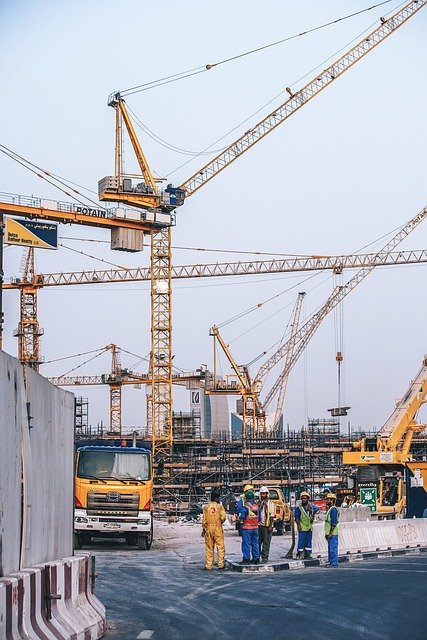
The United States is third in manufacturing in the world and saw its manufacturing output reach a record at $2.00 trillion in Q1 2018. This was nearly twice the amount it had before the Great Recession. Despite a strong domestic economy and a robust manufacturing sector, the United States is still taking a cautious approach to its current problems. We need to be more aggressive when addressing the challenges facing our industry, whether it is because of a lack investment or lack of skilled labor.
The number of jobs has declined by 5,000,000 since 2000
Five million US manufacturing jobs were lost between 2000 and now. Although some believe that trade with China has contributed to the decrease in manufacturing jobs, this accounts for only a quarter of the total decline. Manufacturing jobs were also lost in countries that couldn't compete with Chinese imports. The reasons behind the decline in manufacturing jobs are numerous. Here are some reasons why manufacturing jobs have declined:
Over the past two decades, almost a third have been lost in US manufacturing. It was 17,000,000 in 1965. By 2010, it had fallen to 12,000,000. It is not because of trade that manufacturing jobs are declining. Instead, they have been impacted by structural issues - a declines in output, capital investment, productivity and trade deficits. This is not sustainable. While productivity gains have a major role to play in the decline, they weren't enough to offset the loss of manufacturing jobs. Not productivity gains, but automation is the problem.
Strong demand for manufactured goods
Despite the decline in consumer spending, the US still has a strong demand to manufacture goods. In 1945 personal spending on durable goods accounted 58% of total spending. Today, it accounts for only 28%. This is due to the fact that the cost of manufacturing and selling these goods has declined while the content has risen. As a result, the cost of computers, televisions, and sound equipment has fallen significantly.
The US's recovery in manufacturing activity has resulted in an increase in the production of manufactured goods. The Fifth District Manufacturing Activity Survey reveals that the demand for manufactured products is strong, with production increasing rapidly. However, supply chain problems are slowing down output. The increased production has put strain on supply chains. Respondents reported disruptions in their ability supply chain to maintain required inventories. Backlogs and lead times for vendors have increased.
Trade deficit in manufactured goods has more than doubled in the past decade
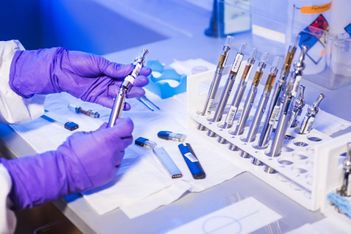
Some economists fear that the U.S.’s trade surplus will lead to lower global GDP and increase instability among its trading partners. However, high imports from the USA of manufactured goods is not necessarily a problem for the U.S. economy. It is crucial to maintaining economic stability worldwide. High levels of foreign market demand can make it difficult for the U.S. to achieve full employment.
Since 2000, the U.S. has almost doubled its trade deficit for manufactured goods. The US deficit has been growing partly because of the increase in Chinese imports. But the larger problem is that this imbalance is concentrated in the manufacturing sector, where wages and employment have decreased since the 1990s. As a result, US manufacturing employment has fallen dramatically from 26 percent in 1970 to 8.5 percent in 2016. Some economists attribute the decline to China's increased competition, but most attribute the decline to automation, productivity increases, and demand shifting away from goods to services.
Industry has a shotgun approach
The US has a variety of advanced manufacturing initiatives. It is also well-established in this area. But some countries are attempting to introduce the internet of things to manufacturing. The US, on other hand, is focused on different technologies and blends traditional mass media with Internet advertisement. The result is a shotgun approach. Companies focus on many technologies and target a broad client base.
FAQ
What are the differences between these four types?
Manufacturing is the process that transforms raw materials into useful products. Manufacturing can include many activities such as designing and building, testing, packaging shipping, selling, servicing, and other related activities.
How can manufacturing reduce production bottlenecks?
Avoiding production bottlenecks is as simple as keeping all processes running smoothly, from the time an order is received until the product ships.
This includes planning for capacity requirements as well as quality control measures.
The best way to do this is to use continuous improvement techniques such as Six Sigma.
Six Sigma management is a system that improves quality and reduces waste within your organization.
It's all about eliminating variation and creating consistency in work.
What are the jobs in logistics?
There are many types of jobs in logistics. Some examples are:
-
Warehouse workers - They load trucks and pallets.
-
Transportation drivers – They drive trucks or trailers to transport goods and perform pick-ups.
-
Freight handlers are people who sort and pack freight into warehouses.
-
Inventory managers – They manage the inventory in warehouses.
-
Sales representatives - They sell products.
-
Logistics coordinators – They plan and coordinate logistics operations.
-
Purchasing agents are those who purchase goods and services for the company.
-
Customer service representatives - They answer calls and emails from customers.
-
Shipping clerks - They process shipping orders and issue bills.
-
Order fillers - These people fill orders based on what has been ordered.
-
Quality control inspectors (QCI) - They inspect all incoming and departing products for potential defects.
-
Others - There is a variety of other jobs in logistics. These include transportation supervisors and cargo specialists.
What is the role of a manager in manufacturing?
A manufacturing manager must make sure that all manufacturing processes run smoothly and effectively. They should be alert for any potential problems in the company and react accordingly.
They should also learn how to communicate effectively with other departments, including sales and marketing.
They should be up to date on the latest trends and be able apply this knowledge to increase productivity and efficiency.
What are the 7 Rs of logistics?
The acronym "7R's" of Logistics stands for seven principles that underpin logistics management. It was developed by International Association of Business Logisticians (IABL), and published as part of their "Seven Principles of Logistics Management Series" in 2004.
The acronym is made up of the following letters:
-
Responsible - ensure that actions are in compliance with legal requirements and do not cause harm to others.
-
Reliable – have faith in your ability and capability to keep promises.
-
Reasonable - make sure you use your resources well and don't waste them.
-
Realistic - Take into consideration all aspects of operations including cost-effectiveness, environmental impact, and other factors.
-
Respectful – Treat others fairly and equitably.
-
Resourceful - look for opportunities to save money and increase productivity.
-
Recognizable provides value-added products and services to customers
What is the difference between a production planner and a project manager?
The main difference between a production planner and a project manager is that a project manager is usually the person who plans and organizes the entire project, whereas a production planner is mainly involved in the planning stage of the project.
Statistics
- Many factories witnessed a 30% increase in output due to the shift to electric motors. (en.wikipedia.org)
- In 2021, an estimated 12.1 million Americans work in the manufacturing sector.6 (investopedia.com)
- You can multiply the result by 100 to get the total percent of monthly overhead. (investopedia.com)
- [54][55] These are the top 50 countries by the total value of manufacturing output in US dollars for its noted year according to World Bank.[56] (en.wikipedia.org)
- Job #1 is delivering the ordered product according to specifications: color, size, brand, and quantity. (netsuite.com)
External Links
How To
How to Use the Just In Time Method in Production
Just-in-time is a way to cut costs and increase efficiency in business processes. It's the process of obtaining the right amount and timing of resources when you need them. This means that you only pay the amount you actually use. Frederick Taylor was the first to coin this term. He developed it while working as a foreman during the early 1900s. After observing how workers were paid overtime for late work, he realized that overtime was a common practice. He decided to ensure workers have enough time to do their jobs before starting work to improve productivity.
JIT is an acronym that means you need to plan ahead so you don’t waste your money. Look at your entire project, from start to end. Make sure you have enough resources in place to deal with any unexpected problems. You can anticipate problems and have enough equipment and people available to fix them. This way, you won't end up paying extra money for things that weren't really necessary.
There are many types of JIT methods.
-
Demand-driven: This type of JIT allows you to order the parts/materials required for your project on a regular basis. This will allow for you to track the material that you have left after using it. You'll also be able to estimate how long it will take to produce more.
-
Inventory-based: This is a type where you stock the materials required for your projects in advance. This allows for you to anticipate how much you can sell.
-
Project-driven: This means that you have enough money to pay for your project. If you know the amount you require, you can buy the materials you need.
-
Resource-based: This is the most common form of JIT. You allocate resources based on the demand. You will, for example, assign more staff to deal with large orders. If you don't have many orders, you'll assign fewer people to handle the workload.
-
Cost-based: This approach is very similar to resource-based. However, you don't just care about the number of people you have; you also need to consider how much each person will cost.
-
Price-based: This is very similar to cost-based, except that instead of looking at how much each individual worker costs, you look at the overall price of the company.
-
Material-based: This is quite similar to cost-based, but instead of looking at the total cost of the company, you're concerned with how much raw materials you spend on average.
-
Time-based: Another variation of resource-based JIT. Instead of focusing solely on the amount each employee costs, focus on how long it takes for the project to be completed.
-
Quality-based JIT - This is another form of resource-based JIT. Instead of thinking about the cost of each employee or the time it takes to produce something, you focus on how good your product quality.
-
Value-based: This is one of the newest forms of JIT. You don't worry about whether the products work or if they meet customer expectations. Instead, your focus is on the value you bring to the market.
-
Stock-based is an inventory-based system that measures the number of items produced at any given moment. It's useful when you want maximum production and minimal inventory.
-
Just-intime (JIT), planning is a combination JIT management and supply chain management. It is the process that schedules the delivery of components within a short time of their order. It's important because it reduces lead times and increases throughput.