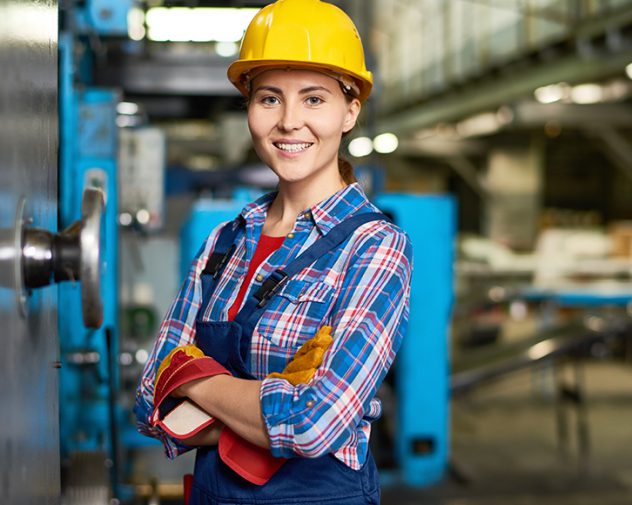
Typically, tool and die makers work in machine shops. They operate lathes, milling machines, and other types of machine tools. They also repair tools and make dies for machine machinists. They might also design tools for customers.
Tool and Die makers must adhere to strict quality control and precision in all of their work. They check the quality of their work and inspect the finished product. To improve processes, tool- and die-makers can work with engineers. To see the tool in action, they may visit a customer's facility. They must also keep their work areas clean and organized. They might also be required to wear protective gear. They may suggest additional tools to improve efficiency.
Tool and die makers typically work 40 hours a week. They may also be expected to do moderately heavy lifting. They are also required to have a strong educational background. Employers may prefer an associate's, bachelor's, or master's degree in a similar field. They might also be eligible for formal training on the job or apprenticeship programs.

Four-year apprenticeship programs for tool and diemakers are typically offered by employers. They receive training on the job from an experienced worker during their apprenticeship program. They also have the option to attend night classes at technical colleges. This program offers both classroom instruction and hands-on training. They may also be given the chance to program computer controlled machine tools. They may be eligible to move up to supervisory posts.
The majority of tool and diemakers hold a high-school diploma or an equivalent. They may also have a degree, such as in engineering or Physics. They may also have prior training in math or science. This training can be very helpful.
Tool and diemakers need good eyesight. They need to be able to concentrate and have patience. They need to be strong enough to lift heavy machinery. They should be hardworking and able to lift heavy items. They must be able read and understand engineering drawings and specifications. They must also be able to communicate well with others. They should also be able to use computers effectively. They might also be needed to maintain computer numerically controlled machines (CNC).
The analytical mind of tool and die-makers is crucial. They have to understand how tools and dies work and how to repair them. They must also be able to solve problems and have mechanical ability. They may also need to be able to learn new machining techniques. They must be skilled in digital skills such computer-aided design and manufacturing (CAM) software. They should also possess sales skills. They must be able work with and independently.
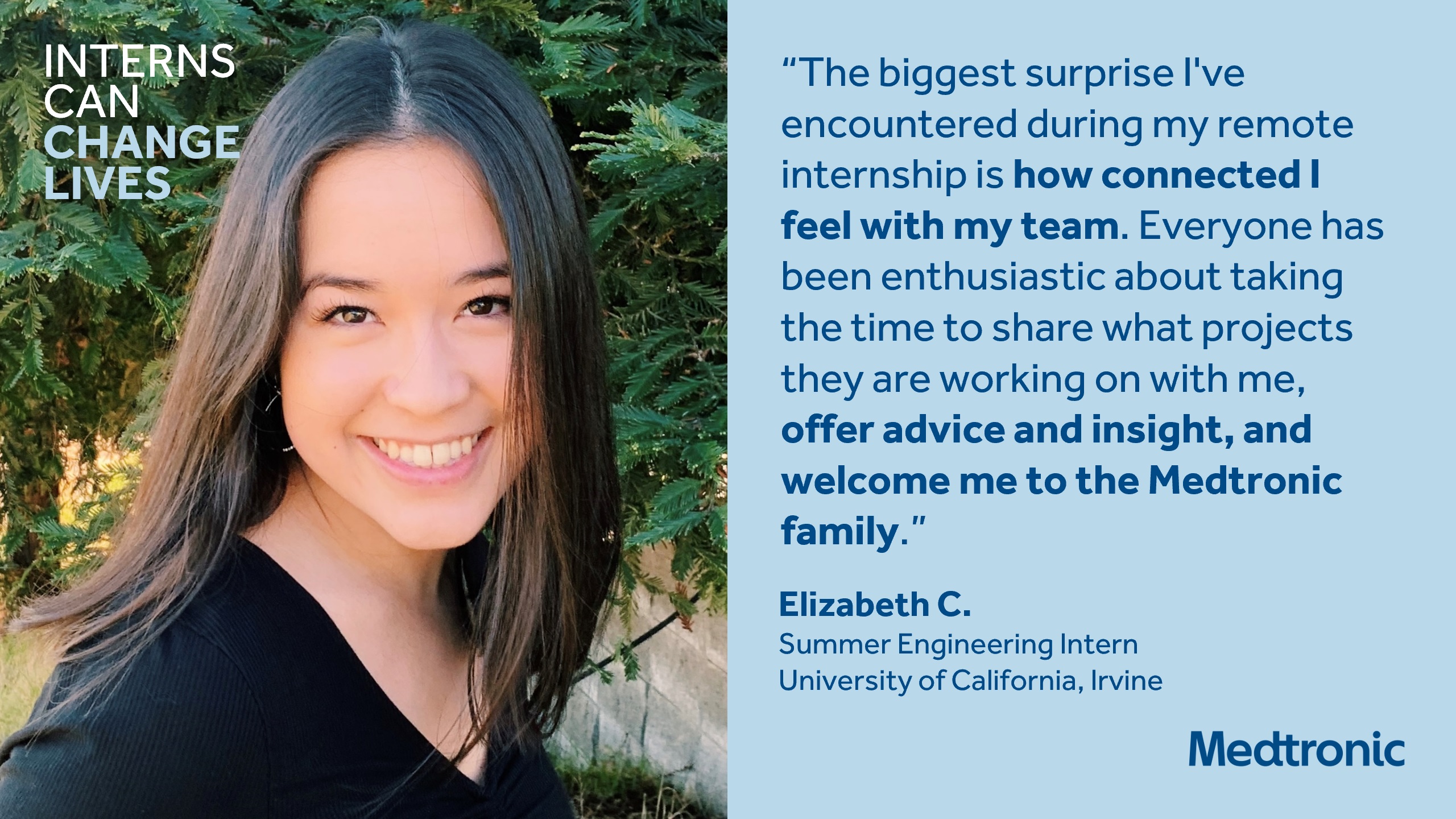
Apprentices can expect to work 40 hours per semaine during an apprenticeship program. They work in a classroom during the night, and they attend class at night. They are eventually able to take on more difficult assignments. For most apprenticeships, you will need a high school diploma. They will also need to take courses in science, math, and technology.
Some tool and diemakers go on to get a master's or bachelor's degree. Average salary for tool and diemakers is $56,186. But, they are likely to see a decrease in their job prospects due to automation.
FAQ
Are there any Manufacturing Processes that we should know before we can learn about Logistics?
No. No. Understanding the manufacturing process will allow you to better understand logistics.
How can excess manufacturing production be reduced?
In order to reduce excess production, you need to develop better inventory management methods. This would reduce the time spent on unproductive activities like purchasing, storing and maintaining excess stock. This will allow us to free up resources for more productive tasks.
This can be done by using a Kanban system. A Kanbanboard is a visual tool that allows you to keep track of the work being done. Work items are moved through various states to reach their destination in a Kanban system. Each state represents a different priority.
To illustrate, work can move from one stage or another when it is complete enough for it to be moved to a new stage. If a task is still in its beginning stages, it will continue to be so until it reaches the end.
This allows work to move forward and ensures that no work is missed. A Kanban board allows managers to monitor how much work is being completed at any given moment. This information allows managers to adjust their workflow based off real-time data.
Lean manufacturing is another option to control inventory levels. Lean manufacturing is about eliminating waste from all stages of the production process. Anything that doesn't add value to the product is considered waste. There are several types of waste that you might encounter:
-
Overproduction
-
Inventory
-
Packaging not required
-
Excess materials
Manufacturers can reduce their costs and improve their efficiency by using these ideas.
What skills should a production planner have?
You must be flexible and organized to become a productive production planner. Effective communication with clients and colleagues is essential.
Are there ways to automate parts of manufacturing?
Yes! Since ancient times, automation has been in existence. The wheel was invented by the Egyptians thousands of years ago. Nowadays, we use robots for assembly lines.
Robotics is used in many manufacturing processes today. They include:
-
Line robots
-
Robot welding
-
Robot painting
-
Robotics inspection
-
Robots that make products
Automation can be applied to manufacturing in many other ways. For example, 3D printing allows us to make custom products without having to wait for weeks or months to get them manufactured.
What does it take for a logistics enterprise to succeed?
To run a successful logistics company, you need a lot knowledge and skills. Good communication skills are essential to effectively communicate with your suppliers and clients. You should be able analyse data and draw inferences. You must be able manage stress and pressure under pressure. You need to be innovative and creative to come up with new ways to increase efficiency. You will need strong leadership skills to motivate and direct your team members towards achieving their organizational goals.
You should also be organized and efficient to meet tight deadlines.
What are the 4 types manufacturing?
Manufacturing is the process by which raw materials are transformed into useful products through machines and processes. It can involve many activities like designing, manufacturing, testing packaging, shipping, selling and servicing.
What is the role of a manager in manufacturing?
A manufacturing manager must make sure that all manufacturing processes run smoothly and effectively. They must also be alert to any potential problems and take appropriate action.
They must also be able to communicate with sales and marketing departments.
They should also be aware of the latest trends in their industry and be able to use this information to help improve productivity and efficiency.
Statistics
- It's estimated that 10.8% of the U.S. GDP in 2020 was contributed to manufacturing. (investopedia.com)
- In the United States, for example, manufacturing makes up 15% of the economic output. (twi-global.com)
- In 2021, an estimated 12.1 million Americans work in the manufacturing sector.6 (investopedia.com)
- [54][55] These are the top 50 countries by the total value of manufacturing output in US dollars for its noted year according to World Bank.[56] (en.wikipedia.org)
- You can multiply the result by 100 to get the total percent of monthly overhead. (investopedia.com)
External Links
How To
How to Use Lean Manufacturing for the Production of Goods
Lean manufacturing (or lean manufacturing) is a style of management that aims to increase efficiency, reduce waste and improve performance through continuous improvement. It was developed by Taiichi Okono in Japan, during the 1970s & 1980s. TPS founder Kanji Takoda awarded him the Toyota Production System Award (TPS). The first book published on lean manufacturing was titled "The Machine That Changed the World" written by Michael L. Watkins and published in 1990.
Lean manufacturing is often defined as a set of principles used to improve the quality, speed, and cost of products and services. It emphasizes reducing defects and eliminating waste throughout the value chain. The five-steps of Lean Manufacturing are just-in time (JIT), zero defect and total productive maintenance (TPM), as well as 5S. Lean manufacturing is about eliminating activities that do not add value, such as inspection, rework, and waiting.
Lean manufacturing can help companies improve their product quality and reduce costs. Additionally, it helps them achieve their goals more quickly and reduces employee turnover. Lean manufacturing can be used to manage all aspects of the value chain. Customers, suppliers, distributors, retailers and employees are all included. Lean manufacturing can be found in many industries. Toyota's philosophy is the foundation of its success in automotives, electronics and appliances, healthcare, chemical engineers, aerospace, paper and food, among other industries.
Five fundamental principles underlie lean manufacturing.
-
Define Value - Identify the value your business adds to society and what makes you different from competitors.
-
Reduce waste - Get rid of any activity that does not add value to the supply chain.
-
Create Flow – Ensure that work flows smoothly throughout the process.
-
Standardize & Simplify - Make processes as consistent and repeatable as possible.
-
Build Relationships- Develop personal relationships with both internal as well as external stakeholders.
Lean manufacturing, although not new, has seen renewed interest in the economic sector since 2008. Many businesses have adopted lean manufacturing techniques to help them become more competitive. Some economists even believe that lean manufacturing can be a key factor in economic recovery.
Lean manufacturing is becoming a popular practice in automotive. It has many advantages. These benefits include increased customer satisfaction, reduced inventory levels and lower operating costs.
The principles of lean manufacturing can be applied in almost any area of an organization. This is because it ensures efficiency and effectiveness in all stages of the value chain.
There are three types principally of lean manufacturing:
-
Just-in Time Manufacturing, (JIT): This kind of lean manufacturing is also commonly known as "pull-systems." JIT refers to a system in which components are assembled at the point of use instead of being produced ahead of time. This method reduces lead times, increases availability, and decreases inventory.
-
Zero Defects Manufacturing, (ZDM): ZDM is focused on ensuring that no defective products leave the manufacturing facility. You should repair any part that needs to be repaired during an assembly line. This also applies to finished products that need minor repairs before being shipped.
-
Continuous Improvement: Continuous Improvement aims to improve efficiency by continually identifying problems and making adjustments to eliminate or minimize waste. Continuous Improvement (CI) involves continuous improvement in processes, people, tools, and infrastructure.