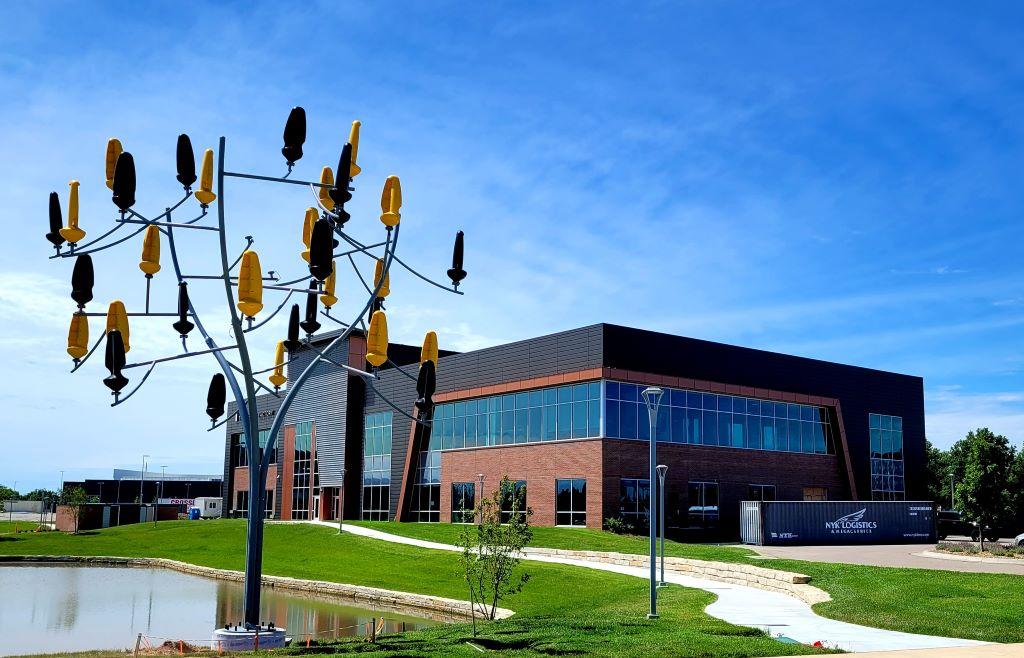
Customers expect products to provide a holistic experience. To meet this expectation, companies need a supply chain capable of delivering personalized products quickly and customized. Modern supply chains are more flexible and responsive to changing needs than their traditional counterparts. Companies can use data and analytics to monitor disruptions and make better business decisions for timely and reliable delivery.
Accenture Strategy, an Accenture service, helps companies transform their supply chain capabilities. This includes finding innovative solutions, improving the capabilities and skills of the supply chain workforce, as well as aligning operating models and business strategies. This includes a strong focus on sustainability and good governance. Ultimately, the company aims to build long-term value for its clients.
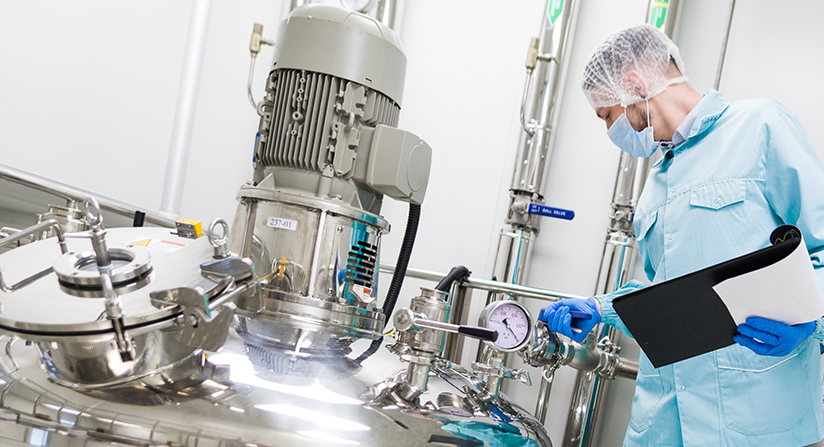
Accenture's focus is on global supply chain improvement. Accenture combines industry knowledge with digital services to help achieve this goal. Combining their industry expertise with a global supply chain, they can help companies create intelligent supply chains that lead to profitable growth and positive change. Supply chain experts from Accenture work with a wide range of industries, ranging from consumer packaged goods to energy. Using a wide array of application and services, Accenture's experts work with clients to help them design, operate, and transform their supply networks.
Accenture also works with clients on sustainability initiatives. Accenture has a global supplier inclusion program which aims to assist more companies in making good business decisions and advancing a sustainable, inclusive, ethical supply chain ecosystem. The company recently released a report that provides advice on creating a sustainable supply chain, leveraging data, and leveraging governance. The report also offers suggestions for creating resilient supply network and supplier scoring data.
Accenture's supply chain analytics team works with clients to improve their sustainability practices and to help them become more responsible. They are able identify clients' strengths, weaknesses and opportunities for improvement. Blue Yonder technology was used by the team in order to assist companies with optimizing their supply chain.
Accenture is well-known for its supply chain expertise. The company also has considerable purchasing power. Accenture's enterprise business system was introduced in 2007 to give businesses the ability to manage and implement supply chains more efficiently. Previously, most companies could not see past a few major suppliers and knew very little about their supply chain. Companies could not respond quickly to changing demand. myConcerto, a company-wide solution that gives companies detailed information about how to monitor their supply channels, was created by the company.
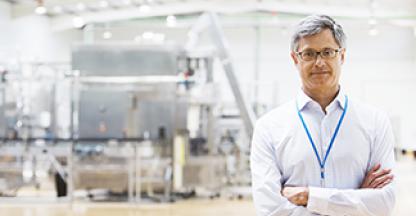
Accenture works with the Defense Logistics Agency, where they help improve the reliability and efficiency in military supply chains. The DLA oversees 520,000 shipments annually, and averages over 8,000 contracts per hour. Accenture collaborates with the DLA in order to increase product availability and decrease delivery times. Accenture also partners with Coles Supermarkets to enhance the customer experience and develop Splunk technology for control tower monitoring.
FAQ
What is the difference between a production planner and a project manager?
The main difference between a production planner and a project manager is that a project manager is usually the person who plans and organizes the entire project, whereas a production planner is mainly involved in the planning stage of the project.
What does it take for a logistics enterprise to succeed?
To be a successful businessman in logistics, you will need many skills and knowledge. Good communication skills are essential to effectively communicate with your suppliers and clients. You need to understand how to analyze data and draw conclusions from it. You will need to be able handle pressure well and work in stressful situations. To improve efficiency, you must be innovative and creative. To motivate and guide your team towards reaching organizational goals, you must have strong leadership skills.
You should also be organized and efficient to meet tight deadlines.
Why should you automate your warehouse?
Modern warehousing is becoming more automated. The rise of e-commerce has led to increased demand for faster delivery times and more efficient processes.
Warehouses must be able to quickly adapt to changing demands. In order to do this, they need to invest in technology. The benefits of automating warehouses are numerous. Here are some reasons why it's worth investing in automation:
-
Increases throughput/productivity
-
Reduces errors
-
Accuracy is improved
-
Safety increases
-
Eliminates bottlenecks
-
Companies can scale more easily
-
This makes workers more productive
-
It gives visibility to everything that happens inside the warehouse
-
Enhances customer experience
-
Improves employee satisfaction
-
It reduces downtime, and increases uptime
-
Quality products delivered on time
-
Human error can be eliminated
-
Assure compliance with regulations
Statistics
- You can multiply the result by 100 to get the total percent of monthly overhead. (investopedia.com)
- (2:04) MTO is a production technique wherein products are customized according to customer specifications, and production only starts after an order is received. (oracle.com)
- Many factories witnessed a 30% increase in output due to the shift to electric motors. (en.wikipedia.org)
- In 2021, an estimated 12.1 million Americans work in the manufacturing sector.6 (investopedia.com)
- According to a Statista study, U.S. businesses spent $1.63 trillion on logistics in 2019, moving goods from origin to end user through various supply chain network segments. (netsuite.com)
External Links
How To
How to Use lean manufacturing in the Production of Goods
Lean manufacturing (or lean manufacturing) is a style of management that aims to increase efficiency, reduce waste and improve performance through continuous improvement. It was developed in Japan during the 1970s and 1980s by Taiichi Ohno, who received the Toyota Production System (TPS) award from TPS founder Kanji Toyoda. The first book published on lean manufacturing was titled "The Machine That Changed the World" written by Michael L. Watkins and published in 1990.
Lean manufacturing is often described as a set if principles that help improve the quality and speed of products and services. It emphasizes reducing defects and eliminating waste throughout the value chain. Lean manufacturing can be described as just-in–time (JIT), total productive maintenance, zero defect (TPM), or even 5S. Lean manufacturing is about eliminating activities that do not add value, such as inspection, rework, and waiting.
Lean manufacturing not only improves product quality but also reduces costs. Companies can also achieve their goals faster by reducing employee turnover. Lean Manufacturing is one of the most efficient ways to manage the entire value chains, including suppliers and customers as well distributors and retailers. Lean manufacturing is widely used in many industries. Toyota's philosophy, for example, is what has enabled it to be successful in electronics, automobiles, medical devices, healthcare and chemical engineering as well as paper and food.
Five basic principles of Lean Manufacturing are included in lean manufacturing
-
Define Value- Identify the added value your company brings to society. What makes you stand out from your competitors?
-
Reduce Waste - Remove any activity which doesn't add value to your supply chain.
-
Create Flow - Make sure work runs smoothly without interruptions.
-
Standardize and simplify - Make your processes as consistent as possible.
-
Build Relationships- Develop personal relationships with both internal as well as external stakeholders.
Although lean manufacturing has always been around, it is gaining popularity in recent years because of a renewed interest for the economy after 2008's global financial crisis. Many companies have adopted lean manufacturing methods to increase their marketability. In fact, some economists believe that lean manufacturing will be an important factor in economic recovery.
With many benefits, lean manufacturing is becoming more common in the automotive industry. These include better customer satisfaction and lower inventory levels. They also result in lower operating costs.
Lean manufacturing can be applied to almost every aspect of an organization. Because it makes sure that all value chains are efficient and effectively managed, Lean Manufacturing is particularly helpful for organizations.
There are three types of lean manufacturing.
-
Just-in-Time Manufacturing: Also known as "pull systems", this type of lean manufacturing uses just-in-time manufacturing (JIT). JIT is a method in which components are assembled right at the moment of use, rather than being manufactured ahead of time. This approach reduces lead time, increases availability and reduces inventory.
-
Zero Defects Manufacturing (ZDM),: ZDM is a system that ensures no defective units are left the manufacturing facility. If a part is required to be repaired on the assembly line, it should not be scrapped. This applies to finished goods that may require minor repairs before shipment.
-
Continuous Improvement (CI), also known as Continuous Improvement, aims at improving the efficiency of operations through continuous identification and improvement to minimize or eliminate waste. Continuous improvement involves continuous improvement of processes and people as well as tools.