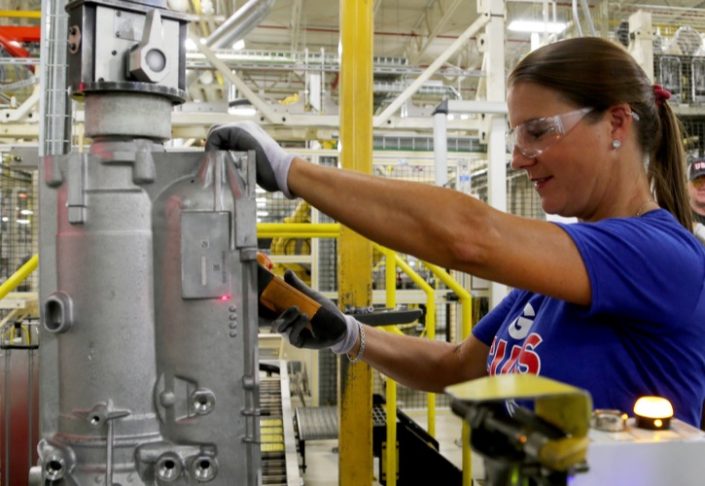
If you're interested in a career in supply chain, you can look into a supply chain entry level salary. One such position is dispatcher. CPSM certification is an additional credential which goes beyond the ASCM standards. CPSM certification is an option if you are interested in a higher starting wage.
CPSM certification, which is a credential that surpasses the ASCM standard, is a credential.
The CPSM certification provides supply chain professionals the tools to address the complex demands of modern supply chains. It is administered through the Institute for Supply Management. The certification requires you to pass three tests and work in supply chains for five years. You will need to complete 60 hours of continuing education in order to keep your CPSM Certification.
Many employers are seeking a CPSM certificate. This credential gives you a better chance of passing than those without it. The CSCP exam typically takes between three and six months to complete. It's a great tool to demonstrate your knowledge in supply chain management, and also to help you get a job interview. Your certifications should be listed on your LinkedIn profile.
Obtaining a CPSM cert can open up opportunities for a higher salary than an ASCM entry-level job. Having a CPSM certifies that you have a solid understanding of supply chain operations, and can work with the organization to achieve their goals.
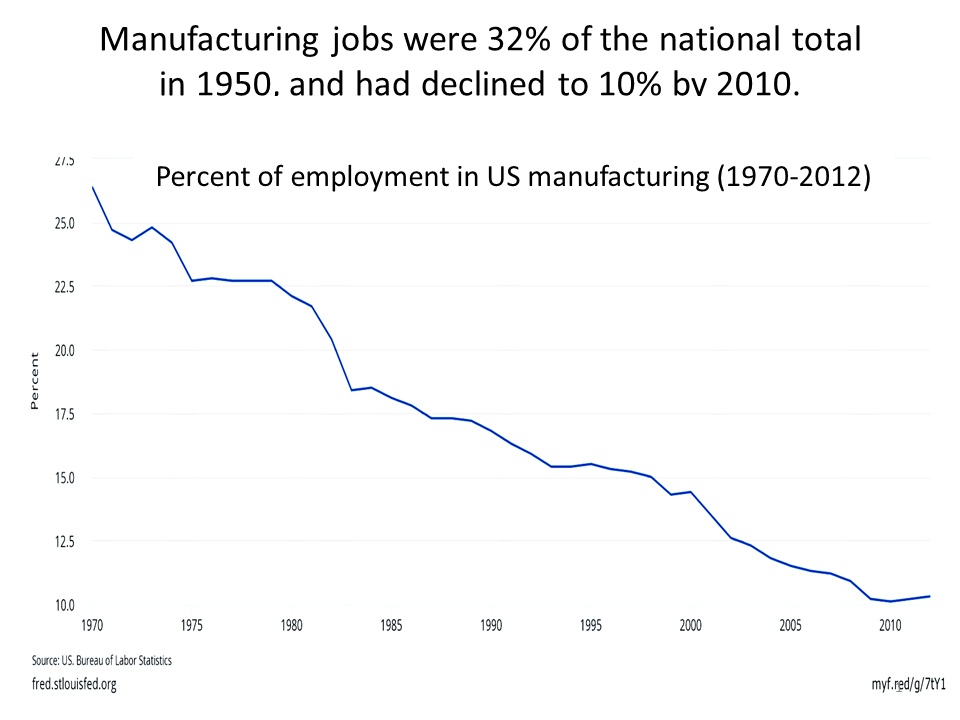
FAQ
What does it take to run a logistics business?
It takes a lot of skills and knowledge to run a successful logistics business. You must have good communication skills to interact effectively with your clients and suppliers. You must be able analyze data and draw out conclusions. You need to be able work under pressure and manage stressful situations. To improve efficiency, you must be innovative and creative. You need to have strong leadership qualities to motivate team members and direct them towards achieving organizational goals.
To meet tight deadlines, you must also be efficient and organized.
What can I do to learn more about manufacturing?
The best way to learn about manufacturing is through hands-on experience. If that is not possible, you could always read books or view educational videos.
Is there anything we should know about Manufacturing Processes prior to learning about Logistics.
No. No. It is important to know about the manufacturing processes in order to understand how logistics works.
What does "warehouse" mean?
Warehouses and storage facilities are where goods are kept before being sold. You can have it indoors or outdoors. It could be one or both.
What is the importance of automation in manufacturing?
Automating is not just important for manufacturers, but also for service providers. It enables them to provide services faster and more efficiently. They can also reduce their costs by reducing human error and improving productivity.
What are the logistics products?
Logistics refers to the movement of goods from one place to another.
They include all aspects of transport, including packaging, loading, transporting, unloading, storing, warehousing, inventory management, customer service, distribution, returns, and recycling.
Logisticians ensure that the product is delivered to the correct place, at the right time, and under safe conditions. Logisticians help companies improve their supply chain efficiency by providing information about demand forecasts and stock levels, production schedules, as well as availability of raw materials.
They monitor shipments in transit, ensure quality standards, manage inventories, replenish orders, coordinate with suppliers and other vendors, and offer support services for sales, marketing, and customer service.
How can we improve manufacturing efficiency?
The first step is to determine the key factors that impact production time. Next, we must find ways to improve those factors. If you don’t know where to begin, consider which factors have the largest impact on production times. Once you have identified them, it is time to identify solutions.
Statistics
- You can multiply the result by 100 to get the total percent of monthly overhead. (investopedia.com)
- According to the United Nations Industrial Development Organization (UNIDO), China is the top manufacturer worldwide by 2019 output, producing 28.7% of the total global manufacturing output, followed by the United States, Japan, Germany, and India.[52][53] (en.wikipedia.org)
- It's estimated that 10.8% of the U.S. GDP in 2020 was contributed to manufacturing. (investopedia.com)
- Job #1 is delivering the ordered product according to specifications: color, size, brand, and quantity. (netsuite.com)
- In the United States, for example, manufacturing makes up 15% of the economic output. (twi-global.com)
External Links
How To
How to use Lean Manufacturing in the production of goods
Lean manufacturing is a management system that aims at increasing efficiency and reducing waste. It was developed in Japan during the 1970s and 1980s by Taiichi Ohno, who received the Toyota Production System (TPS) award from TPS founder Kanji Toyoda. Michael L. Watkins published the original book on lean manufacturing, "The Machine That Changed the World," in 1990.
Lean manufacturing is often defined as a set of principles used to improve the quality, speed, and cost of products and services. It emphasizes eliminating waste and defects throughout the value stream. Just-in-time (JIT), zero defect (TPM), and 5S are all examples of lean manufacturing. Lean manufacturing focuses on eliminating non-value-added activities such as rework, inspection, and waiting.
Lean manufacturing is a way for companies to achieve their goals faster, improve product quality, and lower costs. Lean manufacturing has been deemed one of the best ways to manage the entire value-chain, including customers, distributors as well retailers and employees. Lean manufacturing can be found in many industries. Toyota's philosophy is a great example of this. It has helped to create success in automobiles as well electronics, appliances and healthcare.
Five basic principles of Lean Manufacturing are included in lean manufacturing
-
Define Value- Identify the added value your company brings to society. What makes you stand out from your competitors?
-
Reduce Waste - Remove any activity which doesn't add value to your supply chain.
-
Create Flow - Make sure work runs smoothly without interruptions.
-
Standardize and simplify – Make processes as repeatable and consistent as possible.
-
Building Relationships – Establish personal relationships with both external and internal stakeholders.
Lean manufacturing isn’t new, but it has seen a renewed interest since 2008 due to the global financial crisis. Many businesses have adopted lean production techniques to make them more competitive. Many economists believe lean manufacturing will play a major role in economic recovery.
Lean manufacturing, which has many benefits, is now a standard practice in the automotive industry. These include higher customer satisfaction, lower inventory levels, lower operating expenses, greater productivity, and improved overall safety.
The principles of lean manufacturing can be applied in almost any area of an organization. Because it makes sure that all value chains are efficient and effectively managed, Lean Manufacturing is particularly helpful for organizations.
There are three main types of lean manufacturing:
-
Just-in Time Manufacturing (JIT), also known as "pull system": This form of lean manufacturing is often referred to simply as "pull". JIT refers to a system in which components are assembled at the point of use instead of being produced ahead of time. This strategy aims to decrease lead times, increase availability of parts and reduce inventory.
-
Zero Defects Manufacturing - ZDM: ZDM focuses its efforts on making sure that no defective units leave a manufacturing facility. If a part is required to be repaired on the assembly line, it should not be scrapped. This also applies to finished products that need minor repairs before being shipped.
-
Continuous Improvement (CI), also known as Continuous Improvement, aims at improving the efficiency of operations through continuous identification and improvement to minimize or eliminate waste. Continuous improvement involves continuous improvement of processes and people as well as tools.