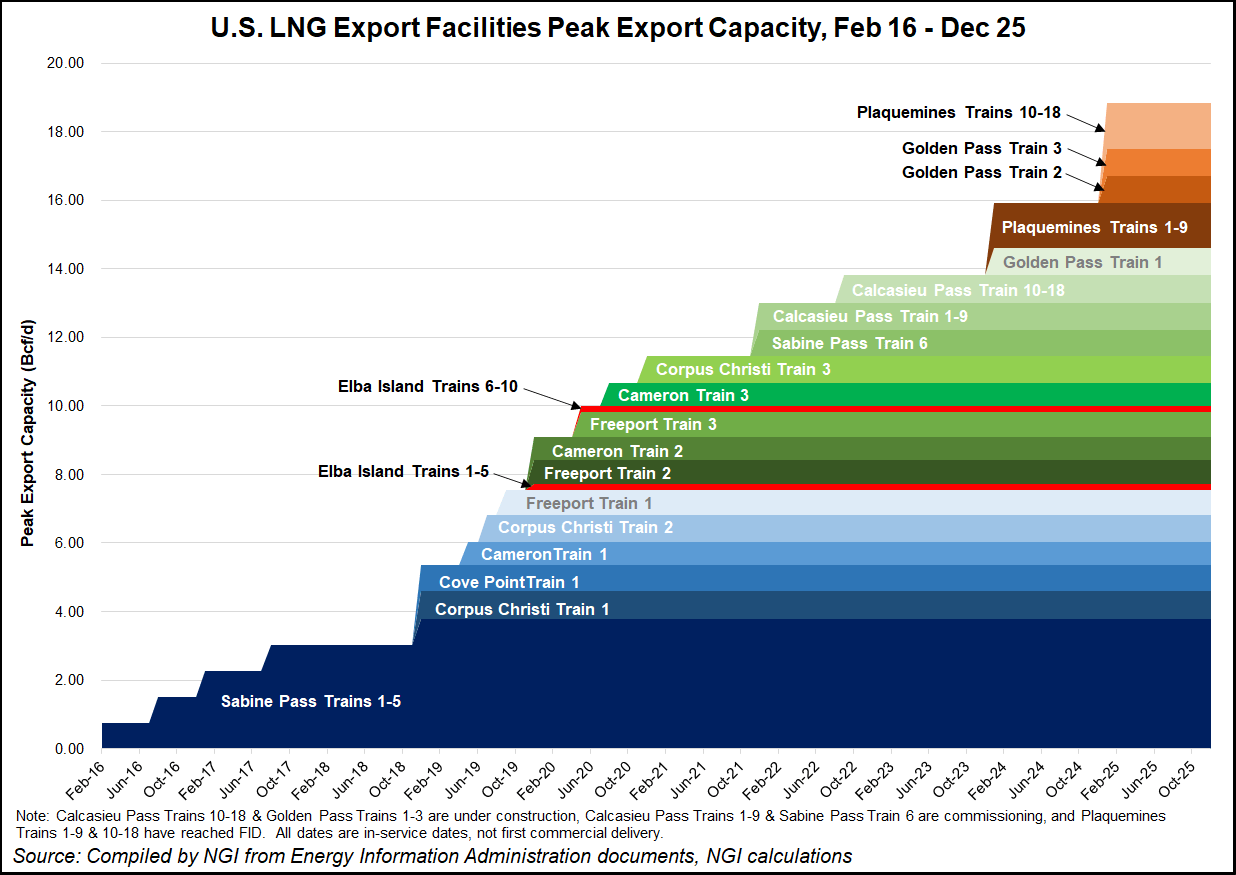
Civil engineers are responsible to create infrastructure such as roads and railways. They also design dams, bridges and harbours. The civil engineers also design and manage water and sewerage projects and other infrastructure.
To become a civil engineering requires a number of skills, as well as a dedication to education. Students who want to enter the field must earn a bachelor's degree in civil engineering or a related discipline, such as construction or business administration. Around one-fifth hold a Master's Degree. This increases your odds of being hired as a senior civil engineer. Some jobs may require a licensing from the Accreditation Council for Engineering and Technlogy (ABET).
Most entry-level jobs require a bachelor’s degree in civil or closely related disciplines, such as construction management. Most civil engineering programs take between four and five years to finish. However, many schools offer special programs which allow you to earn your degree for less money.
Graduates with civil engineering degrees can work in many roles, such a design engineer or project manager. They usually start in a graduate training scheme, where they work under an experienced professional to develop their skills. After gaining experience, they can move into a full-time role and eventually become a lead engineer.
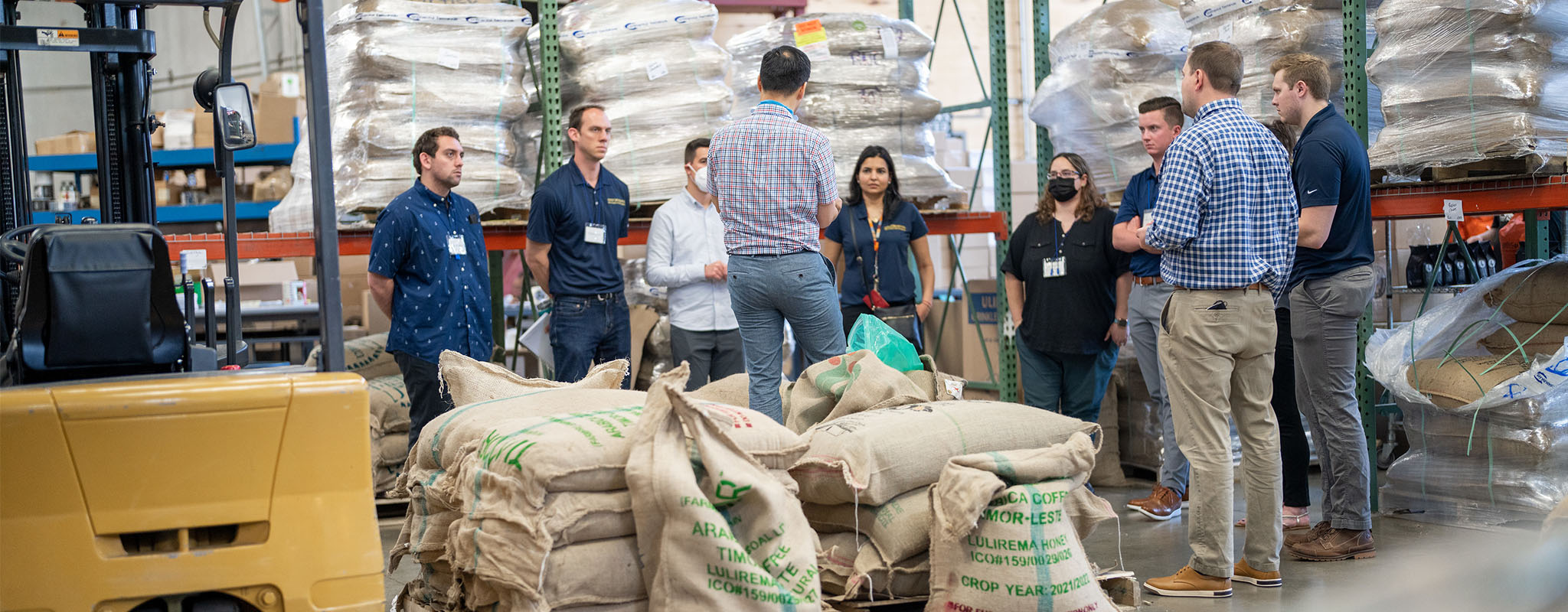
A career in civil engineering can be rewarding and challenging. There is also plenty of room to advance. You'll find these careers in a wide range of industries, such as transportation, energy, manufacturing and building construction.
Employers prefer candidates who are creative, have a good sense of communication and can think critically. These skills can help you to solve engineering problems for your employer and improve their technical processes.
Leadership and teamwork skills are also important, as you often oversee the construction of your projects. Communication skills are essential to resolve issues quickly with team members and vendors.
Civil engineering is a profession that changes with the industry. It's important to stay up-to-date with new trends and regulations. If you want to stay on top of the latest trends, consider joining a professional organisation or pursuing continuing education.
Also, decision-making is key to this job. You will need to make budgeting decisions and balance safety concerns with your own knowledge.
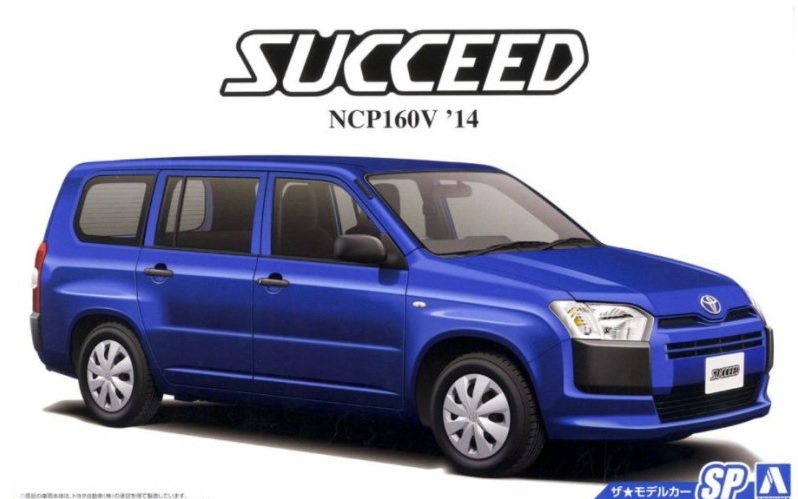
As a civil engineering, your educational and training background is important. You will need to show your worth by completing your projects on time and meeting your deadlines. Communicating with clients, colleagues and contractors is part of this.
Other skills that will help you succeed in this career include a strong understanding of mathematics and physics, as well as the ability to think creatively and come up with innovative solutions. You will also need to have the ability to analyze data, and to present your findings effectively.
The salary of a civil engineer varies widely depending on what you do and where you are located. California, Texas and Florida are the highest-paying states for civil engineers. Alaska, Rhode Island, and Wyoming are also states with high salaries for civil engineering.
FAQ
What is production planning?
Production Planning involves developing a plan for all aspects of the production, including scheduling, budgeting, casting, crew, location, equipment, props, etc. This document is designed to make sure everything is ready for when you're ready to shoot. This document should include information about how to achieve the best results on-set. This includes information on shooting times, locations, cast lists and crew details.
The first step is to decide what you want. You may already know where you want the film to be shot, or perhaps you have specific locations and sets you wish to use. Once you've identified the locations and scenes you want to use, you can begin to plan what elements you need for each scene. You might decide you need a car, but not sure what make or model. You could look online for cars to see what options are available, and then narrow down your choices by selecting between different makes or models.
Once you have found the right vehicle, you can think about adding accessories. Are you looking for people to sit in the front seats? You might also need someone to help you get around the back. Perhaps you would like to change the interior colour from black to white. These questions can help you decide the right look for your car. Also, think about what kind of shots you would like to capture. You will be filming close-ups and wide angles. Maybe the engine or steering wheel is what you are looking to film. This will allow you to determine the type of car you want.
Once you have established all the details, you can create a schedule. You can create a schedule that will outline when you must start and finish your shoots. Every day will have a time for you to arrive at the location, leave when you are leaving and return home when you are done. It will help everyone know exactly what they have to do and when. It is possible to make arrangements in advance for additional staff if you are looking to hire. It is not worth hiring someone who won’t show up because you didn’t tell him.
When creating your schedule, you will also need to consider the number of days you need to film. Some projects take only a few days while others can last several weeks. You should consider whether you will need more than one shot per week when creating your schedule. Multiple shots at the same location can increase costs and make it more difficult to complete. It is better to be cautious and take fewer shots than you risk losing money if you are not sure if multiple takes are necessary.
Budget setting is an important part of production planning. It is important to set a realistic budget so you can work within your budget. Keep in mind that you can always reduce your budget if you face unexpected difficulties. You shouldn't underestimate the amount you'll spend. You'll end up with less money after paying for other things if the cost is underestimated.
Production planning is a detailed process. But, once you understand the workings of everything, it becomes easier for future projects to be planned.
Is it necessary to be familiar with Manufacturing Processes before we learn about Logistics.
No. No. Knowing about manufacturing processes will help you understand how logistics works.
How can I find out more about manufacturing?
Hands-on experience is the best way to learn more about manufacturing. You can also read educational videos or take classes if this isn't possible.
How can we reduce manufacturing overproduction?
It is essential to find better ways to manage inventory to reduce overproduction. This would reduce time spent on activities such as purchasing, stocking, and maintaining excess stock. This could help us free up our time for other productive tasks.
A Kanban system is one way to achieve this. A Kanban board can be used to monitor work progress. Kanban systems allow work items to move through different states until they reach their final destination. Each state represents a different priority level.
When work is completed, it can be transferred to the next stage. It is possible to keep a task in the beginning stages until it gets to the end.
This keeps work moving and ensures no work is lost. Managers can see how much work has been done and the status of each task at any time with a Kanban Board. This allows them to adjust their workflows based on real-time information.
Lean manufacturing is another way to manage inventory levels. Lean manufacturing is about eliminating waste from all stages of the production process. Anything that does nothing to add value to a product is waste. Here are some examples of common types.
-
Overproduction
-
Inventory
-
Unnecessary packaging
-
Exceed materials
These ideas will help manufacturers increase efficiency and lower costs.
Statistics
- Many factories witnessed a 30% increase in output due to the shift to electric motors. (en.wikipedia.org)
- According to a Statista study, U.S. businesses spent $1.63 trillion on logistics in 2019, moving goods from origin to end user through various supply chain network segments. (netsuite.com)
- (2:04) MTO is a production technique wherein products are customized according to customer specifications, and production only starts after an order is received. (oracle.com)
- In the United States, for example, manufacturing makes up 15% of the economic output. (twi-global.com)
- It's estimated that 10.8% of the U.S. GDP in 2020 was contributed to manufacturing. (investopedia.com)
External Links
How To
Six Sigma and Manufacturing
Six Sigma is defined by "the application SPC (statistical process control) techniques to achieve continuous improvements." Motorola's Quality Improvement Department, Tokyo, Japan, developed it in 1986. Six Sigma's core idea is to improve the quality of processes by standardizing and eliminating defects. Many companies have adopted this method in recent years. They believe there is no such thing a perfect product or service. Six Sigma's primary goal is to reduce variation from the average value of production. This means that you can take a sample from your product and then compare its performance to the average to find out how often the process differs from the norm. If you notice a large deviation, then it is time to fix it.
The first step toward implementing Six Sigma is understanding how variability works in your business. Once you understand this, you can then identify the causes of variation. These variations can also be classified as random or systematic. Random variations occur when people make mistakes; systematic ones are caused by factors outside the process itself. For example, if you're making widgets, and some of them fall off the assembly line, those would be considered random variations. However, if you notice that every time you assemble a widget, it always falls apart at exactly the same place, then that would be a systematic problem.
After identifying the problem areas, you will need to devise solutions. You might need to change the way you work or completely redesign the process. After implementing the new changes, you should test them again to see if they worked. If they don’t work, you’ll need to go back and rework the plan.