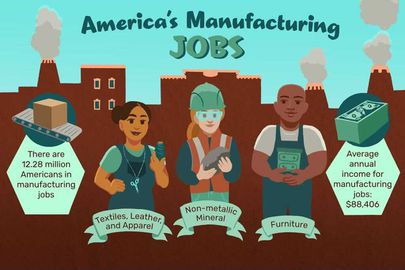
A director of manufacturing manages the company's entire manufacturing process. They play a vital role in overseeing the manufacturing process from design through production. To succeed in this role, the ideal candidate must have extensive experience in manufacturing and be familiar with new technologies. Robotics and 3D printing are two examples of these technologies. A director who keeps up with these technologies is an asset to his company. The director's role in the manufacturing industry will change as it evolves. He or she will need to work closely with engineering and operations, as well as placing greater emphasis on quality control in the manufacturing plant.
Director of manufacturing salary
The region in which a Director or Manufacturing is located can have a significant impact on their salary. Many directors receive compensation in the low six-figures, with some earning significantly more than others. The salary of a Director of Manufacturing may also vary significantly based on years of experience and education. Here are some factors that could impact your salary.
Although the salary of a Director of Manufacturing is variable, it is generally higher for those with more experience. Salary can be affected depending on where you live and how much it costs to live. If you live in a big city, expect to earn higher salaries, but be aware that your salary may not match the cost of living. Always be willing to negotiate for a higher salary, if offered.
A Director of Manufacturing Operations makes between $181,500 and $66,000 a year. The salary for a director of manufacturing operations is variable. It can vary up to 8% from one city to the next. A director of manufacturing operations in Fremont, CA can earn between $128,493 and $164,500, which is considerably more than the national average. The salary of a Director in Manufacturing Operations can vary depending on where you live, how experienced you are, and what company you work for.
Education required
The director of manufacturing is responsible for managing a production facility and overseeing the production process. The director of manufacturing is responsible for hiring new workers, overseeing quality control, working with designers, as well as meeting operational standards. A director of manufacturing usually reports to the top management team. He or she executes sales and policy initiatives. Candidates must have experience in manufacturing and communicate well. Different companies have different requirements for directors of manufacturing.
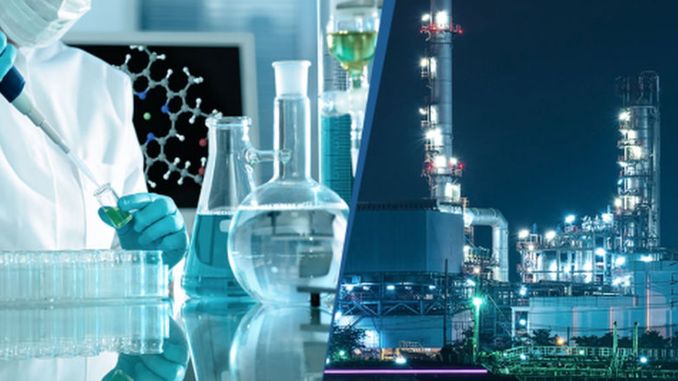
A graduate degree in engineering may not be required to become a director of manufacturing, but a post-secondary education will enhance your skills and knowledge. This position is well-suited for candidates who are interested in learning about business, management and economics. You will ultimately be responsible for managing diverse groups of people.
As a director manufacturing, you will closely work with designers and engineers in the product development phase. During this stage, you will be active in evaluating the feasibility of new processes and ensuring quality standards before committing resources to larger productions. Successful directors are also responsible for overseeing the production process and acting as coaches for their employees. They will coach them in best practices and risk mitigation. A manufacturing director must not only oversee the production process but also be able to solve problems.
Experience required
This position often requires a bachelor's degree in a relevant area and five to ten years of progressive work experience. In general, manufacturing companies prefer to hire employees for this job. The ideal candidate will have a thorough understanding of the manufacturing process and business objectives. Some employers may prefer a graduate certificate. These requirements may not be sufficient. Candidates may need to have additional training in their chosen industry or field.
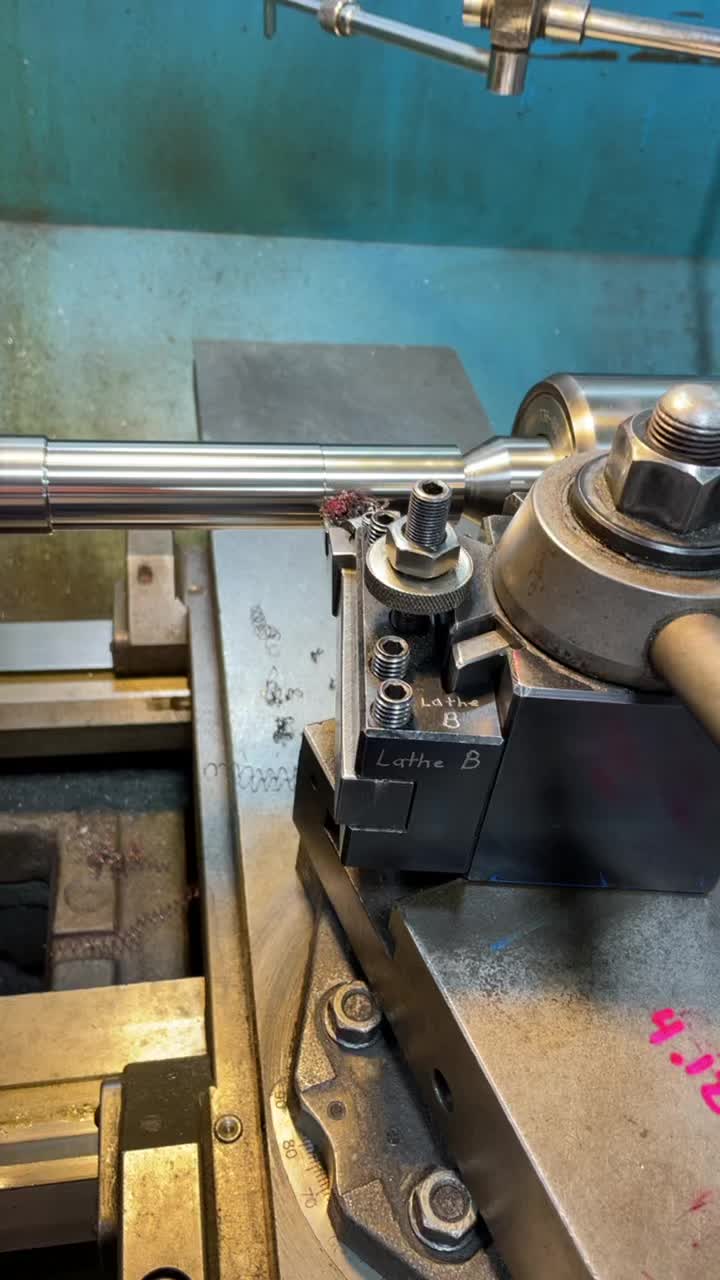
The production process is overseen by a director of manufacturing, which includes engineers, supervisors, workers, and other personnel. They may be responsible in solving problems and creating solutions. A director of manufacturing may not only oversee production but also develop and implement quality-control programs. The manufacturing director reports directly to the chief executive of the organization. Experience in manufacturing management is a must. Experience in manufacturing management can help you succeed in this position.
It is important to have experience as a director in manufacturing. Directors should have at least 10 years' experience in a manufacturing setting. Some of these people may have started as manufacturing supervisors or technicians. They must also be able to communicate well. The director of production should also have an in-depth understanding of the business strategy. Finally, the director of production must be able interact with other departments within the organization. In this capacity, the director oversees the production process and ensures that it meets the highest quality standards.
FAQ
What makes a production planner different from a project manger?
A production planner is more involved in the planning phase of the project than a project manger.
Is it necessary to be familiar with Manufacturing Processes before we learn about Logistics.
No. No. Knowing about manufacturing processes will help you understand how logistics works.
What are the responsibilities for a manufacturing manager
Manufacturing managers must ensure that manufacturing processes are efficient, effective, and cost-effective. They should also be aware and responsive to any company problems.
They must also be able to communicate with sales and marketing departments.
They should be up to date on the latest trends and be able apply this knowledge to increase productivity and efficiency.
What are the 7 Rs of logistics?
The acronym 7R's of Logistic is an acronym that stands for seven fundamental principles of logistics management. It was developed by the International Association of Business Logisticians (IABL) and published in 2004 as part of its "Seven Principles of Logistics Management" series.
The following letters make up the acronym:
-
Responsible – ensure that all actions are legal and don't cause harm to anyone else.
-
Reliable – have faith in your ability and capability to keep promises.
-
Reasonable - make sure you use your resources well and don't waste them.
-
Realistic - Consider all aspects of operations, including environmental impact and cost effectiveness.
-
Respectful - Treat people fairly and equitably
-
You are resourceful and look for ways to save money while increasing productivity.
-
Recognizable - Provide value-added services to customers
What are the essential elements of running a logistics firm?
It takes a lot of skills and knowledge to run a successful logistics business. Good communication skills are essential to effectively communicate with your suppliers and clients. You will need to know how to interpret data and draw conclusions. You will need to be able handle pressure well and work in stressful situations. To improve efficiency, you must be innovative and creative. You need to have strong leadership qualities to motivate team members and direct them towards achieving organizational goals.
To meet tight deadlines, you must also be efficient and organized.
Statistics
- According to a Statista study, U.S. businesses spent $1.63 trillion on logistics in 2019, moving goods from origin to end user through various supply chain network segments. (netsuite.com)
- It's estimated that 10.8% of the U.S. GDP in 2020 was contributed to manufacturing. (investopedia.com)
- Job #1 is delivering the ordered product according to specifications: color, size, brand, and quantity. (netsuite.com)
- Many factories witnessed a 30% increase in output due to the shift to electric motors. (en.wikipedia.org)
- (2:04) MTO is a production technique wherein products are customized according to customer specifications, and production only starts after an order is received. (oracle.com)
External Links
How To
How to Use lean manufacturing in the Production of Goods
Lean manufacturing is an approach to management that aims for efficiency and waste reduction. It was developed by Taiichi Okono in Japan, during the 1970s & 1980s. TPS founder Kanji Takoda awarded him the Toyota Production System Award (TPS). Michael L. Watkins published the "The Machine That Changed the World", the first book about lean manufacturing. It was published in 1990.
Lean manufacturing, often described as a set and practice of principles, is aimed at improving the quality, speed, cost, and efficiency of products, services, and other activities. It emphasizes reducing defects and eliminating waste throughout the value chain. Lean manufacturing is also known as just in time (JIT), zero defect total productive maintenance(TPM), and five-star (S). Lean manufacturing is about eliminating activities that do not add value, such as inspection, rework, and waiting.
In addition to improving product quality and reducing costs, lean manufacturing helps companies achieve their goals faster and reduces employee turnover. Lean manufacturing is a great way to manage the entire value chain including customers, suppliers, distributors and retailers as well as employees. Lean manufacturing practices are widespread in many industries. Toyota's philosophy is a great example of this. It has helped to create success in automobiles as well electronics, appliances and healthcare.
Five fundamental principles underlie lean manufacturing.
-
Define Value - Identify the value your business adds to society and what makes you different from competitors.
-
Reduce Waste - Remove any activity which doesn't add value to your supply chain.
-
Create Flow – Ensure that work flows smoothly throughout the process.
-
Standardize and simplify – Make processes as repeatable and consistent as possible.
-
Build relationships - Develop and maintain personal relationships with both your internal and external stakeholders.
Lean manufacturing is not a new concept, but it has been gaining popularity over the last few years due to a renewed interest in the economy following the global financial crisis of 2008. To increase their competitiveness, many businesses have turned to lean manufacturing. According to some economists, lean manufacturing could be a significant factor in the economic recovery.
With many benefits, lean manufacturing is becoming more common in the automotive industry. These include higher customer satisfaction, lower inventory levels, lower operating expenses, greater productivity, and improved overall safety.
You can apply Lean Manufacturing to virtually any aspect of your organization. However, it is particularly useful when applied to the production side of an organization because it ensures that all steps in the value chain are efficient and effective.
There are three types of lean manufacturing.
-
Just-in-Time Manufacturing (JIT): This type of lean manufacturing is commonly referred to as "pull systems." JIT stands for a system where components are assembled on the spot rather than being made in advance. This approach aims to reduce lead times, increase the availability of parts, and reduce inventory.
-
Zero Defects Manufacturing - ZDM: ZDM focuses its efforts on making sure that no defective units leave a manufacturing facility. You should repair any part that needs to be repaired during an assembly line. This also applies to finished products that need minor repairs before being shipped.
-
Continuous Improvement (CI), also known as Continuous Improvement, aims at improving the efficiency of operations through continuous identification and improvement to minimize or eliminate waste. Continuous improvement involves continuous improvement of processes and people as well as tools.