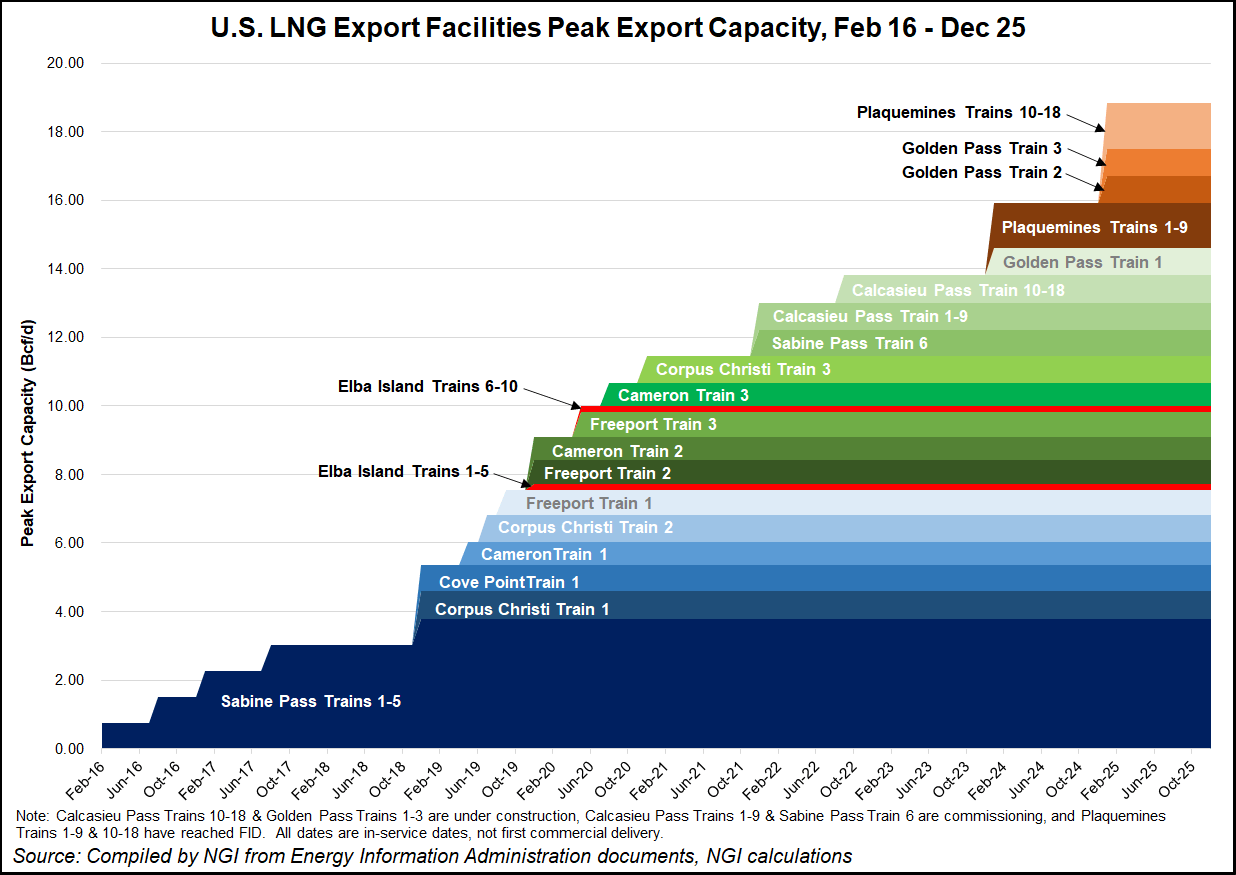
Demand management is a technique used to ensure that a company meets the demands of its customers. In essence, it involves bridging the gap between marketing and supply, by enabling organizations to predict demand. The process can help companies improve the speed and quality of delivery, reduce the amount of invoice disputes, and lower the cost of running the business.
Companies that have a solid demand management system are more likely to respond to market changes. This is because they have a system in place to identify the ideal customer, which can lead to effective marketing.
Demand management can help businesses plan for future demand, and improve customer satisfaction. If done properly, it can reduce invoice disputes and increase asset utilization. A good demand management strategy will also increase operational flexibility and operational resilience.
A project management program can improve the demand management approach. Such software allows teams to collaborate and prevent silos. Companies can also use change management plans to quickly address supply chain issues.
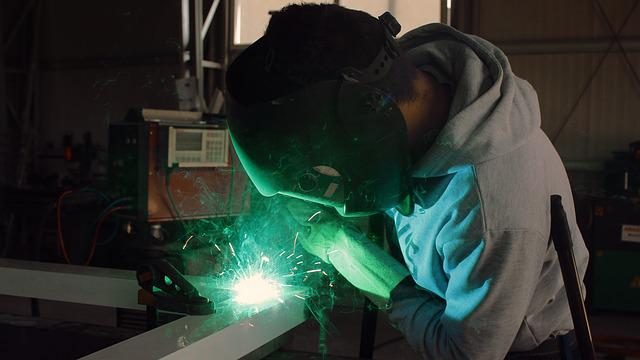
ILOG's PowerOps Suite combines manufacturing scheduling functions. Similarly, QAD and Dynasys offer applications that allow organizations to create a demand and supply plan. These applications help companies visualize the impact of supply chain changes. Optiant's ERP solutions can help organizations develop consistent, efficient and consistent order- and supply-management processes.
Real-Time Inventory, Terra Technology and CDC Software all offer real-time forecasting tools that can reduce supply-chain disruptions. Collaboration management strategies allow companies to share information, and help each other. It can include performance indicators and knowledge sharing.
However, before implementing a demand management strategy, it is important to consider a few factors. These factors will allow professionals to understand the process better, and be able to focus on what is most important.
Leadership buy in is an essential part of a demand management process. Demand management is an extremely collaborative process that involves multiple levels of management. Managers and top executives are the most important players at the highest levels. They are responsible for ensuring all members are on the exact same page. Important to the success and sustainability of the initiative are those at the bottom.
Although there are many software applications that can be used by organizations to implement a supply and demand plan, here are some key elements to keep in mind:
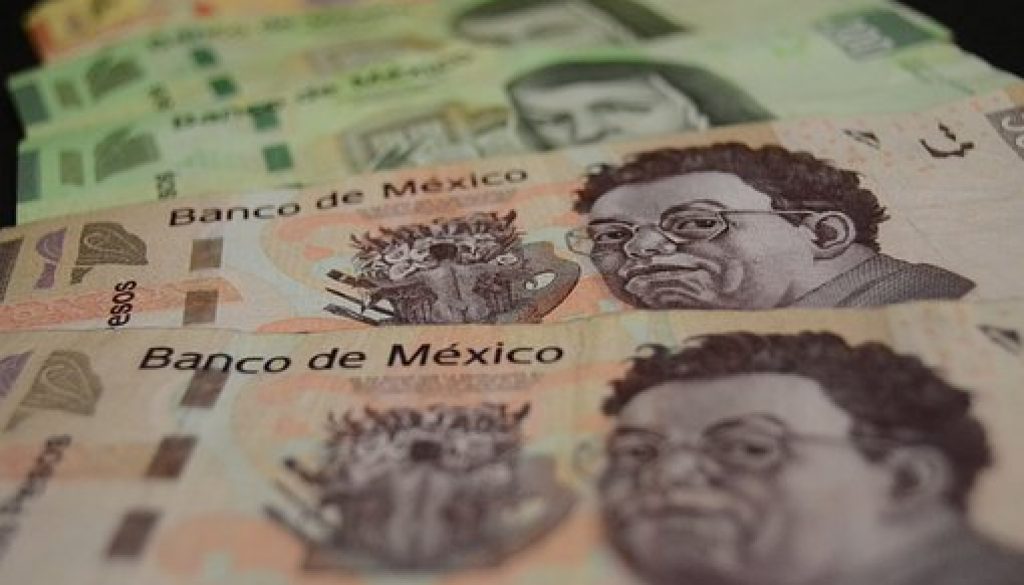
The demand management process is only possible if you know your market well enough to identify the perfect customer. In addition to knowing who to target, the organization should be able to effectively measure and analyze the results of its efforts.
Businesses need to be more agile in order to develop a demand management plan that is easily adaptable to changing circumstances. An effective plan can reduce the tactical forecast error and the number of supply chain disruptions. Finally, demand management can help you develop and execute portfolio and strategic plans.
FAQ
What are manufacturing and logistics?
Manufacturing refers the process of producing goods from raw materials through machines and processes. Logistics includes all aspects related to supply chain management, such as procurement, distribution planning, inventory control and transportation. Manufacturing and logistics can often be grouped together to describe a larger term that covers both the creation of products, and the delivery of them to customers.
What are the essential elements of running a logistics firm?
To be a successful businessman in logistics, you will need many skills and knowledge. For clients and suppliers to be successful, you need to have excellent communication skills. You need to understand how to analyze data and draw conclusions from it. You must be able manage stress and pressure under pressure. To increase efficiency and creativity, you need to be creative. You need to have strong leadership qualities to motivate team members and direct them towards achieving organizational goals.
It is important to be organized and efficient in order to meet tight deadlines.
What does warehouse mean?
A warehouse, or storage facility, is where goods are stored prior to being sold. It can be an outdoor or indoor area. In some cases, it may be a combination of both.
Statistics
- In 2021, an estimated 12.1 million Americans work in the manufacturing sector.6 (investopedia.com)
- You can multiply the result by 100 to get the total percent of monthly overhead. (investopedia.com)
- In the United States, for example, manufacturing makes up 15% of the economic output. (twi-global.com)
- It's estimated that 10.8% of the U.S. GDP in 2020 was contributed to manufacturing. (investopedia.com)
- According to the United Nations Industrial Development Organization (UNIDO), China is the top manufacturer worldwide by 2019 output, producing 28.7% of the total global manufacturing output, followed by the United States, Japan, Germany, and India.[52][53] (en.wikipedia.org)
External Links
How To
How to use 5S in Manufacturing to Increase Productivity
5S stands as "Sort", Set In Order", Standardize", Separate" and "Store". Toyota Motor Corporation developed the 5S method in 1954. It improves the work environment and helps companies to achieve greater efficiency.
The basic idea behind this method is to standardize production processes, so they become repeatable, measurable, and predictable. Cleaning, sorting and packing are all done daily. Because workers know what they can expect, this helps them perform their jobs more efficiently.
There are five steps to implementing 5S, including Sort, Set In Order, Standardize, Separate and Store. Each step involves a different action which leads to increased efficiency. For example, when you sort things, you make them easy to find later. When items are ordered, they are put together. Once you have separated your inventory into groups and organized them, you will store these groups in easily accessible containers. Finally, when you label your containers, you ensure everything is labeled correctly.
Employees must be able to critically examine their work practices. Employees must be able to see why they do what they do and find a way to achieve them without having to rely on their old methods. In order to use the 5S system effectively, they must be able to learn new skills.
In addition to increasing efficiency, the 5S method also improves morale and teamwork among employees. They are more motivated to achieve higher efficiency levels as they start to see improvement.