of Lean Manufacturing are just-in time (JIT), zero defect and total productive maintenance (TPM), as well as 5S. Lean manufacturing is about eliminating activities that do not add value, such as inspection, rework, and waiting.
Lean manufacturing not only improves product quality but also reduces costs. Companies can also achieve their goals faster by reducing employee turnover. Lean manufacturing is a great way to manage the entire value chain including customers, suppliers, distributors and retailers as well as employees. Lean manufacturing is widely used in many industries. Toyota's philosophy, for example, is what has enabled it to be successful in electronics, automobiles, medical devices, healthcare and chemical engineering as well as paper and food.
Five basic principles of Lean Manufacturing are included in lean manufacturing
-
Define Value - Identify the value your business adds to society and what makes you different from competitors.
-
Reduce Waste - Eliminate any activity that doesn't add value along the supply chain.
-
Create Flow: Ensure that the work process flows without interruptions.
-
Standardize & Simplify - Make processes as consistent and repeatable as possible.
-
Build Relationships - Establish personal relationships with both internal and external stakeholders.
Although lean manufacturing has always been around, it is gaining popularity in recent years because of a renewed interest for the economy after 2008's global financial crisis. Many businesses have adopted lean production techniques to make them more competitive. Many economists believe lean manufacturing will play a major role in economic recovery.
With many benefits, lean manufacturing is becoming more common in the automotive industry. These include higher customer satisfaction, lower inventory levels, lower operating expenses, greater productivity, and improved overall safety.
You can apply Lean Manufacturing to virtually any aspect of your organization. However, it is particularly useful when applied to the production side of an organization because it ensures that all steps in the value chain are efficient and effective.
There are three main types in lean manufacturing
-
Just-in-Time Manufacturing (JIT): This type of lean manufacturing is commonly referred to as "pull systems." JIT stands for a system where components are assembled on the spot rather than being made in advance. This approach reduces lead time, increases availability and reduces inventory.
-
Zero Defects Manufacturing - ZDM: ZDM focuses its efforts on making sure that no defective units leave a manufacturing facility. It is better to repair a part than have it removed from the production line if it needs to be fixed. This applies to finished products, which may need minor repairs before they are shipped.
-
Continuous Improvement (CI),: Continuous improvement aims improve the efficiency and effectiveness of operations by continuously identifying issues and making changes to reduce waste. Continuous improvement refers to continuous improvement of processes as well people and tools.