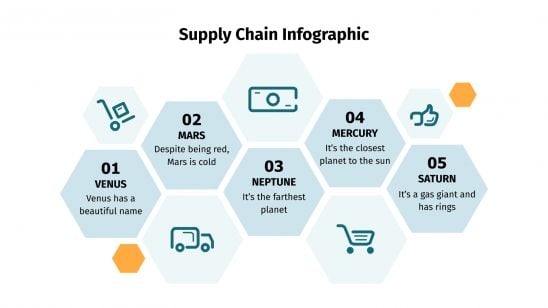
Heijunka, originally created by Toyota in Japan, is a lean production process that improves efficiency in multistep production processes. It reduces the amount of waste in the production process by ensuring that the production schedule is consistent with customer demand. This reduces production fluctuations and helps to reduce waste. Heijunka helps manufacturers meet customer demand and improve profits.
Heijunka is the process of coordinating small production batches across manufacturing line lines. It's used to improve efficiency when multi-step production is being done, particularly when just-in time principles are used. It is also part of Toyota Production System. It reduces waste by leveling production and mixing products. Also, it minimizes batch sizes.
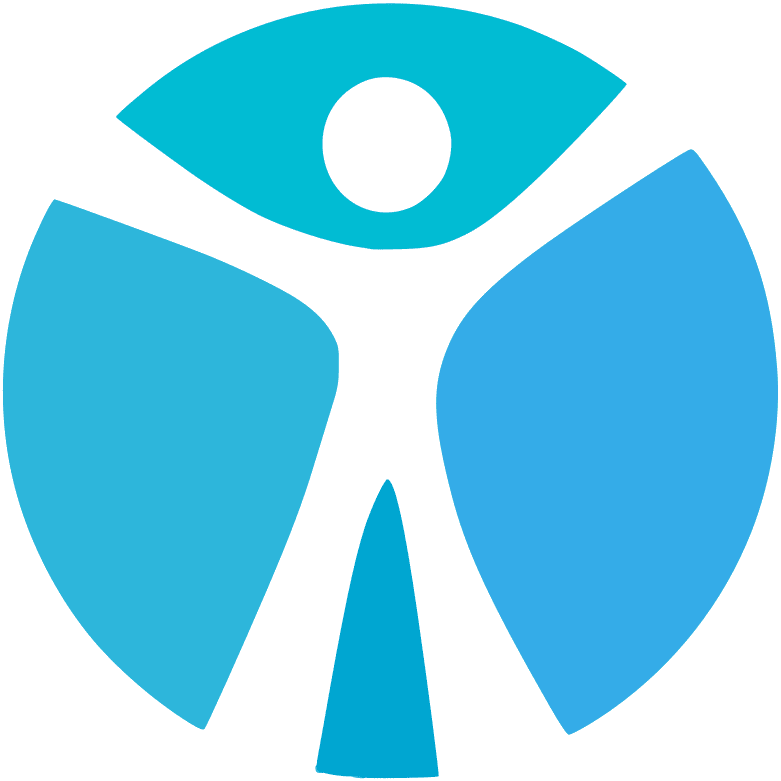
There are two ways you can implement Heijunka. One of them is using a heijunka box, which is a grid of small boxes that are fixed or mounted on a wall. It is a visual management tool that allows production personnel to schedule and visualize the production process. Magnetic cards can also be used to implement Heijunka.
Toyota dealers use Heijunka to increase their changeover time. It is also one of the key methods of the modern Lean framework developed by Toyota. In addition to achieving the necessary production speed, heijunka allows manufacturers to reduce inventory and improve their production. Heijunka allows for better utilization of equipment and labor. Heijunka promotes lean production systems that reduce waste and make better products.
The takt rate, also called the customer buying price, is essential in order to use heijunka. This is how long it takes to make a product that meets customer demand. Heijunka uses takt time as a way to control the production rate. The takt time can be used to determine how much product you need to produce and how fast customers will purchase your products. The takttime can also be used in back-office settings to determine the customer's purchase pace.
Production personnel can visual plan and schedule the production process with the help of the heijunkabox. The heijunka is also useful for shop floor visualizations of the production process. Each component or product type is represented in the heijunka by a series of columns and rows. The column of boxes represents each time period of the day, and the rows of boxes represent each product type.
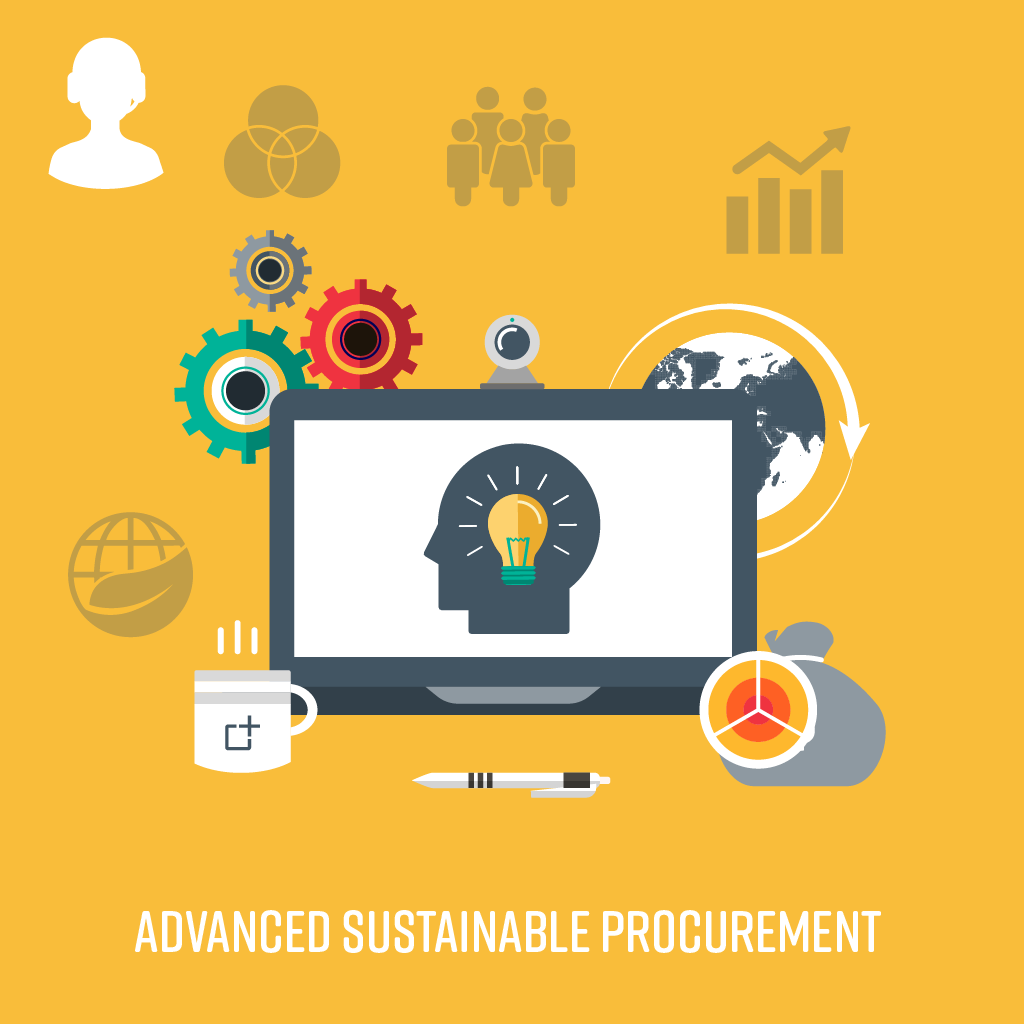
Heijunka Box (or Heijunka Box) is one of most commonly used visual management tools in manufacturing. This tool shows the relationships between component, product and production. This tool also shows the weekly production schedule. It is used together with the kanban deck, which is a set of colored cards that represents the product required for each production step. Kanban card are usually removed from the heijunka box within a given time frame and delivered to the designated production area.
FAQ
What are the 7 R's of logistics?
The acronym "7R's" of Logistics stands for seven principles that underpin logistics management. It was published in 2004 by the International Association of Business Logisticians as part of their "Seven Principles of Logistics Management" series.
The following letters form the acronym:
-
Responsible - ensure that actions are in compliance with legal requirements and do not cause harm to others.
-
Reliable - You can have confidence that you will fulfill your promises.
-
It is reasonable to use resources efficiently and not waste them.
-
Realistic – Consider all aspects, including cost-effectiveness as well as environmental impact.
-
Respectful: Treat others with fairness and equity
-
You are resourceful and look for ways to save money while increasing productivity.
-
Recognizable: Provide customers with value-added service
What are the responsibilities of a logistic manager?
Logistics managers make sure all goods are delivered on schedule and without damage. This is done by using his/her experience and knowledge of the company's products. He/she should ensure that sufficient stock is available in order to meet customer demand.
Is automation important in manufacturing?
Automation is important not only for manufacturers but also for service providers. They can provide services more quickly and efficiently thanks to automation. It helps them to lower costs by reducing human errors, and improving productivity.
What are the main products of logistics?
Logistics are the activities involved in moving goods from point A to point B.
They include all aspects of transport, including packaging, loading, transporting, unloading, storing, warehousing, inventory management, customer service, distribution, returns, and recycling.
Logisticians ensure that the product is delivered to the correct place, at the right time, and under safe conditions. Logisticians help companies improve their supply chain efficiency by providing information about demand forecasts and stock levels, production schedules, as well as availability of raw materials.
They also keep track of shipments in transit, monitor quality standards, perform inventories and order replenishment, coordinate with suppliers and vendors, and provide support services for sales and marketing.
What is the best way to learn about manufacturing?
Practical experience is the best way of learning about manufacturing. If that is not possible, you could always read books or view educational videos.
What is the difference between Production Planning, Scheduling and Production Planning?
Production Planning (PP) is the process of determining what needs to be produced at any given point in time. This is accomplished by forecasting the demand and identifying production resources.
Scheduling refers to the process of allocating specific dates to tasks in order that they can be completed within a specified timeframe.
What does warehouse refer to?
A warehouse or storage facility is where goods are stored before they are sold. It can be indoors or out. It could be one or both.
Statistics
- [54][55] These are the top 50 countries by the total value of manufacturing output in US dollars for its noted year according to World Bank.[56] (en.wikipedia.org)
- (2:04) MTO is a production technique wherein products are customized according to customer specifications, and production only starts after an order is received. (oracle.com)
- In the United States, for example, manufacturing makes up 15% of the economic output. (twi-global.com)
- In 2021, an estimated 12.1 million Americans work in the manufacturing sector.6 (investopedia.com)
- You can multiply the result by 100 to get the total percent of monthly overhead. (investopedia.com)
External Links
How To
How to Use 5S to Increase Productivity in Manufacturing
5S stands to stand for "Sort", “Set In Order", “Standardize", and "Store". Toyota Motor Corporation invented the 5S strategy in 1954. It helps companies achieve higher levels of efficiency by improving their work environment.
The idea behind standardizing production processes is to make them repeatable and measurable. This means that daily tasks such as cleaning and sorting, storage, packing, labeling, and packaging are possible. Through these actions, workers can perform their jobs more efficiently because they know what to expect from them.
There are five steps that you need to follow in order to implement 5S. Each step requires a different action to increase efficiency. By sorting, for example, you make it easy to find the items later. When you arrange items, you place them together. After you have divided your inventory into groups you can store them in easy-to-reach containers. You can also label your containers to ensure everything is properly labeled.
Employees need to reflect on how they do their jobs. Employees must understand why they do certain tasks and decide if there's another way to accomplish them without relying on the old ways of doing things. To implement the 5S system, employees must acquire new skills and techniques.
In addition to increasing efficiency, the 5S method also improves morale and teamwork among employees. They will feel motivated to strive for higher levels of efficiency once they start to see results.