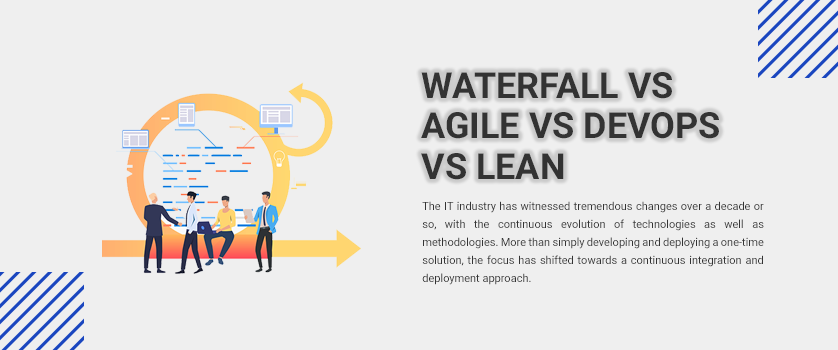
It's easy to overlook the fact that many things are still made in America, especially when globalization has forced factories out of the country. From popular candy to reliable vehicles and some of the nation's most beloved beers, there are plenty of products made in the United States that people love and use.
How to Find American-Made Items
Made in America is one of the most powerful labels in business. It evokes patriotism, and a promise of quality that's not spoken. It's a sign that the company is ensuring the safety of its workers and the future of its country.
The labeling process is equally important. The Federal Trade Commission sets strict guidelines for how manufacturers use this phrase.
A product cannot claim to be manufactured in the United States, unless every part, processing and labor involved in its production are sourced from the United States. A manufacturer may make a qualified claim to let consumers know, however that the item was made in America, but from only certain parts.
Julia Solomon Ensor from the FTC said that some companies that advertise “Made in the USA” may not have satisfied all of these criteria. This is particularly true for products like gas grills that are assembled and shipped in the United States, but then sent to a distributor in another country.
The Federal Trade Commission is cracking down on companies that boast "Made in the USA" claims but that do not meet these requirements. The agency says that the terms used must be clearly defined, and they must include all the components in the product.
Searching for items that were made in the United States can be done by both category and country. You can narrow your search based on country of origin if, for example, you're looking to buy bedding or furniture.
If you're searching for a particular item, you can enter the name or company into the search box to find out if the product is manufactured in the United States. It's a good way to tell companies that you care about American manufacturing.
You can check out the Made in the USA page from a website like Wayfair. The company does a good job of labeling the product by its country of origin. They have an entire section dedicated to US-made items.
It's not hard to find items that are made in the United States on their websites, but if you have any questions or concerns about a specific item, you can always contact them through our link and ask! They'll get back to you as soon as possible.
It's worth checking these retailers out to see if you can find something you need for your home, whether it's clothing, toys, books, or anything else. There are over 500 "Made in USA" products on their website, making it a great starting point for your search.
FAQ
How can manufacturing reduce production bottlenecks?
Production bottlenecks can be avoided by ensuring that processes are running smoothly during the entire production process, starting with the receipt of an order and ending when the product ships.
This includes planning to meet capacity requirements and quality control.
Continuous improvement techniques like Six Sigma are the best way to achieve this.
Six Sigma management is a system that improves quality and reduces waste within your organization.
It seeks to eliminate variation and create consistency in your work.
How can excess manufacturing production be reduced?
Improved inventory management is the key to reducing overproduction. This would reduce the time spent on unproductive activities like purchasing, storing and maintaining excess stock. This will allow us to free up resources for more productive tasks.
A Kanban system is one way to achieve this. A Kanban board, a visual display to show the progress of work, is called a Kanban board. Kanban systems are where work items travel through a series of states until reaching their final destination. Each state represents a different priority.
When work is completed, it can be transferred to the next stage. If a task is still in its beginning stages, it will continue to be so until it reaches the end.
This allows for work to continue moving forward, while also ensuring that there is no work left behind. Managers can view the Kanban board to see how much work they have done. This information allows them to adjust their workflow based on real-time data.
Lean manufacturing, another method to control inventory levels, is also an option. Lean manufacturing emphasizes eliminating waste in all phases of production. Any product that isn't adding value can be considered waste. The following are examples of common waste types:
-
Overproduction
-
Inventory
-
Packaging that is not necessary
-
Exceed materials
These ideas can help manufacturers improve efficiency and reduce costs.
What does it mean to warehouse?
A warehouse, or storage facility, is where goods are stored prior to being sold. It can be an indoor space or an outdoor area. In some cases it could be both indoors and outdoors.
Statistics
- (2:04) MTO is a production technique wherein products are customized according to customer specifications, and production only starts after an order is received. (oracle.com)
- According to a Statista study, U.S. businesses spent $1.63 trillion on logistics in 2019, moving goods from origin to end user through various supply chain network segments. (netsuite.com)
- [54][55] These are the top 50 countries by the total value of manufacturing output in US dollars for its noted year according to World Bank.[56] (en.wikipedia.org)
- According to the United Nations Industrial Development Organization (UNIDO), China is the top manufacturer worldwide by 2019 output, producing 28.7% of the total global manufacturing output, followed by the United States, Japan, Germany, and India.[52][53] (en.wikipedia.org)
- In 2021, an estimated 12.1 million Americans work in the manufacturing sector.6 (investopedia.com)
External Links
How To
How to use the Just-In Time Method in Production
Just-intime (JIT), a method used to lower costs and improve efficiency in business processes, is called just-in-time. This is where you have the right resources at the right time. This means that your only pay for the resources you actually use. Frederick Taylor developed the concept while working as foreman in early 1900s. After observing how workers were paid overtime for late work, he realized that overtime was a common practice. He decided to ensure workers have enough time to do their jobs before starting work to improve productivity.
JIT is a way to plan ahead and make sure you don't waste any money. You should also look at the entire project from start to finish and make sure that you have sufficient resources available to deal with any problems that arise during the course of your project. If you anticipate that there might be problems, you'll have enough people and equipment to fix them. This way you won't be spending more on things that aren’t really needed.
There are many JIT methods.
-
Demand-driven: This is a type of JIT where you order the parts/materials needed for your project regularly. This will allow to track how much material has been used up. It will also allow you to predict how long it takes to produce more.
-
Inventory-based: This allows you to store the materials necessary for your projects in advance. This allows one to predict how much they will sell.
-
Project-driven: This method allows you to set aside enough funds for your project. You will be able to purchase the right amount of materials if you know what you need.
-
Resource-based: This is the most common form of JIT. Here, you allocate certain resources based on demand. If you have many orders, you will assign more people to manage them. If there aren't many orders, you will assign fewer people.
-
Cost-based: This approach is very similar to resource-based. However, you don't just care about the number of people you have; you also need to consider how much each person will cost.
-
Price-based: This approach is very similar to the cost-based method except that you don't look at individual workers costs but the total cost of the company.
-
Material-based is an alternative to cost-based. Instead of looking at the total cost in the company, this method focuses on the average amount of raw materials that you consume.
-
Time-based JIT: This is another variant of resource-based JIT. Instead of worrying about how much each worker costs, you can focus on how long the project takes.
-
Quality-based JIT: This is another variation of resource based JIT. Instead of looking at the labor costs and time it takes to make a product, think about its quality.
-
Value-based JIT is the newest form of JIT. In this instance, you are not concerned about the product's performance or meeting customer expectations. Instead, you are focused on adding value to the marketplace.
-
Stock-based: This inventory-based approach focuses on how many items are being produced at any one time. This is used to increase production and minimize inventory.
-
Just-intime (JIT), planning is a combination JIT management and supply chain management. It refers to the process of scheduling the delivery of components as soon as they are ordered. It reduces lead times and improves throughput.