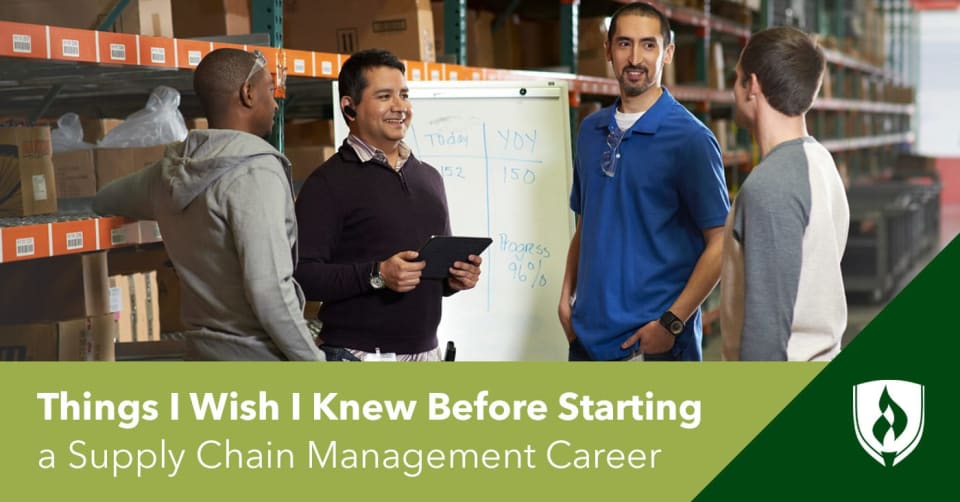
Ideally, a supply chain manager should be experienced in leading manufacturing roles. This means that they should have a bachelor's degree or more, and they should have at least 10 years' experience. They should also have the ability to work with colleagues in their company. They must be self-motivated and capable of making decisions that have an impact on the supply chain. They must be fluent in safety procedures and industry terminology.
Supply chain managers oversee the entire logistics process. They communicate with customers and suppliers to ensure that the company's supply chains run smoothly. They are responsible for finding solutions to all problems and helping to create a productive, functional environment. They also coordinate the company's supply- and distribution strategy.
Managers of supply chains are responsible to coordinate the various phases of raw materials procurement, production, as well as distribution. They should be able negotiate the prices of raw materials and equipment and be able monitor the effectiveness and efficiency of their supply chains. They are responsible for planning and coordinating transportation and storage strategies, as well as keeping the company's inventory databases current.
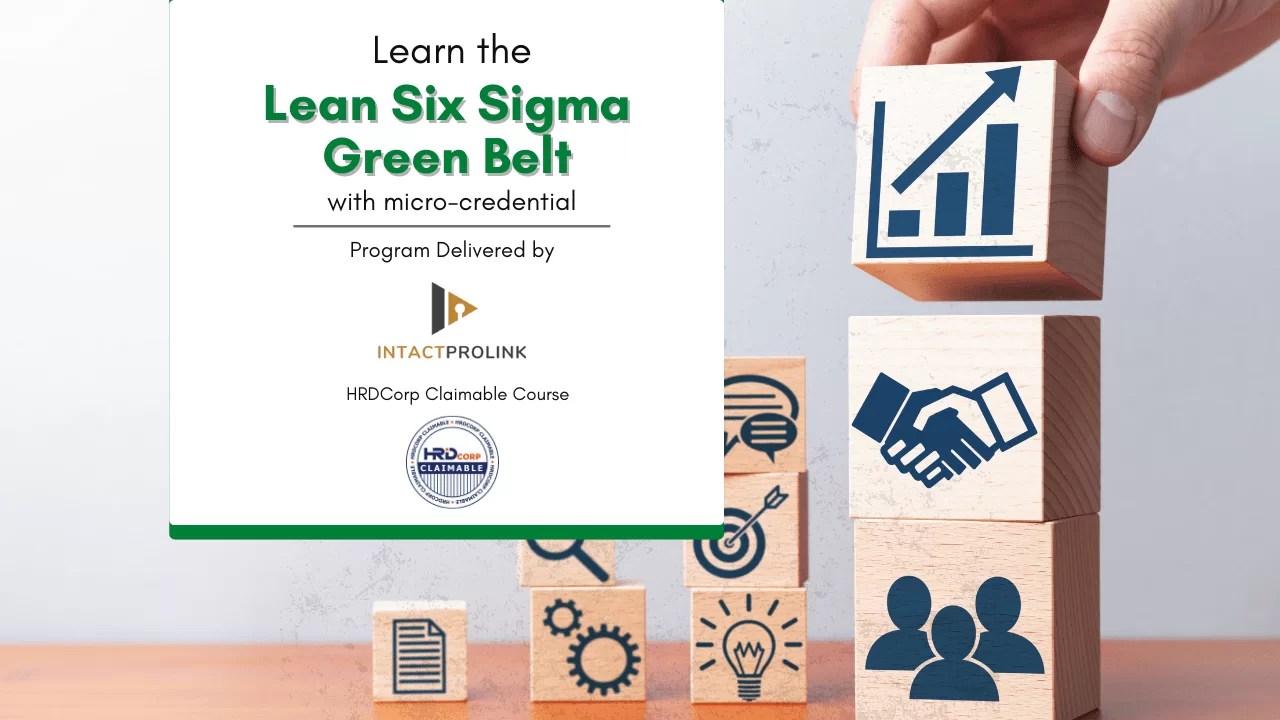
Also, supply chain managers ensure that products of the company are high quality. They are responsible for optimizing the firm’s human and financial resources. They are responsible for finding opportunities to recycle, reuse and repurpose products, materials, and products. They should also be able anticipate future needs throughout the production process.
Many industries employ supply chain managers, including retail, fashion and food. They should be able and willing to communicate with all departments in their company. They will need to have a solid understanding of supply chain management as well as management principles, strategies and techniques. They should have a strong background in manufacturing and be capable of managing large-scale operations.
Supply chain managers must have specific training in inventory control and supplier management. They should be familiarized with the industry's policies. They should have an ability to organize and manage groups. They must also have a thorough understanding of the company's operations and be able to lead their team. They should have a solid understanding and appreciation of company goals.
Managers of supply chains are responsible for monitoring the environmental performance and distribution partners. They may need to investigate the carbon footprint of their storage and transportation providers. They will need to be aware of key performance indicators (KPIs) in the supply chain, and be able develop solutions to any issues. They will need to look for ways to cut costs, including shipping and delivery.
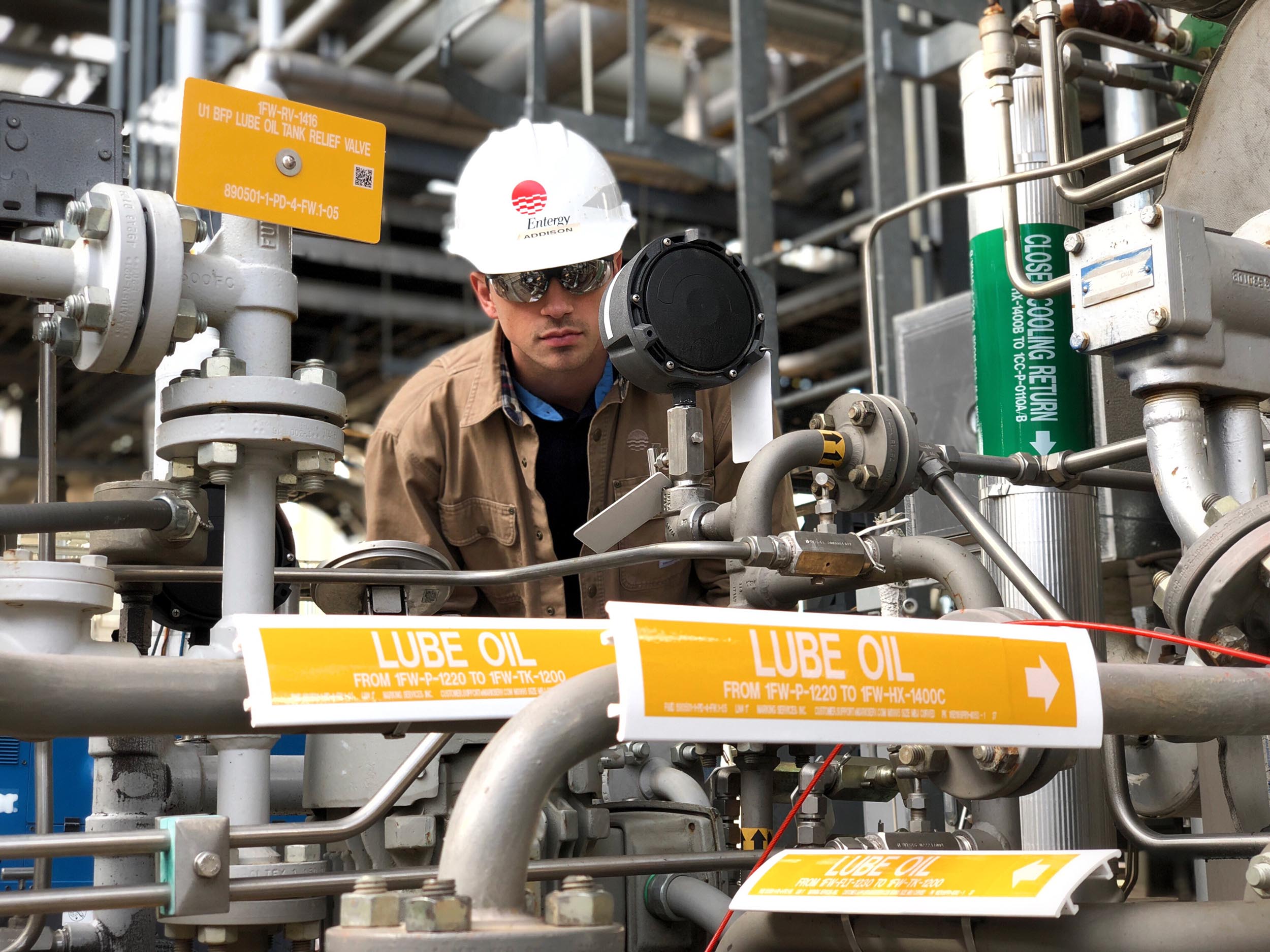
Managers of supply chain work in teams. They coordinate the work and activities of these teams. They are also responsible for training new employees. They should have experience in purchasing, transportation, and manufacturing.
FAQ
Can certain manufacturing steps be automated?
Yes! Yes! Automation has existed since ancient times. The wheel was invented by the Egyptians thousands of years ago. Robots are now used to assist us in assembly lines.
Robotics is used in many manufacturing processes today. These include:
-
Assembly line robots
-
Robot welding
-
Robot painting
-
Robotics inspection
-
Robots that make products
Automation can be applied to manufacturing in many other ways. 3D printing makes it possible to produce custom products in a matter of days or weeks.
What skills does a production planner need?
To become a successful production planner, you need to be organized, flexible, and able to multitask. Also, you must be able and willing to communicate with clients and coworkers.
What are the 7 Rs of logistics?
The acronym "7R's" of Logistics stands for seven principles that underpin logistics management. It was developed by the International Association of Business Logisticians (IABL) and published in 2004 as part of its "Seven Principles of Logistics Management" series.
The acronym consists of the following letters:
-
Responsible - ensure that all actions taken are within legal requirements and are not harmful to others.
-
Reliable - You can have confidence that you will fulfill your promises.
-
It is reasonable to use resources efficiently and not waste them.
-
Realistic - consider all aspects of operations, including cost-effectiveness and environmental impact.
-
Respectful – Treat others fairly and equitably.
-
Responsive - Look for ways to save time and increase productivity.
-
Recognizable: Provide customers with value-added service
What are my options for learning more about manufacturing
Practical experience is the best way of learning about manufacturing. If that is not possible, you could always read books or view educational videos.
Statistics
- According to the United Nations Industrial Development Organization (UNIDO), China is the top manufacturer worldwide by 2019 output, producing 28.7% of the total global manufacturing output, followed by the United States, Japan, Germany, and India.[52][53] (en.wikipedia.org)
- It's estimated that 10.8% of the U.S. GDP in 2020 was contributed to manufacturing. (investopedia.com)
- Job #1 is delivering the ordered product according to specifications: color, size, brand, and quantity. (netsuite.com)
- You can multiply the result by 100 to get the total percent of monthly overhead. (investopedia.com)
- In the United States, for example, manufacturing makes up 15% of the economic output. (twi-global.com)
External Links
How To
Six Sigma: How to Use it in Manufacturing
Six Sigma is defined as "the application of statistical process control (SPC) techniques to achieve continuous improvement." Motorola's Quality Improvement Department, Tokyo, Japan, developed it in 1986. Six Sigma's basic concept is to improve quality and eliminate defects through standardization. Since there are no perfect products, or services, this approach has been adopted by many companies over the years. Six Sigma's main objective is to reduce variations from the production average. This means that if you take a sample of your product, then measure its performance against the average, you can find out what percentage of the time the process deviates from the norm. If you notice a large deviation, then it is time to fix it.
Understanding how variability works in your company is the first step to Six Sigma. Once you've understood that, you'll want to identify sources of variation. These variations can also be classified as random or systematic. Random variations are caused when people make mistakes. While systematic variations are caused outside of the process, they can occur. You could consider random variations if some widgets fall off the assembly lines. It would be considered a systematic problem if every widget that you build falls apart at the same location each time.
After identifying the problem areas, you will need to devise solutions. This could mean changing your approach or redesigning the entire process. After implementing the new changes, you should test them again to see if they worked. If they don't work you need to rework them and come up a better plan.