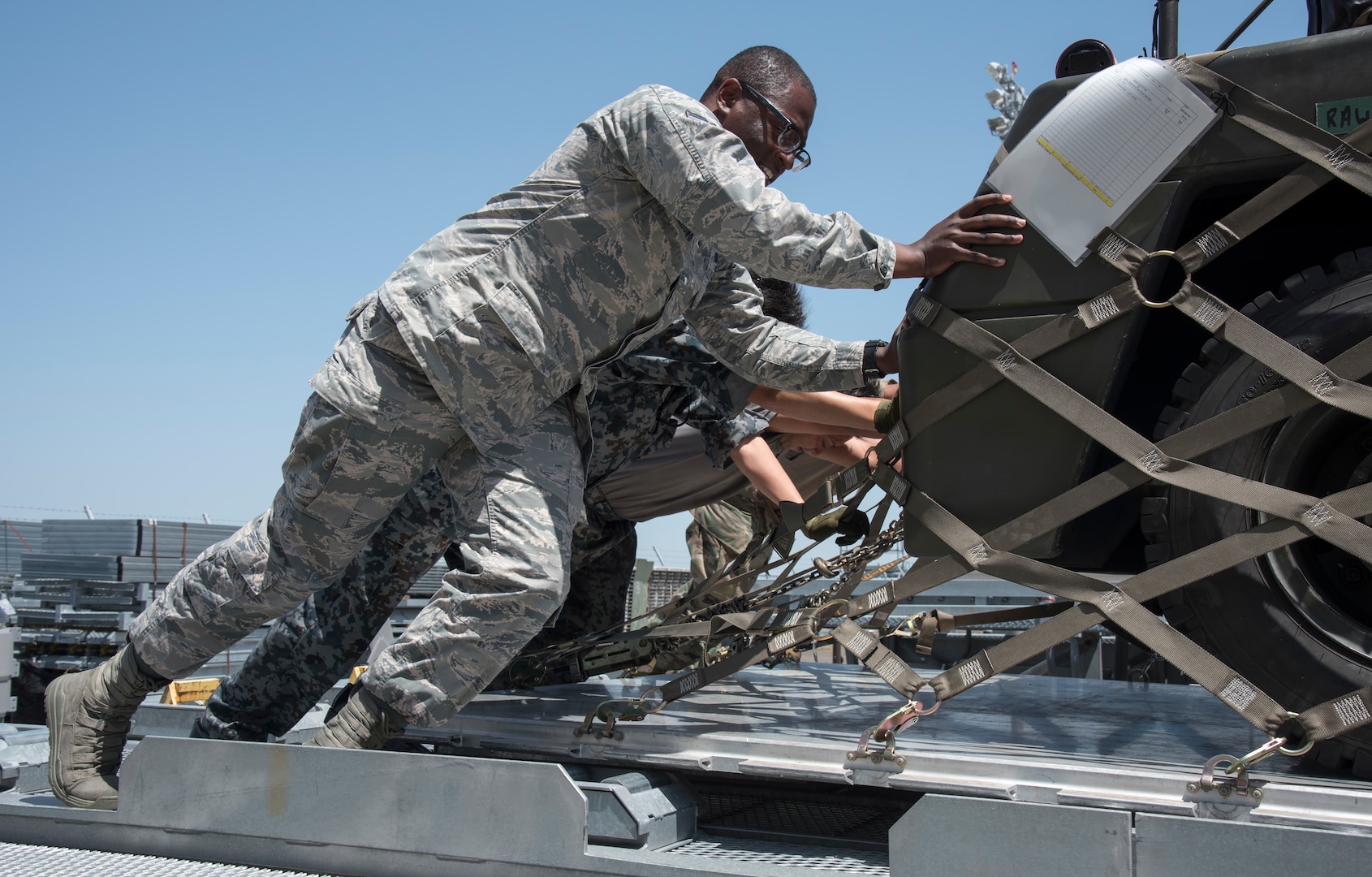
You should be aware of the average salary you can earn, regardless if you are looking for work or pursuing a degree. The pay for industrial engineers can vary depending on what kind of degree you pursue, your industry and your experience. The average industrial engineer income is $95,300. However, salaries are often higher in the top paying metropolitan areas.
Industrial engineers are responsible for designing, developing and installing systems that increase the productivity of the production process. They can also help make workplaces safer. The industrial engineer can design equipment, plan facilities, and analyze the specifications for products. This is possible by analysing how changes to design impact the cost of manufacturing the product.
An industrial engineer can earn a very high salary if he or she has experience. An industrial engineer can earn a higher wage if they have a master’s degree. This degree is popular with international students. It can lead them to careers in manufacturing, healthcare, and engineering services.
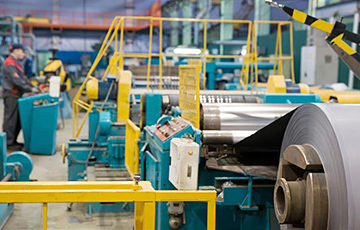
Industrial engineers are also expected to have a high employment growth rate over the next decade. The employment of industrial engineers is expected to rise 10 percent between 2021 and 2031. This is higher than what the average salary for all occupations. The top 10 per cent of industrial engineers earns more than $85,000 each year. You can also expect them to earn more if you have management experience. Industrial engineers with advanced degrees also conduct cost-benefit analyses, review cost distribution in operational processes and negotiate for purchasing decisions.
Industrial engineers can think out of the box and create innovative ways for processes to be more efficient. Many industrial engineers work in offices. They may also interact with production workers. Industrial engineers can also handle telephone calls, emails and face-to–face conversations. They might present their plans either in written reports or oral presentations.
Industrial engineers are expected to find work in a variety of industries, such as construction, pharmaceuticals, manufacturing, transportation, energy and utilities. Depending on their work, industrial engineers may develop systems that reduce the waste generated by production processes.
A bachelor's degree is usually required for industrial engineers. Industrial engineers can also pursue a master's degree in industrial engineering, which can lead to a career in engineering consulting or manufacturing. Most programs include courses in mathematics, science, and general engineering. It may take up to seven years for the program to be completed.
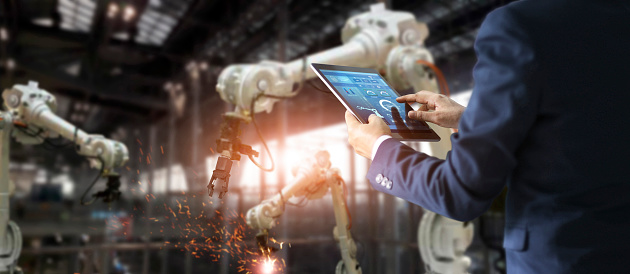
The average salary for an entry-level industrial engineer is $65,000 to $75,000, although the range of salary increases with experience. An industrial engineer with experience earns $86,809 annually. If an industrial engineer has a master's in engineering or doctorate, their salary may be higher.
Industrial engineers need to have good communication skills and technical knowledge. They must be able solve problems outside of their usual scope. They must know how to work with workers, equipment and materials to create efficient systems. They must also have good interpersonal skills. The job can be both challenging and rewarding.
FAQ
Can we automate some parts of manufacturing?
Yes! Since ancient times, automation has been in existence. The wheel was invented by the Egyptians thousands of years ago. We now use robots to help us with assembly lines.
Actually, robotics can be used in manufacturing for many purposes. These include:
-
Line robots
-
Robot welding
-
Robot painting
-
Robotics inspection
-
Robots that make products
Automation could also be used to improve manufacturing. For example, 3D printing allows us to make custom products without having to wait for weeks or months to get them manufactured.
What does manufacturing industry mean?
Manufacturing Industries are those businesses that make products for sale. Consumers are the people who purchase these products. This is accomplished by using a variety of processes, including production, distribution and retailing. These companies produce goods using raw materials and other equipment. This includes all types if manufactured goods.
How can I learn about manufacturing?
Practical experience is the best way of learning about manufacturing. But if that is not possible you can always read books and watch educational videos.
Why should you automate your warehouse?
Modern warehouses are increasingly dependent on automation. Increased demand for efficient and faster delivery has resulted in a rise in e-commerce.
Warehouses have to be flexible to meet changing requirements. Technology is essential for warehouses to be able to adapt quickly to changing needs. Automating warehouses is a great way to save money. These are some of the benefits that automation can bring to warehouses:
-
Increases throughput/productivity
-
Reduces errors
-
Improves accuracy
-
Safety increases
-
Eliminates bottlenecks
-
Companies can scale up more easily
-
Workers are more productive
-
Gives you visibility into all that is happening in your warehouse
-
Enhances customer experience
-
Improves employee satisfaction
-
It reduces downtime, and increases uptime
-
This ensures that quality products are delivered promptly
-
Eliminates human error
-
Helps ensure compliance with regulations
What are the responsibilities of a logistic manager?
Logistics managers ensure that goods arrive on time and are unharmed. This is done using his/her knowledge of the company's products. He/she should also ensure enough stock is available to meet demand.
Statistics
- Many factories witnessed a 30% increase in output due to the shift to electric motors. (en.wikipedia.org)
- In 2021, an estimated 12.1 million Americans work in the manufacturing sector.6 (investopedia.com)
- (2:04) MTO is a production technique wherein products are customized according to customer specifications, and production only starts after an order is received. (oracle.com)
- Job #1 is delivering the ordered product according to specifications: color, size, brand, and quantity. (netsuite.com)
- [54][55] These are the top 50 countries by the total value of manufacturing output in US dollars for its noted year according to World Bank.[56] (en.wikipedia.org)
External Links
How To
How to Use the Just In Time Method in Production
Just-intime (JIT), a method used to lower costs and improve efficiency in business processes, is called just-in-time. It allows you to get the right amount resources at the right time. This means that you only pay for what you actually use. The term was first coined by Frederick Taylor, who developed his theory while working as a foreman in the early 1900s. Taylor observed that overtime was paid to workers if they were late in working. He decided that workers would be more productive if they had enough time to complete their work before they started to work.
JIT is about planning ahead. You should have all the necessary resources ready to go so that you don’t waste money. Look at your entire project, from start to end. Make sure you have enough resources in place to deal with any unexpected problems. You'll be prepared to handle any potential problems if you know in advance. This way, you won't end up paying extra money for things that weren't really necessary.
There are different types of JIT methods:
-
Demand-driven: This type of JIT allows you to order the parts/materials required for your project on a regular basis. This will allow to track how much material has been used up. This will allow to you estimate the time it will take for more to be produced.
-
Inventory-based: This is a type where you stock the materials required for your projects in advance. This allows one to predict how much they will sell.
-
Project-driven : This is a method where you make sure that enough money is set aside to pay the project's cost. You will be able to purchase the right amount of materials if you know what you need.
-
Resource-based: This is the most common form of JIT. You assign certain resources based off demand. For example, if there is a lot of work coming in, you will have more people assigned to them. If you don't have many orders, you'll assign fewer people to handle the workload.
-
Cost-based: This approach is very similar to resource-based. However, you don't just care about the number of people you have; you also need to consider how much each person will cost.
-
Price-based: This is a variant of cost-based. However, instead of focusing on the individual workers' costs, this looks at the total price of the company.
-
Material-based: This approach is similar to cost-based. However, instead of looking at the total cost for the company, you look at how much you spend on average on raw materials.
-
Time-based: This is another variation of resource-based JIT. Instead of focusing on how much each employee costs, you focus on how long it takes to complete the project.
-
Quality-based JIT: This is another variation of resource based JIT. Instead of looking at the labor costs and time it takes to make a product, think about its quality.
-
Value-based: This is one of the newest forms of JIT. In this instance, you are not concerned about the product's performance or meeting customer expectations. Instead, you're focused on how much value you add to the market.
-
Stock-based is an inventory-based system that measures the number of items produced at any given moment. This method is useful when you want to increase production while decreasing inventory.
-
Just-intime (JIT), planning is a combination JIT management and supply chain management. It is the process that schedules the delivery of components within a short time of their order. It's important as it reduces leadtimes and increases throughput.