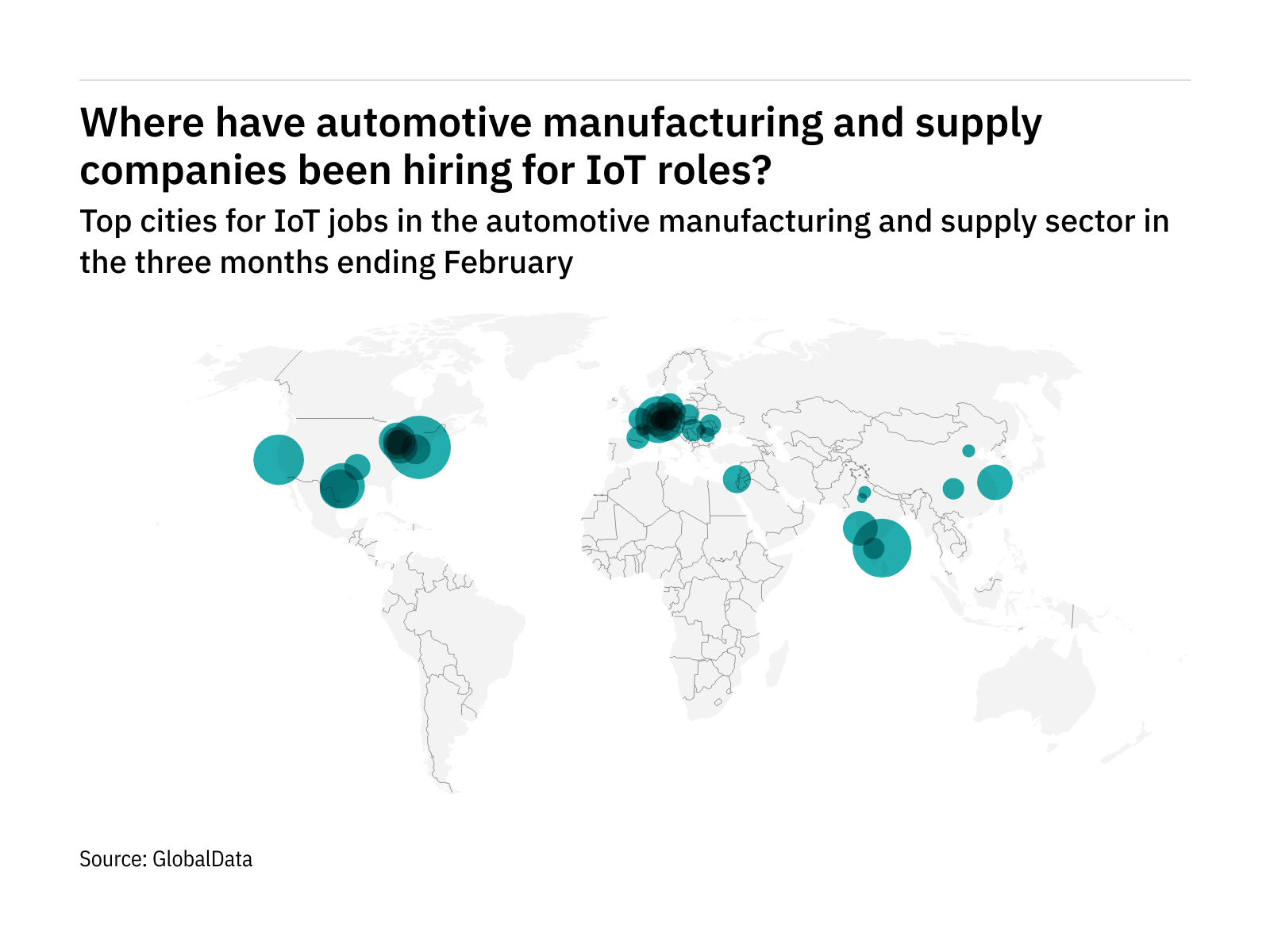
The United States is currently the third-largest manufacturer in the globe. Its manufacturing output reached a record high of $2.00 trillion in Q1 2018, nearly double what it was before the Great Recession. However, despite a strong domestic economy, the United States manufacturing industry is taking a shotgun approach to its current challenges. We need to be more aggressive in addressing the industry's challenges, regardless of whether this is due to a lack or skilled labor.
Since 2000, jobs have dropped by 5 million
The US has lost five million manufacturing jobs since 2000. Some claim that the rise of trade with China is to blame. However, only about a quarter the decline in manufacturing jobs can be attributed to this. In addition to trade with China, manufacturing jobs were lost in local markets that didn't compete with Chinese imports. But there are many factors that contributed to the decline of manufacturing jobs. Among the reasons cited are the following:
The US manufacturing sector has lost almost a third of its jobs over the past 20 years. It was 17,000,000 in 1965. By 2010, it had fallen to 12,000,000. Trade is not responsible for the decline in manufacturing jobs. However, it has been caused structural problems like a decline of capital investment, output, and productivity. These problems are not sustainable. Although productivity gains played a significant role in the decline of manufacturing jobs, they were not enough to compensate. Automation is the problem, and not productivity improvements.
Strong demand is for manufactured products
In the United States, the demand for manufactured goods remains strong despite the fact that the share of consumer spending on these items has decreased over the past few decades. In 1945, personal expenditures on durable goods accounted for 58% of total spending, compared to just 28% today. This is because the costs of manufacturing and selling durable goods have dropped, while the contents have increased. As a result, the cost of computers, televisions, and sound equipment has fallen significantly.
The US's recovery in manufacturing activity has resulted in an increase in the production of manufactured goods. The Fifth District Manufacturing Activity Survey shows that demand for manufactured goods is strong and production is ramping up, although supply chain bottlenecks are hampering output. The increased production has stressed supply chains. Respondents report that they have experienced supply chain disruptions that impact their ability keep adequate inventories. Backlogs of orders and vendor lead times have also increased.
Trade deficit in manufactured goods has more than doubled in the past decade
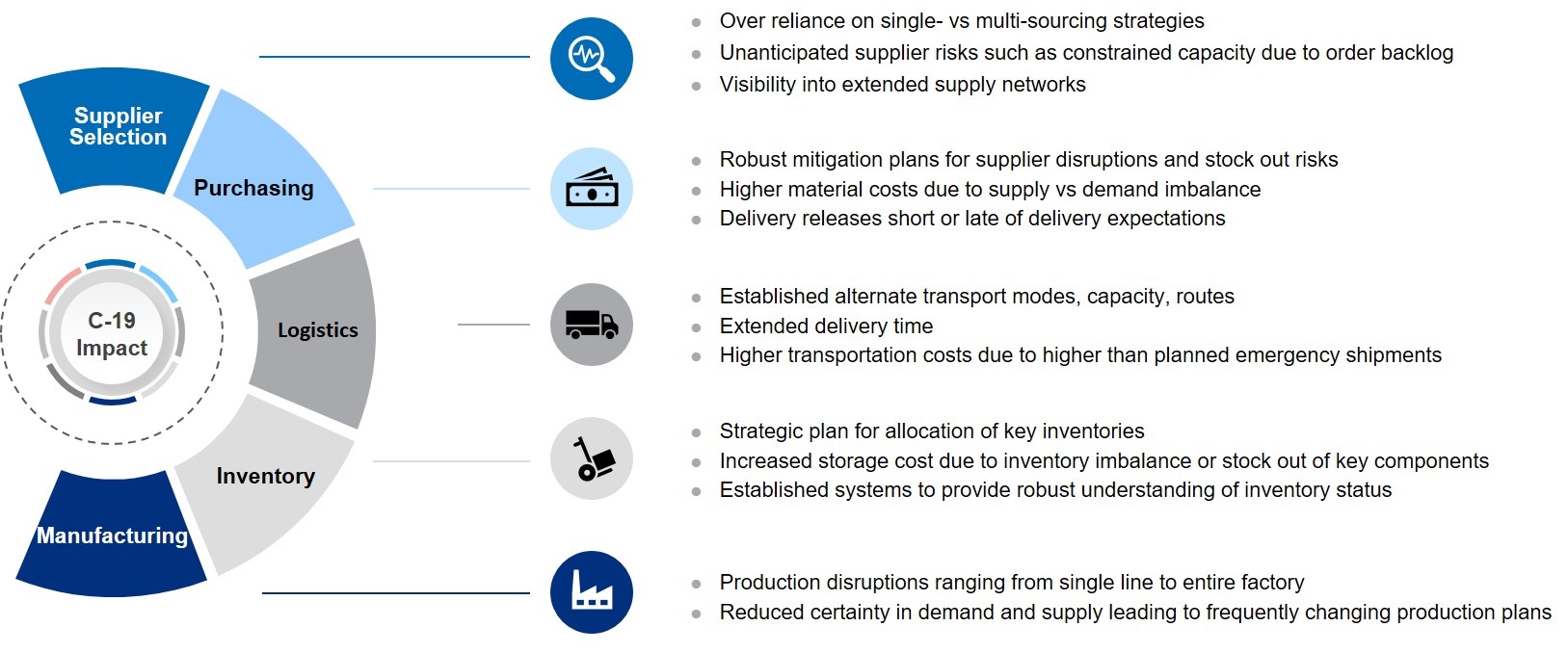
Economists are concerned that the U.S. trade surplus could lead to lower global growth and more instability among its trading partners. However, high imports from the USA of manufactured goods is not necessarily a problem for the U.S. economy. It is crucial to maintaining economic stability worldwide. The trade deficit may even be a necessary evil, since the U.S. relies heavily on foreign markets to generate its economic output, while high levels of foreign demand may make it difficult to achieve full employment.
Since 2000, the U.S. has almost doubled its trade deficit for manufactured goods. Partially, the US trade deficit in manufactured goods has doubled since 2000. The problem is even more severe: this imbalance is concentrated at the manufacturing sector, where wages are down and employment is declining since the 1990s. US manufacturing employment fell dramatically from 26% in 1970 to 8.5% in 2016. Some economists attribute the decline to China's increased competition, but most attribute the decline to automation, productivity increases, and demand shifting away from goods to services.
Industry follows a shotgun approach
The US has a variety of advanced manufacturing initiatives. It is also well-established in this area. But some countries are attempting to introduce the internet of things to manufacturing. The US, on other hand, is focused on different technologies and blends traditional mass media with Internet advertisement. This results in a shotgun approach where companies concentrate on different technologies and seek a wide customer base.
FAQ
Can certain manufacturing steps be automated?
Yes! Yes. Automation has been around since ancient time. The Egyptians discovered the wheel thousands and years ago. Nowadays, we use robots for assembly lines.
There are many applications for robotics in manufacturing today. These include:
-
Robots for assembly line
-
Robot welding
-
Robot painting
-
Robotics inspection
-
Robots that create products
Manufacturing could also benefit from automation in other ways. 3D printing is a way to make custom products quickly and without waiting weeks or months for them to be manufactured.
Why is logistics so important in manufacturing?
Logistics are an essential component of any business. They enable you to achieve outstanding results by helping manage product flow from raw materials through to finished goods.
Logistics are also important in reducing costs and improving efficiency.
What is the responsibility of a manufacturing manager?
The manufacturing manager should ensure that every manufacturing process is efficient and effective. They should be alert for any potential problems in the company and react accordingly.
They should also be able communicate with other departments, such as sales or marketing.
They should also be aware of the latest trends in their industry and be able to use this information to help improve productivity and efficiency.
How can manufacturing efficiency be improved?
The first step is to identify the most important factors affecting production time. The next step is to identify the most important factors that affect production time. If you don’t know how to start, look at which factors have the greatest impact upon production time. Once you've identified them all, find solutions to each one.
What are the products of logistics?
Logistics refers to the movement of goods from one place to another.
These include all aspects related to transport such as packaging, loading and transporting, storing, transporting, unloading and warehousing inventory management, customer service. Distribution, returns, recycling are some of the options.
Logisticians ensure that products reach the right destination at the right moment and under safe conditions. They provide information on demand forecasts as well stock levels, production schedules and availability of raw material.
They monitor shipments in transit, ensure quality standards, manage inventories, replenish orders, coordinate with suppliers and other vendors, and offer support services for sales, marketing, and customer service.
What is the job of a logistics manger?
A logistics manager makes sure that all goods are delivered on-time and in good condition. This is done using his/her knowledge of the company's products. He/she also needs to ensure adequate stock to meet demand.
What do you mean by warehouse?
A warehouse is a place where goods are stored until they are sold. It can be an outdoor or indoor area. Sometimes, it can be both an indoor and outdoor space.
Statistics
- Job #1 is delivering the ordered product according to specifications: color, size, brand, and quantity. (netsuite.com)
- It's estimated that 10.8% of the U.S. GDP in 2020 was contributed to manufacturing. (investopedia.com)
- According to a Statista study, U.S. businesses spent $1.63 trillion on logistics in 2019, moving goods from origin to end user through various supply chain network segments. (netsuite.com)
- According to the United Nations Industrial Development Organization (UNIDO), China is the top manufacturer worldwide by 2019 output, producing 28.7% of the total global manufacturing output, followed by the United States, Japan, Germany, and India.[52][53] (en.wikipedia.org)
- You can multiply the result by 100 to get the total percent of monthly overhead. (investopedia.com)
External Links
How To
How to Use Just-In-Time Production
Just-in-time is a way to cut costs and increase efficiency in business processes. This is where you have the right resources at the right time. This means that only what you use is charged to your account. Frederick Taylor, a 1900s foreman, first coined the term. Taylor observed that overtime was paid to workers if they were late in working. He realized that workers should have enough time to complete their jobs before they begin work. This would help increase productivity.
JIT is an acronym that means you need to plan ahead so you don’t waste your money. You should also look at the entire project from start to finish and make sure that you have sufficient resources available to deal with any problems that arise during the course of your project. If you expect problems to arise, you will be able to provide the necessary equipment and personnel to address them. This will prevent you from spending extra money on unnecessary things.
There are several types of JIT techniques:
-
Demand-driven JIT: You order the parts and materials you need for your project every other day. This will enable you to keep track of how much material is left after you use it. This will let you know how long it will be to produce more.
-
Inventory-based: You stock materials in advance to make your projects easier. This allows you to predict how much you can expect to sell.
-
Project-driven : This is a method where you make sure that enough money is set aside to pay the project's cost. If you know the amount you require, you can buy the materials you need.
-
Resource-based JIT: This type of JIT is most commonly used. Here you can allocate certain resources based purely on demand. You will, for example, assign more staff to deal with large orders. If you don't receive many orders, then you'll assign fewer employees to handle the load.
-
Cost-based: This is the same as resource-based except that you don't care how many people there are but how much each one of them costs.
-
Price-based: This approach is very similar to the cost-based method except that you don't look at individual workers costs but the total cost of the company.
-
Material-based - This is a variant of cost-based. But instead of looking at the total company cost, you focus on how much raw material you spend per year.
-
Time-based: This is another variation of resource-based JIT. Instead of focusing on how much each employee costs, you focus on how long it takes to complete the project.
-
Quality-based: This is yet another variation of resource-based JIT. Instead of looking at the labor costs and time it takes to make a product, think about its quality.
-
Value-based JIT: One of the most recent forms of JIT. You don't worry about whether the products work or if they meet customer expectations. Instead, your focus is on the value you bring to the market.
-
Stock-based: This stock-based method focuses on the actual quantity of products being made at any given time. It's used when you want to maximize production while minimizing inventory.
-
Just-intime planning (JIT), is a combination JIT/sales chain management. It's the process of scheduling delivery of components immediately after they are ordered. It's important because it reduces lead times and increases throughput.