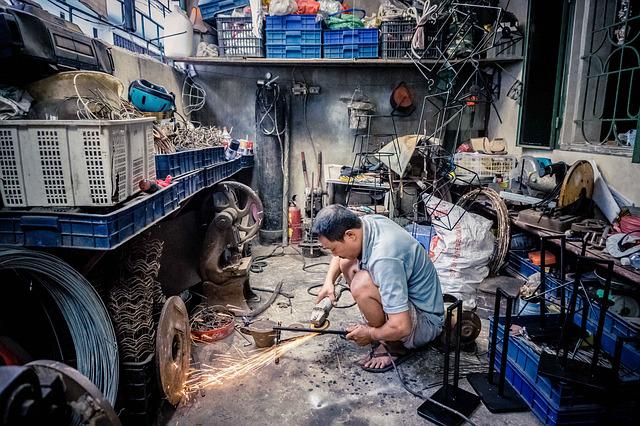
You may be interested in Estimator jobs. But, are you wondering how to get the job? This article will provide information about the typical role and the salary range. You will also find the necessary skills and experience to perform this role. Continue reading to learn even more. Listed below are a few of the most important qualities that an ideal candidate should have. This will make your job easier as an Estimator.
Ideal candidate for estimator role
The ideal candidate for Estimator should be proficient in Mathematics principles and possess exceptional analytical skills. He or she should also possess excellent communication skills and be detail-oriented. The ideal candidate should have at least a Bachelor's degree and 3 years' experience in a relevant field. Candidates should also be proficient in MS Office suite. They should possess excellent analytical skills and be able handle pressure.
A bachelor's degree is essential for Estimator roles. On top of that, the candidate should be highly motivated and enthusiastic. They should be able communicate with clients, have self-confidence and be positive about the job. They must also be able to present their estimates and make a good first impression. It is crucial that the candidate can fulfill their promises and hold them accountable for meeting deadlines.
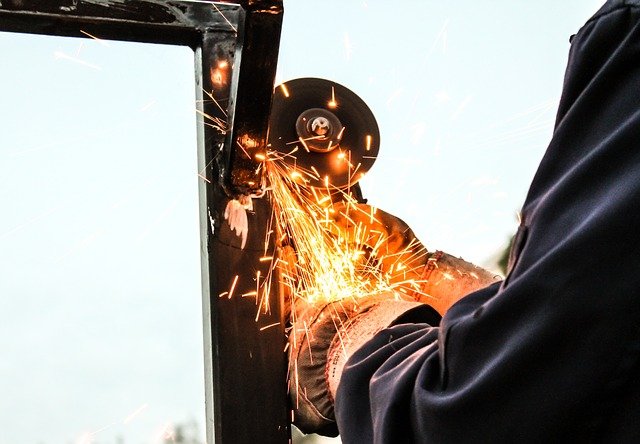
Job description
The primary function of an estimator is to provide detailed reports to improve a company's profitability and growth. The role of an estimator involves using computer software and communicating with personnel to determine the estimated cost and time for a project. An estimator also creates and presents reports to clients that include recommendations and budget risks. Estimators make educated guesses about the costs of a project. These workers are still valuable to employers and can greatly improve a company's bottom-line.
In this role, the job description for estimators should be tailored to the particular area of interest of the applicant. A job description for a construction estimator might include a background in quantity surveys, but that knowledge is not necessary for all construction projects. Estimators must also be proficient in other areas, such as technology, energy, and environment. It doesn't matter if the company is looking to hire a fulltime employee or contractor, there will be a suitable job description.
Salary
An estimate is someone who works in the construction industry to determine a project's cost. Estimators have a wide variety of responsibilities and may specialize in a particular area. Before you can increase the salary for an estimator you should first identify the relevant experience. An apprenticeship program is a great option for new employees. An associate's degree is helpful if your skill set includes estimating. Then, you can advance in your career to a full-time salary.
In addition to delivering valuable information, an estimator must have a thorough knowledge of building materials and methods. These skills allow them to make accurate and useful forecasts. These professionals work in high-pressure situations. However, they are highly collaborative and must be able to provide accurate information and work with others. Salary information for estimators is based upon Indeed Salaries data. These figures can be affected by the location, employer, and education of candidates.
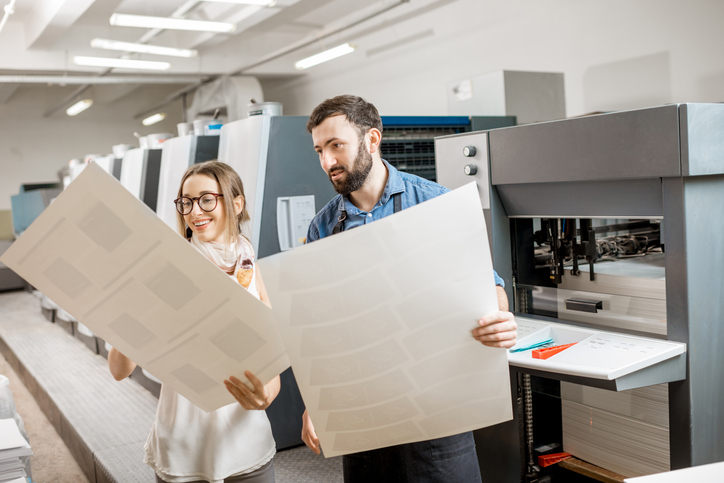
Work environment
As an estimator, your main responsibility will be to prepare bids for construction projects. You will also be responsible for all aspects of estimating, including analyzing RFPs and identifying high-yielding work. Your responsibilities include setting priorities, attending pre-bid meeting, and identifying labor, equipment, or materials requirements for each job. You will also be working with project managers to prepare different change orders.
Most estimator jobs require a bachelor’s degree, but some employers will accept a high school diploma. While some employers will accept applicants with an associate's degree but not a five-year college degree, many prefer applicants with a four- or five year college degree. Popular degrees include business-related degrees and mathematics. For construction estimators, you will need strong numeracy skills.
FAQ
Why automate your warehouse
Automation has become increasingly important in modern warehousing. E-commerce has increased the demand for quicker delivery times and more efficient processes.
Warehouses need to adapt quickly to meet changing needs. They must invest heavily in technology to do this. The benefits of automating warehouses are numerous. These are just a few reasons to invest in automation.
-
Increases throughput/productivity
-
Reduces errors
-
Accuracy is improved
-
Safety is boosted
-
Eliminates bottlenecks
-
Companies can scale more easily
-
It makes workers more efficient
-
Gives you visibility into all that is happening in your warehouse
-
Enhances customer experience
-
Improves employee satisfaction
-
Reducing downtime and increasing uptime
-
Quality products delivered on time
-
Eliminates human error
-
It helps ensure compliance with regulations
What is manufacturing and logistics?
Manufacturing is the process of creating goods from raw materials by using machines and processes. Logistics covers all aspects involved in managing supply chains, including procurement and production planning. Logistics and manufacturing are often referred to as one thing. It encompasses both the creation of products and their delivery to customers.
What is production planning?
Production Planning involves developing a plan for all aspects of the production, including scheduling, budgeting, casting, crew, location, equipment, props, etc. This document will ensure everything is in order and ready to go when you need it. You should also have information to ensure the best possible results on set. This includes information on shooting times, locations, cast lists and crew details.
It is important to first outline the type of film you would like to make. You may have already chosen the location you want, or there are locations or sets you prefer. Once you have determined your scenes and locations, it is time to start figuring out the elements that you will need for each scene. Perhaps you have decided that you need to buy a car but aren't sure which model. This is where you can look up car models online and narrow down your options by choosing from different makes and models.
Once you have found the right car, you can start thinking about extras. What about additional seating? Maybe you need someone to move around in the back. You may want to change the interior's color from black or white. These questions can help you decide the right look for your car. You can also think about the type of shots you want to get. Will you be filming close-ups or wide angles? Maybe the engine or steering wheel is what you are looking to film. These things will help you to identify the car that you are looking for.
Once you have made all the necessary decisions, you can start to create a schedule. You can create a schedule that will outline when you must start and finish your shoots. Each day will include the time when you need to arrive at the location, when you need to leave and when you need to return home. It will help everyone know exactly what they have to do and when. It is possible to make arrangements in advance for additional staff if you are looking to hire. You don't want to hire someone who won't show up because he didn't know.
You will need to factor in the days that you have to film when creating your schedule. Some projects are quick and easy, while others take weeks. When creating your schedule, be aware of whether you need more shots per day. Multiple takes at the same place will result in higher costs and longer completion times. If you aren't sure whether you need multiple shots, it is best to take fewer photos than you would like.
Budget setting is an important part of production planning. You will be able to manage your resources if you have a realistic budget. If you have to reduce your budget due to unexpected circumstances, you can always lower it later. You shouldn't underestimate the amount you'll spend. You'll end up with less money after paying for other things if the cost is underestimated.
Production planning is a detailed process. But, once you understand the workings of everything, it becomes easier for future projects to be planned.
How can efficiency in manufacturing be improved?
First, identify the factors that affect production time. The next step is to identify the most important factors that affect production time. You can start by identifying the most important factors that impact production time. Once you have identified the factors, then try to find solutions.
Statistics
- (2:04) MTO is a production technique wherein products are customized according to customer specifications, and production only starts after an order is received. (oracle.com)
- According to the United Nations Industrial Development Organization (UNIDO), China is the top manufacturer worldwide by 2019 output, producing 28.7% of the total global manufacturing output, followed by the United States, Japan, Germany, and India.[52][53] (en.wikipedia.org)
- In 2021, an estimated 12.1 million Americans work in the manufacturing sector.6 (investopedia.com)
- It's estimated that 10.8% of the U.S. GDP in 2020 was contributed to manufacturing. (investopedia.com)
- Many factories witnessed a 30% increase in output due to the shift to electric motors. (en.wikipedia.org)
External Links
How To
How to Use 5S for Increasing Productivity in Manufacturing
5S stands for "Sort", "Set In Order", "Standardize", "Separate" and "Store". The 5S methodology was developed at Toyota Motor Corporation in 1954. It improves the work environment and helps companies to achieve greater efficiency.
This method has the basic goal of standardizing production processes to make them repeatable. This means that every day tasks such cleaning, sorting/storing, packing, and labeling can be performed. This knowledge allows workers to be more efficient in their work because they are aware of what to expect.
Implementing 5S requires five steps. These are Sort, Set In Order, Standardize. Separate. And Store. Each step requires a different action, which increases efficiency. Sorting things makes it easier to find them later. Once you have placed items in an ordered fashion, you will put them together. Then, after you separate your inventory into groups, you store those groups in containers that are easy to access. You can also label your containers to ensure everything is properly labeled.
This process requires employees to think critically about how they do their job. Employees must understand why they do certain tasks and decide if there's another way to accomplish them without relying on the old ways of doing things. In order to use the 5S system effectively, they must be able to learn new skills.
In addition to improving efficiency, the 5S system also increases morale and teamwork among employees. As they begin to see improvements, they feel motivated to continue working towards the goal of achieving higher levels of efficiency.