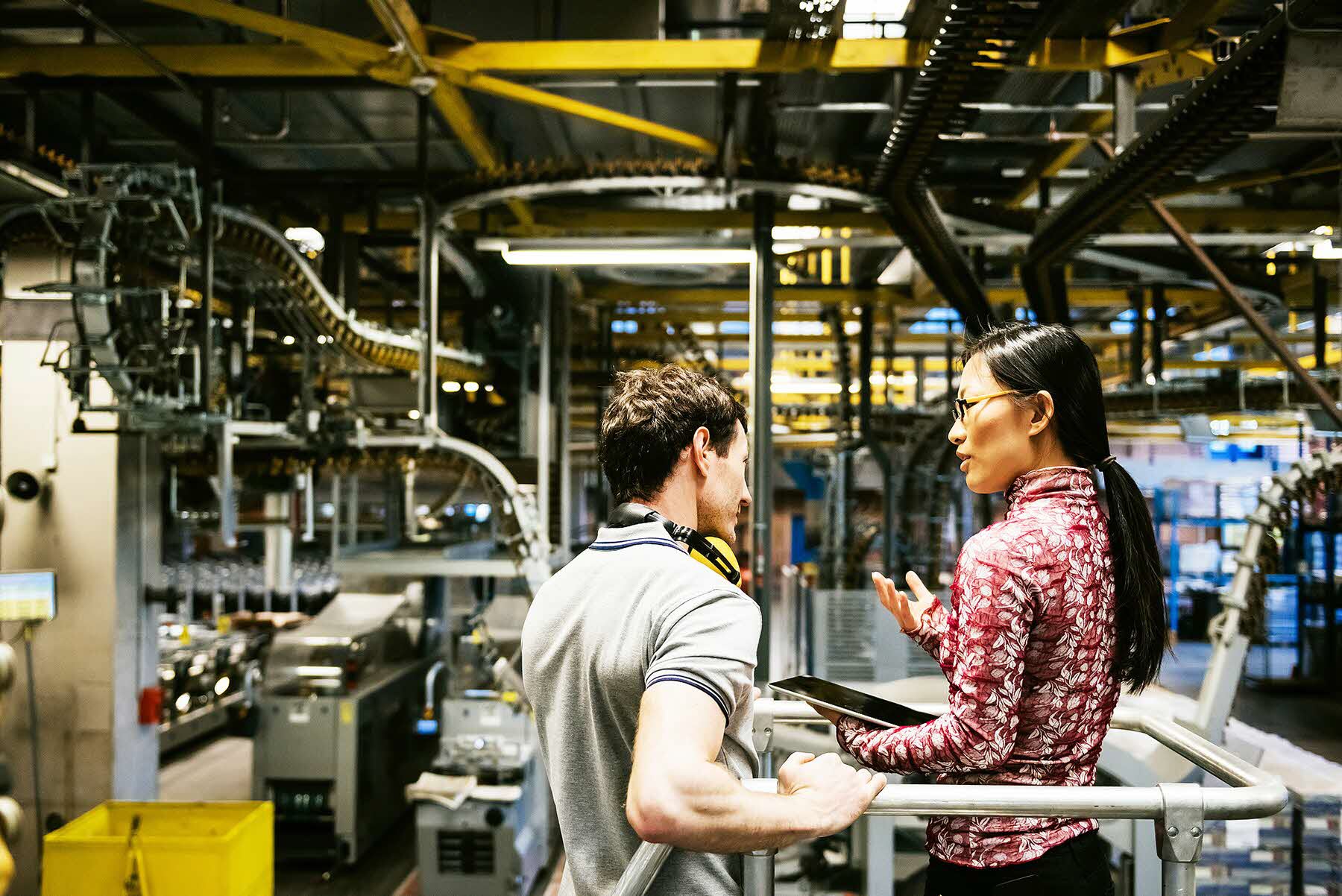
CEVA Logistics provides logistics services. These logistics companies offer many benefits to employees, whether you are looking for a career change or simply want to find a new job. These companies offer a variety of benefits to their employees. Here are the steps you need to take in order for you apply for a job as a logistics professional. You can search for jobs by region.
Job description
CEVA Logistics offers a range of jobs that are open to people with different education levels and work experience. The company's core values include customer service dedication and timely delivery. The company is looking for people who are enthusiastic about logistics and are willing to work hard. Candidates who have some or no previous experience in logistics and who have a positive attitude will be given preference when applying for a job.
CEVA Logistics is seeking a Process/Industrial Engineer to design and implement new processes and improve efficiency. The ideal candidate should be energetic and self-motivated. They must also be able to work in collaboration with staff at the plant. This includes managing projects, designing and implementing process layouts, and applying analytical and modeling skills. To improve quality and efficiency, they must be proficient in robotics and other manufacturing processes.
Education required
CEVA Logistics offers a variety of job opportunities for applicants interested in working as a warehouse manager or sales rep. They have the option to become operations managers, which involves managing the day-today operations, including inventory scheduling and customer service. Many of these positions have a team under them. Candidates for these positions usually have a bachelor’s degree in logistics, supervisory and strong leadership and management skills.
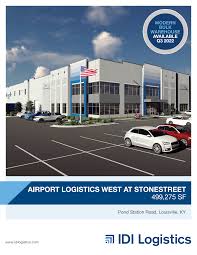
You can apply online, or through recruiters, if you are interested. Candidates must first create a profile on the company's career portal to apply online. They can use their LinkedIn accounts to connect to their profile, attach their resumes, and input relevant information. Once their profile has been completed, they are able to choose their preferred country and get in contact with a recruiter.
Salary range
If you are interested in applying for a CEVA Logistics career, the first thing to do is create a profile at the company's online job portal. This allows to link with your LinkedIn profile, upload your resume, and allow you to create a job application. You can also input details about your work experience, skills, or other pertinent information. Next, select the country or region in which you would like to work. You'll then receive contact information for a recruiter in the region.
CEVA Logistics salaries vary depending on job title and experience. A Vice President at CEVA Logistics is paid $166,000 per year, while an Air Break Bulk Specialist receives $24,000. But, the economic climate in each region can mean that salaries may vary.
Locations
CEVA Logistics is a great place to start a career in logistics. The company has a number of different positions, each with its own responsibilities and qualifications. You can apply for a job by entering the job title and location in the search box. You can search for Edison job listings. You will need experience driving and be able and able to communicate with both internal and external customers.
CEVA Logistics offers many career opportunities, including supervisory positions. Supervisors manage the company's day-to-day operations. Supervisors manage inventory, coordinate schedules, oversee employees' activities, and monitor their performance. Operations supervisors usually have a team reporting to them and require a bachelor’s degree or related experience. You will also need strong leadership and management skills.
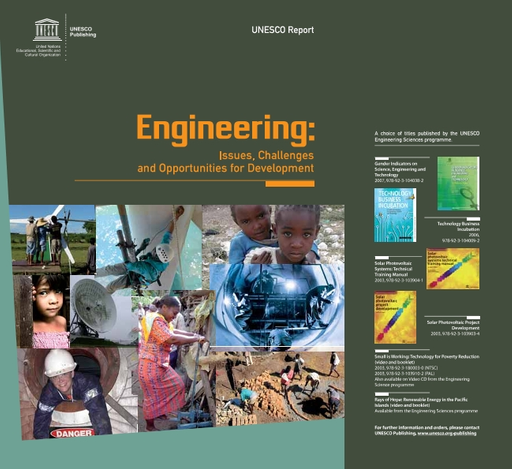
Online application
CEVA Logistics offers a variety of jobs for people looking for work in logistics. Ceva Logistics is an international company that was created in 2006 through the merger two Australian and Texan logistics companies. Its operations are now located in more than 950 countries. Job seekers are eligible to apply for either full-time or partial-time positions.
Although many positions at CEVA do require some experience, most are entry-level. Others require minimal to moderate experience. Customer service representative, dispatcher, and admin clerk are some of the entry-level jobs.
FAQ
Is there anything we should know about Manufacturing Processes prior to learning about Logistics.
No. No. But, being familiar with manufacturing processes will give you a better understanding about how logistics works.
What is production planning?
Production Planning involves developing a plan for all aspects of the production, including scheduling, budgeting, casting, crew, location, equipment, props, etc. It is important to have everything ready and planned before you start shooting. This document should also include information on how to get the best result on set. It should include information about shooting locations, casting lists, crew details, equipment requirements, and shooting schedules.
The first step is to outline what you want to film. You may have already decided where you would like to shoot, or maybe there are specific locations or sets that you want to use. Once you have identified your locations and scenes it's time to begin figuring out what elements you will need for each one. You might decide you need a car, but not sure what make or model. If this is the case, you might start searching online for car models and then narrow your options by selecting from different makes.
After you have selected the car you want, you can begin to think about additional features. Are you looking for people to sit in the front seats? Perhaps you have someone who needs to be able to walk around the back of your car. You may want to change the interior's color from black or white. These questions will help guide you in determining the ideal look and feel for your car. You can also think about the type of shots you want to get. Will you be filming close-ups or wide angles? Maybe you want the engine or the steering wheels to be shown. This will allow you to determine the type of car you want.
Once you have determined all of the above, you can move on to creating a schedule. You will know when you should start and when you should finish shooting. The schedule will show you when to get there, what time to leave, and when to return home. This way, everyone knows what they need to do and when. If you need to hire extra staff, you can make sure you book them in advance. You should not hire anyone who doesn't show up because of your inaction.
Your schedule will also have to be adjusted to reflect the number of days required to film. Some projects only take one or two days, while others may last weeks. When creating your schedule, be aware of whether you need more shots per day. Multiple shots at the same location can increase costs and make it more difficult to complete. It's better to be safe than sorry and shoot less takes if you're not certain whether you need more takes.
Budgeting is another crucial aspect of production plan. A realistic budget will help you work within your means. Remember that you can always reduce the budget later on if you run into unforeseen problems. You shouldn't underestimate the amount you'll spend. If you underestimate how much something costs, you'll have less money to pay for other items.
Production planning is a detailed process. But, once you understand the workings of everything, it becomes easier for future projects to be planned.
What are the responsibilities for a manufacturing manager
A manufacturing manager must make sure that all manufacturing processes run smoothly and effectively. They should also be aware of any problems within the company and act accordingly.
They should also learn how to communicate effectively with other departments, including sales and marketing.
They should be up to date on the latest trends and be able apply this knowledge to increase productivity and efficiency.
What are the 4 types manufacturing?
Manufacturing refers the process of turning raw materials into useful products with machines and processes. Manufacturing involves many activities, including designing, building, testing and packaging, shipping, selling, service, and so on.
How can I find out more about manufacturing?
Experience is the best way for you to learn about manufacturing. However, if that's not possible, you can always read books or watch educational videos.
Statistics
- According to the United Nations Industrial Development Organization (UNIDO), China is the top manufacturer worldwide by 2019 output, producing 28.7% of the total global manufacturing output, followed by the United States, Japan, Germany, and India.[52][53] (en.wikipedia.org)
- Many factories witnessed a 30% increase in output due to the shift to electric motors. (en.wikipedia.org)
- According to a Statista study, U.S. businesses spent $1.63 trillion on logistics in 2019, moving goods from origin to end user through various supply chain network segments. (netsuite.com)
- In the United States, for example, manufacturing makes up 15% of the economic output. (twi-global.com)
- Job #1 is delivering the ordered product according to specifications: color, size, brand, and quantity. (netsuite.com)
External Links
How To
How to use the Just In-Time Production Method
Just-intime (JIT), which is a method to minimize costs and maximize efficiency in business process, is one way. This is where you have the right resources at the right time. This means that you only pay for what you actually use. The term was first coined by Frederick Taylor, who developed his theory while working as a foreman in the early 1900s. He saw how overtime was paid to workers for work that was delayed. He then concluded that if he could ensure that workers had enough time to do their job before starting to work, this would improve productivity.
JIT is a way to plan ahead and make sure you don't waste any money. The entire project should be looked at from start to finish. You need to ensure you have enough resources to tackle any issues that might arise. You'll be prepared to handle any potential problems if you know in advance. This way, you won't end up paying extra money for things that weren't really necessary.
There are many types of JIT methods.
-
Demand-driven: This is a type of JIT where you order the parts/materials needed for your project regularly. This will let you track the amount of material left over after you've used it. You'll also be able to estimate how long it will take to produce more.
-
Inventory-based : You can stock the materials you need in advance. This allows you predict the amount you can expect to sell.
-
Project-driven : This is a method where you make sure that enough money is set aside to pay the project's cost. Knowing how much money you have available will help you purchase the correct amount of materials.
-
Resource-based JIT : This is probably the most popular type of JIT. Here, you allocate certain resources based on demand. If you have many orders, you will assign more people to manage them. You'll have fewer orders if you have fewer.
-
Cost-based: This is the same as resource-based except that you don't care how many people there are but how much each one of them costs.
-
Price-based pricing: This is similar in concept to cost-based but instead you look at how much each worker costs, it looks at the overall company's price.
-
Material-based - This is a variant of cost-based. But instead of looking at the total company cost, you focus on how much raw material you spend per year.
-
Time-based JIT is another form of resource-based JIT. Instead of worrying about how much each worker costs, you can focus on how long the project takes.
-
Quality-based JIT is another variant of resource-based JIT. Instead of thinking about how much each employee costs or how long it takes to manufacture something, you think about how good the quality of your product is.
-
Value-based JIT is the newest form of JIT. This is where you don't care about how the products perform or whether they meet customers' expectations. Instead, your focus is on the value you bring to the market.
-
Stock-based: This stock-based method focuses on the actual quantity of products being made at any given time. This is used to increase production and minimize inventory.
-
Just-intime (JIT), planning is a combination JIT management and supply chain management. This refers to the scheduling of the delivery of components as soon after they are ordered. It's important as it reduces leadtimes and increases throughput.